Fugitive emissions pose a problem for industrial communities. This interview with Bob Gallagher will cover regulations and the instrumentation utilized to detect fugitive emissions. The discussion will also touch upon how government and industry are working together to make this world cleaner, healthier and safer for everyone around the globe, including a brief history of the Clean Air Act.
LRAR, which stands for Leak Detection and Repair will also be covered, including the regulation and standards that are driving LRAR regulation for fugitive missions and some of the major players in the LRAR arena ranging from the large oil and gas companies down to the contractors who do the work.
Furthermore, the interview will include the type of equipment utilized in this type of monitoring, some of the specifications of equipment, and some of the common faults that are seen in terms of the government agencies.
What are fugitive emissions?
Fugitive emissions are unintended leaks of gases or vapors from pressurized industrial equipment from industries that use or produce gases and chemicals that are hazardous to both humans and the environment. Fugitive emissions can be especially dangerous to the workers, the community and the surrounding environment.
How do leaks occur?
The most common cause of links is a seal or gasket failure due to normal wear and tear. In some of these refineries, there are miles and miles of piping and contraction expansion of the components creating those leaks.
There is also improper maintenance. The top seven sources of equipment leaks are valves, connectors, pumps, sampling connections, compressors, pressure relief devices and open-ended lines. These top sources of leaks account for about 90% of the emissions out of a facility.
At a typical refinery, there are more than 2.5 million potential sources of leaks on the grounds. As a result, a typical refinery will emit anywhere from 600 to 700 tons of volatile or organic chemicals (VOCs) annually from the leaking equipment. Studies have shown that the average cost of product loss is about $1,400 per ton. With a facility emitting 600 to 700 tons of VOCs, there is an average loss of $750,000 to $800,000.

Image Credit:Shutterstock/TRSTOCK
Why do leaks need to be fixed?
The number one reason is to keep the workers safe. The health of a worker may be at stake if a facility is processing hazardous gases and chemicals. Suppose a worker is exposed to these when there are unintended leaks. Not only is there a concern of the chemical leak and the injury it could do to the worker a reason, but there is also a long history of explosions and loss of worker lives due to poor maintenance practices.
For instance, in 2005, BP in Texas City, Texas, had an explosion that killed 15 employees and injured more than 70. This followed multiple violations from the previous year.
The second reason to fix leaks is to protect the environment. Most recently, the COP26 UN Climate Change meeting in Glasgow, Scotland, discussed greenhouse gases, such as methane, and how they contribute to climate change.
Additionally, one of the most important things for a company is abiding by and the upkeep of its reputation. Suppose you are known as a company that does not care for the environment. In that case, there will be some long-term consequences not only to your reputation but also to the environment and the community’s reputation.
Detecting and responding to pollution helps protect neighbors and the surrounding communities around a facility. Namely, a lot of companies that are in urban areas have fence line monitoring. They keep a very close eye on the wind direction when it enters communities, track it, and prevent its exposure to the surrounding neighborhood.
Can you describe government compliance with regulating fugitive emissions and the history of the US Clean Air Act?
Over the years, more and more governments have implemented regulations around inspecting for fugitive emissions. Those countries also levy fines. A company in violation could receive federal, state and local violations. Compliance and maintaining good standing means facilities can avoid fines and other enforcement actions up until the closure of that facility.
It is also about protecting your revenue. The more gas you can keep in your pipe – ultimately it hits your bottom line.
The US Clean Air Act has been around for over 50 years now and was established to regulate air emissions. It gave the EPA, the Environmental Protection Agency, authority to establish the National Ambient Air Quality Standards to protect the public and the environment back in 1970.
In 1983, the LDAR Method 21, the point inspection of leaks, was introduced. Then in 1999, there was an LDAR enforcement alert. In 2006, with the 40 CFR Part, 60 more subparts were released that covered the standard performance of equipment leaks of VOC or SOCMI, synthetic organic chemical facilities. In 2015, the Quad Oa regulations regulated emissions at onshore crude oil and natural gas facilities.
