Heavy plate testing in the steel industry is an essential yet complex process designed to ensure that these extremely large steel slabs meet the high-quality standards required by demanding applications.
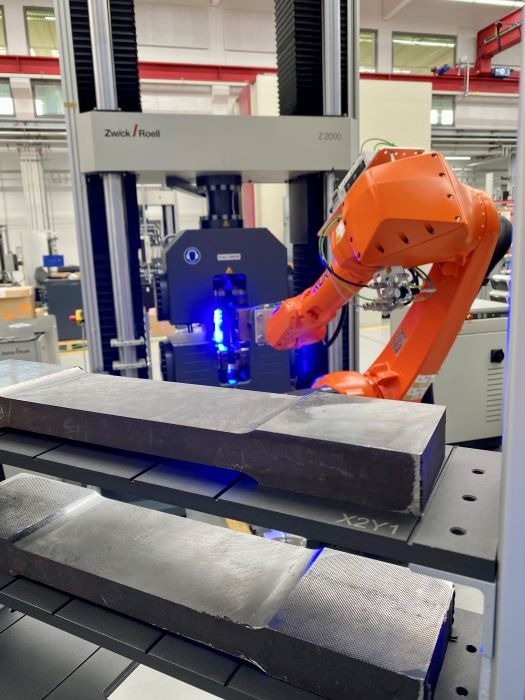
Image Credit: ZwickRoell GmbH Co. KG
This article summarizes a number of challenges, requirements, and solutions commonly associated with heavy plate testing, covering a range of essential topics such as automation and the importance of testing in high-tech industries.
An Introduction to Heavy Plates
Heavy plates are generally produced from steel slabs, heating, rolling, and cutting them as required to achieve the desired final size. The thickness of these plates can vary significantly—from 3 mm to 400 mm—and their production routinely involves forces of up to 120 Mega Newtons (mn).
Heavy plates are advanced, high-tech materials commonly used in critical applications such as shipbuilding, bridge construction, and offshore wind towers. Their production involves precise processes, including heat treatment, controlled cooling, and specialized cutting techniques.
While they may outwardly appear to be simple, heavy-duty metal sheets, heavy plates are central to the contemporary energy, construction, and transportation sectors, most notably in applications where high strength and corrosion resistance are critical.
Common applications of heavy plates include pressure vessels, wind towers, and defense utilities.
Challenges in Heavy Plate Testing
Testing heavy plates presents a number of distinct challenges, primarily due to the specimen’s size and weight. Heavy plates can weigh up to 40 kg, requiring specialized equipment and the implementation of specific ergonomic practices for the operators.
Testing procedures must also account for the diverse environmental and working conditions that heavy plates are routinely exposed to, including high-impact forces, extreme temperatures, and corrosive environments.
Heavy plate testing is often mistakenly thought to be limited to high-capacity tensile tests. In reality, a wide variety of tests are employed, including pendulum impact tests, hardness tests, and assessments of fatigue and fracture mechanics. Each of these tests plays a crucial role in evaluating the plate's performance under various real-world stress conditions.
Common Types of Testing
The tests most commonly performed on heavy plates include:
Static Tensile Testing
Static tensile testing is the most widely recognized test. This test is designed to evaluate tensile strength, yield strength, elongation at break, and other properties.
Tensile tests are conducted using round, flat, or welded specimens tailored to meet specific testing requirements. Common challenges in this method include ensuring proper ergonomic handling of large specimens and accommodating the high forces involved.
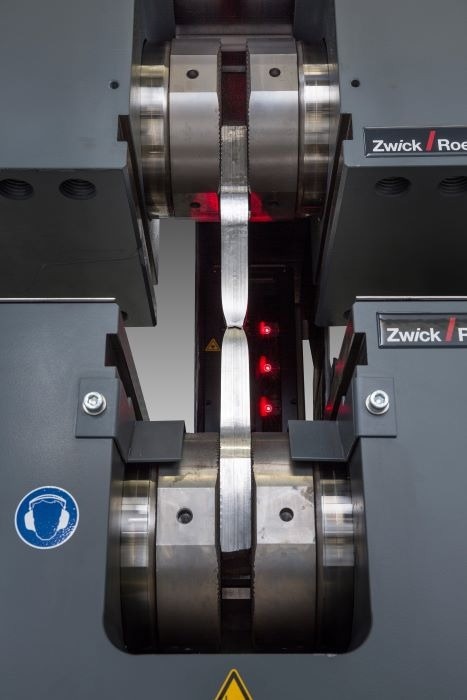
Tensile test up to 2,500 kN with optical strain measurement. Image Credit: ZwickRoell GmbH Co. KG
Pendulum Impact Testing
Pendulum impact testing determines a material’s fracture energy. This type of test is often used to assess material’s behavior in brittle or ductile conditions.
