Interview conducted by Olivia FrostApr 9 2021
In this interview, Dave Wolff, the Region Manager of Eastern US and Canada at Nel Hydrogen, talks to AZoM about hydrogen generation for new industrial facilities.
What is hydrogen used for in industrial facilities?
There are many types of industrial processes that use hydrogen because of its unique chemical and/or physical properties. Hydrogen is a powerful chemical reducing agent, which enables hydrogen to be used to split chemical bonds for crude oil refining to produce fuel, oils and lubricants, edible oil refining, and pharmaceutical manufacturing. Hydrogen is used in massive quantities to make ammonia and methanol – important chemicals themselves, and key chemical intermediates for other chemicals. Hydrogen’s reducing capacity also makes it ideal for thermal processing of ores and metals – enabling the refining of ores to pure metals and protecting metals during subsequent thermal processing to produce the shapes and physical characteristics required. Because of its ability to prevent oxidation, hydrogen is broadly deployed in semiconductor fabrication. Hydrogen’s tiny molecule size and relatively low cost enable its use to operate analytical equipment across a range of industries. Hydrogen/nitrogen blends are frequently employed as leak-check gases in preference to scarce and expensive helium.
Additionally, there are new and emerging energy-related applications for hydrogen that have unique value because hydrogen can release energy without emitting carbon dioxide. Hydrogen can be reacted with the oxygen in atmospheric air to emit thermal and/or electrical energy without creating carbon dioxide or any other pollutant. Under controlled conditions the only emission of hydrogen oxidation is water!
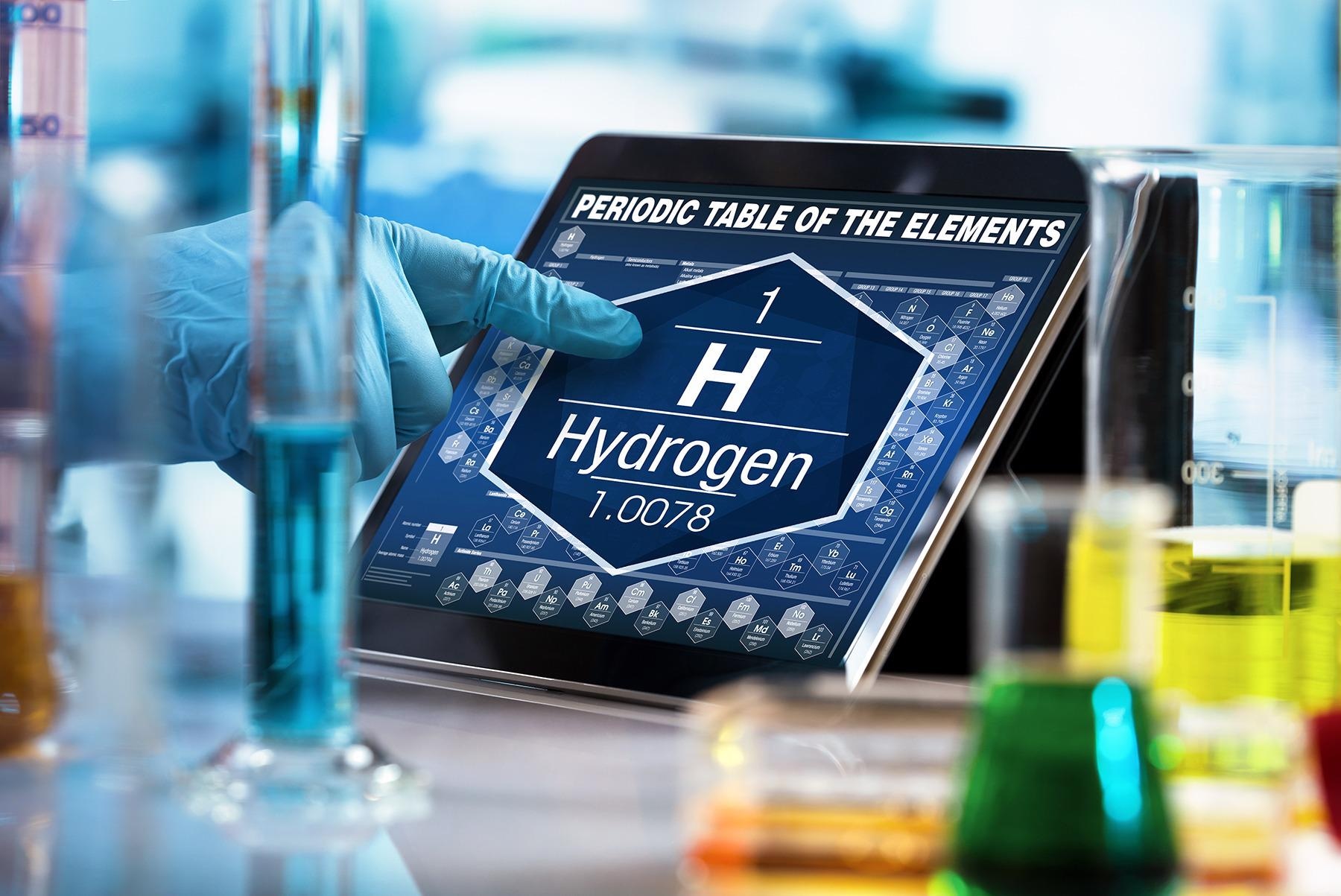
What type of facilities are we talking about?
- Chemical and oil refining facilities
- Primary metallurgy
- Secondary metallurgy such as metal hot rolling and fabrication, metal tubing and wire
- Fabrication shops building intricate gas and liquid systems like braking systems and refrigeration systems that must be leak-proof
- Semiconductor fabrication facilities use an enormous amount of hydrogen for chip fabrication
- Universities and research facilities use hydrogen for advanced technology applications
- There’s a whole new class of facilities using hydrogen for lift trucks to replace battery-powered electric lift trucks in giant warehouses
- Proponents of hydrogen-fueled fuel cell lift trucks include Amazon, Walmart, Home Depot, and diverse food and pharma distribution warehouses
- A single large warehouse can consume the equivalent of three tractor-trailers of liquid hydrogen every week
