Almost all semiconductor devices are formed of heterostructures, which are stacked layers of distinctive materials deposited using distinctive techniques. These layers have a thickness in the range of micrometers down to almost singular atomic thickness. The electronic configuration at layer interfaces plays a vital role in the accurate operation of an electronic device. Although it is possible to simulate the electronic characteristics of such interfaces, various physical effects brought about by the deposition process and layer interactions have an impact on the interface in a specific and often unpredictable manner.
This article presents a robust way of carrying out an in situ analysis of heterostructure interfaces with an organic solar cell structure as an example. The technique and the study presented in this article were developed and carried out by Saive et al.1. Electrical characterization of interfaces has been performed by Scanning Kelvin Probe Force Microscopy (SKPM). Similar to a traditional Kelvin probing system, the SKPM technique offers information related to the work function (chemical potential) difference between the sample surface and a sensing tip.
.png)
Sample after preparation by focused ion beam (FIB)
In the case of SKPM, an atomic force microscope (AFM) tip is used as a Kelvin probe sensor, which enables the measurement of changes in work function with exceptionally high lateral resolution, and down to the atomic level in certain cases. The inherent potential of a material, the electronic configuration such as carrier type and density, and an ultimately applied electrical potential govern the work function. An SKPM measurement on the cross-section of a heterostructure leads to absolute measurements of differences in work function between the different layers. This also allows the direct measurement of the drop in voltage between the different layers upon applying an external voltage across the heterostructure.
Since the surface of an organic semiconductor is highly sensitive to air exposure, these semiconductors must be enclosed in airtight containers. High-resolution electrical characterization mandates the exposed surfaces to be protected from air contamination. The combination of the Carl Zeiss AURIGA crossbeam workstation and the Carl Zeiss AFM option for MERLIN enables the solar cell to be prepared and investigated without the need to expose the prepared structure to air.
The high-capability zoom of the SEM ensures that the AFM tip is directly navigated to the region of interest with precision. Thus, information related to the mechanical, topographical, electrical and magnetic properties of the surface can be obtained at nanoscale resolution.
.png)
AFM micrograph showing the 3D topography of the cut-out section
SEM-AFM
What is the need to develop a combined SEM-AFM? When compared to the two systems, a combined SEM-AFM has various advantages as stand-alone.
The system provides innovative possibilities for the measurement of nanostructures and surfaces. The SEM and AFM combination enables accurate positioning of the AFM tip. The AFM offers precise information related to the electrical, topographical and mechanical properties of the surface.
.png)
.png)
Applications
- Analysis of surface properties such as:
- Chemical surface potential by Kelvin Probe Force Microscopy (KPFM)
- Magnetic force on the surface of the sample
- Conductivity of the surface
- And much more
- Potential difference between the two electrode materials
- Potential distribution along the layer structure of an SMD capacitor
- Graphene and other 2D materials
- Electrical and topographical properties
- Characterization of:
- Energy storage
- Heterogenic structures of nanosized devices and functional structures in semiconductor
- Sustainable energy production
Hardware Integration
The technique for achieving a combined SEM-SPM system is dependent on the integration of a vacuum compatible SPM into current SEM systems. This combination was chosen to achieve the highest usability and performance of the system. Another advantage of this approach is that it is possible to optimize current SEM systems to a combined SEM-SPM system. In both cases, the function of the SEM will not be limited, thereby enabling combined SEM/SPM measurements.
The SPM is designed like a sample scanner for integration. This design allows highest precision alignment of the SPM tip and the electron beam as the tip and the beam are not moved against each other. Even at the time of SPM scanning, this allows unknown probabilities of combined measurements. Moreover, this framework has the ability to realize the highest performance in terms of frame rate and resolution. The scan unit itself is the next advancement step of the SemiLab STM scanner, famous for high reliability and stability in the past few decades. With a possible sample size of 10 mm and a scan volume of 9 µm × 9 µm × 1 µm, the claim of the design for high resolution is clearly evident. Electronic components such as the detector, the laser diode and the preamplifier are positioned inside the vacuum chamber in hermetically encapsulated compartments. The exchange of the cantilever and the sample as well as the alignment of the laser path can be carried out without breaking the vacuum. The SPM tip can be positioned to the area of interest and the SPM can be positioned with respect to the SEM with the help of a remote control. A UHV-compatible version can be availed by making very few changes to the SPM.
.png)
Software Integration
The grade of functionality of highly complex scientific instruments such as the SEM-AFM is based on the operating software. A single-software user interface is mandatory to realize the seamless integration of the techniques. The open design of our SPM Software ScanTool™ enables the integration of a self-designed SEM operating software. Hence, the operator can control both the systems from a single platform and the same software without the need to click through a network of tabs and windows. The view on all settings and image data of both techniques is accessible and unblocked. The software has been developed for the highest workflow and throughput. Simultaneously, program functions such as the DME Automator offer access to all functions of the SEM-AFM system, thereby enabling user-designed advanced measurement routines to be designed and performed. Hence, automatically running measurement routines can be created for acquiring comparable data from different regions of the sample. Image data from SEM and SPM are investigated in the ScanTool™ software. There exist standard analyzing tools, and more specialized or advanced analysis procedures can be executed by the company, or executed by the company based on customer demand, through the “DME Automator” or “DME Image Calculator.”
.jpg)
Features
- The SEM-AFM system is based on the DME UHV AFM and the Carl Zeiss Auriga® Crossbeam Workstation.
- Highly stable scan unit developed for 3D single-atomic resolution.
- Single-software interface for both SEM and AFM components.
- The crossbeam point of SEM and FIB lies at the cantilever tip. The design as a sample scanner enables performing combination measurements of all three techniques at precisely the same point on the sample and in space.
- SEM viewing angle of 0°–85° while maintaining a minimum SEM working distance of 5 mm.
- Scanner specification: scan range (x,y,z) 10 µm × 10 µm × 1 µm, real resolution subatomic in all three dimensions.
- Ability to reach the cantilever tip and the sample by FIB in 0° and 54° position, in situ tip sharpening by FIB supported
- Automatic laser/detector alignment on cantilever change
- Common data storage of AFM and SEM images
- Supports all common AFM operation modes
- Supports easy exchange between AFM and standard Auriga® functionality by user-exchangeable SEM door
- Ability to update prevalent Auriga® SEMs to BRR functionality by simple door exchange
- Unlimited functionality through the use of all standard AFM cantilevers, without the need for active probes
References and Further Reading
1. Rebecca Saive, Michael Scherer, Christian Mueller, Dominik Daume, Janusz Schinke, Michael Kroeger, Wolfgang Kowalsky, Imaging the electric potential within organic solar cells, Advanced Functional Materials Volume 23, Issue 47, December 2013, Pages 5854-5860.
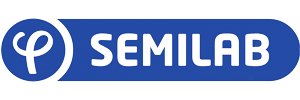
This information has been sourced, reviewed and adapted from materials provided by Semilab Semiconductor Physics Laboratory.
For more information on this source, please visit Semilab Semiconductor Physics Laboratory.