This article outlines a range of application methods for the reliable and efficient analysis of a diverse range of sulfur contents using UV fluorescence, with a reduced requirement for sample preparation and calibration.
Gaseous hydrocarbons are beneficial source materials for fuels, synthesis processes, auxiliary materials, or energy carriers in cosmetics and pharmaceuticals. Their composition and quality, particularly their sulfur content, play a crucial role. They must be free from sulfur (c < 100 ppb) to be used as a propellant gas.
When used for the synthesis of high molecular compounds (such as polyethylene), the same rule applies because sulfur compounds may produce undesirable byproducts, catalyst contamination, and higher production costs.
Reliable detection of sulfur traces in these matrices demands safe and precise metering technology, highly sensitive detectors, and quantitative combustion.
Different standards and requirements apply when they are used as combustibles or fuel (LPG, CNG). For this application, sulfur emission limits must be adhered to and the sulfurous odorants introduced for safety requirements must be at a suitable level. The efficient detection of high and ultra-low sulfur contents is needed in LPG analysis to ensure optimal product quality and instant process optimization.
Two primary challenges arise when the operator conducts LPG analysis. The first is sample digestion, such as sample introduction and combustion quality, and the second is the evaluation of analysis, such as quality assurance of results and calibration strategies.
Due to the broad range of pressures, controlled and safe dosing and handling of LPG into the analysis system is difficult. Samples are prone to early evaporation which impacts the quality of analysis and operating safety as a result of incomplete combustion, soot formation, explosion, or deflagration.
When the LPG is expanded to provide more control over sample handling, the samples begin to change as a result of condensation, adsorption loss, and other factors, which significantly impacts the quality of the analysis.
One way to solve these challenges is through the direct analysis of LPGs out of the liquefied phase before stepwise evaporation in safe, controllable, and small volumes. Inert coating (for example SilcoNert) of the appropriate parts assists in the detection of the smallest TS impurities without the falsification of component losses.
A quantitative sample conversion does not always result in accurate analysis results. These heavily depend on a correct and suitable calibration technique. The system is generally calibrated either by using a single certified standard in a single point calibration or by performing a laborious and error-prone dilution line for one standard material.
The first technique can provide accurate results when the blank does not have to be considered and when high element contents must be measured. For measurement in the trace and ultra-trace range, when no appropriate calibration gases are available, this technique will provide falsified results as they are too low.
In this case, it is recommended that a dilution line is used, but this requires a skilled and dedicated operator as it is highly prone to errors (for example pressure effects, cross-contamination, adsorption loss, changing blank, and more).
The application of different calibration techniques can easily solve these challenges. These techniques make laboratory work more simple, and make the acquisition of reliable results possible, regardless of the experience and skills of the operator.
System calibration can be attained by employing a calibration gas with injection volumes that are variable, along with calibration kits of liquid standards at various concentrations and consistent injection volume. This is achievable due to the quantitative detection provided by the multi EA 5100.
Detection of the SO2 is the same whether it originates from the combustion of a solid, gaseous, or liquid sample. The daily factor function helps to verify the long-term stability of the respective calibration which provides optimal results without the need for lengthy re-calibration of the system.
Materials and Methods
Samples and Reagents
- LPG (butane/propane mix)
- 3.70 mg/L TS standard (dimethyl sulfide in propane)
Sample Preparation
The samples were kept in LPG cylinders. The pressure of the samples varied across a broad range. The LPG standards and samples were directly analyzed with no sample pretreatment.
Calibration
The analysis system was calibrated in advance, where two different techniques were applied to verify the suitability of alternative calibration strategies instead of the commonly used technique.
Figure 1a demonstrates the calibration of the system utilizing one calibration gas with differing injection volumes. The calibration technique that involves the use of liquid standards at various concentrations (in this example, dibenzothiophene in iso-octane) is demonstrated in Figure 1b. The calibration functions received already demonstrate the comparability of both techniques.