So, what’s so challenging about using hydrogen in industry?
Hydrogen gas has no single property that make it uniquely challenging to use in industry. But it has an unusual combination of characteristics that cause hydrogen to behave differently than other gases in wide industrial use – such as common fuel gases methane and propane, inerts like nitrogen and argon, and commonly-used compressed air. Hydrogen’s unique combination of characteristics include:
- It’s flammable across a very wide fuel/air range
- Hydrogen has enormous energy content by weight – a small mass of hydrogen can release a lot of energy if it burns
- Hydrogen burns quickly, and will explode if allowed to collect and ignite
- It’s far lighter than air, and highly buoyant
- It’s a tiny molecule, able to leak through miniscule holes
- It ignites with minimal activation energy – even the static electricity of an escaping gas
- It heats up when it expands – the only flammable gas to do so
- It burns virtually invisibly in daylight because the flame has no luminosity from carbon
- It cannot generally be odorized because the odorant compounds would damage the downstream equipment
These behavior differences, and the fact that hydrogen use is becoming more common as new applications are introduced and gain favor, is creating concern that hydrogen installations must be safely managed.
What is not a hazard about hydrogen?
Hydrogen is not kryptonite – we must respect it, but we don’t need to be afraid of it. There are many reasons that hydrogen can be widely employed and used safely. For one, hydrogen is not poisonous or corrosive, so in that sense it is safer than alternatives such as ammonia. Also, hydrogen is highly buoyant, meaning that it escapes straight up if allowed to do so – so it disperses readily in case of a leak if the system design allows it to escape. Early demonstrations compared gasoline-fueled automobiles to hydrogen-fueled vehicles in case of a fuel leak – the gasoline leaked onto the ground under the car and ignited, incinerating the car and everything in it, while the hydrogen in the hydrogen-fueled car escaped the intentional leak and was immediately dispersed in air as it rose straight up. Even in cases where the escaping hydrogen was ignited, the flame had little radiant energy because of its low luminosity, so it did not heat up adjacent surfaces unless the flame impinged directly. Unlike nitrogen, which readily mixes with, and displaces breathable air, and is frequently the cause of low-oxygen mishaps, hydrogen rises to the top of an air column, and does not generally present an oxygen-displacement risk.
