Government and space agencies are investing significantly in free space laser communications to meet the demands of data-intensive applications. By leveraging multiple wavelengths, laser sources have the potential to achieve data transfer rates that far exceed those of traditional radio-frequency (RF) communications.
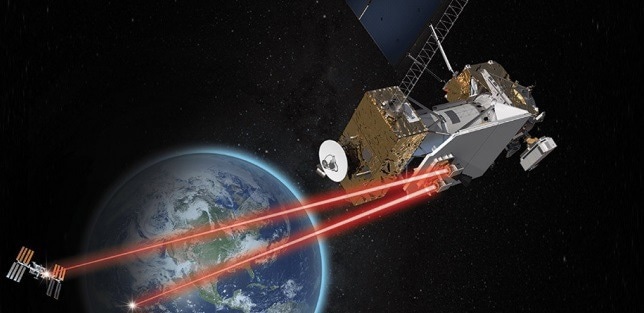
NASA’s Laser Communications Relay Demonstration communicating with the International Space Station over laser links. Image Credit: NASA’s Goddard Space Flight Center.
However, establishing those data linkages necessitates optics that exceed the capabilities of today's manufacturing processes and metrology to validate them. 4D Technology metrology solutions are leading the way in regulating wavefront error, surface figure, and surface roughness at critical wavelength bands.
What is Driving the Switch to Optical Communications?
Telecommunications companies have relied heavily on RF communication as the primary signal transmission method for years.
These companies are now focusing on laser-based communications for uplink, downlink, and data transfer purposes between satellites and terrestrial stations in situations where traditional cable or fiber connections are not viable. This transition is motivated by several significant factors.
Data volume and transfer speed
The escalating demand for more extensive data volumes from government, defense, and commercial entities has increased the need for optical communications, providing a significantly higher data capacity than RF systems.
While RF systems operate within the frequency range of 300 Hz–300 GHz, optical systems can operate at frequencies exceeding 300 THz. Due to their shorter wavelengths, optical beams retain better focus during propagation, resulting in increased power collection by the receiver and a higher signal-to-noise ratio (SNR).1
Providers can substantially boost data rates by employing multiple wavelength bands simultaneously. However, this approach introduces greater complexity and places additional demands on the system optics.
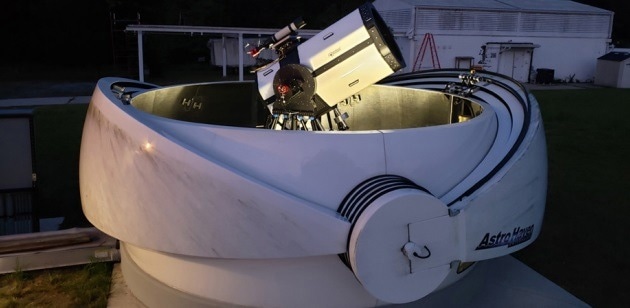
NASA’s Low-Cost Optical Terminal (LCOT) prototype ground telescope. Image Credit: NASA
Security
Radio and microwave communication beams have a wide spread, rendering them vulnerable to interception, jamming, and frequency interference.
As the beam from a spacecraft travels toward the receiver, it can expand to hundreds of kilometers in width. In contrast, an optical return beam within the C band can be as narrow as tens of meters at the receiver. This significantly tighter beam enhances security and renders the signals virtually undetectable.
Cost
Optical systems offer the advantage of transmitting vast amounts of data over extended distances while utilizing fewer and smaller transmitters and receivers. This reduced hardware size and weight directly impacts payload satellites and spacecraft, leading to substantial cost savings.
Consequently, due to these advantageous characteristics, the government, defense groups, and various space agencies have been early adopters of optical communications.
With these entities' successful validation of the technology and the significant reduction in space access costs over the past decade, commercial applications are now expanding, particularly in air-to-air, maritime, and remote settings where fiber connections are impractical.
Metrology to Meet Optical Communication Challenges
Stringent controls must be applied to the optical components and systems transmitting, relaying, and receiving these signals. Thorough testing of the components at each functional wavelength is crucial to comprehend the beams' propagation, spread, and scattering.
Previously, optical technology predominantly operated at wavelengths within 950 nm and 1064 nm. However, the industry is currently focused on expanding communications in the C-band, which has received approval for communications and undergone extensive testing, helping increase the adoption rate.
4D Technology has been at the forefront of metrology development for space-based optics for over two decades.
The instruments have played a pivotal role in testing optical systems for numerous space missions and payload satellites, contributing to multiple innovations that ensure the quality and durability of these optics, enabling them to withstand the rigorous demands of space.
