Industrialization is rapidly expanding. Even Third World countries are no longer exempt from this. In the well-developed industrial nations of this world, the extent of mechanization has touched a point at which nature alone cannot compensate the strains related to technology. Crucial issues, such as global warming and the decreasing of the ground water level can be seen across many newspapers and are the subject of passionate public debate. The calls to preserve the environment are increasingly louder.
The Process
There are many possible methods to safeguarding the environment. In the case of wastewater, there is the option of using pressure ventilation in biological wastewater treatment plants or ventilating sediment tanks. The incorporation of oxygen is crucial for wastewater treatment systems with standard aeration tanks, deep wastewater tanks, or natural clarification ponds alike.
If wastewater has already entered the natural cycle, ventilating rivers and lakes prevents further contamination. When treating drinking water, rinsing the filters with compressed air guarantees the supply of pure water, and natural water reserves are not excessively burdened. Gases coming out of landfill sites, in digestion towers and gases utilized for treating wastewater no longer seep into the environment, and are not burned off unnecessarily.
.jpg)
.jpg)
Image Credit: Aerzen
As an alternative, these are used sustainably to form energy that relieves environmental strain and rectifies resource deficits. The pressure increase in biogas blowers moves gas to generators or CHPs, where the converted energy can be used to heat greenhouses, buildings, etc. The gas that is generated is measured by AERZEN rotary piston gas meters. During sludge drying processes, AERZEN positive displacement blowers can be employed for the following pneumatic transport of the dried sludge. However AERZEN products do a lot more than this.
Just as there are a number of ways of protecting the environment, there are also a number of areas of application for AERZEN rotary lobe compressors, positive displacement blowers and turbo blowers. Heat recovery can also make a considerable contribution to the conservation of energy resources.
.jpg)
Image Credit: Aerzen
Application Report
Wastewater Treatment Plant in Rheda-Wiedenbrück
(Up to 35 % more energy-efficient air thanks to Performance and AERsmart)
Efficient Air for Wastewater Treatment Plants: AERZEN Combines Blower Technology
Modernizations are a crucial trend in wastewater treatment, and the steadily falling limit values for ammonium, phosphate, and nitrate are driving the applicable investment decisions. When it comes to budgeting conclusions, the interdependency of climate protection and finances means that it pays off to include energy efficiency into one’s plans. In light of the fact that the air-supply aspect of aeration alone frequently makes up for more than 70% of operating costs, it soon becomes clear why efficiency enhancements are particularly helpful in this field - and with high investment returns.
This is precisely how the wastewater treatment plant Rheda-Wiedenbrück (326,000 population equivalents) was designed. The plant is presently testing a brand-new control concept for the AERZEN blower technology: the AERsmart control combination.
In 2013, the modernization efforts on the wastewater plant started. The plant is associated with the population of the Rheda-Wiedenbrück region, as well as Germany’s biggest slaughterhouse for swine. One of the key objectives of the project was to boost the efficiency of the air supply to the biological material by not only changing old ventilation grids, but also fixing new grids 30 cm deeper in the base of the aeration tanks.
In view of the surface of the six basins we could increase our processing volume by several hundred cubic meters.
Hendrik Wulfhorst, Wastewater Manager
However, a spatial gain of 30 cm caused an increase in system pressure of 30 mbar, which had to be taken into account in the blower technology design.
Prior to the modernization of the plant had been done, biological material had been channeled into the basins with a high surplus of oxygen, which was mainly aimed at counteracting the vacillations in the inlet values at the slaughterhouse. But the project targets involved decreasing operating costs and CO2 emissions, which meant that, going forward, the aeration of the basins would have to be correlated a lot closer with the shifting wastewater load and the resulting oxygen requirements. The main step toward accomplishing this involved needs-based speed regulation of the four AERZEN blower units.
More Intelligent Air Supply
.jpg)
Image Credit: Aerzen
The setpoint values are produced by the programmable logic controller (PLC) from the data measured in the wastewater - mostly in the form of ammonium and nitrate concentrations. Furthermore, there is intelligent control of the diaphragm regulating valves. They close gradually when the required oxygen saturation in the water of the corresponding basin has been accomplished. To avoid higher pressure levels and, subsequently, resistance in the pipe, the PLC simultaneously decreases the target pressure.
Otherwise we would destroy energy by means of the diaphragm regulating valves, because with constant pressure regulation, the blowers have to work against the pressure loss caused by the diaphragm regulating valves. With a sliding pressure control, we are now regulating considerably more intelligently and efficiently.
