As one aspect of a Dutch innovation program called TAPAS 2 (Thermoplastic Affordable Primary Aircraft Structures 2), NRL has created a technique to produce large and thick thermoplastic composite parts using Advanced Fiber Placement (AFP).
Automated Production of Large and Thick Thermoplastic Composite Aircraft Parts
.jpg)
The part is created using Toray Cetex® TC1320 C/PEKK uni-directional tape and is six meters long and 28 millimeters thick. Replacing a steel upper spar with a pylon upper spar made of composite lets aircraft manufacturers minimize production costs and weight, thereby saving on aircraft fuel consumption.
NLR laid extended thermoplastic tracks alongside each other using its sophisticated fiber placement machine and subsequently ‘fused’ them to create a pylon upper spar in Fokker’s autoclave. As a result of using AFP, the ‘buy-to-fly ratio’ of the material is high, because locale build-ups are capable of being created without scrap edges.
Recyclable
The production of a composite pylon upper spar is more sustainable than manufacturing a structure that contains steel. The cutting does not leave much residual material and the leftovers that do arise are recyclable.
In addition, the pylon upper spar itself is also capable of being fully shredded and reused at the last part of its service life. The method developed by NLR is also appropriate for other aircraft parts, such as wing spars, stabilizer spars, and floor beams, and there are additional applications outside the aviation sector.
Toray Cetex® TC1320 C/PEKK Uni-Directional Tape
- Resilient towards solvents and chemicals
- Good impact resistance and toughness
- Low moisture uptake, good hot or wet strength retention
- Flame retardant
- Good density after impact performance
Toray Cetex® C/PEKK uni-directional tape is appropriate for automated fiber placement, which, combined with exceptional mechanical properties, allows for the efficient automated manufacture of a high-performance aerospace structure.
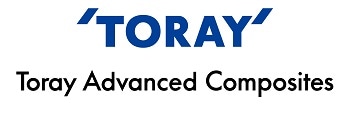
This information has been sourced, reviewed and adapted from materials provided by Toray Advanced Composites.
For more information on this source, please visit Toray Advanced Composites.