Rheology is the science of studying the flow and deformation of materials rooted in the laws of elasticity and viscosity proposed by Hooke and Newton in the late 17th Century. Thermoplastic polymer melts are widely used in many modern industrial processes to manufacture a multitude of objects.
Polymers are used because they are relatively cheap to form into complex shapes in the molten state and therefore, we need to understand how they flow when being processed.
Characterizing the Rheological Properties of Polymers
Polymers are complicated materials to characterize rheologically because there are many factors that influence their flow properties. Examples of factors that influence the flow behavior may include: Processing temperature; Rate of flow; Residence time etc.
Furthermore the rheological properties of polymers are in between those of a liquid and a solid. This leads to time dependence of the flow properties and other important characteristics, some of which are discussed below.
Melt Viscosity and Temperature
Melt viscosity is well known to be critically dependent on temperature. By lowering the temperature of a mold until the part being produced has a matt finish, the processor can learn the minimum temperature (hence maximum resin viscosity) at which the process can be run without surface defects becoming apparent. Reducing the mold temperature saves energy and can reduce cycle times and so an understanding of the temperature dependence of melt viscosity is very useful.
Die Swell
Polymer melts are known to exhibit die swell when extruded. This phenomenon reveals itself as an increase of diameter of an extrudate after exiting a die. The amount of die swell is related to the amount of elastic deformation of the material at the inlet of the die. A further fact to be considered is that the degree of die swell (more correctly extrudate swell) is dependent on the length of the die when material is extruded at constant throughput.
In other words polymer melts exhibit time dependency as the material forgets the elastic deformation applied at the entrance of the die, the more time the material spends within the die the less die swell.
The Effect of Melt Elasticity
Melt elasticity can also have profound implications for many other polymer processes such as:
- Blow Molding where the wall thickness of the blown component depends on the degree of swell that has taken place during the extrusion process prior to the mold being closed.
- Vacuum Forming or Thermoforming where the polymer must maintain a degree of elasticity to prevent the material sagging before it is pulled by vacuum over the cold forming die. If the material does not have sufficient elasticity it is likely to come into contact with the chilled die before the vacuum or pressure is applied. Polymer processing properties also depend on the concentration of lubricants, plasticizers, fillers and other components in the compound being processed. From this brief introduction one can appreciate that proper characterization of polymer melt flow behavior is likely to require sophisticated and versatile instrumentation.
Components of Thermoplastic Rheology
From the point of view of the Rheologist polymer flow behavior can be conveniently separated into three components: Shear and extensional flows which are characterized by the corresponding viscosities and Elastic behavior which is characterized by measurement of modulus or swell ratios.
Instruments for Characterizing Thermoplastic Rheology
To fully characterize a material, instrumentation is required which has the capability of extracting these parameters over a range of temperatures and shear/extension rates. Modern laboratory rheological test apparatus can be divided into two broad categories of rotational rheometers and capillary extrusion rheometers.
Rotational Rheometers
These instruments normally require a small specimen of the material to be tested in the form of disk – typical dimensions being 25 mm diameter and 1 mm thick. The sample is placed between a pair of parallel plates or upper cone and lower plate whose temperature can be maintained by an external heating device such as a blown gas oven or electrical heating of the plates.
Modern rotational rheometers are capable of a number of test types to allow full characterization of a material over a range of temperatures and flow rates. Examples of the types of the types of tests available are:
- Flow curves
- Creep tests
- Stress relaxation tests
- Small amplitude sinusoidal oscillatory testing
Flow Curves
Flow curves to measure the shear viscosity versus shear rate or shear stress. At sufficiently low shear rates a constant value for the viscosity will be attained.
This so called zero shear viscosity has been shown to depend on the average molecular weight of the polymer and the length of the plateau (how high a rate before the viscosity decreases) is known to reflect the width of the molecular weight distribution. Software packages are available to determine the average molecular weight and molecular weight distribution from such data.