The specimen is struck with a hammer at high speed, with typical challenges including minimizing wear on testing equipment and ensuring the precise positioning of specimens.
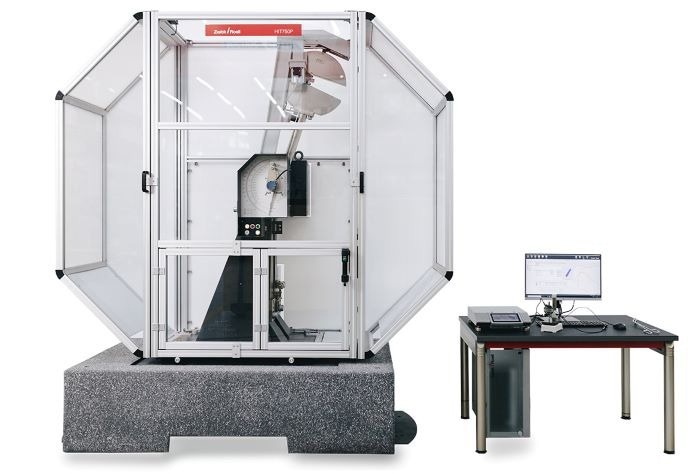
Charpy impact test up to 750 J. Image Credit: ZwickRoell GmbH Co. KG
Hardness Testing
Hardness testing typically leverages the Brinell or Rockwell methods to determine a material's wear resistance or strength. A key challenge associated with this method lies in ensuring consistent results while conducting these tests on rough, dirty surfaces typical of heavy plates.
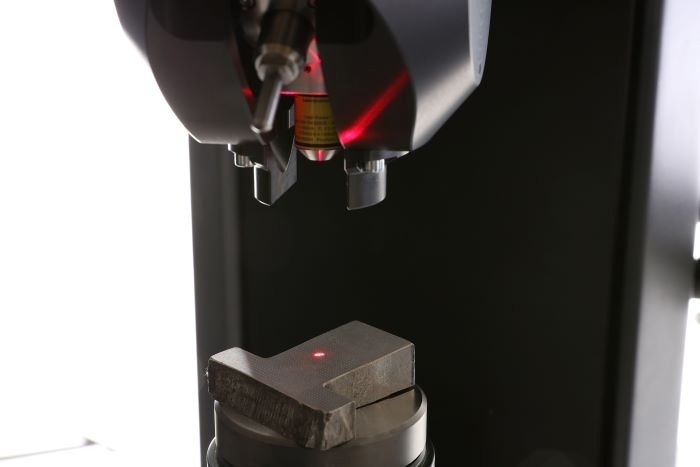
Hardness testing. Image Credit: ZwickRoell GmbH Co. KG
Fatigue and Fracture Mechanics
Fatigue and fracture mechanics testing is key to predicting a material's performance under cyclic loading. This is an especially important consideration in wind towers and other structural applications.
Fracture toughness and low-cycle or high-cycle fatigue tests can be used to determine the number of stress cycles that a material can endure before it fails.
Digitalization and Automation in Testing
Automation and digitalization are becoming increasingly commonplace in heavy plate testing applications.
Automation helps to increase throughput, minimize the risk of human error, and improve safety by limiting the need to manually handle heavy specimens, while digitalization supports remote operation, real-time monitoring, and advanced data analysis—factors that ultimately lead to increased precision and greater efficiency.
ZwickRoell offers two key automated testing systems for heavy plates:
- Robotest R: This industrial robotic arm can be integrated with testing machines, making it ideally suited to operations requiring high magazine capacity and flexibility.
ISO 6892-1 & ASTM E 8 | Roboter-Prüfsystem ‚roboTest R‘ für Zugversuche an Grobblech 1200 kN
Video Credit: ZwickRoell GmbH Co. KG
- Robotest P: This linear portal system enables easier manual operation during tests, making it especially useful when using multiple machines.
Tensile Testing on Heavy Plate with Robotic Testing System roboTest P
Video Credit: ZwickRoell GmbH Co. KG
Both systems offer distinct benefits, so when selecting a system, it is important to consider specific testing requirements such as operational flexibility and the magazine capacity for holding specimens.
