In this interview, Annika Völp discusses QC and research into battery slurries through rotational rheology.
Could you please introduce rheology and the application of rotational rheometry in battery manufacturing and research?
Rotational rheology is a critical tool for both quality control and research of battery slurries, as well as semi-dry or solvent-free processed cathode films. Rheology, the science of studying how materials flow and deform, plays a vital role in these areas. Rotational rheometers measure various properties such as viscosity as a function of shear rate and temperature, structure recovery, yield stress, and zero shear viscosity of slurries. They also evaluate the viscoelastic behavior of dry process electrode films. In contrast, spindle viscometers offer limited insights, providing only apparent viscosity values at fixed shear rates.
Understanding the rheology of battery pastes is crucial for optimizing quality control processes, it saves time and reduces costs in developing new formulations, and processing techniques. Moreover, rheology aids in predicting the storage stability of slurries and their behavior during the electrode coating process.
What exactly is a rotational rheometer?
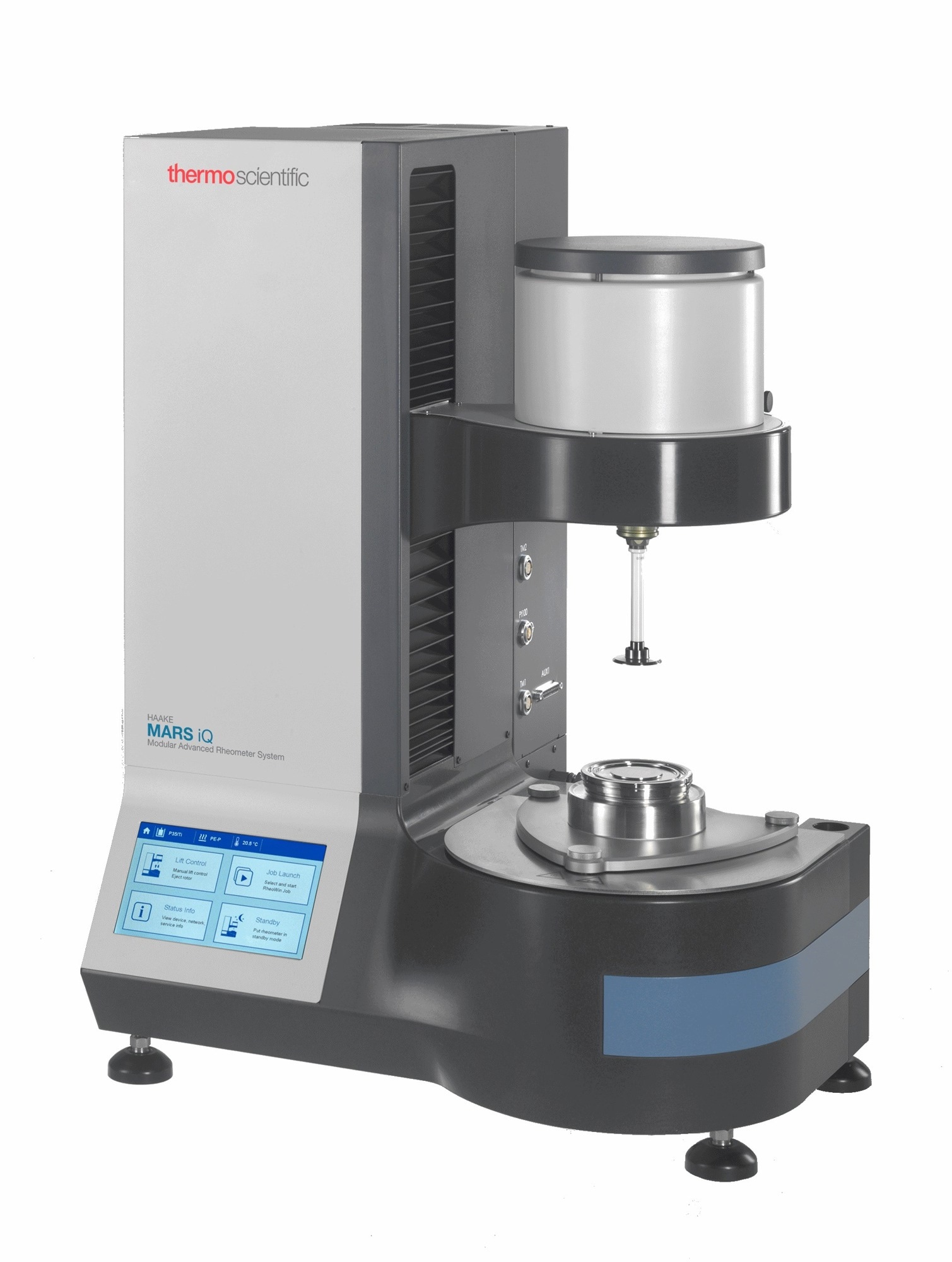
Thermo Scientific™ HAAKE™ MARS™ Rotational Rheometer. Image credit: Thermo Fisher Scientific
Rotational rheometers are sophisticated devices used to investigate the flow properties of a wide range of materials under various conditions. They are invaluable across many industries for the quality control of raw materials, intermediates, and final products, as well as for the development of new formulations. These instruments provide detailed insights into a material’s rheological behavior, which is essential for ensuring proper performance in specific applications or processing.