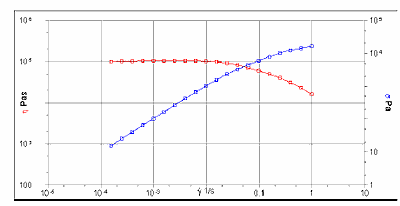
Figure 1. Flow curve for LDPE at 190°C showing low shear rate plateau for viscosity. The magnitude of the zero shear viscosity is determined by the average molecular weight of the polymer.
Creep Tests
Creep tests (application of constant stress for a defined period of time) allow an alternative means of determining the zero shear viscosity. When combined with recovery testing (removal of the stress) these tests enable the amount of elasticity in the sample to be measured because a material will with elasticity will recoil and attempt to recover its original shape.
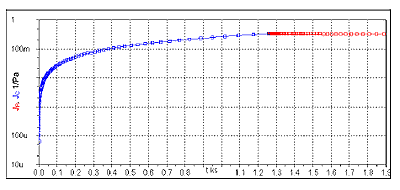
Figure 2. Creep (Blue) & Recovery (Red) Curve Polypropylene at 190ºC allow zero shear viscosity to be determined and equilibrium recoverable compliance.
Stress Relaxation Tests
Stress Relaxation tests apply an instantaneous deformation (strain) to the sample and record the time dependent decay of stress with time. The rate of decay of the stress depends on the viscoelasticity of the polymer at the test temperature. The data is often displayed as relaxation modulus versus time. Integration of the modulus versus time function is an often forgotten but rapid means of determining the zero shear viscosity and hence average molecular weight. Differentiation of the modulus/time function produces the continuous relaxation time distribution curve. This rather complex function in principle contains information relating to the molecular weight distribution of the polymer.
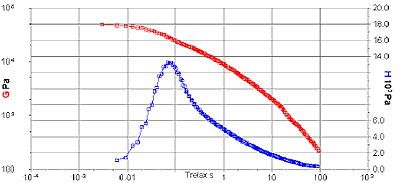
Figure 3. Stress relaxation data LDPE at 190°C. The relaxation time distribution curve includes information aboput the molecular weight distribution of the polymer.
Small Amplitude Sinusoidal Oscillatory Testing
Small amplitude sinusoidal Oscillatory Testing as function of test frequency is a rapid and often used method to measure the viscous and elastic properties of a polymer simultaneously. Two parameters are most often reported – Storage (Elastic) modulus and Viscous (Loss) modulus (G’’) which represent the relative degrees of the material to recover (elastic response) or flow (viscous response) respectively as the rate of deformation (test frequency) changes.
A typical response for a polymer melt is to exhibit elastic dominated behavior at high frequencies and viscous dominated behavior at low frequencies. This means that there is a critical frequency at which the two responses are equal. This is obviously a well-defined point and conveniently this “cross-over” frequency and modulus has been shown to depend on the molecular weight and molecular weight distribution of some linear polymers.
A potential advantage of utilizing this point as a quality control tool is that the cross-over of elastic and viscous moduli occurs at significantly higher frequencies than the point at which a constant value of shear viscosity occurs. Testing times may therefore be considerably reduced when compared to making flow curve measurements or performing creep tests.
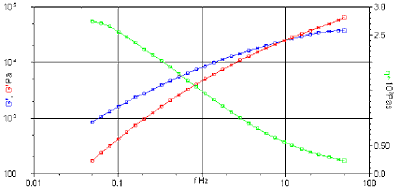
Figure 4. Frequency Sweep for Polypropylene at 190ºC. The Cross-Over Point is determined by the average molecular weight and molecular weight distribution.
A full discussion of the relationship between molecular parameters and processing performance is beyond the scope of this short article, but the following examples are included to illustrate how viscoelastic characterization of polymers has solved real processing problems:
- Variability of tube and pipe gauges in extrusion processes
- Reducing inconsistent fiber spinning properties
Variability of Tube and Pipe Gauges in Extrusion Processes
Oscillatory testing at low frequencies (below 0.1 Hz) revealed differences in the elastic modulus between different batches of material. Clearly pipe gauge will depend on the degree of recovery of the polymer after being extruded and so not surprisingly, the pipes and tubes with the higher gauge have greater elastic modulus.
