In this Interview, AZoMaterials speaks to Boston Micro Fabrication's CEO John Kawola, about micro precision 3D printing.
What is micro-precision 3D printing, and how is it different from other 3D printing processes?
Micro-precision 3D printing is a technique used to create 3D parts with extremely high resolution, accuracy and precision, typically with features that are smaller than 100µm.
Boston Micro Fabrication uses a 3D printing approach called PμSL (Projection Micro Stereolithography) that leverages light, customizable optics, a high quality movement platform and controlled processing technology to produce the industry’s most accurate and precise high-resolution 3D prints for product development, research and industrial short run production. The technology represents a true industry breakthrough by empowering product manufacturers to capitalize on the benefits of 3D printing without sacrificing quality or scale, helping push new boundaries in innovation.
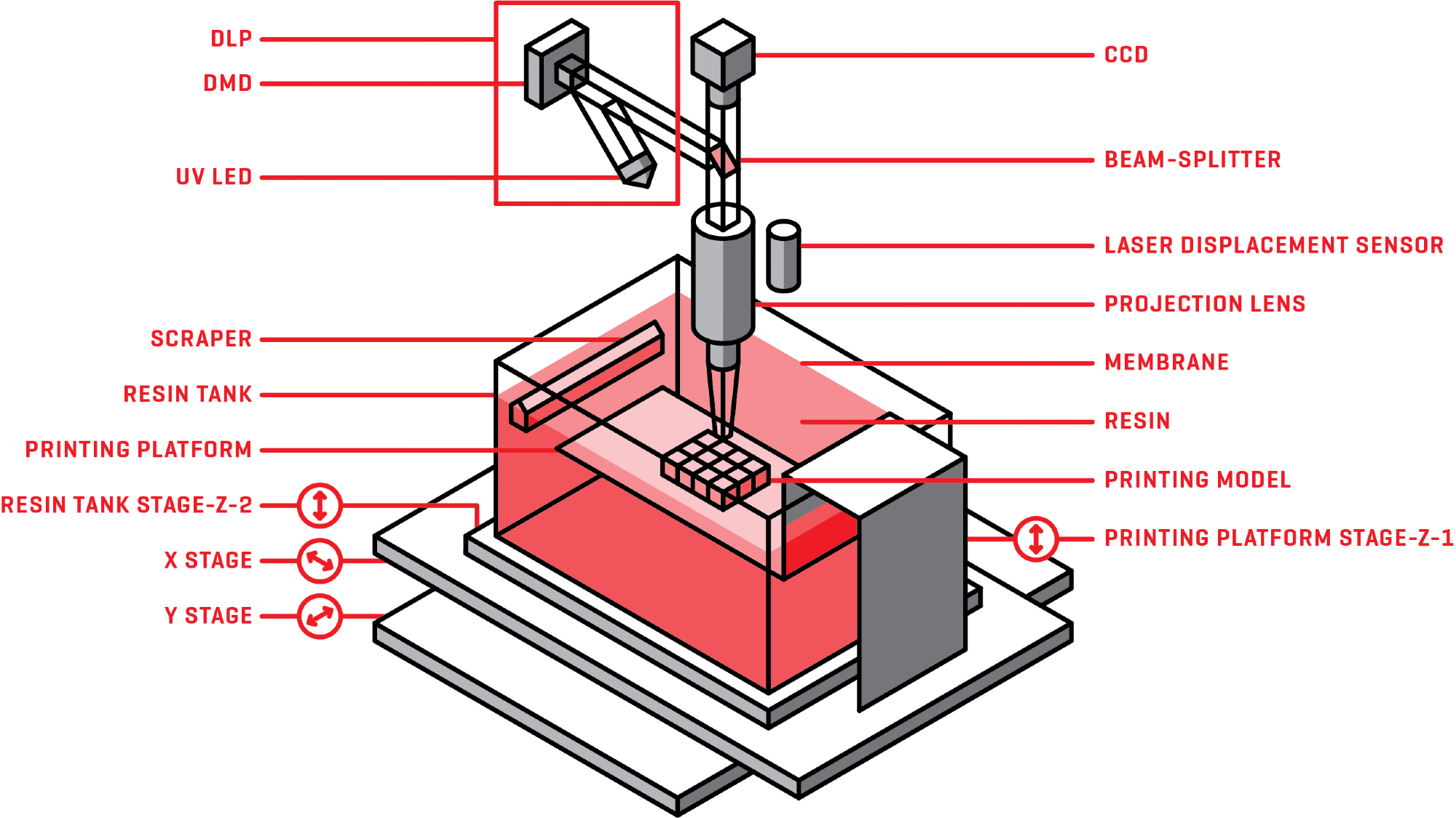
BMF’s PµSL technology
The smaller the part and the more complex the geometry, the trickier it is to manufacture. So, at BMF, we are fulfilling a real need, making prototypes and end-use parts for small, complex geometries - available faster and at much cheaper costs than other methods.