Markus Haverkamp, Project Engineer, Aquaconsult
For the base load supply of the biological material - which requires an alternating circuit of ventilated and unventilated basins with three purification stages - the Hannover-based engineering firm chose, among other systems, a turbo blower from AERZEN.
Turbo Blower for the Base Load
The type AT 150-0.8S-G5 accomplishes an intake volume flow of 4,800 m3 per hour with a nominal motor power of 143 kW at an intake pressure of 1 bar and a final pressure up to 1.8 bar. For Cord Utermann, sales engineer at AERZEN, turbo blowers are a perfect example of energy-optimized base-load machines meant to run 24 hours-a-day within nominal value parameters. This is because they function at the maximum level of economic efficiency.
As with almost any turbo technology, the energy efficiency falls as soon as the machines are driven into the partial-load range.
Cord Utermann, Sales Engineer, AERZEN
Therefore, concepts must be developed to meet the energy-efficient cleaning of dirt loads that differ from high to low throughout a day. For ideal energy efficiency in a wastewater treatment plant, this approach means that the air requirement, beyond the base load, has to be covered by displacement machines such as rotary lobe compressors and positive displacement blowers. These are resilient in high control ranges between 25% and 100% and have good efficiency, also in partial-load operation. Thus, two AERZEN Delta Hybrid (D 62 S) packaged units, and one Delta Blower (GM 80 L), are also part of the compound system in the wastewater treatment plant in Rheda-Wiedenbrück.
.jpg)
Best possible energy supply for the real load profile. Image Credit: Aerzen
New Control System for Energy-Saving Operation - Even in Case of Load Changes
AERZEN has built the AERsmart to guarantee that this quartet does not only provide the essential oxygen for the aeration tanks via a safe process, but also produces the essential air volume in the most energy-efficient way in the compound system. According to Cord Utermann, “The art of the control engineering is to create the transitions between the overlaying operating areas as fluently as possible and as energy-efficiently as possible for each load, i.e. to operate the different machines in combination, and always at the greatest efficiency level.” This occurs when, “every load complies with the actual requirement,” according to Markus Haverkamp. Here, there are, “always upward and downward peaks.”
Since three different machines with diverging efficiencies and operation ranges are used in the wastewater treatment plant in Rheda-Wiedenbrück, their operation must be coordinated in such a way, “that the number of switching operations will be as low as possible, since constantly switching them on and off would increase wear,” the project engineer of aquaconsult reveals. “Efficient air distribution among the aeration tanks (sliding pressure control, intrusion of disturbances as for example NH4-N, amount of water etc.) and efficient machine selection are necessary for an optimal overall efficiency. This is realized using AERZEN’s new control system.”
The oxygen requirement across the three clearance stages is the foundation for the optimization of the control system with the AERsmart control. The indices are processed by the main PLC of the plant and the resulting target pressure is conveyed by Profibus to the blower control. AERsmart then provides for the optimally combined operation of the four packaged units with regard to energy saving. “The turbo blower used here has, for example, the highest efficiency at a capacity of 83 percent,” explains Cord Utermann.
If the air requirement surpasses this value, it may be more efficient to switch off the base-load machine totally and to cover the fairly low air requirement using both Delta Hybrid machines. “Our bacteria do not care where the oxygen comes from,” Hendrik Wulfhorst says with a smile. But the manager of the wastewater treatment plant emphasizes that the blower technology was designed so that the performance of the turbo blower would be adequate for “normal” everyday requirements.
The intermediate result was promising: the waste treatment plant in Rheda-Wiedenbrück realized energy savings of approximately 30% for the treatment of biological material using energy-optimized blowers and a relatively simple process controller that was more closely connected to the real values. AERsmart here provides an extra five-to-eight percent saving because of blower optimizations. How much the overall saving will amount to over a longer operating phase will be made known by the field test in the wastewater treatment plant.
Rheda-Wiedenbrück is the first wastewater plant in Germany trying out the AERsmart under real conditions. “We need the application on site as we can only recognize the complex connections of a wastewater treatment plant in field; this cannot be reproduced on a test bench. This is why the intensive cooperation with our customers is so important, as only this proceeding provides us with a close application reference for future-oriented developments,” summarizes Cord Utermann.
AERZEN Service
AERZEN provides reliable service that guarantees and increases energy efficiency in biological wastewater treatment plants.
