This is the final article in a three-part series on a novel nanoelectrical imaging technique that goes beyond a 2D map, and produces a correlated nanomechanical DataCube and comprehensive electrical DataCube.
Case Study: DataCube Scanning Microwave Impedance Microscopy (DCUBE–sMIM) on Delicate Samples
In the sMIM approach, a microwave signal reflected from the interface between the tip and the sample retains information of the electrodynamic characteristics of the sample surface beneath the tip apex.8 Real-time detection and processing of the reflectance enable sMIM to directly access the material’s conductivity and permittivity. When an AFM-type sMIM probe is scanning across the surface of the sample, sMIM has the potential to image the differences in capacitive (sMIM-C) and resistive (sMIM-R) characteristics. This method of detection eliminates the necessity for making electrical contact between the substrate and the sample, since sMIM is predicated on the capacitive coupling between the sample and the tip.
When the sample is AC-biased, sMIM also offers carrier profiling (dC/dV) capability akin to conventional SCM. Likewise, it exclusively enables the mapping of nonlinear resistive characteristics (dR/dV).
With both AC and DC sMIM signals, sMIM can be used for analyzing surfaces with channeling composition and across a wide dynamic range, for instance, insulating, semiconducting, and metallic domains. As a near-field technique, the sMIM’s resolution is restricted by the probe’s tip radius and it can effortlessly realize less than 30 nm lateral resolution for electrical mapping. Sub-aF sensitivity and high signal/noise ratios are realized by using waveguide tips with coaxial shielding.
When integrated with PeakForce Tapping mode, sMIM results can be obtained on fragile samples like carbon nanotubes and, at the same time, mechanical sample characteristics such as adhesion and modulus8 can be achieved. Using DCUBE-sMIM, the same properties can be acquired at an array of sample voltages, in a single scan, and the “full picture” can be obtained.
Doped Si Device
Figure 9 illustrates an example of DCUBE-sMIM, collected on a set of doped Si devices. Furthermore, the adhesion map is directly extracted from the force-distance spectra existing in every pixel and, for instance, can be used for detecting contamination. Both dC/dV-V and C-V spectra were collected in every pixel, leading to C, dC/dV phase, and dC/dV amplitude maps for voltages ranging from −2 V to +2 V. As an example, the dC/dV amplitude voltages at certain discrete sample voltages are shown, demonstrating how the observed contrast differs strongly with the applied voltage and the type and concentration of a carrier.
.jpg)
Figure 9. DCUBE-sMIM data acquired while ramping the sample bias from −2 V to +2 V. As an example, slices of the dC/dV amplitude data-cube at selected voltages are displayed and show voltage-dependent contrast for some regions. Adhesion and height are measured simultaneously and also displayed.
Si with Staircase Carrier Profile
Typical data obtained from a DCUBE-sMIM study is illustrated in Figure 10. In this case, a Si sample with a p-type and n-type staircase carrier profile was used; this creates a candidate sample for quantifying AFM-based carrier profiling techniques.32 The R-V spectra (sMIM-R versus sample bias) and the C-V spectra (sMIM-C versus sample bias) were obtained within 100 ms for each pixel, covering a bias range of −2 V to +2 V. The presence of images over this bias range helps in differentiating and identifying all carrier regions and levels in the sample.
This can be observed in the sMIM-C data illustrated in Figure 10a–c. As shown in Figure 10a, the negative bias pushes the p-type regions into the depletion regime, improving their contrast. While the n-type regions are in the inversion regime depressing their contrast, the positive bias shown in Figure 10c has the reverse effect. This information is combined in one spatio-spectral slice, as shown in Figure 10g.
.jpg)
Figure 10. DCUBE-sMIM study of a Si sample with n-type and p-type staircase carrier profile: (a)–(c) “sMIM-C” capacitance image slices at selected sample biases; (d)–(f) 11 spectral sets of force, sMIM-R, and sMIM-C, respectively, collected at user-selected positions marked on (b); (g) slice image representing the sMIM-C signal versus sample bias and X position at a fixed Y location.