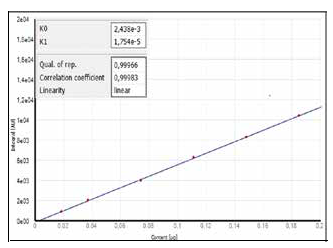
Figure 1a. Calibration using a LPG standard.

Figure 1b. Calibration using liquid standards.
Instrumentation
The multi EA 5100, an elemental analyzer, was used to perform the analysis in vertical operation mode. An LPG 2.0 high-pressure LPG sampling system was added to the multi EA 5100 for the direct addition of liquefied pressurized gases up to 34 bar, in adherence to ASTM D6667 and D7551 and DIN EN 17178.
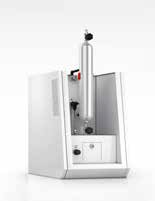
Figure 2. LPG 2.0 module.
The LPG 2.0 module can be flexibly utilized for the automatic metering of liquefied gases at various pressures. The volume of the sample can be adjusted by the operator within the range of 1–50 µL (liquid phase). A 10 µL sample volume (liquid phase) was injected for every LPG measurement during the investigation.
LPGs can expand even when pressure reduction is kept to a minimum (for example sampling). This leads to a non-reproducible sample analysis at high speeds, which can cause sooting of the analysis system and strongly scattering results.
The pressure of the sample is usually increased through the use of an auxiliary gas to prevent this. This is no longer required due to the cooled sampling valve of the LPG 2.0. The analysis of liquefied gases at the lowest pressure (for example butadiene at 2.1 bar) can be performed with strong reproducibility.
Before they are transferred to the combustion module, the samples pass through a heated evaporation chamber where all components (inhibitors etc.) are quantitatively changed into a gaseous state. This excludes memory effects and inaccurate measurements.
Perma Purge, an effective inert gas flushing, is used to quantitatively transfer the gaseous samples to the combustion system. The bi-phasic, catalyst-free combustion procedure is performed at temperatures of up to 1,050 °C.
In the initial stage of the process, volatile sample components are evaporated in an inert gas stream. The formed gaseous products are then combusted in an oxygen-rich environment. The second stage of the process is where formed pyrolysis products and heavier sample components are quantitatively oxidized in pure oxygen.
The quartz pyrolyzer modulates the combustion process, prevents incomplete combustion, and guarantees uniform evaporation. This produces the ideal conditions for efficient and reproducible analysis.
The Auto-Protection System used ensures optimum operational safety, such as an aerosol and particle trap, and a total transfer of the formed SO2 into the ultraviolet fluorescence detector (UVFD) after the reaction gases have been sufficiently dried.
The multi EA 5100 offers a detection limit as low as 5 μg/L S, without the requirement for a lengthy enrichment process (trap and release).
A fivefold measurement of a typical LPG was carried out 10 times over a period of 24 hours to ensure the performance of the system. The deviation of the single analysis is less than 2%. Replicate analyses can be reduced to a minimum due to this superior reproducibility.
Table 1. Reproducibility test of LPG analysis.
Measurement |
1 |
2 |
3 |
4 |
5 |
6 |
7 |
8 |
9 |
10 |
cS in mg/L |
3.78 |
3.60 |
3.69 |
3.71 |
3.68 |
3.69 |
3.61 |
3.66 |
3.69 |
3.56 |
Average value |
3.67 mg/L |
SD |
0.06 mg/L |
RSD |
1.77% |
Method Parameters
Standard method settings for vertical operation kept in the method library were used. Table 2 presents a summary of the parameter settings for the combustion procedure. A quartz wool plug was installed in the inner tube of the quartz combustion tube.
Table 2. Process parameters.
Parameter |
Specification for liquid calibration |
Specification for LPG analysis and calibration |
Furnace temperature |
1050 °C |
1050 °C |
Second combustion |
60 s |
60 s |
Ar flow (first phase) |
150 mL/min |
100 mL/min |
O2 main flow |
200 mL/min |
200 mL/min |
O2 flow (second phase) |
150 mL/min |
100 mL/min |
Draw up |
2 µL/s |
automatically by LPG 2.0 |
Injection |
0.5 µL/s |
automatically by LPG 2.0 |
Evaluation Parameters
Standard method settings from the method library were utilized. Table 3 provides a summary of these parameters.
