Owing to massive advances in metallurgy over the last 30 years, 21st century steel production is revolutionizing the world and the built environment. Obviously, a huge part of the steel production process is the application of coke, which offers as much as 80% of the furnace’s thermal needs, a big portion of the furnace's CO gas (which serves as a reducing reagent) and carbon for dissolution in the molten metal. As with any other manufacturing process, the quality of the raw materials has an enormous impact on the quality of the final product. It is thus important to ensure the coke is expansively tested.
On a small testing scale, coke can be formed by the slow heating of coking coal in a refractory lined coal testing oven (CTO) to 1000 ˚C for 3 to 4 hours without the presence of air. The coal softens at a temperature of between 400 and 500 ˚C to form a plastic or liquid phase, agglomerates, swells and particles fuse. At temperatures of between 450 and 550 ˚C, there is re-solidification forming semi-coke, which is the first stage of shrinkage. Lastly as the temperature of the raw material in the CTO crosses 550 ˚C, there is a loss of oxygen and hydrogen and the second stage of shrinkage takes place. Using only 7 kg of 5% moisture coal and a Carbolite CTO, a sufficient-sized sample can be created to define % yield and hot strength (CSR/CRI).
For larger testing/pilot plant situations, a movable wall oven, such as that manufactured by Carbolite, can be employed. Holding 227 kg of raw coking coal, this pilot plant mirrors real-world coke production over a basic 18 hour processing time. When the cycle is completed, the contents of the oven are expelled at temperature and quenched with water developing a grey mass of coke.
Testing the Coke
The coke strength after reaction (CSR) test is based on a process developed in the 1970s by Nippon Steel Corporation as an effort to get an indication of coke performance. It refers to the coke’s strength (thermal potential) via a simulated reaction emulating what might be expected in an industrial blast furnace. Those original tests over four decades ago have become an accepted standard for testing coke, mainly when blending coking coal to guarantee it performs to the essential specification.
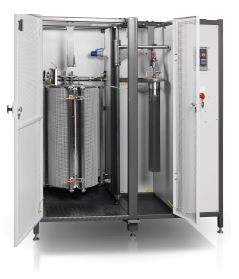
Coke reactivity test unit
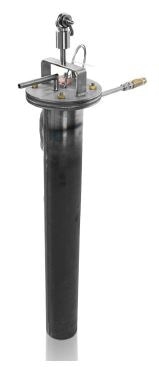
Coke reactivity test resort
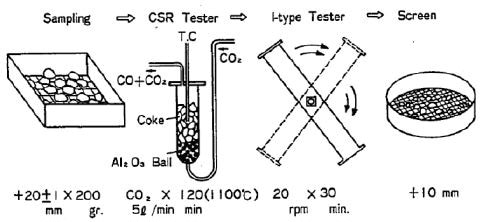
CSR measurement
In the test, a 200 g sample of 20 mm coke fragments are put in a carbon dioxide atmosphere at 1 – 2 bar pressure and then heated at 1100 ˚C for two hours. The coke is preheated and cooled under nitrogen and the weight loss during reaction is measured. The percentage weight loss is measured against the Coke Reactivity Index (CRI) for which the universal standard is ISO 18894 (2006).
The reacted coke is put in an I-tester cylinder chamber and subjected to 600 revolutions in 30 minutes. The percent of carbon material eliminated from the drum that is +10 mm after sieving is the CSR.
This recognized test procedure in a laboratory imitates coke lumps descending in an industrial blast furnace where they are subjected to abrasion as they rub together and against the walls of the furnace in a current of CO2. These two simultaneous processes chemically react with the coke lumps generating an excess of fines that can reduce burden permeability resulting in increased coke requirement rates and lost hot metal production.
A typical coke reactivity furnace (from a manufacturer such as Carbolite) has a highest operating temperature of 1100 ˚C with a controller that meets either the ASTM D 5341-14 or ISO 18894 (2006) standard. Carbolite's furnace has three distinct heated zones with low thermal mass insulation across a 700 mm length. There is also a gas safety system and audible alarms for over- temperature, flame failure and low gas flow. Most significantly, the interior of the dual walled furnace houses an Inconel retort, which is corrosion and oxidization resistant and which allows incoming gas to be preheated.
The Process
Step One
The first operation is to load the tubular shaped retort. The liner in the retort has a perforated base to enable the free flow of gas through the sample, which is made up of small 20 mm pieces of coke weighing about 200 g in total. After the coke sample has been loaded into the retort liner, it is returned to the retort and the thermocouple sheath is placed into the liner and sample before the retort lid is tightly secured.