DCUBE-sMIM offers useful nanoelectrical data both during the surface hold time and during the “approach” and “retract” processes. This can be seen in Figure 10d–f, which are spectra acquired at the locations labeled by X in Figure 10b. Firstly, during the hold time, the sMIM-C signals indicated in Figure 10e display a slow change in slope with carrier density. A majority of the curves were taken in the p-type region.
The sample — at negative bias — is in the accumulation regime, leading to a similarly high sMIM-C signal, which reduces subsequently as the bias becomes positive and the sample goes into the depletion regime. For lower-doped regions, the signal reduces further. Secondly, as shown in Figure 10e and 10f, the sMIM signals are also captured before the probe touches and before the application of the bias, thereby automatically capturing the distance dependence.
Tip-shape information is extracted by fitting the sMIM-C versus distance spectra. The capacitance image can be easily extracted at a specified, fixed height over the sample. This image indicates the stray capacitance or “background” and can be deducted from all capacitance data to eliminate the background effects. This improves the sMIM-C data, eliminates the effects of any stray capacitance, and offers a method for quantifying the sMIM-C data.
Comprehensive analysis and comparison of the sMIM signal at the time of the “extend” and “retract” period also offer more data. For instance, asymmetric behaviors specify a change in the surface of the sample following the dwell period.
Maghemite (γ-Fe2O3)
An instance of a DCUBE-sMIM analysis of a γ-Fe2O3 sample is shown in Figure 11, in which the electrical conditions were constantly maintained during the measurement and the sMIM signals were determined over time during the dwell period. γ-Fe2O3 spindle-like nanoparticles (100 x 500 nm in size) deposited into a continuous film is illustrated in Figure 11a. Figure 11b shows the related adhesion map obtained from each force ramping cycle.
.jpg)
Figure 11. DCUBE-sMIM study of a γ-Fe2O3 sample: (a) surface topography, (b) quantitative adhesion map, (c) a slice of sMIM-C from the DCUBE results, and (d) a slice of sMIM-R from the DCUBE results.
This sample exhibits conductivity inhomogeneity across the surface and has been utilized as a reference sample in conductive AFM modes, as shown in Figures 3 and 4. The sample’s local impedance differs across the surface of the sample and reveals contrast on the sMIM-R and the sMIM-C channels, as indicated in Figures 11c and 11d. sMIM-C spectra at locations with varied dielectric constants are shown in Figure 11e.
The sMIM-C signal shows the predicted increase as the probe nears the surface. The sMIM-C signal suddenly increases after the snap-in contact at approximately 8 ms. Afterward, as the tip indents into the sample or the force increases to <1 ms, the area of tip-sample interaction interface increases, leading to an additional signal increase. The sMIM signals are detected for 50 ms during the dwell time, whereas all electrical conditions are kept unchanged, making it possible to average over a comparatively extended period and realize excellent signal/noise ratios in the sMIM maps.
Case Study: DataCube Piezoresponse (Piezoforce) Microscopy (DCUBE-PFM) on Piezoelectric Films
When voltage is applied to piezoresponsive materials, they experience mechanical deformation. The characteristics of piezoresponsive materials make them handy in many different applications, ranging from biosensors to microelectromechanical systems (MEMS). As a subset of piezoelectrics, ferroelectric materials have certain beneficial functional characteristics. With a continuous improvement in process control and the more common fabrication of tiny volume ferroelectrics, scientists have found that the physical properties of these materials change as they reduce in size.
PFM allows topographical imaging and high-resolution nanoscale characterization of piezoresponsive materials. It is a contact AFM method used for determining the displacement of a sample in response to an applied AC bias. The ensuing cantilever deflection of the probe that remains in contact with the sample is identified and subsequently demodulated by using a lock-in amplifier in such a way that ferroelectric and topography domains can be concurrently imaged with high resolution.
