Concerns about corrosion, corrosion control, and testing are essential for industries producing items susceptible to corrosive elements like chemicals, oxygen, water, electrolytes, and UV light. This article will outline the nature of corrosion, methods of prevention, protective coatings, and the significance of testing.
What is Corrosion and How can it be Prevented?
Corrosion is the breakdown of metal, stone, or other materials. The most prevalent form of corrosion is rust, a chemical reaction when iron combines with oxygen and water. Rust commonly affects unprotected metal exposed to wet or humid conditions.
Corrosion Prevention and Control (CPC) involves thwarting substrate deterioration by minimizing chemical reactions causing corrosion. This is achieved by altering the environment, changing materials, or placing a barrier between the material and its surroundings.
A system is established to delay, diminish, or prevent corrosion through material selection, non-destructive inspections, protective coatings, finishes, and surface preparation, including cleaning, repairs, and maintenance.
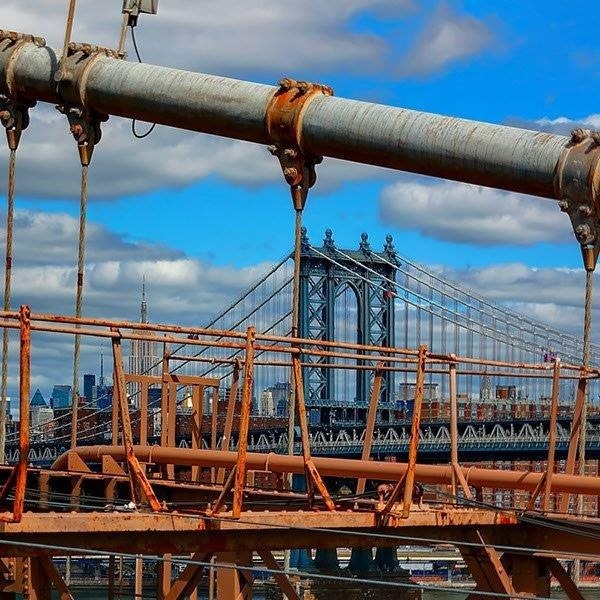
Image Credit: Paul N. Gardner Company, Inc.
Why Use Protective Coatings?
Protective coatings, including paint, resin, or powder coatings, are commonly employed to safeguard composite, metal, or alloy surfaces from corrosive conditions. These coatings offer a straightforward approach to mitigating corrosion by restricting surface exposure to corrosive elements like oxygen, water, electrolytes, and UV light.
Various protective layers can be administered, creating a barrier that depends on factors such as coating quality, material selection, application, and handling of painted and powder-coated materials.
In metal protection, there are four types of coatings: barrier, inhibitive, sacrificial, and combination. Barrier coatings shield metal by preventing contact with water, oxygen, and electrolytes. Inhibitive coatings incorporate chemicals that impede corrosion.
Sacrificial coatings provide galvanic protection by sacrificing themselves instead of the underlying metal, generating electrons to reverse corrosion.
For aluminum alloy surfaces, a typical application involves three protective coating layers: chromate conversion coating, primer coating, and a top layer coating.
Applying these coatings with care is essential to prevent damage and ensure longevity. Special fabrication and surface preparation procedures are necessary for equipment like tanks and pipes to undergo proper coating for effective corrosion control.
The pivotal step in coating systems' ultimate performance is surface preparation. Contaminants such as oil, grease, mud, or salts must be removed using appropriate chemical and mechanical methods before blasting.
Failure to address contaminants can lead to coating delamination, underscoring the importance of a well-adhered, regularly maintained coating to safeguard the metal.
Importance of Physical Testing
Conducting physical tests on coatings is vital to ascertain their quality, durability, and service life.
One can ensure that the coating or barrier protects the substrate by assessing corrosion, surface finish requirements, wear resistance, lubrication, and aesthetics. Without proper testing, the likelihood of coating failures increases significantly.
Physical tests to evaluate the integrity of protective coatings:
- Abrasion Test: Evaluates wear resistance and coating reliability
- Holiday Test: Continuity Test that identifies unacceptable discontinuities like pinholes and voids
- Bond Adhesion Test: Adhesion Test that measures the force needed to break or crack the coating
- Bend Test: Adhesion Test that detects peeling or flaking of the coating
- Coating Mass Test:
- Contamination Test: Detects unwanted deposits like iron, oxide, rust, grease, and more
- High Humidity Test: Determines performance in severe environments with elevated temperatures and humidity fluctuations
- Black Light Test: Offers a quick visual check of surface cleanliness
- Copper Sulfate Test: Assesses the effectiveness of stainless-steel passivation treatment
- Ferroxyl Test: Identifies porosity in metal coatings like copper, nickel, lead, or tin on iron or steel
- Coating Moisture Test: Moisture Test that measures absorbed moisture and surface wetting
- Coating Thickness Test: Coating Thickness Tests, Wet Film Thickness, and Dry Film Thickness determine coating thickness, weld overlay, corroded sample wall thickness, and similar applications
- Embrittlement Test: Coating Ductility Test that assesses the loss of material ductility without deformation
- Cathodic Disbonding Testing: Disbonding Test that measures resistance to cathodic bonding between coatings and metal substrates
- Surface Profile Test: Ensures the proper surface profile for adhesion using methods like Testex or similar tape
- Surface Salt Test: Measures salt contamination that can lead to coating failure, using tests like Bresle patches or Chlor Test
- Cross Hatch Adhesion Test: Also known as cross-cut, this test measures adhesion by cutting the surface and applying tape
- Pull-Off Adhesion Test: Measures the force required to remove a coating from a surface
- Surface Temperature: Ensures proper curing of coatings
- Dew Point Measurement: Ensures no trapped condensation between the surface and the coating, preventing coating failure and corrosion
The primary industrial uses include:
- Shipbuilding
- Marine applications
- Pipelines, gas, and oil sectors
- Chemical production
- Automotive industry
- Construction
- Architecture
- Electrical works
- Farming
- Manufacturing
- Machinery production
- Fire safety
- Railways
- Mining operations
- Bridges
- Water tanks
- Dams
- Tunnels
- Power utilities
In conclusion, safeguarding composite, metal, or alloy surfaces from corrosive elements relies heavily on corrosion control and protective coatings. These coatings limit surface exposure, a critical step in preserving their integrity.
Ensuring the substrate, coating, and its application undergo thorough physical testing is equally essential.
The actual toll of corrosion extends beyond monetary value; it encompasses personal safety and investor trust. Protective coatings and their testing play pivotal roles in ensuring the safety, longevity, performance, and visual appeal of equipment and structures. Their presence promotes overall health and well-being across industries.
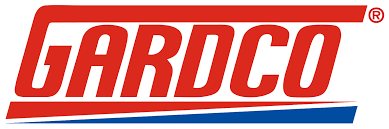
This information has been sourced, reviewed and adapted from materials provided by Paul N. Gardner Company, Inc.
For more information on this source, please visit Paul N. Gardner Company, Inc.