Step Two
The retort is positioned in the CRI furnace in its parked position, the thermocouple linked and the retort tethered to an earth connection. The retort can then be linked to the gas supply pipe at which time a nitrogen purge automatically using the mass flow control with pre-set alarms and complete data logging and charting of the gas purge.
Step Three
Once initially purged with nitrogen, the retort can be linked to the lifting arm, the safety gates closed, and the CRI testing arrangement can start after the flame failure unit has been started. It should be noted that the safety flame is automatically ignited via an electrical spark and is optically checked by a flame failure detection unit. This flame is important to guarantee that any deadly gas exiting the retort during the testing phase will be burnt. All that is left for the operator to perform is to press the cycle start button and the furnace will heat to an even 1100 ˚C.
Step Four
Once the furnace has attained 1100 ˚C, an alert will sound and the retort can be loaded into the hot furnace. The safety gates are opened, the top insulation plug is taken off and then the retort is freed from its parked position and swung over towards the split tube furnace, which is briefly opened to accept the retort before the split tube is clamped shut and the safety cage closed once again, and the key process starts. As soon as the exact nitrogen purge conditions are re-confirmed, carbon dioxide flows automatically and the nitrogen purge of the retort ends. The observer will note that the flame size grows as a result of the carbon dioxide flow.
Step Five
At the end of the test process, an intermittent siren can be heard along with a warning lamp. The test operator can then open the doors of the safety cage, unclamp the split tube furnace, and return the retort to its parked position to cool.
Step Six
Once totally cooled, the coke sample can be eliminated from the retort liner. It is crucial to guarantee that the retort is completely cooled before trying to recover the coke sample.
Step Seven
The coke sample has been heated in CO2 for two hours in the split tube furnace and can presently be moved to the CSR I- Tester. This unit has a tumbler on which the number of revolutions is preset but which can be easily altered by the operator. The standard arrangement will result in the tumbler rotating 600 times at a constant 20 RPM over a 30 minute cycle time before it stops and the vessel should be taken away from the tumbler. The lid of the tumbler vessel can presently be removed, the retort extracted, and the resulting final sample poured from the retort to enable the CSR measurement to finally be made.

Moving wall coke oven discharging
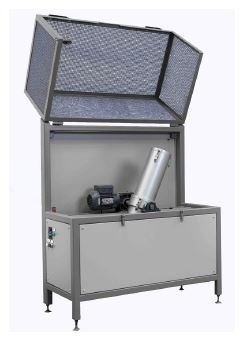
Tumbler test for coke
Conclusion
This whole seven step process may seem intricate or complicated but it is a well-proven process that delivers accurate results of the performance of any particular coke sample with a high CSR signifying a strong coke.
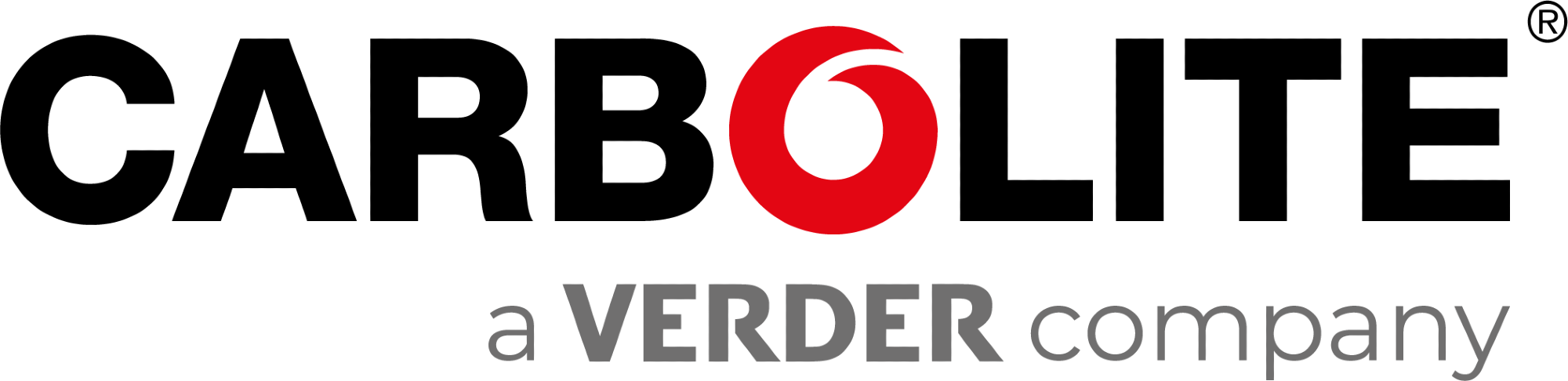
This information has been sourced, reviewed and adapted from materials provided by CARBOLITE.
For more information on this source, please visit CARBOLITE.