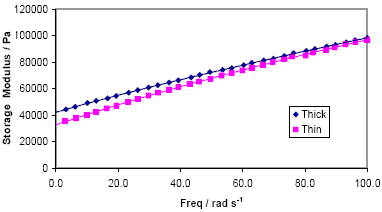
Figure 5. Frequency Sweep data for two HDPE pipes. The sample with higher elastic modulus produced the larger gauge pipe.
Reducing Inconsistent Fiber Spinning Properties
Low frequency oscillatory testing was able to show differences in the elastic properties of different batches of material. No differences were observed in the viscosity, indicating the material was of consistent molecular weight.
The differences in elasticity at low frequency are related to differences in the molecular weight distribution (MWD) with the result that the broader MWD results in increased molecular chain entanglement which hinders the draw down process of the fiber spinning process. This in turn causes inconsistency in the final product.
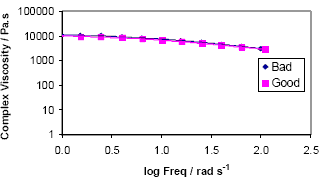
Figure 6. Complex Viscosity as a function of frequency for good and bad PP Fiber samples. Note that no discernable difference is evident.
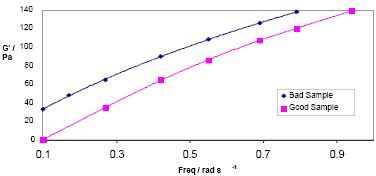
Figure 7. Storage Modulus as a function of frequency for good and bad PP Fiber samples. The bad sample had more elasticity causing inconsistent fiber diameter.
Capillary Extrusion Rheometers
Advanced capillary extrusion rheometers comprise a temperature controlled barrel incorporating one or more precision bores fitted with capillary dies at the exit. Melt pressure transducers are mounted immediately above the dies to record the pressure drop as polymer melt is extruded through the dies at programmed flow rates.
By the use of a capillary die and an “orifice”or “zero length” die the shear and extensional viscosities of a polymer melt may be determined simultaneously against shear and extension rates.
Additional accessories are available to record die swell by means if a laser scanning gauge and or extrudate melt strength by passing the strand of polymer through a series of speed controlled nip rollers and recording the force (melt tension) as a function of haul off speed.
Differences between Capillary and Rotational Rheometers
As a general rule, capillary rheometers are used to measure melt properties at higher shear rates than rotational rheometers and allow determination of flow behavior under typical processing conditions.
A particularly important consideration is the ability to measure extensional (elongational) properties at higher extension rates than by other techniques (such as counter rotating pulley devices) and more importantly at extension rates encountered on a processing line.
Shear and Extensional Data
Figures 8 & 9 show both shear and extensional data, which illustrates an important and often neglected point: Two polymers may have almost identical shear flow behavior, but may exhibit considerably different extensional properties.
As noted previously, many polymer processes (fiber spinning, blow molding) are essentially extensional processes and so determination of extensional viscosity is more important than measuring shear viscosity.
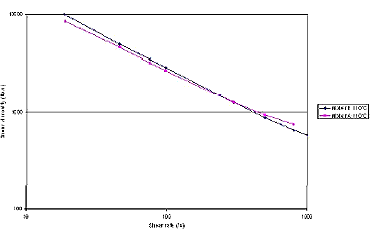
Figure 8. Shear viscosity versus shear rate. The data for the two rubbers is indistinguishable.
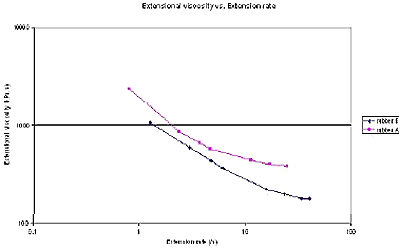
Figure 9. Extensional viscosity versus extension rate for the same materials shown in figure 8. There are clear differences in the extensional.
Flow Instability and Melt Fracture
Flow instability or melt fracture is generally the result of tensile stress when the melt flows from a large cross-section to a smaller one. If the tensile stress becomes large enough, the melt fractures.
The effect of melt fracture becomes less noticeable as the length of die is increased and as the die temperature is increased. Increasing die length damps out the effect of the cross-section change at the entrance of the die and increasing temperature reduces the viscosity and also the stress at the same shear rate.