A rotational rheometer works by placing a sample in a measuring geometry where it undergoes a defined shear stress or deformation, with the machine measuring the material’s response. This response is then used to compute rheological parameters. Modern rheometers can apply shear stresses or shear strains through continuous rotation or sinusoidal oscillation, with oscillation modes offering deep insights into the viscoelastic properties of materials.
What parameters are important when using a rotational rheometer?
When using a rotational rheometer, several parameters are crucial:
- Viscosity: Indicates a material’s resistance to flow, with dynamic viscosity being the ratio of shear stress to shear rate.
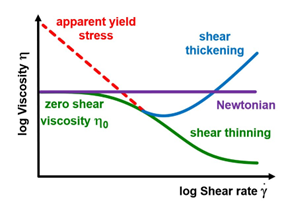
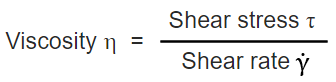
Image credit: Thermo Fisher Scientific
- Shear Stress: Proportional to the force applied or the rotor torque in the rheometer.
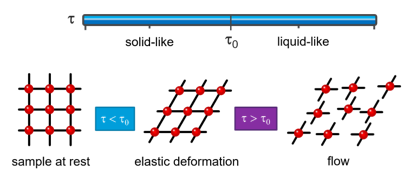
Image credit: Thermo Fisher Scientific
- Shear Rate: The rate at which the material deforms over time, similar to the rotor speed in a rheometer.
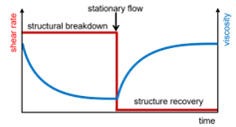
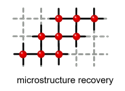
When shear forces are removed, the microstructure will recover. Image credit: Thermo Fisher Scientific
Fluids are also classified based on their response to shear:
- Newtonian Fluids maintain a constant viscosity regardless of shear rate changes.
- Shear Thickening Fluids, like a starch-water mix, viscosity increases as the shear rate rises.
- Shear Thinning Fluids, such as ketchup, viscosity decreases with increasing shear rate.
Additional advanced properties include Zero Shear Viscosity, and Viscoelastic Materials, which behave like solids under low stress and like fluids under high stress.
Yield stress is the minimum shear stress to overcome irreversible elastic deformation and flow. The onset of flow is dependent on the structural breakdown of the material.
Thixotropy, which describes the time-dependent change in material structure, is also crucial.
How do rheometers integrate into the manufacturing workflow for lithium-ion battery electrodes?