How are these parts traditionally manufactured, and how can micro 3D printing fit into the manufacturing process?
Conventionally, these parts are manufactured using injection molding. The smaller and more complex a part is, the higher the cost associated with creating a mold and the turnaround time can be months. BMF is disrupting traditional manufacturing with 3D printing, enabling engineers to create prototypes at a fraction of the time and cost to be used for fit and form testing, manufacturing aids, molding and casting tools, and end-use parts for production.
The trend toward miniaturization is growing, as the demand for smaller parts and components in the fields of medical devices, biotech, electronics, and wearables increases. However, the cost is a significant challenge in manufacturing miniaturized parts for medical devices, electronics, and optics. Traditional 3D printing struggles with producing smaller parts, but micro 3D printing can deliver precision for complex components at scales as small as a single micron.
At BMF, we are essentially helping engineers 3D print parts they have not been able to in the past - that match the quality of an injection molded part at a fraction of the cost.
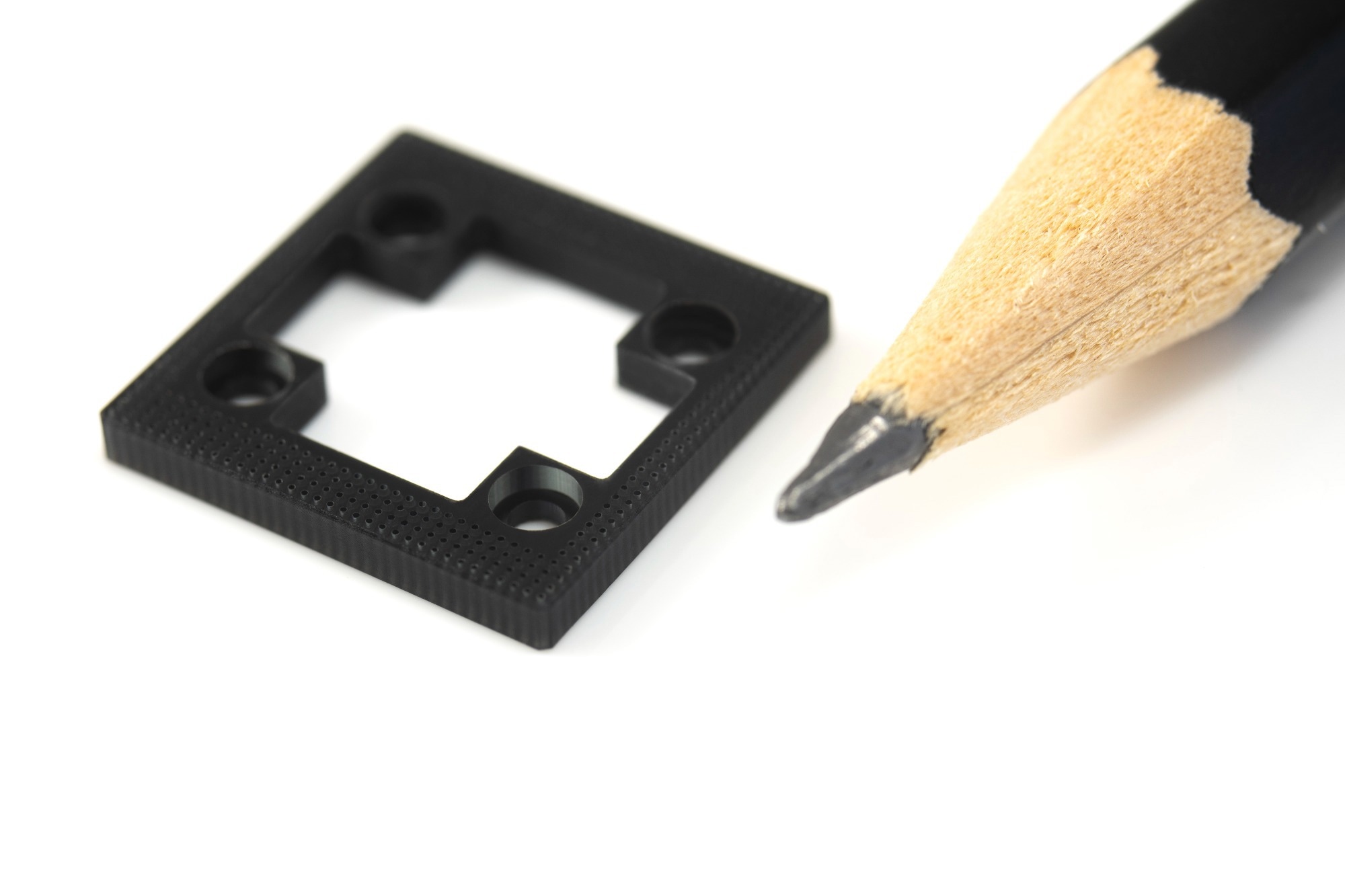
Chip Socket, Arrays of 130μm through holes
What are the economic benefits of micro 3D printing?
