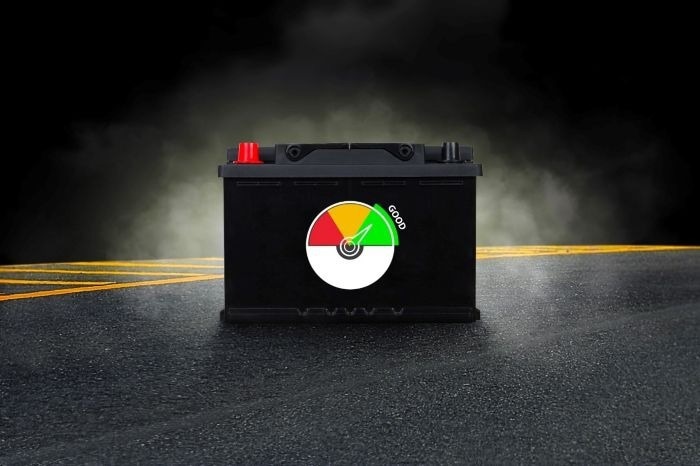
Image Credit: BLKstudio/Shutterstock.com
What is the role of cryogenic plasma FIB-SEM in battery research?
Dr. Yao Bin Xu: At Pacific Northwest National Laboratory (PNNL), we extensively use cryogenic plasma FIB-SEM (focused ion beam scanning electron microscopy) to investigate lithium and sulfur cathode materials. Xenon plasma FIB allows high-current milling for large-volume 3D reconstructions without gallium implantation. With integrated EDS and EBSD (energy dispersive spectroscopy and electron backscatter diffraction, respectively) under cryo conditions and inert gas protection, we can map microstructure, porosity, and chemical gradients at high spatial resolution—key parameters for optimizing electrode performance.
How do imaging techniques help address lithium metal battery challenges?
Dr. Yao Bin Xu: In-situ environmental TEM (transmission electron microscopy) has been key to uncovering how lithium behaves under different conditions. We observed that lithium grows in distinct forms depending on the surrounding gas—whiskers form in CO2 due to lithium carbonate films, while nitrogen leads to more particle-like structures. Current density also plays a critical role: at low current, lithium deposits uniformly; at higher currents, growth becomes nucleation-limited, resulting in fewer but thicker deposits.
These insights help us better understand how the solid-electrolyte interphase (SEI) and external fields influence lithium deposition and dendrite formation.
What new understanding have you gained about the SEI layer using advanced TEM?
Dr. Yaobin Xu: Our cryo-TEM and in-situ bias experiments have shown that SEI layers aren't just passive insulators—they often exhibit semiconducting behavior. At low current densities, we observed monolithic SEI layers, while higher currents produced mosaic-like structures with embedded nanocrystals. EELS analysis revealed that salt-derived SEIs, which are rich in LiF and Li2O, have lower electrical conductivity than those formed from solvents. These differences in electrical properties are closely tied to lithium morphology and overall battery performance.
What strategies are used to study silicon anodes and their degradation mechanisms?
Dr. Yao Bin Xu: We’ve applied in-situ heating and bias TEM to study porous silicon anodes coated with pitch-derived carbon. This carbon coating enhances conductivity and helps accommodate the material’s volume expansion during cycling. Cryo-TEM imaging revealed that the SEI grows inward over time, but the carbon layer limits electrolyte penetration, leading to improved cycling stability. These results highlight the potential of carbon-coated silicon composites as a more durable architecture for high-capacity anodes.
Why is inert gas sample transfer (IGST) preferred over vacuum transfer for sensitive materials?
Brandon Van Leer: Vacuum transfer can still allow trace amounts of air or moisture to leak in over time, which poses a problem for highly reactive materials. IGST offers a better solution by maintaining a positive argon pressure, effectively creating a barrier against contamination.
In side-by-side studies, lithium metal transferred using IGST showed less than 3% oxidation after 15 minutes, compared to over 35% degradation in samples exposed to air. This approach is critical for preserving the integrity of sensitive surfaces during analysis.
Can EDS detect lithium? What are the limitations?
Brandon Van Leer: Detecting lithium with EDS is difficult due to the element’s low atomic number and weak X-ray emission. You need a windowless detector and high beam current, which risks damaging delicate samples. It works for bulk lithium, but nanoscale SEI detection is unreliable.
Dr. Yao Bin Xu: In TEM, we prefer EELS or 4D-STEM to map lithium distribution. These techniques offer higher spatial resolution and can extract chemical bonding information critical for understanding SEI formation.
How are these imaging insights transforming battery development and manufacturing?
Dr. Yao Bin Xu:Imaging allows us to study materials at atomic resolution, capturing morphological and chemical evolution during cycling. This helps guide electrolyte design, improve electrode formulations, and mitigate dendrite risks.
Brandon Van Leer: From a manufacturing standpoint, integrating high-resolution analytics into R&D shortens development cycles, reduces product failures, and helps new companies scale faster by embedding quality assurance early in the process.
Watch the Accompanying Webinar: Cutting-Edge Imaging Characterization Techniques for Beam-Sensitive Battery Materials
About the Speakers
Dr. Yao Bin Xu, Senior Materials Scientist at Pacific Northwest National Laboratory (PNNL)
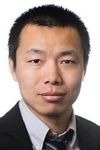
Dr. Yao Bin Xu specializes in understanding how microstructure impacts performance in energy materials. His research focuses on lithium metal batteries, high-energy cathodes, and solid-state systems. He earned his Ph.D. from the Chinese Academy of Sciences and completed postdoctoral work at Northwestern University. Currently, he leads advanced microscopy efforts—using cryo-TEM, in-situ holders, and FIB-SEM—to diagnose and improve battery performance at the nanoscale.
Brandon Van Leer, Director for Clean Energy, Thermo Fisher Scientific
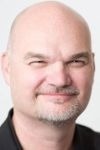
With more than 27 years of experience in analytical techniques, Brandon Van Leer develops instrumentation workflows for batteries and clean energy materials. He has a background in physics and electrical engineering and has held a variety of roles at Thermo Fisher since 2004. His recent work centers on inert gas workflows and cryogenic solutions designed to preserve and analyze highly reactive battery materials.
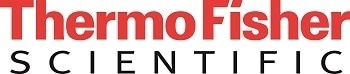
This information has been sourced, reviewed and adapted from materials provided by Thermo Fisher Scientific.
For more information on this source, please visit thermofisher.com/battery-solutions.
Disclaimer: The views expressed here are those of the interviewee and do not necessarily represent the views of AZoM.com Limited (T/A) AZoNetwork, the owner and operator of this website. This disclaimer forms part of the Terms and Conditions of use of this website.