Rheometers are integral to the manufacturing workflow of lithium-ion battery electrodes, primarily for evaluating the rheology of electrode slurries—a crucial quality indicator. These devices are essential for quality control, as they enable precise characterization of the viscosity and shear rate dependence of both anode and cathode slurries. Such detailed characterization is critical, as it helps predict the slurry’s dispersion stability during storage and its behavior throughout the coating process.
Employed for several vital functions, rheometers ensure consistent slurry mixing, which is pivotal for maintaining quality across production batches. They also assist in the development of new slurry formulations and in tailoring slurry rheology to optimize the coating process. While spindle viscometers are often used for their simplicity, they only provide measurements of apparent viscosities.
In contrast, rotational rheometers are indispensable for their ability to deliver precise viscosity measurements under defined flow conditions, offering a more accurate assessment of material properties. This precision is vital for enhancing the manufacturing efficiency and quality of lithium-ion battery electrodes.
Why is measuring viscosity crucial for electrode slurries?
Electrode slurries exhibit shear-thinning behavior, where their viscosity decreases as shear rates increase—from high levels at low shear rates to lower levels at higher shear rates. This property is beneficial for several reasons. When at rest or at low shear rates, the high viscosity helps prevent sedimentation or aggregation, enhancing the shelf life of the slurry and reducing the need for frequent agitation during storage.
Additionally, high shear rates occur during the application of the slurry to the current collector foil using slot-die coating. To achieve an effective and uniform coating that maintains consistent layer thickness, it is crucial to control the slurry’s viscosity within an optimal range, ensuring it is neither too high nor too low.
Therefore, detailed viscosity profiles that span from low to high shear rates are essential. These profiles are critical for predicting and managing various aspects throughout the processing cycle of an electrode slurry, such as ensuring stability and proper storage behavior at low shear rates, optimizing the mixing process at medium shear rates, and refining the slot-die coating process at high shear rates.
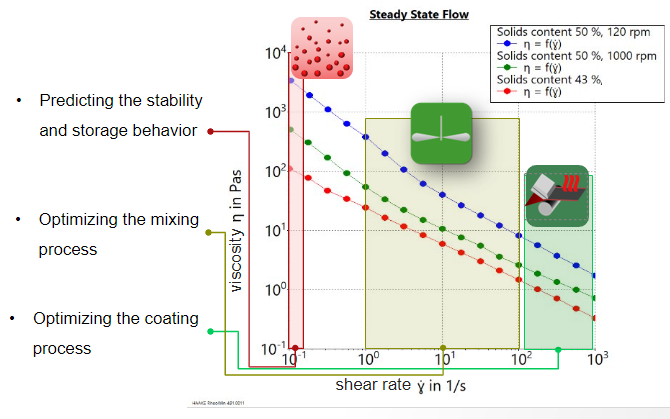
Measuring the viscosity in continuous rotational deformation over a broad range of shear rates reveals the dispersion quality of slurries, their processability, and stability. Image credit: Thermo Fisher Scientific
Can you give an example of a workflow where a rheometer has been used to measure viscosity in an electrode slurry?
In a specific study, we evaluated the viscosity response to varying shear rates for an aqueous LFP (Lithium Iron Phosphate) based cathode slurry. This slurry had two different solid contents: 43 % and 50 %.
We prepared the slurries using a lab-scale twin screw extruder operated at speeds of 100 RPM for the lower solid content and 1,000 RPM for the higher solid content. The viscosities of these slurries were then measured using a HAAKE MARS Rheometer equipped with 35-millimeter parallel plates, employing a steady rotational shear deformation method.
The results showed a significant increase in viscosity with the addition of 7 % more solid content—at a shear rate of one reciprocal second, the viscosity increased by more than an order of magnitude. However, for the 50 % solid content slurry, applying higher shear forces during the mixing process (achieved by increasing the extruder speed) considerably reduced the viscosity.