The elevated cost of tooling for micro-injection molds and the minimal volume of the parts requiring less material greatly impacts the cost analysis. 3D printing can be more cost-effective and efficient than traditional manufacturing processes depending on the output volume needed, and this crossover point gets higher as the parts get smaller. The fact that 3D printing doesn't require tooling has always been an advantage. This advantage is even more obvious when looking at micro-injection molding. The cost of a single cavity complex micro mold can often cost upwards of $100k.
Also key to the cost analysis, the printed parts use very little material, so material costs are minimal. With micro 3D printing, you can print tens of thousands of parts before the amortization of the tool is realized. If you only need 100's of parts, the value of micro 3D printing skyrockets. Quite simply, fabricating micro parts through traditional manufacturing methods is costly and difficult. BMF's PµSL technology is a very attractive alternate solution for complex, micro parts.
What are some applications for micro 3D printing?
Often, 3D printing is used to accelerate prototyping and design testing across a number of industries. Single-use disposable medical devices are a great fit, as well as microfluidics, electronic connectors and components and drug delivery systems. On top of these applications, we're helping advance the industry's use of 3D printing through self-drive innovation.
This method is capable of manufacturing end-use parts for short-run production, which are challenging to produce using traditional methods. For small-scale injection molding, 3D printing is a cost-effective alternative to creating molds and casting tools, as traditional machining requirements become more expensive as parts decrease in size.