In addition, the PFM technique has been extensively used for ferroelectric switching and domain writing studies.33–35 When combined with the data cube method, the DCUBE-PFM technique allows concurrent acquisition of nanomechanical mapping and PFM phase/amplitude spectra in each pixel, demonstrating the switching behavior of every individual domain in one data set. DCUBE-PFM also overcomes sample damage, artifacts, and difficulties of data analysis related to the traditional contact mode-based method.
An instance of DCUBE-PFM studies of a BiFeO3 (BFO) piezoelectric film is illustrated in Figure 12. In this kind of experiment, the sample voltage is increased from −6 V to 0 V at the time of the dwell period while acquiring the PFM phase and amplitude signals. The surface topography is shown in Figure 12a, indicating a flat film with 0.37 nm roughness.
.jpg)
Figure 12. DCUBE-PFM studies of a BiFeO3 (BFO) piezoelectric film: (a) height; (b) PFM amplitude image; and (c) 50 of the selected 110 spectra along a 1.2-μm long line as indicated in (a) and (b), crossing multiple domains in a BFO ferroelectric sample; (d) and (e) plots of those 110 spectra show both PFM amplitude and PFM phase vs bias during a ramp from −6 V to 0 V; (f) map of switching voltages extracted from the data cube.
At −4.5 V, a PFM amplitude slice distinguishes different piezoelectric domains, as shown in Figure 12b. Shown in Figure 12c is the initial 50 of the chosen 110 spectra along a long line of 1.2 μm, as represented by the white-dashed lines in Figure 12a and 12b, crossing various domains in this BFO ferroelectric sample. Such spectra denote clear switching voltages among varied domains as the minimum of every spectrum spreads from approximately −5.0 V to −2.0 V, as shown in Figure 12c. Switching voltages like these can be obtained for every single domain by spectral analysis.
Color plots of those 110 amplitude and phase spectra are shown in Figure 12d and 12e, respectively. The sudden variations in color along the direction of the voltage (vertical) indicate the locations of the switching voltages. Additional analysis of the data cube makes it possible to extract the switching voltage at each pixel. The switching voltages can be plotted in a fresh map (Figure 12f), demonstrating that mixed piezoelectric characteristics are present not only between the domains but also within certain single domains.
The same data cube results are presented in Figure 13 but in a different format. Two sets of amplitude and phase spectra extracted from two domains are shown in Figure 13a and 13b, respectively. Sample biases for the increased phase spectra and the least amplitude spectra denote the switching voltages for the matching pixel on the XY plane. The amplitude and phase data cubes are shown in Figure 14c and 14d, respectively.19 X and Y — the horizontal directions — correspond to the sample’s scan area, which measures 1 x 1 μm2. Z is the vertical direction from bottom to the top and follows the time of the hold segment while the sample bias was applied linearly from −6 V to 0 V. The cube’s size is 128 x 128 x 833 pixels.
All the four horizontal planes match with the slices of phase or amplitude at varied sample biases. In order to better demonstrate the domain boundaries, the center slice in the phase cube is indicated as a series of contours over the range of values emerging at this sample bias. Phase or amplitude changing over the sample bias, or Z direction, along a couple of line positions in the XY plane are represented by the two vertical slices along the XZ direction. Slices of amplitude at varied sample bias, obtained from the data cube, are shown in Figure 13e–13i.
.jpg)
Figure 13. DCUBE-PFM studies of a BiFeO3 (BFO) piezoelectric film: (a) two sets of amplitude spectra from two different domains inside the red circles in (f) and (h); (b) corresponding phase spectra to those in (a); (c) and (d) are cubes of the amplitude and phase data, respectively. X and Y correspond to the 1 μm x 1 μm scan area. The vertical direction, Z, from bottom to the top, is the sample bias from −6 V to 0 V. The cube color represents the amplitude or phase in the cube space, i.e., the measured PFM signal at a specific XY location and applied bias. The cube size is 128 x 128 x 833 (or 1 x 1 μm2 x 6 V). The four horizontal planes correspond to the slices of amplitude or phase at different sample bias. The middle slice in the phase cube is shown as a set of contours over the range of values appearing at this bias. The two vertical slices along the XZ direction represent amplitude or phase changing over the sample bias (Z direction) along two line positions in the XY plane. (e)–(i) are slices of amplitude at different sample bias and (j)–(n) are slices of phase at different sample bias.