Background: Energy and Cost Efficiency for Biological Wastewater Treatment Plants
Every biological wastewater treatment plant requires a compressed air station to supply the oxygen for the aeration tank. But this station will only work at highest energy efficiency if the following is avoided: a downstream increase in system pressure, extreme intake temperatures because of insufficient ventilation, and increased operating hours because of insufficient maintenance. Practical examples show that these criteria impact the energy efficiency of a blower negatively and cause a significant increase in energy costs.
Practical examples show that a pressure increase of, for example, 50 mbar can lead to increased energy consumption of five to ten percent, depending on the design of the blower. This can lead to several thousands of euros in extra costs. (...).
Frank Glöckner, After-Sales-Service
Example: Increased System Pressure Caused by the Downstream System
Every blower is set to a pre-defined pressure prior to leaving the factory. The air compressed to this pressure is then directed to vents distributed all over the tank via a ring line with several stub lines. Diaphragm control valves, properly operated at the tank inlet, are a requirement for ideal operation. Wrongly set valves quickly result in increased pressure in the supply network and the blowers must then be operated against the increased pressure, which results in a rise in energy costs.
Additionally, the diaphragm control valves are controlled via pressure stabilization. This means the supply lines are automatically shut when the necessary oxygen level is reached. The blowers, which are frequently frequency-regulated, are shut-down with a time-lag after the valve is closed. If this delay (waiting period) is fixed too long, the blowers have to work against closed or partly closed valves in full load. This causes air to escape via the pressure valves. Moreover, this does not only cause air losses: in extreme cases an increased counter pressure can also damage blower packaged units.
.jpg)
Image Credit: Aerzen
The counter pressure can also increase when the diffusers in the tank have aged because of chemical compounds in the wastewater. This is also possible when pipelines and/or diffusers have become blocked over time due to the pressure silencers of the pressure generators are cladded with absorbing material which has come loose over time and then entered the system via the network. This issue does not happen in AERZEN displacement blowers built after 1995, or in AERZEN rotary lobe compressors in the Delta Hybrid range. The core of these systems is a pulsation silencer and a reduction in noise is achieved by diverting air, not by using absorbing material.
Example: Excessive Intake Temperatures
The air used for compression and cooling in a blower is frequently taken directly from the place of installation and not supplied through air inlet channels for biological wastewater treatment plants. This means that the room temperature has a great impact on the energy balance of the system. The room temperature increases when the ventilation openings are placed wrongly and/or are too small, if the air supply is not supported by fans controlled via thermostats or if their performance is not adequate, if the roof of the compressor room is not properly insulated against intensive sun radiation, or if the compressed air supply lines within the station are not suitably insulated.
The increase in room temperature also causes an increased compressed air temperature and thus to reduced oxygen levels in the compressed air, a reduced filling level and to inferior cooling of the blowers. All of these factors have one consequence: the compressed air generator has to function longer to generate the required amount of oxygen. As a rule of thumb, one can say that a temperature drop of 3 °C saves 1% of energy. This is one reason why AERZEN blowers always suck in air on the “cold” side of the packaged unit and not on the discharge side with the pipe connection, as on this side there is a higher quantity of radiated heat.
Example: Insufficient Maintenance
If the system is not maintained as per the manufacturer’s instructions, this can also cause a negative effect on the energy balance. Perfect examples are pressure valves damaged by resistances which are very high, or an air filter which was substituted too late. If the air filter is not substituted, but rather removed and cleaned, perhaps to save costs of about 50 euros, the total energy consumption of the blower will in due course increase. As a basic guideline: a 10 mbar reduction in pressure on the intake side lessens energy costs by approximately 1%. Another example: a new filter lessens the pressure by approximately 5 mbar, while a dirty filter causes a pressure decrease of 30 mbar.
Conclusion
Increasing energy costs can be prevented if all blowers are properly maintained and serviced by the service team from the manufacturer and/or the operator. After all, the energy costs of a compressor, viewed in terms of its total service life, make up nearly 90% of the system’s total cost. Just approximately 10% of costs is spent on investment and maintenance.
.jpg)
Image Credit: Aerzen
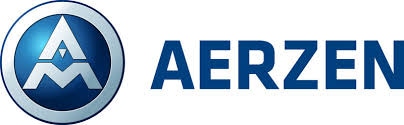
This information has been sourced, reviewed and adapted from materials provided by Aerzen Machines Ltd.
For more information on this source, please visit Aerzen Machines Ltd.