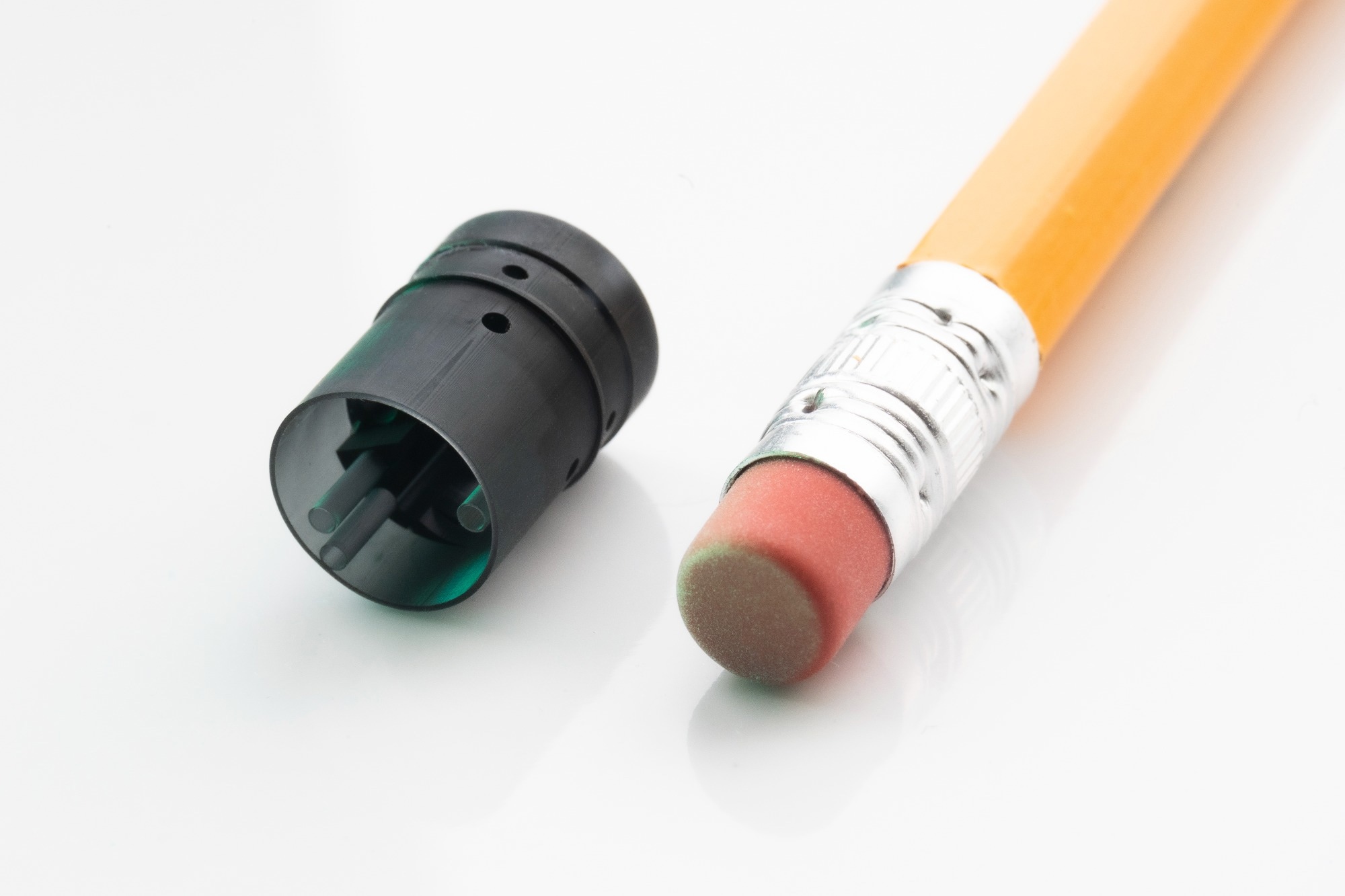
Endoscope Shell, 150μm wall thickness
Do you foresee this technology being used for more end-use production?
The shift towards short-run production using 3D printing is currently underway, with some of our early customers utilizing this technology to qualify their processes. Due to various economic factors, such as supply chain issues, many manufacturers are feeling the pressure and are thus considering this approach as an alternative solution.
Additionally, as parts become smaller, they become more expensive to produce, and the cost of injection molds for micro components can be hundreds of thousands of dollars, as opposed to $10,000. This economic reality is leading many manufacturers to explore the potential of 3D printing for their manufacturing needs.