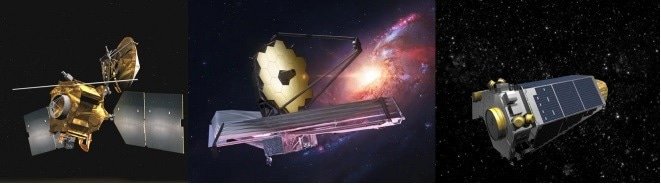
4D Technology has been enabling space-based optics innovation for over 20 years. Left to right: HiRISE Mars imager, JWST observatory, and Kepler exoplanet observatory. Image Credit: 4D Technology
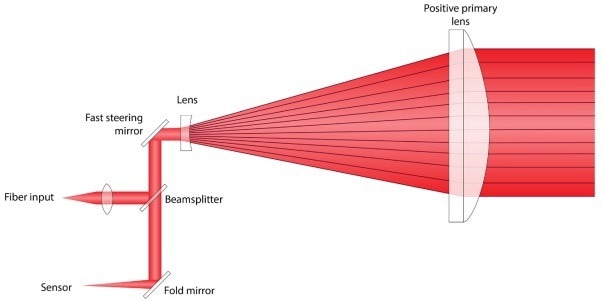
Generic optical layout for a communications telescope. Image Credit: 4D Technology
The 4D AccuFiz® SWIR Fizeau Interferometer and PhaseCam® Twyman-Green SWIR Interferometer, operating around the 1550 nm wavelength, offer several advantages for optical measurements, which include:
- Compact, lightweight design that simplifies test setups
- Vibration immunity allows measurements in challenging environments without the need for isolation.
- Unique capability to accept external sources at wavelengths throughout the C-Band, enabling manufacturers to test optical components and systems at every operational wavelength.
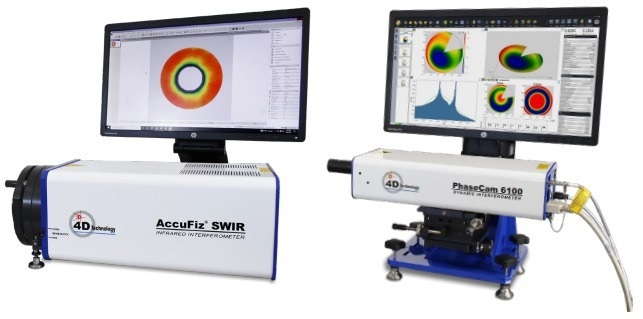
AccuFiz Fizeau and PhaseCam Twyman-Green interferometers for vibration-insensitive testing throughout the C-Band. Image Credit: 4D Technology
Measuring Despite Vibration
Dynamic interferometry is a transformative technology that enables vibration-immune and instantaneous measurement of optical components and systems. This technology has demonstrated immense value in the testing of optics, particularly in the following scenarios:
- Vibration-heavy environments, such as cryovac environmental chambers
- Long cavity measurements
- Small and large optics
- Real-time system alignment
Both the PhaseCam SWIR and AccuFiz SWIR instruments are equipped with dynamic measurement capabilities, significantly reducing the need for vibration isolation and substantially lowering the cost of testing these crucial optics.
Measure at Functional Wavelengths
The PhaseCam and AccuFiz instruments accurately measure surface figures and transmit wavefront error for focal and afocal optics, aspherical lenses, optical systems, telescopes, prisms, corner cubes, and more.
The AccuFiz features a large aperture, making it suitable for rapid and repeated measurements of optical components. On the other hand, the PhaseCam is a fully on-axis instrument that incorporates a built-in beam ratio adjustment, measures low return systems, and is particularly adept at measuring aspheric optics using a Computer Generated Hologram (CGH).
Real-Time Alignment and Collimation
Continuous Mode allows us to compute and visualize the Zernike coefficients of an optical component or system, offering real-time feedback for swiftly aligning and collimating parts of free-space optical systems.
Measuring Roughness
Surface roughness represents a crucial factor in optical communications.
Excessive beam scattering results in:
- Signal loss and diminished data transfer rates.
- Crosstalk between different channels within multi-wavelength systems
- Amplification of thermal changes, leading to thermal stresses that can deform the optical shape
The NanoCam HD optical profiler has been specifically engineered to measure roughness on optical-grade surfaces to address these concerns.
Whether mounted on a robot or used in a handheld configuration, the NanoCam swiftly captures measurements at multiple locations across an optic to ensure that roughness falls within all specifications.
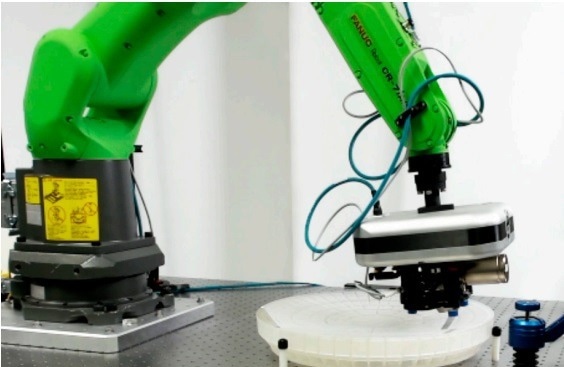
NanoCam HD mounted on robot for production roughness measurements. Image Credit: 4D Technology
Conclusion
4D Technology's metrology systems offer vibration-insensitive testing capabilities tailored explicitly for the wavelengths essential in optical communications.
With a diverse range of products boasting unique capabilities, coupled with their extensive experience in optics for communications and telescopes spanning several decades, 4D Technology is actively supporting the pursuit of enhanced data throughput, heightened security, and improved reliability within the industry.
References and Further Reading
- Sburlan, S. (2016), Introduction to Optical Communications for Satellites [Powerpoint presentation]. Available at: https://kiss.caltech.edu/workshops/optcomm/presentations/Sburlan.pdf (Accessed: 2/17/23)

This information has been sourced, reviewed and adapted from materials provided by 4D Technology.
For more information on this source, please visit 4D Technology.