Table 3. S detection parameters.
Parameter |
Specification S |
Max. integration time |
240 s |
Start |
1.0 ppb |
Threshold |
1.1 ppb |
Stability |
7 |
Results and Discussion
Table 1, 4, and 5 summarize the results of the analysis of one standard material and two different LPG samples. They are either three replicate analyses (Table 4 and 5) or averages of five (Table 1). A threefold measurement was adequate to attain results of within 3% RSD due to the matrix-optimized combustion.
The sample processing time was significantly decreased by this which provided a higher sample throughput. The results from the analyses and their reproducibility demonstrate the superior quality of the digestion process.
The accurate performance of the analysis system and the suitability of the different calibration techniques applied (adapted from liquids calibration) was verified by investigating a TS standard material with a known concentration (as shown in Table 4).
Table 4. Comparison of different calibration strategies.
Sample |
cS [mg/L] LPG calibration |
cS [mg/L] Liquid calibration |
3.70 mg/L TS standard
(dimethyl sulfide in propane) |
3.73 ± 0.03 mg/L |
3.73 ± 0.03 mg/L |
LPG (butane/propane mix) |
579.59 ± 5.10 µg/L |
571.62 ± 5.55 µg/L |
A volume of 20 µL was dosed for the liquefied gases (2) and (3). Considering the high purity of the sample (1), the volume was increased to 50 µL in order to attain optimal results.
The volume of the sample can be flexibly adapted to the predicted sulfur contents in order to optimize the analysis process and to attain the best result in the fastest time.
The next sample can be investigated after a minimum of replicate measurements due to the high accuracy of the metering technology, which produces a high sample throughput.
Table 5. Sulfur contents of the examined gas and liquefied gas samples.
Sample |
cS [mg/L] |
SD [mg/L] |
Butadien (1) |
0.02 |
<0.01 |
6.56 mg/L S in butane (2) |
6.56 |
0.11 |
3.70 mg/L S in propane (3) |
3.73 |
0.03 |
A typical TS analysis curve is demonstrated in Figure 3. The measurement time relies on the metering volume and sulfur content and is between 150 and 420 seconds.
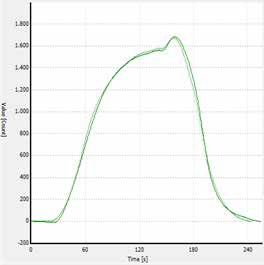
Figure 3. TS analysis curve for propane (LPG).
Conclusion
High-quality analysis results can be attained in an efficient time-frame by applying liquids calibration. This also involves minimum costs and effort as opposed to the traditional calibration techniques (LPG dilution line or one-point LPG).
Equivalent results were achieved using both strategies. The use of liquids calibration is superior, particularly in trace and ultra-trace analysis, as it provides a suitable blank correction, and trustworthy liquid standards are available in concentration amounts as low as ppb-level.
With the analysis system multi EA 5100 and the LPG 2.0, liquefied gases can be investigated irrespective of their pressure and matrix characteristics in the fastest time and with no requirement for sample pretreatment.
Intelligent safety features such as the Self Check System and high-precision metering technology that are integrated within the system guarantee total sample digestion and high-quality results.
Further features, for example, the purge tool for preventative care and the integrated filter system, drastically reduce the maintenance requirements. The superior safety standards and the easy-to-operate hardware allow the device to be used in analysis centers and in shift operation with the highest possible sample throughput.
A measuring range of up to 10000 mg/L starting at a limit of detection as low as 5 μg/L of sulfur can easily be reached as a result of the novel HiPerSens technology. The effective sample digestion and the fast Auto-Protection System, comprising of a high capacity membrane dryer, provide superior reproducibility.
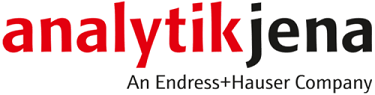
This information has been sourced, reviewed, and adapted from materials provided by Analytik Jena US.
For more information on this source, please visit Analytik Jena US.