Case Study: DCUBE — Contact Resonance (CR) PFM on a LiTAO3 Sample
In PFM, the applied AC bias of a specific frequency leads to a periodic AC deformation of the surface of the sample at the same frequency. In the PFM approach, operation at or close to the contact resonance has been exploited to offer improved piezoelectric response signal.36,37 The implementation of this method is rather limited for a single-frequency, PFM measurement because the contact resonance moves not only with the nature of the tip-sample contact but also the sample material properties.
This problem is resolved with DCUBE-CR PFM, where the frequency is swept to obtain a complete contact resonance spectrum during the dwell period. This hybrid mode retains all the benefits of the FASTForce Volume Contact Resonance (FFV-CR) mode developed for characterizing viscoelastic mechanical characteristics5:
- It is possible to perform frequency sweeps across a wide range (around 5 MHz) allowing simultaneous observation and tracking of various eigenmodes
- It is possible to extract quality factor and resonance frequency with a real-time fit of the spectrum, and the same can be computed into loss tangent, storage modulus, and loss modulus when the proper mechanical model is applied
- Modulus, stiffness, and adhesion are extracted from the force-distance spectrum
- Piezoelectric characteristics can be obtained from the amplitude and phase signals, specifically at the resonance frequency
Some standard DCUBE-CR PFM force ramping, PFM phase, and PFM amplitude spectra of a LiTaO3 (LTO) sample are shown in Figure 14a to 14c. In a measurement like this, the frequency was increased from 250 to 400 kHz in each pixel during a dwell period of 100 ms.
.jpg)
Figure 14. DCUBE-CR PFM studies on a LiTaO3 sample: (a)–(c) typical DCUBE-CR PFM force ramping, PFM phase, and PFM amplitude spectra, respectively, frequency swept from 250 to 400 kHz during the 100 ms dwell period; (d)–(e) visualization of the phase and amplitude data cubes, respectively, where XY are the scan area and z is the frequency sweep. Size is 3 x 3 μm2 x 150 kHz, and the pixel density is 256 x 256 x 260. Horizontal planes show phase or amplitude maps at specific frequencies. Vertical planes are phase or amplitude changing over the sweep frequency. (f) Surface topography, at scan 1 x 1 μm2 scan size; (g) number of valid solutions found for the characteristic equation from which stiffness and damping are determined; (h)–(i) maps of contract resonance frequency, amplitude, and quality factor found upon fitting the hold sweep spectra.
The phase and amplitude data cubes are respectively shown in Figure 14d and 14e.19 The space pixel density and the size of these two cubes are 256 x 256 x 260 and 3 x 3 μm2 x 150 kHz. Figure 14d and Figure 14e indicate the horizontal planes showing phase or amplitude maps at particular frequencies, respectively, where varied piezoelectric domains are suitably differentiated at and close to the contact resonance. Vertical planes are phase, as indicated in Figure 14d, or amplitude, as shown in Figure 14e, changing with the sweep frequency, which shows shifts in the contact resonance frequency between varied domains. The DCUBE-CR PFM data on the same LiTaO3 sample with a tinier scan size of 1 x 1 μm2 are shown in Figure 14f–14j.