Most recently, the COP26 UN Climate Change Conference was held in Glasgow, Scotland. Coming out of that, there are a lot of countries now proposing aggressive proposals to reduce greenhouse gas emissions. At the moment, there are a lot of pre-meetings with the EPA going through proposals and welcoming comments from the general public as well as companies with innovative technologies.
What is LDAR?
Facilities can control emissions from equipment leaks by implementing a Leak Detection and Repair (LDAR) program. The EPA clearly defines LDAR as a work practice designated to identify leaking equipment so that emissions can be reduced through repairs.
A component that is subject to LDAR requirements must be monitored at specified regular intervals to determine whether or not it is leaking. Any leaking component must then be repaired or replaced within a specified time frame. For instance, if there’s a very small leak, a company might be able to wait until their annual shutdown to repair that leak.
Leaks of a greater severity could require a shutdown and repair in as little as a few days or up to a week, depending on the PPM severity of the leak.
What are some examples of governments implementing air emission regulations according to LDAR?
In regard to regulations, the United States, as well as Europe, are some of the leading areas to implement Clean Air Act regulations. Four in particular – the New Source Performance Standards, the National Emission Standards of Hazardous Air Pollutants, the Resource Conservation and Recovery Act and the State Implementation Plan – are even more stringent at times than the federal regulations. For instance, New Mexico, Colorado and especially California, given the smog and the pollution in those areas, have a much more stringent regulation plan in place.
Each of these standards list LDAR programs that are required under 40 CFR, the Code of Federal Regulations part 60, that utilize Method 21.
In the EU, they go by the Fugitive Emission Standards EN 15446:2008. That regulates the measurement of fugitive emissions of vapors generated from equipment and piping leaks. Other areas such as Mexico are looking at methane regulations in 2021. Colombia, Argentina, Nigeria and the Ivory Coast are considering similar regulations to Mexico. LDAR is gaining momentum in areas around the world to help protect the environment and also to regulate industry.
In the US, there has been a recent reversal. The Trump New Source Performance Standard regulations did not require monitoring for well sites and compressors that were built prior to 2015. At COP26, EPA has proposed additional guidelines for the NSPs for these existing sources. The goal of that proposal is to reduce 41 million tons of methane emissions from 2022 to 2035.
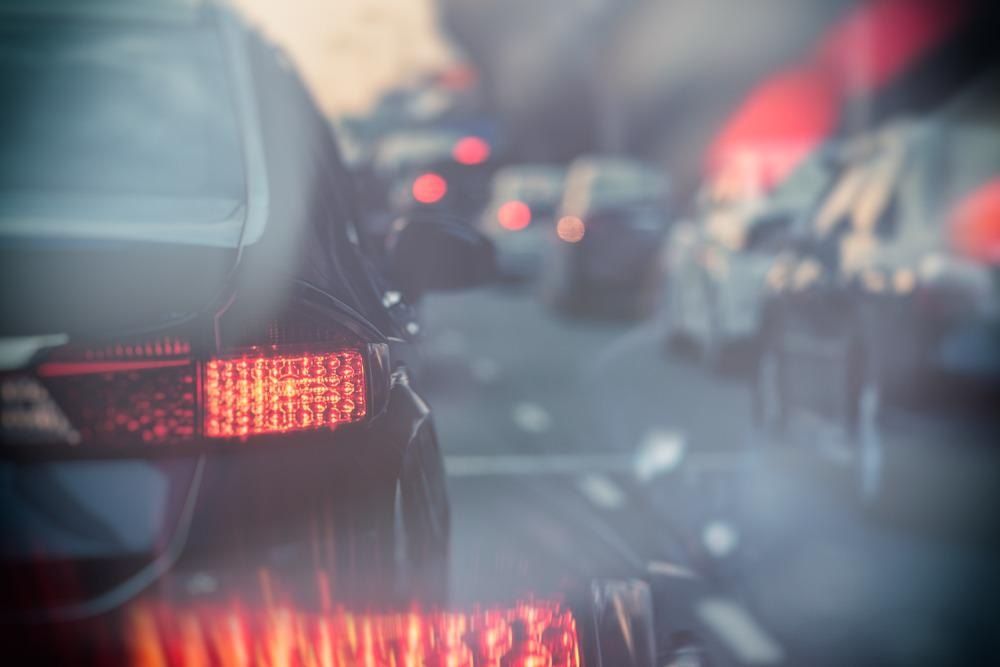
Image Credit:Shutterstock/ALLABOUTSPACE
Can you list examples of industries that are currently regulated that require a formal LDAR program using Method 21 and which is reported up to the EPA?
