Active or passive technology can be used to isolate vibrations from equipment. By employing active techniques, opposite but equal forces are created electronically via actuators and sensors to cancel out any unwanted vibrations. Using passive techniques, isolation is attained by limiting the ability of vibrations to be coupled to the item to be isolated.
This is achieved by utilizing a mechanical connection which redirects or dissipates the energy of vibration prior to it getting to the item to be isolated. Passive techniques sometimes entail using electromechanical controls for adjusting the system, but the isolation mechanism itself is passive.
Passive systems may utilize springs, fluids, elastomers, or negative-stiffness components, and they typically cost less than active systems. Their relative simplicity makes them more safe and reliable.
Simple Spring Vibration Isolation
A spring placed between the surface transmitting vibration or shock and the item to be isolated is one of the most basic passive isolators. The spring opposes the impulse on it and absorbs some energy as it deforms. For damping, an elastomeric or fluid element is added to the spring element.
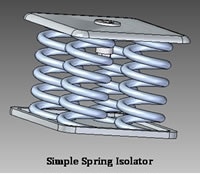
One simple example is a car’s shock absorber. In this instance, mechanical energy from the vibration or shock works on the fluid and is converted to thermal energy in the fluid, decreasing the amount of energy transmitted to the body of the car.
Elastomer Damping Vibration Isolator
Elastomers are rubber-like materials which, by deforming, absorb mechanical energy. Examples of elastomeric isolators are vibration and shock mounts for building foundations, aircraft components, industrial machinery, and automobile engines.
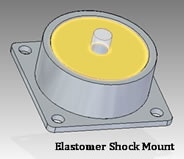
Isolation may be much better in one axis than the others, as rubber does not possess the same characteristics in all directions. The most sophisticated passive isolators utilize negative-stiffness or air technology.
In advanced technology applications such as microscopy (including SPM, SEM, etc.), interferometry, micro-hardness testing and nano-fabrication, the best passive vibration isolation devices permit the instruments to perform at their best.
Air Table Vibration Dampening
Pneumatic systems support a platform or heavy table on compressed air pistons, which supply the decoupling link between the table and the ground, i.e. the table floats on the air.
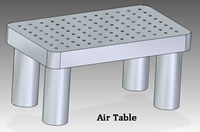
The most sophisticated air tables can be quite expensive, but do a good job of isolating floor vibrations at small amplitudes. While they isolate in a passive manner, they need a leveling system, an air supply, and associated controls and maintenance.
The less sophisticated air systems do not isolate well at the low frequencies which are handled so well by negative-stiffness systems, or in all directions. Problematic ambient vibration can be caused by the air supply system for pneumatic isolators. Using electrical techniques for controlling air cylinder pressure and leveling the table adds to the complexity and potential for failure.
Negative Stiffness Vibration Isolator
For sensitive instrumentation at low frequencies and amplitudes of floor and building vibrations, negative-stiffness isolators supply a reliable, simple, and highly effective isolation solution. They are relatively small, stable, lightweight, and cost-effective.
Negative-stiffness isolators from Minus K are fully mechanical, and an optional electronic auto-adjust system is available for special applications. Isolation is acquired using an arrangement of springs and negative-stiffness mechanisms. These systems supply isolation in 6 degrees of freedom with resonant frequencies as low as 0.5 Hz or lower.
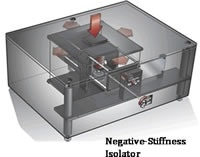
Isolation begins around 1 Hz and is around 50 to 100 times better than most high-performance air tables in the 5-10 Hz range for a 0.5-Hz system, which is crucial in buildings. With respect to vibration, a number of isolators can be combined while still acting as one, which enables great versatility in designing for a variety of applications.
Minus K's negative-stiffness technology has been implemented successfully for sensitive instrumentation loads from a few pounds to many tons. The isolators are simple to adjust and use. They can take up less space than air systems, be more economical, supply better isolation at very low vibration amplitudes, and need no maintenance.
Typically, negative-stiffness systems are not designed to handle large angular changes and shock loads like those that happen in vehicle or aircraft applications. The Minus K devices can be utilized selectively to greatly enhance the performance of sensitive instruments during operations in aircraft or vehicles.
Both negative-stiffness and pneumatic systems can be sensitive to temperature adjustments but can be modified to compensate. Negative-stiffness systems can be modified to be utilized in a vacuum chamber or clean room easily, but in this environment, air systems are prone to difficulties.
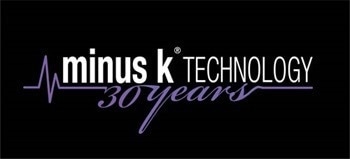
This information has been sourced, reviewed, and adapted from materials provided by Minus K Technology.
For more information on this source, please visit Minus K Technology.