What are the new materials that BMF has recently introduced?
At BMF, we offer a range of materials with different properties for various applications. As an open-source material company, we have our own line of formulated liquid resins that are made specifically for our line of micro-precision 3D printers, but we also partner with material companies to provide third-party material options that give flexibility based on the application.
We have recently developed and validated several new materials which are now available for use on BMF’s microArch platforms. These include BMF MED and LOCTITE 3D 3955. BMF MED powered by 3D Systems is a custom-formulated biocompatible resin that meets the requirements of FDA class II biocompatibility. This combined with its great aging properties makes it suitable for end-use medical devices, pharmaceutical, and research applications. This resin also features fast and simple post-processing requirements for improved ease of use.
We also recently collaborated with Henkel to validate LOCTITE 3D 3955 for use on the microArch platforms. This material is compatible with our new microArch S350 printer for printing flame-resistant parts at 25µm resolution. This high-performance halogen-free flame retardant UL94-V0 high modulus photopolymer resin is suitable for end-use parts including electrical connectors, housings, electronic components, and other parts requiring high flame resistance or the ability to withstand harsh environments.
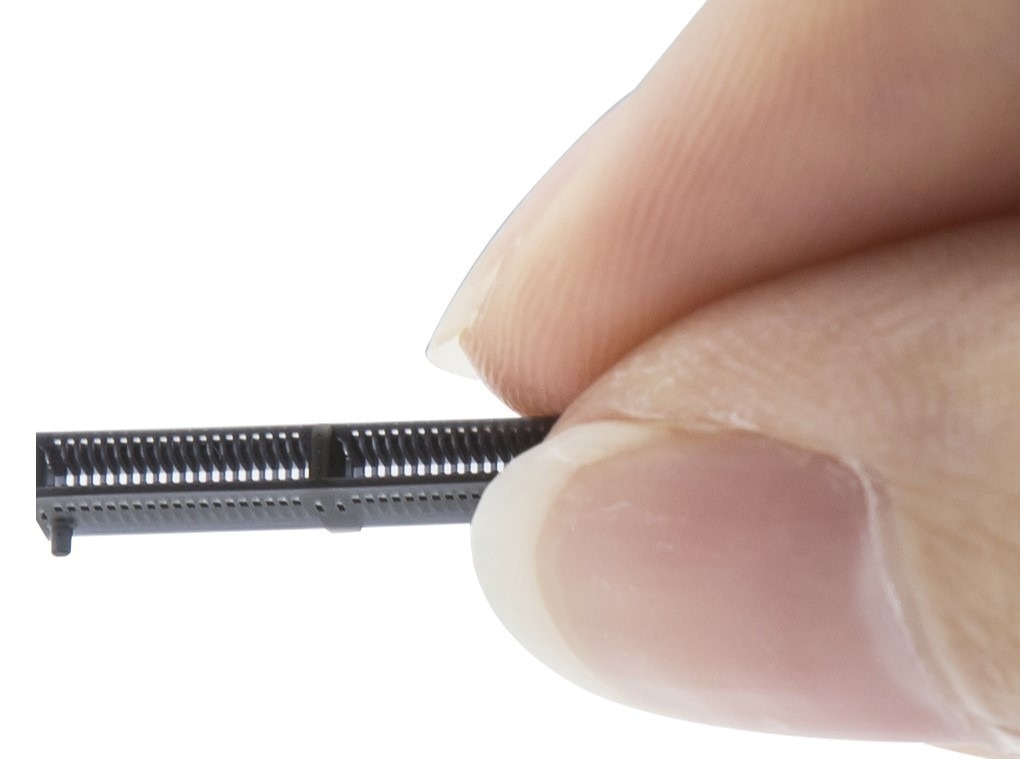
3D Printed Electronic Connector, 280 μm spacing between connector teeth
How sturdy are these parts compared to plastic injection molded parts?