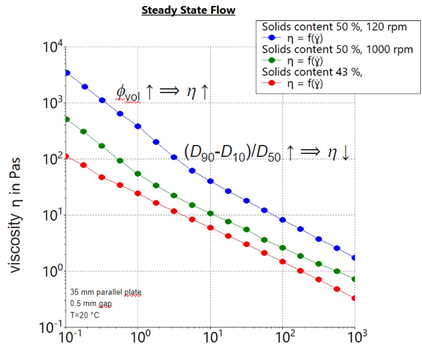
Viscosity curve versus shear rate reveals changes in solid content, particle size distribution, dispersion of carbon black and binders. Image credit: Thermo Fisher Scientific
This reduction in viscosity is attributed to the broadened particle size distribution, which, while potentially less favorable for battery electrochemistry, generally decreases the viscosity of the suspension. This example highlights how manipulating process parameters like extruder speed and analyzing viscosity at different shear rates can help tailor slurry properties for optimal electrode manufacturing.
How can a rheometer inform about the effects of screw speed?
A rheometer can provide valuable insights into the effects of screw speed on the particle size distribution and rheology of an anode paste mix.
In a specific study, the role of screw speed was explored using a twin-screw extruder to process the anode slurry. As the screw speed was increased, there was a notable shift in the particle size distribution toward smaller sizes in the anode slurry. This effect is primarily due to the capability of the extruder, which largely depends on the design and speed of the screws, to effectively break up carbon black agglomerates.
By using a rheometer to measure the viscosity of the anode slurry across different shear rates, we can track the rheological changes that result from modifications in particle size distribution. A notable increase in viscosity correlates with the presence of smaller particle sizes. This observation underscores that the viscosity of the slurry is influenced not only by its composition but also significantly by its structural characteristics, which are affected by the mechanical action of the screw speed in the extruder.
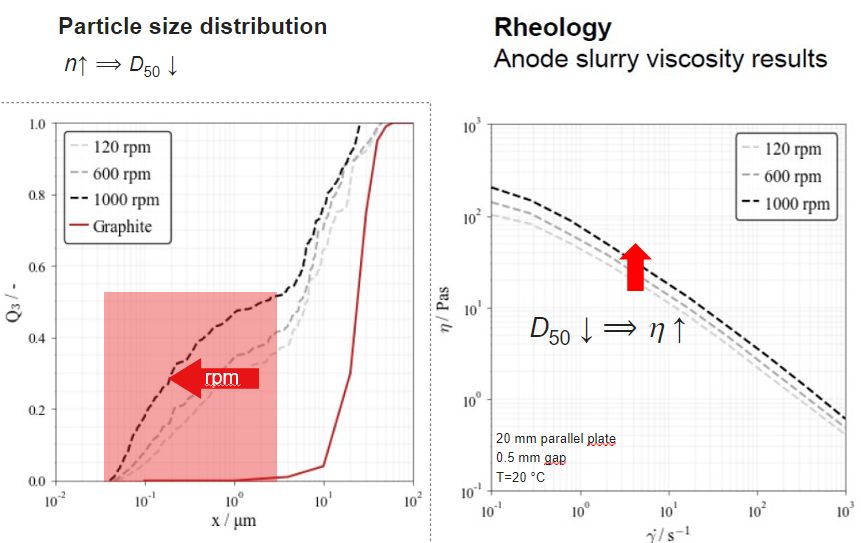
Analysis of the effect of screw speed on slurry rheology, particle sizes (PSD) and homogeneity. Image credit: Thermo Fisher Scientific
This insight enables the optimization of extrusion parameters to achieve desired rheological properties in the slurry, thereby enhancing processing efficiency and potentially improving the performance characteristics of the final battery product.
How can a rheometer help us to understand slurry stability?
The yield stress of a suspension is defined as the minimum stress required to initiate flow. When a sample is subjected to increasing shear stress, the deformation increases linearly up to the yield stress point, beyond which the sample deforms disproportionately.
Understanding yield stress is crucial as it informs us about the suspension’s resistance to sedimentation during storage, and it helps predict the spread of the coating after it is applied via slot-die coating.