Hydrogen challenges magnified by hydrogen storage
While hydrogen has unusual properties, it is widely and safely employed in industry. Hydrogen in small quantities can be easily managed through knowledge and respect for its characteristics. It is the storage of hydrogen that creates complexities. Storage of hydrogen increases the hazard because of the enormous energy content of flammable gas stored, the relatively high potential of leakage or mishap, and the serious consequences of a hydrogen ignition.
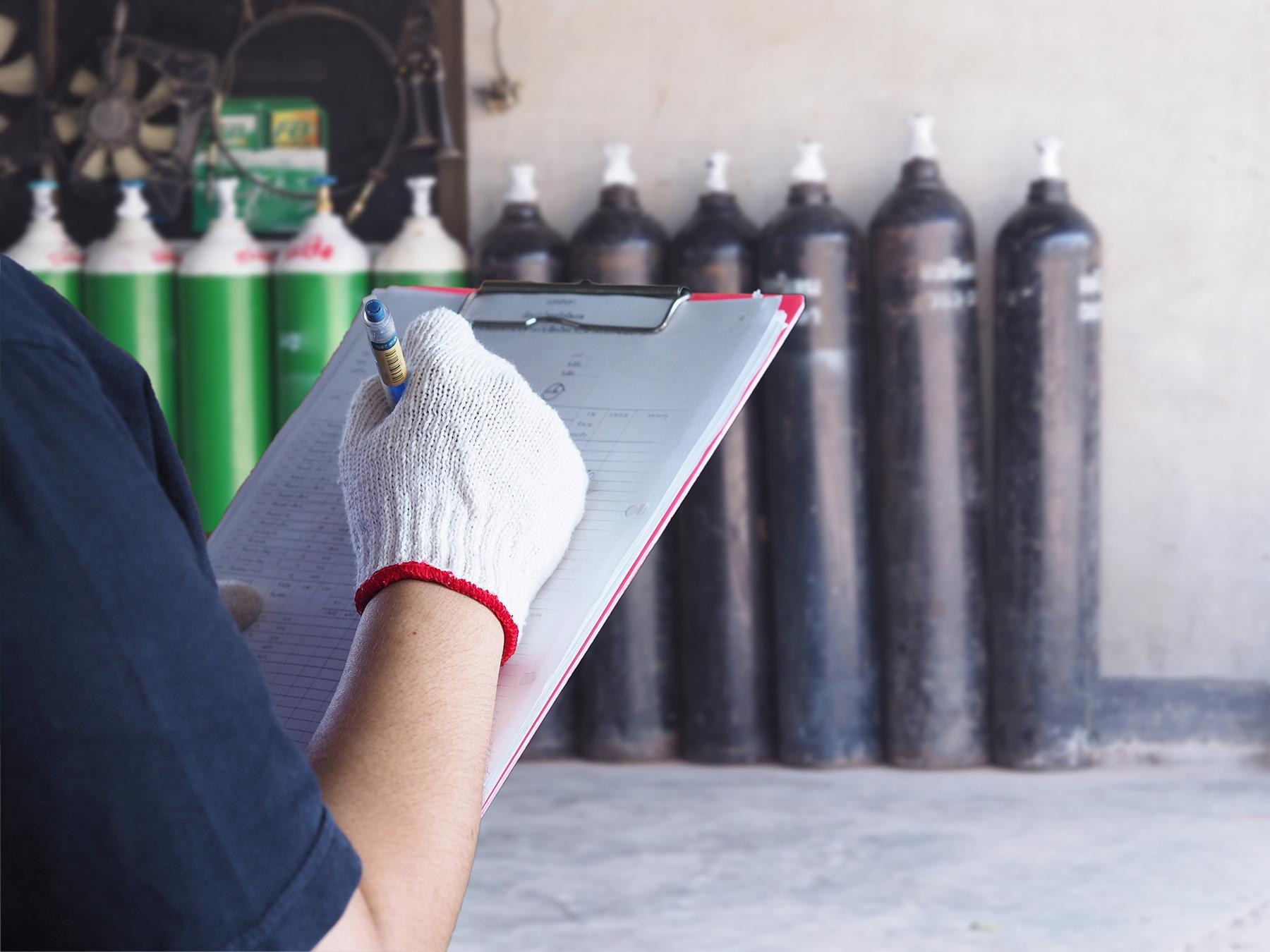
What is unique about the challenges created by hydrogen storage?
