Interview conducted by Alex SmithMay 9 2022
In this interview, AZoM talks to Chris Aylott, Senior Engineer at Newcastle University, about fatigue testing in the development of low carbon transport solutions.
Please could you give a brief overview of what you are currently working on and the kind of instruments needed?
Design Unit, which is based within the School of Engineering at Newcastle University, is currently working on a range of projects targeting the development of mechanical transmission systems for low carbon transport solutions that require increased efficiency, reduced weight and improved reliability.
In addition to supporting the development of concepts and designs, a large part of Design Unit’s current activity involves generating performance data through fatigue testing.
As an example, Design Unit is currently working with Jaguar Land Rover on a large collaborative research and development project supported by the UK Advanced Propulsion Centre that is investigating future automotive electric drive systems.
Within this project, bending fatigue strength data will be generated using electromagnetic resonance machines and contact fatigue data will be generated using back-to-back, power recirculating gear test rigs developed by Design Unit.
The University’s capability to generate fatigue strength data in the very high cycle range has been enhanced with a newly-acquired Shimadzu USF-2000A ultrasonic fatigue test machine.
To understand and quantify the results obtained, Design Unit’s suite of metallurgical analysis equipment will be used to fully characterize the tested specimens in terms of microstructure, hardness and residual stress.
Detailed fractography will also be carried out using optical and scanning electron microscopy to characterize the failure mechanisms observed.
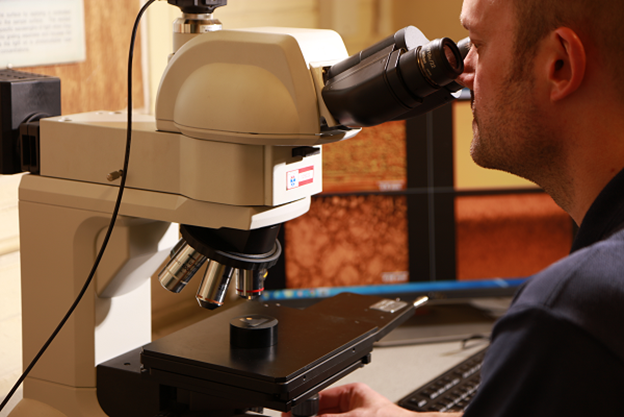
Image Credit: Design Unit, Newcastle University
Why are ultrasonic testing machines necessary?
Gearing used in certain applications (e.g. electric drive units for electrified vehicles) can be required to operate at speeds in excess of 15,000 rpm. Significant numbers of fatigue cycles are therefore accumulated within relatively short periods of operation.
Establishing a material’s fatigue strength above 107 cycles using conventional electromagnetic resonance machines is not practical due to the limited test frequencies achievable with such equipment.
Ultrasonic testing machines, such as the Shimadzu USF-2000A system, that are capable of operating at a significantly higher frequency are therefore necessary to meet the increasing demand for fatigue data in the very high cycle range.
What are your future plans and how will Shimadzu’s instrument factor into this?
Design Unit will explore funding opportunities to allow detailed investigation of the critical material properties and the differences in failure mode across the low to very high cycle fatigue range with particular emphasis on the effects of steel chemistry and cleanliness.
This study will also determine if the endurance limit for a given material drops between 107 and 1010 cycles in line with the recommendation outlined in ISO 6336-3:2006 for gears used in critical applications.
The Shimadzu USF-2000A system will therefore be key to delivering fatigue data in the very high cycle range. Furthermore, the test machine will allow screening tests up to 107 cycles to be completed in a matter of weeks rather than months which will aid the downselection of candidate materials for future research and development projects.
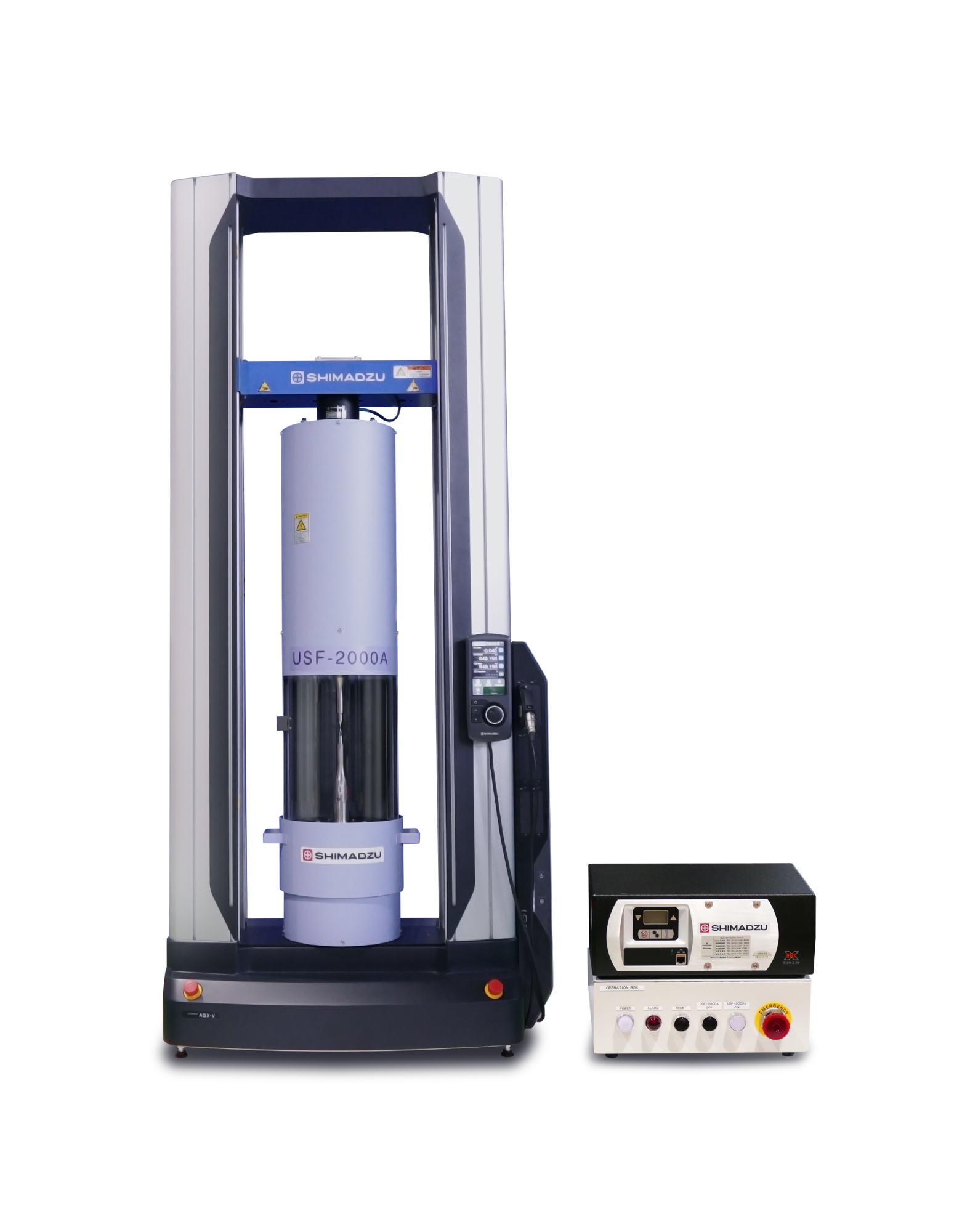
Image credit: Shimadzu UK Ltd.
What were the main factors behind selecting Shimadzu as a testing partner?