There are 25 different distinct industries that are regulated in terms of 40 CFR. For instance, under the synthetic chemical facilities, you have companies such as DuPont, Textron, PPG and Proctor & Gamble that fall under that regulation. 40 CFR Part 60 subpart DDD is for polymer manufacturing. Other companies such as Dow Chemical, Lyondell Basell, BASF, LG Chemical are under that regulation.
Regarding pharmaceutical production, there is Pfizer, Johnson & Johnson, Merck and AstraZeneca to name a few, who do have LDAR programs that inspect for leaking pipes.
Then there are another 28 industries that require the use of Method 21 but do not have a formal LDAR program specifically. For instance, municipal solid waste landfills monitor a capped landfill to ensure no cracks where rainwater can actually penetrate and leech through the landfill and potentially seep into the water system or the aquifer.
The pulp and paper industry is also regulated. International Paper and Kimberly-Clark are a few companies that might be under that regulation.
What are some major players in the fugitive mission of the LDAR industry?
There are large oil and gas companies such as Exxon, Shell and Chevron. There are also polymer manufacturing or chemical companies, such as Lyondell Basell, DuPont and Dow. Then, you have industries that specifically focus on monitoring, and they are considered LDAR contractors.
EMSI, Montrose and Think Environmental are companies that specifically bid on contracts at these large chemical or refinery locations and then conduct the LDAR inspections while being directed by the EHNS or the LDAR coordinator of that facility.
Other areas like the South Coast Air Quality Management District or the Bay Area Air Quality Management District are state-run agencies regulating and enforcing a more stringent requirement LDAR. Facilities must develop a program to control and record the results of their monitoring. These records are submitted and audited by the EPA and local regulatory agencies for compliance with the facility’s specific operating permit.
With a successful program, fewer leaks translate into lower emissions. Thus, you can reduce your monitoring and save in terms of manpower if you show that you have a good solid LDAR program at your facility.
How can advanced software help companies monitor fugitive emissions?
Another area in LDAR that you can record on the instrument is monitoring, or you could have a specific LDAR software that maps out a route that the technician will pursue on a daily basis. Each junction is typically tagged with that location. In addition to collecting the monitoring results, the software can also provide compliance reports, quality control data and total emissions predictions.
There are a few specialized companies, as well as a lot of small in-house developed programs or software monitoring programs. The software has evolved with data logging and transferring to field collection over the years. Now, with cloud capabilities where users can automatically and instantly upload information to the cloud, multiple areas of a company can access that data.
What is a consent decree?
A consent decree is a situation if a facility is found to be in violation of their operating permit, they could be fined and forced to perform additional monitoring. This increases the frequency of the monitoring points to show due diligence.
As facilities become more efficient with fewer leaks, they can reduce the frequency of monitoring. If a consent decree is issued and the company is at a reduced monitoring point, but they are seeing signs of increased fugitive emissions, then all monitoring would return to the original schedule.
LDAR contractors supply the manpower. They could supply the analyzers, the knowledge and record-keeping to those facilities that need to comply with Method 21. Some contractors will work with other manufacturers to develop alternate means of capturing the monitoring results, as well as both software and hardware capabilities.
These services often differentiate themselves in industry based on data conversion and data management offerings. Everything is cyclical, and some companies will want to perform with their own personnel, while other ones feel that it is more cost-effective to outsource it to a contractor that solely specializes in this area.
Image Credit Shutterstock/
Can you discuss Method 21 in a bit more detail and what it entails as defined in 40 CFR Part 60?