Hydrogen has several unique chemical properties that make it particularly challenging to store at an industrial site. First, hydrogen reacts with oxygen to release a tremendous amount of thermal energy – the highest energy density per mass of fuel as compared with any other substance. Second, hydrogen will ignite with the smallest amount of energy – it has the lowest activation energy of any gas. Hydrogen also burns quickly – four to five times faster than typical hydrocarbons such as gasoline vapor or methane.
Finally, because hydrogen is such a tiny molecule, hydrogen is very difficult to store securely – it will leak through the most minor piping or fitting imperfection. The leakage issue is exacerbated by the fact that hydrogen is colorless and odorless, and cannot be odorized because the odorant would compromise other key hydrogen attributes (see CFR 192.625). Hence it is possible to have a significant hydrogen leak without being aware of it - that’s why facilities that use hydrogen have carefully designed facility ventilation systems and many use dedicated hydrogen detectors.
Because hydrogen is extremely combustible, extraordinarily low in density, and leaks given any chance to do so, it is very challenging to store. As a result, the regulations around hydrogen storage are built around minimizing the damage to life and property if a leak does occur. Storage rules prescribe outdoor storage if possible, adjacency requirements, clearance distance, intervening structural walls, ventilation and electrical requirements, and highly regimented inspections to ensure the ongoing safety of hydrogen storage.
What does “hydrogen pooling” mean?
The extraordinary low density of hydrogen means that it will rise through an air column in case of a leak. That predictable behavior provides a safety benefit if the hydrogen is allowed to escape by rising, as in the case of a tank sited out of doors. But if there is a roof, or cover, or intervening structure that impedes the hydrogen from rising to escape, the hydrogen will create a pool of hydrogen on the bottom of the structure – the hydrogen is held there by the structure itself impeding the hydrogen from escaping. If additional hydrogen is added from a continuing leak, the hydrogen pool will expand horizontally across the structure, just as a water puddle expands across pavement. Unfortunately, the hydrogen puddle generally finds a light fixture or other source of ignition mounted on the underside of the structure and ignites – often causing great damage.
The prevention of hydrogen pooling on the underside of a roof or elevated structure is among the most important safety precautions that can be implemented to avoid hydrogen mishap.
- Elimination of the structure is the best approach – don’t place hydrogen storage or generation or use under a roof unless you have to.
- If the hydrogen application must be under roof, then ensure that there is adequate exhaust from the under-roof area to remove the hydrogen at a faster rate than it can build up.
How are the hazards of hydrogen best mitigated?
The challenges of working with hydrogen are best managed by limiting the amount of hydrogen on-hand. Hydrogen storage creates issues for several reasons:
- More hydrogen stored means more destructive energy in case of a mishap
- Hydrogen storage is generally in the form of pressurized hydrogen – subject to leaks, and able to deliver unlimited flow rates of hydrogen instantaneously in case of a piping failure
- Hydrogen may be stored as liquid hydrogen – storing vast volumes of hydrogen in the form of cryogenic liquid, creating liquefied air risks, requiring considerable clearances for safety, and at risk of high hydrogen delivery rates in case of a piping failure
As compared with stored hydrogen, hydrogen generation makes hydrogen at the same rate that it is required by the hydrogen-using process – no hydrogen is stored. Even if a catastrophic piping failure were to occur, the hydrogen flow rate would be in the range that the process, and standard safety systems, were designed for.
What are the advantages of generating hydrogen versus getting hydrogen delivered?