Thixotropy in slurries, indicating their stability under coating conditions, can be assessed through a shear recovery test. In this test, slurries are subjected to a low shear stress of 0.1 reciprocal seconds until a steady viscosity is achieved. The slurries are then exposed to a high shear rate, simulating the conditions in a slot-die coater.
When the shear rate is abruptly changed back to the low shear rate, the viscosity is then plotted against time, allowing you to measure how quickly the viscosity recovers to its initial value before exposure to the high shear. The faster the structural recovery, the less spreading, and bleeding exhibited by a coated slurry.
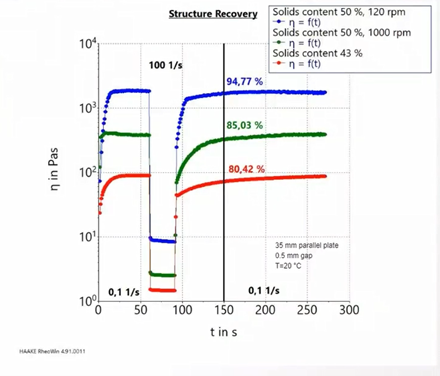
Transition between solid and liquid behavior of LFP cathode slurries. Image credit: Thermo Fisher Scientific
Additionally, slurry stability can be evaluated using a creep test. Here, slurries undergo constant stress, and their deformation over time is tracked. Typically, deformation responds linearly over time. By analyzing the deformation versus time graph’s slope, the shear rate is determined.
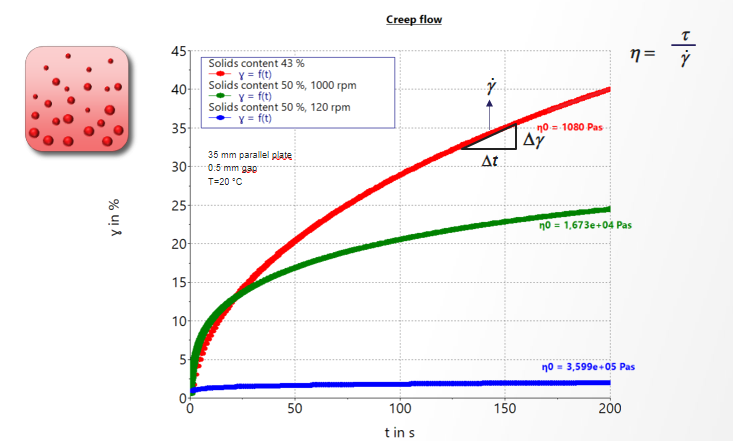
Stress relaxation predicts sedimentation behavior. Image credit: Thermo Fisher Scientific
Zero shear viscosity is then calculated by dividing the applied stress by this shear rate. A lower zero shear viscosity suggests reduced storage stability of the slurry, highlighting the importance of these measurements in optimizing slurry formulations for better performance and reliability.
How can rotational rheometers be used to characterize viscoelastic material?
Rotational rheometers are instrumental in characterizing the viscoelastic properties of materials, particularly useful when creating solvent-reduced or dry cathode or anode films— a promising area that remains under investigation due to the complexities involved in scaling up.
The viscoelastic behavior can be optimized by selecting appropriate binder systems and adjusting processing parameters in the mixing and calendaring stages. Knowledge of the film’s viscoelasticity allows for the fine-tuning of these steps.
For such measurements, the rheometer must be capable of oscillatory deformation of the sample. A common test performed in this mode is known as an amplitude sweep. During this test, the material undergoes a series of incrementally increasing deformation amplitudes at a constant frequency. This procedure sheds light on the overall structure of the material, determining whether it behaves more like a liquid or a solid and assessing the firmness and structural stability.
The information that can be extracted from this sort of experiment includes the storage modulus G prime, which is a constant value at low strain values in the linear viscoelastic regime and serves as a parameter for stiffness. The loss modulus G double prime in a linear viscoelastic range is a parameter for cohesion.