This describes a protocol for monitoring fugitive emissions. Facilities impacted include chemical and petrochemical plants and pharmaceutical, pulp and paper, semiconductor and seed oil facilities. Each of these areas is regulated by individual subparts through the previously discussed 25 industries that have formal programs and 28 that have informal LDAR programs. The method defines the monitoring requirement with respect to technology, the response time of the equipment, the response factors and other critical parameters.
Method 21 is defined by the standard, where the technician places a probe inlet at the surface of the component interface where the leaking could occur at the flange or the valve junction. They’ll move the probe along the interface periphery while observing the instrument readout.
If an increased meter reading is observed, they slowly sample the interface where the leakage is indicated until the maximum meter reading is obtained. The technician will then leave the probe inlet at this maximum reading location for approximately two times the instrument response time.
Typically with these instruments, the response time is anywhere from three to four seconds. To double that, it would be seven to eight seconds that the technician would have to dwell at that area. If the maximum observed meter reading is greater than the leak definition in the applicable regulation, they record and report the results as specified.
What is a flame ionization analyzer?
Nearly all facilities use a flame ionization analyzer, an FID, for monitoring due to stability and response factors. An FID is very sensitive to hydrocarbons. For example, a lot of the methane, benzene and toluene from a refinery or petrochemical facility is very sensitive when using an FID. A permit or a consent decree can mandate data collection, so users could electronically capture the data either on the instrument itself by using the enhanced probe or through a handheld device via Bluetooth to the instrument.
Some of the requirements of the instrument include that it must meet those defined in Method 21, which would be a response time of less than 30 seconds. It has to be intrinsically safe because when you are in a class one div one or class one div two location, the response factor is less than 10. Furthermore, a quarter-inch probe opening and quarterly precision tests are required on the instrument to ensure repeatability.
What are the calibration specifications of a flame ionization analyzer?
In terms of the instrument itself, it has to be calibrated on a daily basis. You have to calibrate it close to, but not exceeding, the leak definition of your facility. Typically, you will have a zero, 500 or 2,000 span gas. You could also have a 10,000 PPM leak definition. There are states and areas that require a second calibration, whether it be midday or post-shift.
There are some regions where you have all three. Essentially, after you have been out in the field monitoring in the morning and you come back in and do a drift assessment on the instrument itself. It has to be within 10% of the original calibration. If not, that morning's data is invalid and needs to be redone. This ensures that the instrument is capable and fully calibrated and that users are reporting an accurate leak. Quarterly precision tests are also required on the instrument itself.
What are some of the attributes of good monitoring equipment and an example by Thermo Fisher?
It must be ruggedized for the very demanding work environment, with technicians climbing up through ladder cages and instruments getting banged around. It has to be relatively robust. It must be easy to maintain and calibrate, and it must be dependable. Without a working function, no work or monitoring is done, which could cause contract agencies to lose wages.
One such instrument is the Thermo Fisher TVA2020 Toxic Vapor Analyzer. This type of instrument is utilized globally to detect fugitive emission leaks to reduce greenhouse gas emissions.
The instrument is also used in terms of first responders for hazardous spills or incident containment, as well as remediation or landfill survey tools, according to the Resource Conservation and Recovery Act.
What are some traditional methods to calibrate the device?
There is a need to calibrate the device to ensure that it is reporting accurately in regard to a leak. There are traditional methods used to calibrate the device. You can fill a Tedlar bag, and it calibrates one instrument at a time. It is a relatively slow process where you fill each bag, and there are multiple bags required for each span gas or according to your leak definition. You could not put in a 500 PPM span gas into a 2,000 PPM bag, or else you could get false readings.
There is also a method that also calibrates one unit at a time. It will use slightly more gas because you are venting or over-pressurizing to start the instrument. There are multiple portable tanks required for each span concentration.
The demand flow method is, again, a single unit being calibrated. It will use less gas because it relies on the flow of the instrument to pull the gas out of the demand flow unit. It is a lengthy process if you had to calibrate to three or four different types of span gases.
What are some common mistakes made with calibration findings?
There has been a number of companies that will use expired gases. There are recommended expiration dates from the gas manufacturer. But if that is the case and a company was caught using an expired gas, it would result in a pretty significant fine.