In a capillary rheometer a region of melt fracture is revealed as a regular oscillation of the melt pressure signal as shown below. The melt effectively fractures and then reforms with the effect that adjacent elements have experienced different extensional histories and so will swell differently upon exiting the die.
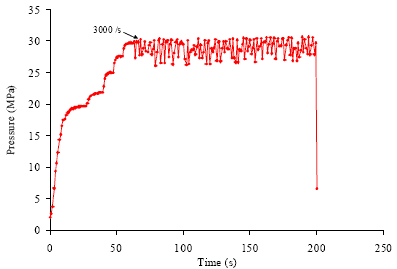
Figure 10. Evidence of Melt Fracture is shown by the oscillating pressure signal. The material is polypropylene measured at 190ºC.
Behavior of Thermoplastics at the Wall of the Capillary Die
A fundamental assumption when calculating rheological properties with a capillary rheometer is that the material at the wall of the capillary die is stationary – this is the so-called stick condition. In practice polymer melts deviate from this situation at a critical stress and the material flows as combination of shear flow superimposed onto a plug flow.
Wall slip and determination of the critical stress can be analyzed in a capillary rheometer by measurement of flow curves at the same temperature for at least three sets of capillary dies with the same length to diameter ratio. For a material not experiencing wall slip identical shear stress versus shear rate profiles will be generated.
In the case of wall slip occurring, shear stress will decrease as the die diameter increases at constant shear rate. Analysis of the flow data allows the “slip velocity” and critical stress to be determined. These parameters are often required by computational fluid dynamics software packages along with shear and extensional viscosity data to predict the flow of melts in molds and extrusion profiles.
The two examples above show how a capillary extrusion rheometer may be used to help predict the processing performance of a polymer melt. Other test regimes are also possible: Determination of polymer degradation by multiple flow curve measurements or viscosity versus time; Measurement of critical temperature for flow to commence at constant extrusion pressure; Stress relaxation after flow cessation; Melt compressibility at constant temperature etc.
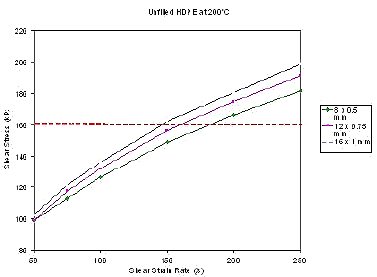
Figure 11. Rheograms for HDPE at 200ºC. The line of constant stress reveals evidence of Wall slip.
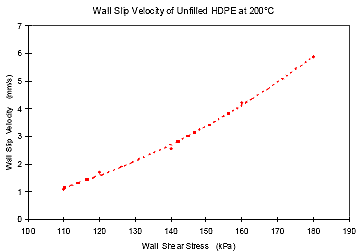
Figure 12. Slip velocity versus shear rate for HDPE at 200ºC. Slip velocity is calculated by Mooney’s method.
Conclusion
Polymer melt rheology is a complex subject that requires careful experiment design in order to obtain the information needed to meet an investigator’s requirements. rotational rheometers are the preferred choice when the requirement is to obtain information concerning the molecular structure and how this affects processing characteristics.
In particular, the ability to easily extract information about the average molecular weight and molecular weight distribution via measurement of the viscoelastic properties makes the rotational rheometers a powerful tool. The capillary rheometer extends the shear rate range attainable in the laboratory beyond that available in a rotational instrument and allows the flow properties to be measured under typical processing conditions.
In addition, the ability to readily determine both the shear and extensional properties under real life conditions provide the polymer producer and processor with information that is vital to the successful use of a polymer melt. Finally, the capillary rheometer enables processing problems to be investigated in a controlled environment without the need to stop production on the factory floor.
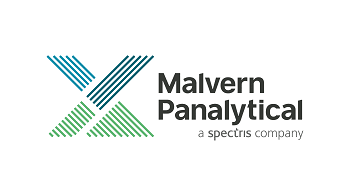
This information has been sourced, reviewed and adapted from materials provided by Malvern Panalytical.
For more information on this source, please visit Malvern Panalytical.