Because storing hydrogen is so complex, hydrogen users are interested in ways to use hydrogen without storing hydrogen. Actually using hydrogen is not particularly challenging – its characteristics are learnable if not familiar, predictable, and unchanging. Straightforward design approaches and facility features can make working with hydrogen as safe as working with any flammable gas. But that only applies to the relatively modest amounts and flows of hydrogen expected in a process – a leak of stored hydrogen creates an overwhelming problem by potentially releasing a massive amount of hydrogen almost instantaneously.
Facilities can be designed to handle a flood of hydrogen caused by a major leak from a storage vessel – but it is expensive. It requires the ability to exhaust enormous amounts of highly flammable gas from under the roof of a facility automatically and nearly instantly by using giant rooftop explosion-proof exhaust fans triggered by flammable gas detectors. The system must react instantaneously to a hydrogen sensor at roof level, and all components must be explosion-proof.
It is so much easier to simply regulate the maximum flow rate of hydrogen available, using hydrogen generation capable of meeting the maximum flow rate needs of the processes, but without storing amounts of hydrogen that can be released nearly instantly in case of a mishap.
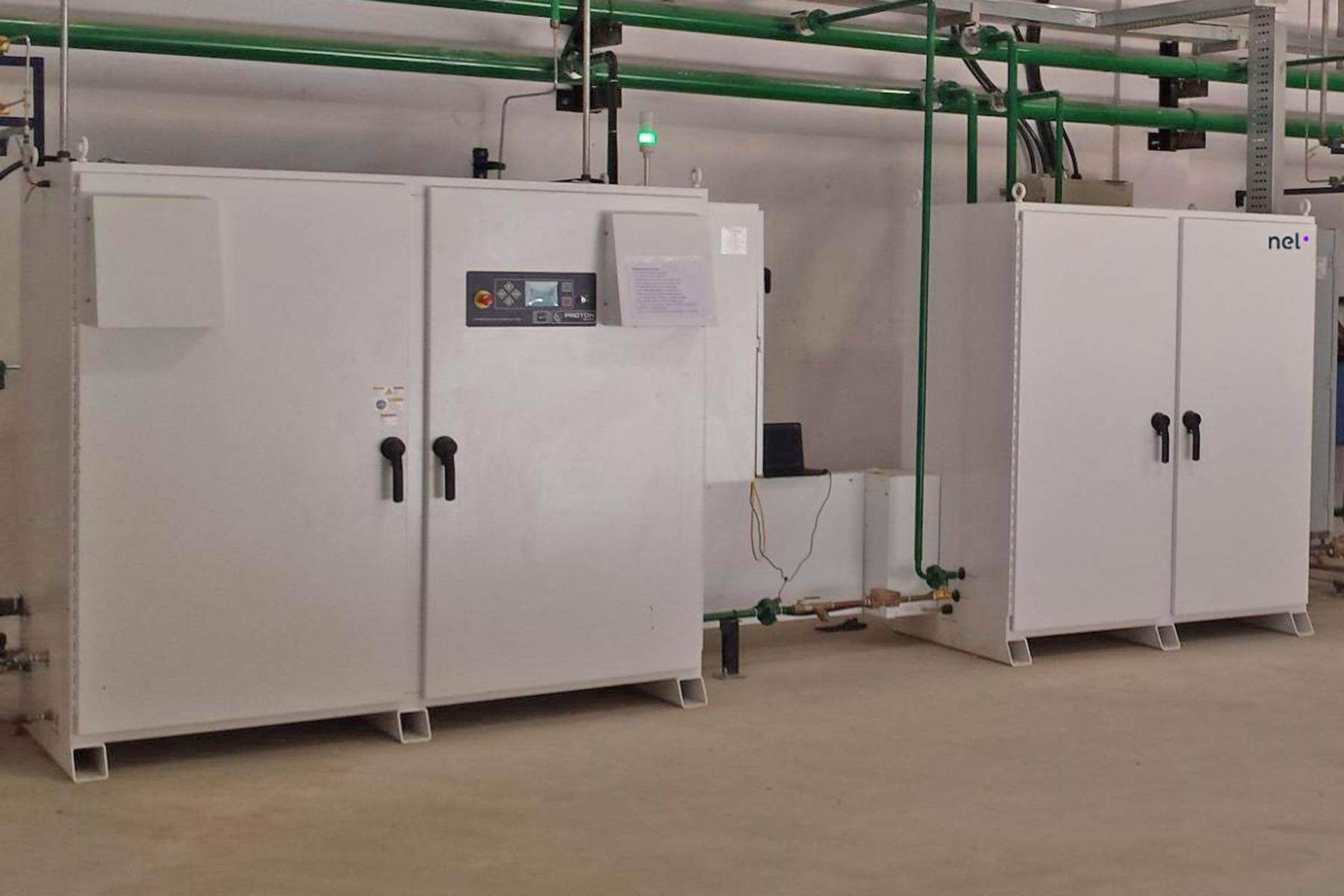
How does the cost of generating hydrogen compare with delivered hydrogen?