Some of the common calibration findings include when companies use incorrect leak definitions in their calibrators. Others include when they are not recording daily instrument calibrations. That is a breakdown in the overall LDAR program. Also, there have been instances of not entering correct span gas values. The span gas used should be within 2% of the rated value. If it is not, then it should not be used in the application.
Another breakdown in the system is when you are not conducting the required calibration precision or response tests on a quarterly basis, and you are not performance testing at all leak definitions. Each facility has its permit with its number of leak definitions. Depending on the route that you are going out, you need to calibrate the device to all the leak definitions that you will see during that process or shift.
Regarding incorrect response time after probe modification, a lot of facilities have extended probes that could be six feet long, and users need to adjust their response time during their calibration process when utilizing the extended probes.
Furthermore, if the drift assessment is greater than 10%, disregard the monitoring data. That data is invalid, and that route needs to be redone with an instrument that is recalibrated. Another area of concern is not flushing with zero gas or zero span gas between each calibration precision step to ensure that there is no remaining PPM gas in the piping or in the tubing that is going to skew results. Not recording your morning, midday and end of shift concentrations and the percentage of drift will also skew results.
Do you have any comments regarding some of the consolidations and acquisitions that are occurring in the LDAR monitoring segment?
Over the years, there have been a number of consolidations within the industry. A refinery sometimes will have its own internal hires do the monitoring.
There has been a lot of consolidation even within the LDAR contractors. Most recently, there has been a number of acquisitions of these LDAR contractors by large environmental and industrial service companies.
For instance, in October of 2021, Clean Harbors – a well-known environmental company – recently required an LDAR contractor named HydroChemPSC to branch their first venture into the LDAR contractor market. Back in 2020, Alliance also acquired their first emission monitoring company of the Bureau Veritas monitoring segment. Then, in early 2021, they acquired EMSI, an emissions monitoring company. Both of these acquisitions now make them a very large player in the LDAR market, specifically in the US, which carries over into Europe.
Globally, various countries are moving toward the same page with regulations. Do you see that trend continuing in the short term, with further consolidation and continued acquisitions?
I see more of those companies being more global than regional. You do have the instrumentation companies that are relatively global, like Thermo Fisher Scientific. But now, you also see these monitoring companies taking best practices and carrying them over to a region that maybe does not have that level of expertise.
Instruments are relatively robust since they are being utilized out in the field rather than in a sterile lab condition. Do they require annual factory calibration given how much of a rough and tumble environment they are utilized in, and do they require more frequent calibration?
In general, a lot of these class one div one and class one div two environments require something very robust. A lot of equipment has rubberized shock absorbers just in case it is dropped or banged up against a pipe or ladder cage. For instance, the Thermo Fisher Scientific TVA2020 does incorporate a rubberized boot both at the top and bottom of the equipment to absorb these types of shocks that typically are countered on an average monitoring day or shift.
In regard to the calibration side of it, customers can do their own calibration where they calibrate the instruments prior to them going out in the field to make sure that their readings are very accurate. With that in mind, a lot of the instrumentation is built so that users can calibrate. They can also do a lot of their in-house repairs. For major repairs or areas where the industry or even the customers require that the manufacturer does the factory calibrations. More expertise is involved in that, and they should be conducted at an authorized depot repair center. Thermo Fisher is a relatively global company. We have those repair capabilities in the US, UK, Taiwan and multiple locations within China.
Could you summarize some of the points about the digital regulations of the EPA methane proposal that is coming out?
Essentially the EPA methane proposal will result in more monitoring of emissions for both upstream and midstream operations. In particular, what has been discussed is the well sites and compressor stations that were not covered under either Method 21 or even any type of emissions monitoring.
The new regulations are proposed for both new and existing locations of these well sites and compressor stations. This new proposal also incorporates the reversal of when the Trump administration did a rollback of the Obama monitoring regulations that were implemented. The Trump rollback grandfathered a lot of these sites that were built prior to 2015, and now those are being reversed.