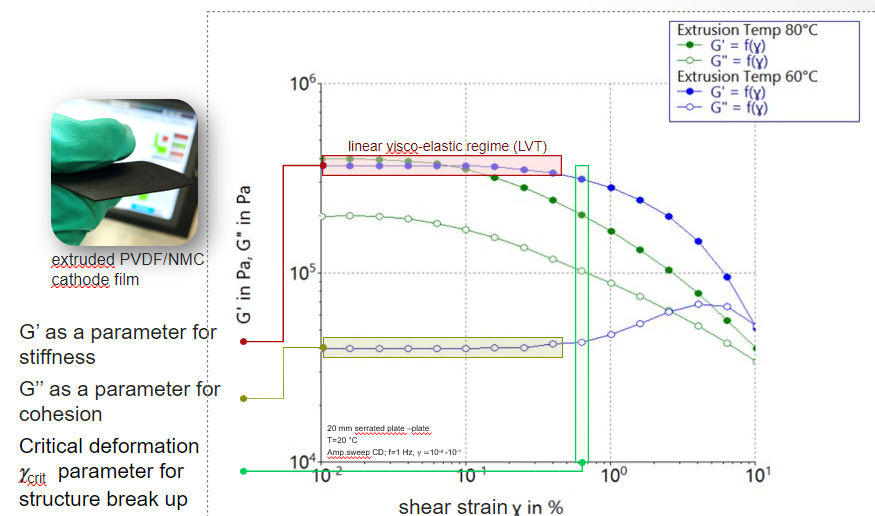
Characterization of shear stress in sinusoidal oscillatory deformation reveals viscoelastic parameters defining. Image credit: Thermo Fisher Scientific
Additionally, the critical deformation point, where the linear viscoelastic range ends, marks the structural breakdown and indicates the sample’s stability. For example, in an amplitude sweep test on semi-dry extruded PVDF and MC cathode films, it may be observed that materials mixed at lower temperatures exhibit comparable stiffness to those processed at higher temperatures but are more resilient to significant deformations.
How can oscillatory rheology be used to characterize fibrillation and network strength in dry PTFE electrode films?
In another application, we did an amplitude sweep test on a PTFE graphite mixture that was mixed with a twin-screw extruder and passed through one or two mixing zones. PTFE is known to form fibers under the shear and acts as a binder in dry-processed electrodes.
The sample that was exposed to two mixing zones in the extruder exhibited a higher plateau value of G prime in the linear viscoelastic regime compared to the sample exposed to only one mixing zone. SEM analysis revealed that using two mixing zones results in the formation of a larger number of smaller PTFE fibers.
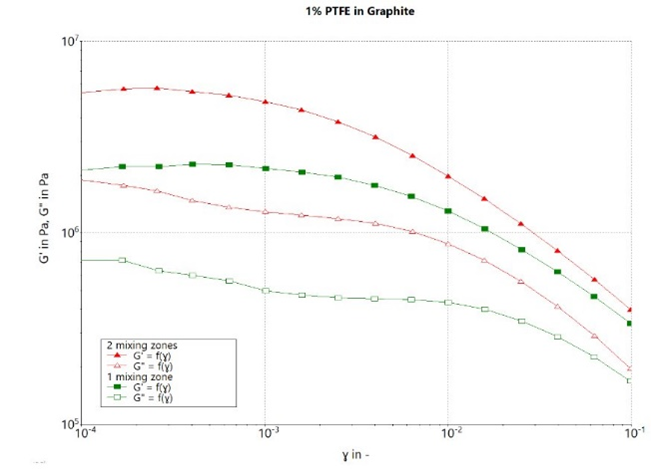
Investigation of PTFE fibrillation. Image credit: Thermo Fisher Scientific
This results in a stronger network between the graphite particles and higher G prime but a gradual breakdown with increasing deformation. In contrast, the fewer, thicker PTFE fibers in the sample mixed with one mixing zone presumably withstand greater deformation, as indicated by a smaller drop in G prime at higher critical deformation.