While air-derived industrial gases such as nitrogen, oxygen and argon are generally widely and economically available in industrial areas, hydrogen, which is typically made from natural gas or coal, may not be as easily available, and if available may be costly because of long distance transportation.
Hydrogen supply via delivered liquid or gaseous hydrogen is thought to be a low-capital investment approach – after all, the supplier provides the tank(s) and all the delivery equipment – but often, it is not as low-capital as might be believed. To start, the customer must supply the infrastructure for hydrogen delivery from the vehicle into the storage vessel(s) located at the customer, and siting and protection for the storage vessel(s) – delivery stanchions, foundations, fencing, lighting, underground piping etc. Because large hydrogen storage, especially liquid hydrogen storage, requires long clearance distances from buildings, property lines, parking, public access areas, non-explosionproof lighting, air intakes etc., the underground piping to serve the tank may be longer and more expensive than anticipated. Cost for installing a leased liquid hydrogen tank can frequently reach or exceed $70,000.
So, the anticipated low upfront cost for delivered hydrogen may be higher than expected. Once the investment is made, the supplier will begin supplying hydrogen to the customer under the terms of a supply agreement that defines supply responsibilities and pricing. Both parties are locked into this agreement – make sure that you understand it, as your business depends on it.
Hydrogen delivery is generally thought to be a low fixed cost, but higher variable cost, approach as compared with hydrogen generation. The fixed costs for hydrogen delivery include the capital invested in tank and piping infrastructure, and the monthly fixed payment for tank rental, while variable cost would be the charges for the actual hydrogen delivered and the associated fees charged by the supplier.
By comparison, a hydrogen generator requires a meaningful capital investment of $70,000 to $600,000 for a hydrogen generator model that meets the needs of that hydrogen user. By comparison with delivered hydrogen, that is higher fixed capital. But a hydrogen generator makes hydrogen for a fraction of the variable cost as compared to delivered hydrogen – generation may incur a variable cost of 60 cents to $2.00 per 100 scf for electricity, while delivered hydrogen may be priced at $1.75 for large liquid hydrogen users to as much as $70.00 per 100 scf for smaller, high purity cylinder users. Pricing depends on hydrogen volume, form, distance from sourcing, and purity specifications.
In general, generated hydrogen is favorable for processes that use hydrogen for long periods, at a fairly steady rate, and which benefit from higher purity and higher pressure. Delivered hydrogen may be a better choice for temporary requirements, or highly intermittent usage, or customers whose use rate may grow or shrink before it can be predicted.
Are many hydrogen-users making this change?
Working with customers to consider hydrogen generation has been a process of educating people that the option exists. That is still a work in progress. Those customers that have chosen hydrogen generation almost never change back, as they appreciate the assured supply, predictable, competitive cost and superior safety of generated hydrogen supply.
About Dave Wolff
Dave Wolff has over 40 years of project engineering, industrial gas generation and application engineering, marketing and sales experience.
He has been a Sales and Marketing leader for hydrogen generation technologies since 1999. Dave holds a degree in Engineering Science from Dartmouth College. He has an extensive background in hydrogen generation at large and small scale, hydrogen distribution, storage and industrial utilization, as well as application knowledge across a diverse range of industries.
Disclaimer: The views expressed here are those of the interviewee and do not necessarily represent the views of AZoM.com Limited (T/A) AZoNetwork, the owner and operator of this website. This disclaimer forms part of the Terms and Conditions of use of this website.