The Importance of Heavy Plate Testing
Heavy plates are key components in a range of high-tech applications throughout the construction, aerospace, and energy sectors. Testing processes must ensure that these plates feature appropriate mechanical properties, including toughness, fracture resistance, and stability under extreme conditions.
Testing is especially important for applications involving exposure to corrosive environments, such as offshore wind towers, or low temperatures, such as shipbuilding in icy waters.
Despite its centrality to many key applications, the heavy plate sector receives comparatively less attention than, for example, the automotive sheet metal industry.
Nevertheless, heavy plates remain essential for infrastructure projects and a range of high-tech applications, highlighting the need for advanced, reliable testing methods and technologies.
Key Challenges and Solutions
There are a number of challenges associated with heavy plate testing:
Handling and Safety
The size and weight of heavy plate specimens pose specific challenges to their manual handling, including operator risk and testing accuracy. Automation helps mitigate these issues by improving precision and reducing the need for manual intervention.
Surface Quality
Heavy plates tend to feature rough surfaces, which can affect hardness tests’ accuracy. Advanced optical systems like ZwickRoell's video extensometers can help ensure accurate measurement without extensive surface preparation prior to analysis.
High Testing Forces
The mass and size of heavy plates mean that testing machines must be able to accommodate very high forces. ZwickRoell addresses this challenge by offering electromechanical machines with the required capacity and long-term cost efficiency.
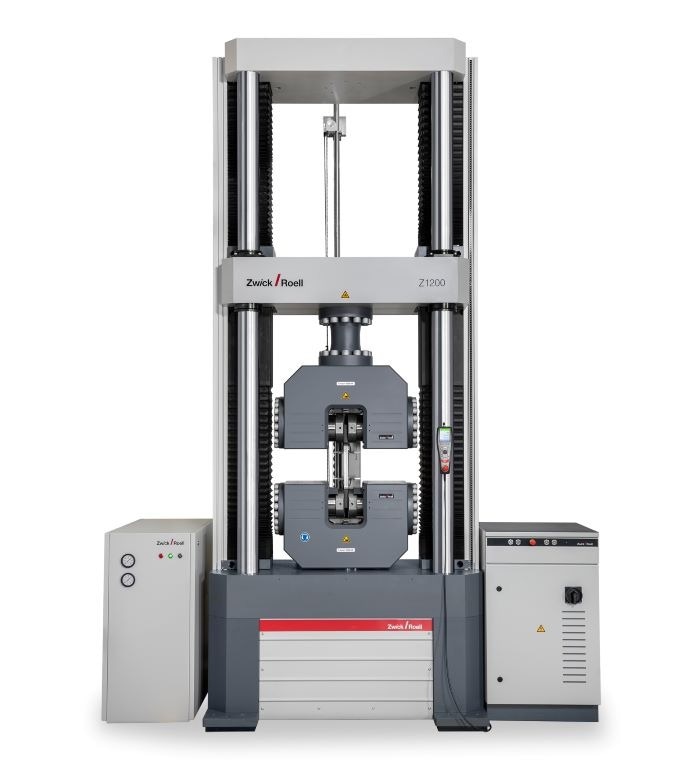
ZwickRoell provides electro-mechanical testing solutions up to 2,500 kN. Image Credit: ZwickRoell GmbH Co. KG
Summary and Outlook
Advances in automation and digitalization underpin the ongoing evolution of heavy plate testing, continuing to improve efficiency, accuracy, and safety. These developments are leading to more reliable and less labor-intensive heavy plate testing, most notably via the integration of advanced data management solutions and automated testing systems.
Heavy plates continue to represent a key component in high-tech applications across a diverse array of industries, with rigorous testing processes ensuring their performance under a range of challenging conditions.
It is anticipated that heavy plate testing will continue to integrate digital and automated solutions in the future, enabling remote collaboration, real-time monitoring, and more efficient production processes.
As stringent quality requirements become commonplace throughout the industry, advanced heavy plate testing will become increasingly important in ensuring that these vital materials continue to meet the high standards demanded by their essential and diverse applications.
Acknowledgments
Produced from materials originally authored by ZwickRoell GmbH & Co. KG.
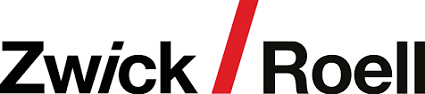
This information has been sourced, reviewed and adapted from materials provided by ZwickRoell GmbH Co. KG.
For more information on this source, please visit ZwickRoell GmbH Co. KG.