Their ability to provide a proven, market-leading solution to our technical requirements, their commitment to providing the technical support required to harness the full capabilities of the USF-2000A system as a research tool and their strong desire to establish a long-lasting collaboration between organizations were the main factors behind our decision to select Shimadzu as a testing partner.
What are the main challenges you encounter in the field of fatigue testing?
The greatest challenge we face is to ensure that our laboratory-scale fatigue tests provide knowledge and understanding that is relevant to the given application, especially when translating learning from early stage, lower TRL tests on simplified specimens to full-scale component testing.
Using test gears to generate bending and contact fatigue data helps to meet this challenge, but care must be taken to ensure that the test gears are as representative of the given application as possible in terms of their design, material selection and manufacturing route.
When evaluating contact fatigue performance, care must also be taken to ensure that the test conditions replicate the in-service operating conditions for the given application as closely as practicably possible; this can be especially challenging for gears used in high-speed applications such as EDUs for low carbon transport applications.
In terms of your plans going forward, what are you seeking to achieve and how will fatigue testing play a part?
Fatigue testing will play a vital role within our current research strategy to assist the development of efficient, low-carbon transport solutions.
Design Unit will continue to work closely with the gearing industry to identify potential pathways to increased efficiency, reduced weight and enhanced fatigue life through the optimization of steel chemistry and cleanliness, heat treatment processes, manufacturing methods, surface treatments and lubricant technology.
Where can readers find more information?
https://www.ncl.ac.uk/gears/
https://www.apcuk.co.uk/impact/funded-projects/jaguar-land-rover-hvems-uk/
About the Researcher
Chris Aylott joined Design Unit in 1999 having graduated from Newcastle University with a master’s degree in Materials Design and Engineering. Design Unit is a specialist centre with expertise in mechanical power transmission systems and is based within Newcastle University's School of Engineering. Design Unit is the UK’s largest group of its kind and has been delivering design, development, research and consultancy services to industrial engineering customers in the UK and worldwide since 1970.
Chris previously worked as the lead materials researcher on 11 projects funded by the EC, TSB/Innovate UK and the UK gearing industry. He is currently working as the lead materials researcher on the APC funded CompETe project and performs consultancy activities related to material characterisation, fatigue testing and failure analysis, a role which involves work on behalf of UK and international clients in the aerospace, automotive, defence, power generation and renewable energy sectors.
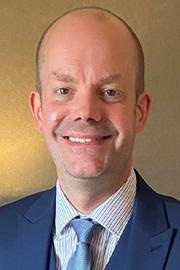
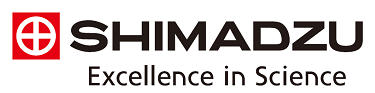
This information has been sourced, reviewed and adapted from materials provided by Shimadzu UK Limited.
For more information on this source, please visit Shimadzu UK Limited.
Disclaimer: The views expressed here are those of the interviewee and do not necessarily represent the views of AZoM.com Limited (T/A) AZoNetwork, the owner and operator of this website. This disclaimer forms part of the Terms and Conditions of use of this website.