Recent advances in 3D printing have led to materials with mechanical properties approaching those of traditional injection molding materials. End-use materials are now reaching 90% of the strength and flexibility of injection molding materials. Functional designs are now possible using these materials.
What does the post-processing of parts involve?
Post-processing for DLP or SLA-based part production involves post-washing to remove uncured resin and removing supports. Our photo-polymer-based process follows the same steps, but our small parts require less solvent and support. Form Wash and Form Cure devices are used for post-processing and are effective for our micro 3D printed parts.
Can you tell us about your printers?
Boston Micro Fabrication delivers one of the highest levels of precision available on the market, and we manufacture and sell printers capable of achieving 2µm, 10µm and 25µm resolution parts. Our 2µm series includes the microArch S130 and S230, both capable of achieving tolerances within +/-10µm.
Our 10µm series includes the microArch S140 and S240, both capable of achieving tolerances within +/-25µm.
Our newest printer, the microArch S350 is a 25µm platform, capable of achieiving +/- 50µm tolerance.
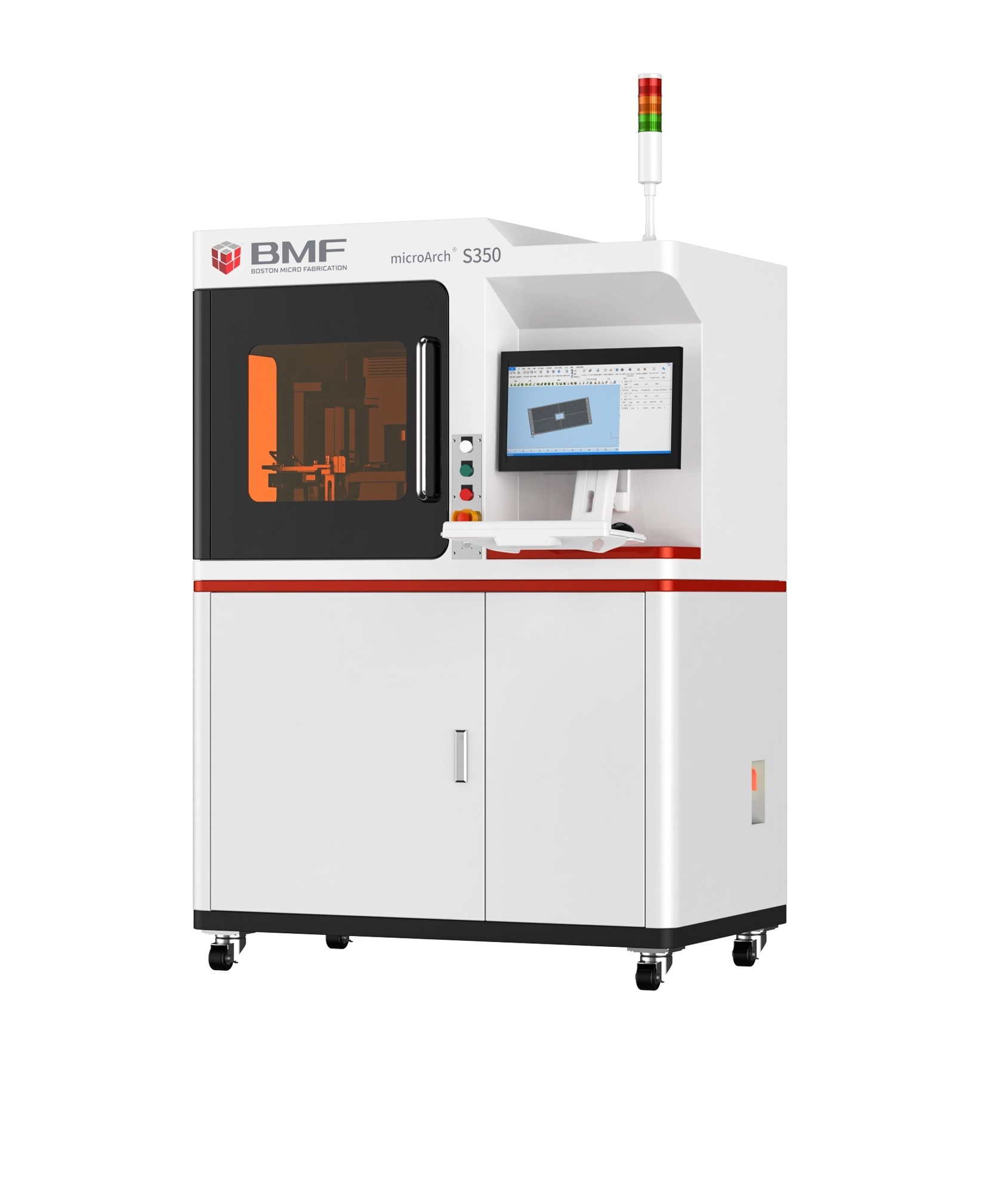
MicroArch S350
What is the achievable surface roughness of the parts?
