The PAEK (polyaryletherketone) group’s matrices in thermostatic composites have garnered attention over the past decade. Toray’s Cetex® thermoplastic product range features PEEK and PEKK based composites, which are among the best materials in mechanical performance, chemical, and heat resistance available on market.
An engineered PAEK based composite is now joining Toray through Toray Cetex® TC1225, which combines the high service temperature and excellent mechanical and chemical properties of other PAEK family materials with lower processing temperature and extraordinary processing characteristics. Toray Cetex® TC1225 is available in a high-quality UD tape, fabric strengthened prepegs, and fabric strengthened thermoplastic laminates.
Tape Quality is an Important Consideration
The expanding use of thermoplastic composites in large parts and challenging industries such as primary and secondary aircraft structures leads to a demand for materials that are fit for large-scale production and process automation.
.jpg)
Figure 1. A cross section photo showing a Toray Cetex® UD tape. Image Credit: Toray Advanced Composites
Because of this, it is important that the necessities are met in the UD materials that are used; uniform fiber and resin distribution and a very low void content. The production processes by Toray accomplish a high-quality tape that is superior in respect to the market in these aspects and ensures reproducible results.
Toray Cetex® UD Tapes
- Uniform fiber allocation
- Level resin distribution around the fibers
- Low void content
- Low tension in tape
- Constant quality
Processing of Toray Cetex® TC1225 UD Tape
The Toray Cetex® TC1225 UD tape, based on an engineered resin system from the PAEK family, is a Toray offered material that distinguishes itself in the flow properties of the resin and is consistent with the aforementioned process automation operations.
.jpg)
Figure 2. Press consolidation provides a robust and proven baseline process. Image Credit: Toray Advanced Composites
A good bond between the different layers of laminate is ensured by the low melt viscosity of the resin, while the product’s mechanical abilities remain equal to other PAEK family-based composites such as PEEK and PEKK. This in combination with the comparatively low processing temperature of the UD tape aids in accelerating the production process.
.jpg)
Figure 3. State of art. Toray Cetex® TC1225 books good results in a fast vacuum-aided oven consolidation process. Image Credit: Toray Advanced Composites
While composite parts from UD tapes are frequently press consolidated, or autoclave consolidated, TC1225 attains excellent results in vacuum aided oven consolidation. Autoclave independent processing is seen as a next generation process and has great potential to reduce processing time, costs, and energy usage by a substantial amount.
.jpg)
Figure 4. Nearing the ultimate goal: Toray Cetex® TC1225 books promising results for full in situ tape placement. Image Credit: Toray Advanced Composites
In the event that a product needs to be formed in a secondary operation, Toray Cetex® TC1225 offers the option of shortening processing times even more due to its lower processing temperature. This is comparable to the savings made with the same resin system in reinforced thermoplastic laminates.
.jpg)
Figure 5. Micrograph after tape placement and oven consolidation.Image Credit: Toray Advanced Composites
.jpg)
Figure 6. Micrograph after in situ tape placement at deposition rates >200mm/s. Image Credit: Toray Advanced Composites
Processing Toray Cetex® TC1225 Reinforced Thermoplastic Laminates
Companies looking to combine the optimum in material properties with a reduced processing temperature can find their solution in Toray’s fabric reinforced Cetex® TC1225.
The TC1225, based on the same engineered PAEK matrix material, enables processing with temperatures between 50 and 75 °C (122 to 167 °F) lower than PEEK, but with comparable mechanical and chemical properties and even a similar glass transition temperature. The glass transition temperature dominates the service temperature of a part, while the crystallization temperature dominates the processing temperature.
.jpg)
Figure 7. TC1225 offers benefits in with a lower processing temperature range while maintaining a high Tg. Image Credit: Toray Advanced Composites
One thing many PAEK family materials share is the need to be processed in high temperature equipment and might need high capital investment in machinery and tools. This requirement can be deterring to companies already equipped to process other high-heat thermoplastic composites, such as PEI and PPS. TC1225 has a lower processing temperature, which reduces the heating and cooling cycle, thereby saving time and energy costs.
.jpg)
Figure 8. A lower processing temperature results in a shorter production cycle. Image Credit: Toray Advanced Composites
Where semi-impregnated prepregs are utilized instead of consolidated laminates, Toray Cetex® TC1225 low melt viscosity resin system will combine faster and reduce the cycle time in comparison to PEEK or PEKK materials.
Overmolding Toray Cetex® TC1225
As a result of the last year’s tradeshows and online attention, Toray Cetex® TC1225 has gained substantial attention as a perfect material for overmolding purposes. Overmolding of a continuous fiber part made from Cetex® TC1225 with a filled or non-filled PEEK resin leads to a superior bond, due to the difference between the melt temperatures in the two materials.
A grid stiffened panel demonstrator created within the scaffold of the COMPeTE project that Toray supported displays the opportunities of combining the design freedom of an injection molded product with the exceptional mechanical properties of a continuous fiber reinforced laminate.
.jpg)
Figure 9. Grid stiffened panel. Image Credit: Toray Advanced Composites
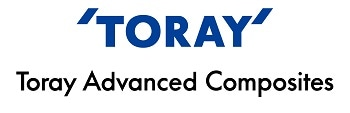
This information has been sourced, reviewed and adapted from materials provided by Toray Advanced Composites - Aerospace.
For more information on this source, please visit Toray Advanced Composites - Aerospace.