What rheometers do ThermoFisher Scientific offer, and how can customers decide what is right for their needs?
Thermo Fisher Scientific offers a range of different rotational rheometers for research and development, from compact quality control instruments to high-end rheometers. Those instruments differ in available measuring range with regard to torque and rotational speed, as well as in the available accessory portfolio.
Which of these instruments is right for your application depends on the type of sample you have and the kind of experiments you want to conduct. All of our rheometers can be equipped with a temperature control unit, generate absolute viscosity data, and perform shear rate sweep tests to produce complete flow and viscosity curves.
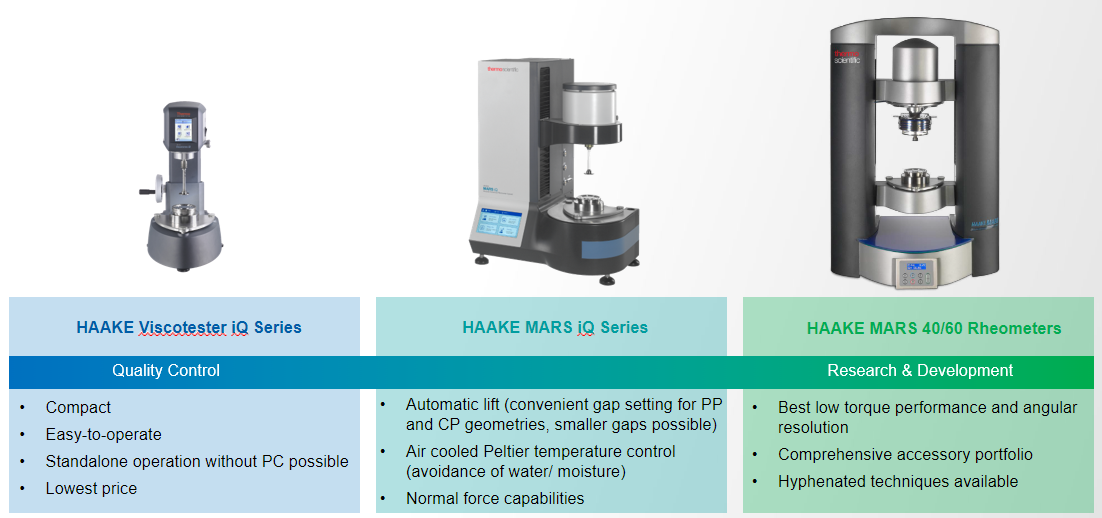
Flexible and robust rheometers for Quality Control up to Research and Development. Image credit: Thermo Fisher Scientific
Where can readers find out more?
For further information, check out our website, www.thermofisher.com/battery-rheology or watch the webinar
About the interviewee:
Annika Völp, Process Application Specialist, Thermo Fisher Scientific
Annika Völp, Dr.-Ing is an Application Specialist with Thermo Fisher Scientific focusing on the extrusion of polymers and twin-screw compounding of battery materials. Annika received her Dr. -Ing from the Institute for Mechanical Engineering and Mechanics, Karlsruhe Institute of Technology (KIT), Karlsruhe, Germany. During her Ph.D. studies, she investigated the structure and rheology of foams. Annika also has a degree in Bioengineering from KIT.
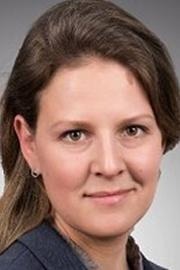
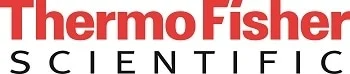
This information has been sourced, reviewed and adapted from materials provided by Thermo Fisher Scientific – Production Process & Analytics.
For more information on this source, please visit Thermo Fisher Scientific – Production Process & Analytics.
Disclaimer: The views expressed here are those of the interviewee and do not necessarily represent the views of AZoM.com Limited (T/A) AZoNetwork, the owner and operator of this website. This disclaimer forms part of the Terms and Conditions of use of this website.