Surface finish ranges between 0.5 to 2 microns RA, depending on the orientation of the surface. Feature size is usually a multiple of the resolution, such as 10 microns or 2 microns. For example, a 10-micron resolution can produce features of approximately 50 microns, while a 2-micron resolution can achieve features of around 10 microns.
Cleaning of the printing channels is essential. Can you provide an overview of this process and what it involves?
The uncured resin inside the channel must be removed after printing, which we have accomplished using various techniques, such as chemical washing and vacuum removal, developed in the past 18 months.
Do you offer sample parts?
We offer sample parts and benchmark parts at no cost to prospective customers to evaluate our technology, which is a crucial aspect of our sales process. If you'd like to request a sample part, please visit our website and submit a request.
About John Kawola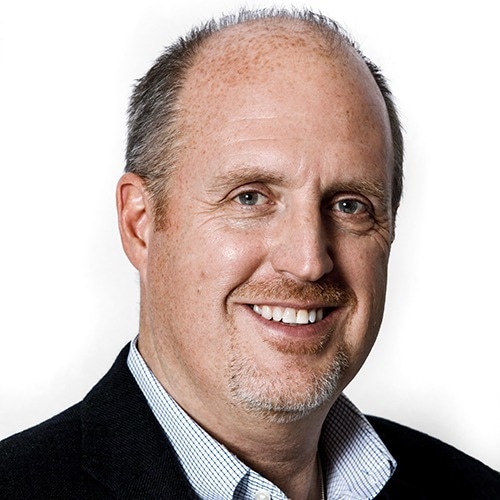
John is the CEO of Boston Micro Fabrication (BMF) an additive manufacturing technology company with a focus on high resolution, accuracy and precision. From 2016 to 2019, John served as President-Americas for Ultimaker, the leading open source desktop 3D printing company. From 2012 to 2016, John was the CEO of Harvest Automation. Harvest developed and deployed an autonomous mobile robotic platform that assists workers with difficult, repetitive material handling. John was VP of Sales and then CEO of Z Corporation from 1997 until 2012. Z Corporation led the way in introducing fast, easy to use and full color 3D printing into a wide range of industries. John is also currently the Chairman of Labminds, a laboratory automation technology company and a Board Director at Industrial ML, an industrial machine learning company. John received a BS in Mechanical Engineering from Cornell University, MS in Mechanical Engineering from Rensselaer and an MBA from Union College.
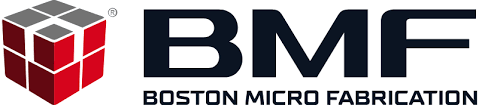
This information has been sourced, reviewed and adapted from materials provided by Boston Micro Fabrication (BMF).
For more information on this source, please visit Boston Micro Fabrication (BMF).
Disclaimer: The views expressed here are those of the interviewee and do not necessarily represent the views of AZoM.com Limited (T/A) AZoNetwork, the owner and operator of this website. This disclaimer forms part of the Terms and Conditions of use of this website.