The surface topography with a roughness (Rq) of approximately 1.5 nm is shown in Figure 14f. Figure 14g depicts the number of peaks detected by the algorithm during the fitting. This signal becomes zero at the domain boundaries and in certain contaminant positions, suggesting that the material does not exhibit piezoelectric response. Figure 14h to 14i respectively shows “CR Frequency,” “CR Amplitude,” and “CR Q” channels that are maps of contact resonance frequency, amplitude, and quality factor detected when the hold sweep spectra are fitted. This example shows that DCUBE-PFM along with contact resonance offers complete benefits of DCUBE-PFM with the additional advantage of providing a frequency ramp at each pixel, thus offering the peak sensitivity and a full spectrum at the contact resonance.
Conclusions
This article has shown how DCUBE-based nanoelectrical modes offer a general big data approach with the capability to provide novel information in an array of applications, particularly on highly complex samples. The extraction of spatio-spectral slices, image slices, or spectra at each pixel presents new opportunities to reveal sample characteristics that are easily missed or not accessible in traditional nanoelectrical modes, in which images at just one or a few discrete settings can be obtained. Table 2 shows the positive comparison of DCUBE modes to both contact and PeakForce Tapping modes.
Table 2. DCUBE-based electrical modes are compared to contact mode and PeakForce Tapping–based electrical modes.
|
Contact Mode |
PeakForce Tapping |
DataCube |
Samples |
Challenging on soft and fragile sample |
All samples |
All samples |
Correlation to Mechanical properties |
No |
Integrated |
Integrated |
High dimensional electrical data (= at different electrical settings) |
No |
No |
Yes |
Maps of new electrical properties (flat-band voltage, barrier height, switching voltage,…) |
No |
No |
Yes |
Speed per image |
Standard afm imaging speed |
Standard afm imaging speed |
Slightly slower |
Tip lifetime |
Limited on certain samples |
Excellent |
Excellent |
The DataCube approach can also be applied to many AFM-based electrical characterization modes, such as PFM, sMIM, SSRM, SCM, and TUNA, enabling researchers to examine spectral data across a wide range of operating conditions. Other benefits include correlation between mechanical and electrical characteristics; huge data content with complete spectral data and images at different operating conditions, integrated in one data set; the potential to determine soft and delicate samples; elimination of contact mode for longer tip lifetime; and mapping of novel nanoelectrical characteristics, such as piezoelectric switching voltages, flat-band voltages, Schottky barrier height, etc.
Finally, the DataCube approach enhances each separate nanoelectrical mode, including, for instance, the potential to determine and subtract background capacitance contributions in PFM and sMIM data acquisition at maximum sensitivity using a contact resonance method.
- Schweinbock, T. and Hommel, S., “Quantitative Scanning Microwave Microscopy: A Calibration Flow,” Microelectron Reliab 54, 2070-74 (2014).
- Gruverman, A., Auciello, O. and Tokumoto, H., “Imaging and Control of Domain Structures in Ferroelectric Thin Films Via Scanning Force Microscopy,” Annu Rev Mater Sci 28, 101-23 (1998).
- Wang, C. S. et al., “Ferroelastic Switching in a Layered-Perovskite Thin Film,” Nat Commun 7, 10636 (2016).
- C., A. J. et al., “Machine Detection of Enhanced Electromechanical Energy Conversion in PbZr0.2Ti0.8O3 Thin Films,” Advanced Materials 30, 1800701 (2018).
- Harnagea, C., Alexe, M., Hesse, D. and Pignolet, A., “Contact Resonances in Voltage-Modulated Force Microscopy,” Appl Phys Lett 83, 338-40 (2003).
- Harnagea, C., Pignolet, A., Alexe, M. and Hesse, D., “Higher-Order Electromechanical Response of Thin Films by Contact Resonance Piezoresponse Force Microscopy,” IEEE T Ultrason Ferr 53, 2309-22 (2006).
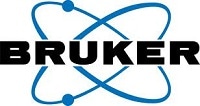
This information has been sourced, reviewed and adapted from materials provided by Bruker Nano Surfaces.
For more information on this source, please visit Bruker Nano Surfaces.