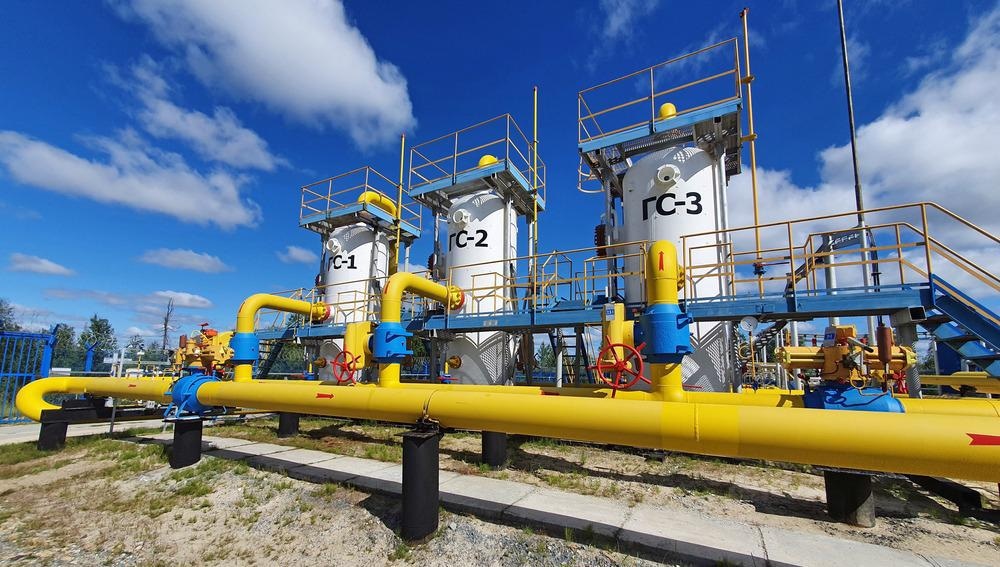
Image Credit:Shutterstock/grigoriipisotsckii
Is that the early proposal to disallow the rollback, or is it part of something larger?
The Congressional Act will disallow the previous amendment that the Trump administration did for Quad O, as well as Quad Oa. These are typically the upstream and midstream operations. The new proposal also includes new subparts like Quad Ob, which will impact new, modified and reconstructed sources that will be put in place after this proposal, which was made on November 15th 2021. It will include these new operations under a stricter requirement to measure for methane, as well as other VOCs.
They do have a proposal called Quad Oc, which will address existing sources in place prior to November 15th, 2021, and that includes compression stations all the way through the transmission of the compound. This will cover both oil and gas, as well as natural gas distribution facilities, and will require that they undergo mandatory monitoring.
Those regulations, depending on the size and the VOC estimated output, have broken it into three different categories: less than three tons of emissions, three to eight tons and greater than eight tons. If you have greater than eight tons, you are going to be monitoring on a quarterly basis. With three to eight tons, monitoring will be done on more of a biannual basis. If you are less than three tons and you show that you have inspected and the leaks are at a small enough level, then you can potentially go without doing any type of future monitoring.
Do you have any predictions on future EPA meetings and what may result now that COP26 has come to its conclusion?
They wanted to eliminate the gas-driven pneumatic controllers, which tend to be a high emittance area. They are encouraging the move to electric controllers to prevent the venting of VOCs and methane. They have a very aggressive goal of eliminating 41 billion tons of methane emissions by 2035. You will see a lot more regulations being put in place for oil and gas, as well as natural gas facilities. Things are evolving, and there is obviously more change to come.
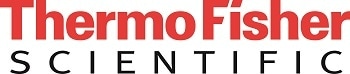
This information has been sourced, reviewed and adapted from materials provided by Thermo Fisher Scientific – Environmental and Process Monitoring Instruments.
For more information on this source, please visit Thermo Fisher Scientific – Environmental and Process Monitoring Instruments.
Disclaimer: The views expressed here are those of the interviewee and do not necessarily represent the views of AZoM.com Limited (T/A) AZoNetwork, the owner and operator of this website. This disclaimer forms part of the Terms and Conditions of use of this website.