Fastener manufacturers improve production rates and fastener quality by using heat in their heading, threading and patching manufacturing processes. Induction heating helps faster and more-efficient heating of fasteners with maximum repeatability.
The features and advantages of induction heating are as follows:
- A clean, non-contact heating method
- A rapid heating process for enhanced productivity and higher volumes
- Delivers precise and uniform heating of all, or part, of the fastener
- Instant on, instant off heating with safety and reliability
- Easy to integrate with remote workheads
- Cost effective, saves more energy than other heating techniques.
Ambrell provides heating systems for a myriad of induction heating applications. The company’s systems are already used by fastener manufacturers for small (0.5 mm OD) and large (76 mm OD) applications. A customer can test its applications at Ambrell’s Applications Lab for free to get the right solution depending on the requirement.
Heading
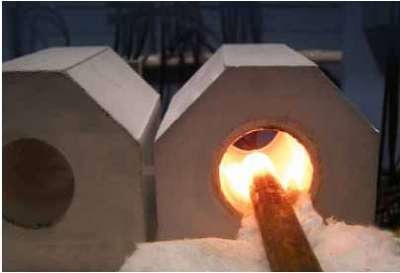
Induction heating - preheating bolts and screw heads prior to forging.
Induction heating is widely utilized to preheat bolt and screw heads before forging. The advantages of induction heating for the hot or warm heading process are as follows:
- Improved productivity: The need for post-production tempering and heat treating is reduced
- Quality: The spring back effect is eliminated for higher quality parts
- Consistency: direct precise heat application even for the part
- Economical: lessens pressure on the die, thus extending die life
- Safe: Low pressure and minimal residual stress on components.
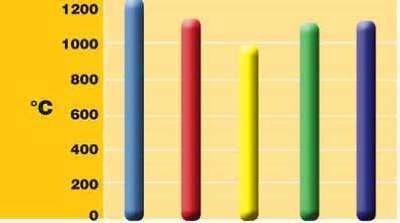
Required temperature for hot heading fasteners of different materials.
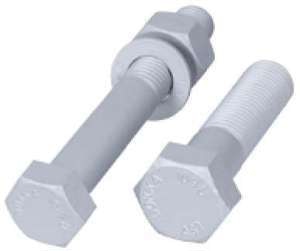
The normal part heating temperature for hot heading applications is 1,100° C. Small parts of 6 mm diameter require a few seconds for heating when compared larger parts of 76 mm as more time is required for the heat to reach the center. The typical cycle time of heating fasteners up to 20mm in diameter in line with a heading press is up to 10 seconds. Large diameter fasteners are heated using a multi-position coil, which creates one part in every 15–20 seconds for the heading press. Ambrell systems heat to the center of a fastener head rapidly and more efficiently.
Thread Rolling
Thread rolling uses a thread roll die to create a thread into a heated fastener. Unlike thread cutting, thread rolling creates the shape by pushing the material against a thread roll die. This not only reduces material waste but also lessens stress to the fastener.
The quality of the products produced by thread rolling is much higher than that of cutting. It is easier to integrate induction heating into the thread rolling production process. Induction heating is a rapid and uniform heating method that provides superior repeatability and better production efficiency in mass production of parts.
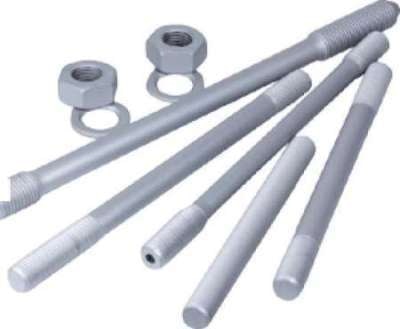
Ambrell systems can cost-effectively meet the demands of virtually any thread rolling application.
Application of induction heating in thread rolling provides following benefits:
- Precise homogenous heating of the fastener’s threaded part alone with reduced material stress
- Instant on/instant off feature eliminates oven ramp up time or surrounding space heating, thus increasing efficiency
- Decreased cycle times leads to higher productivity
- Manufactures stronger, more durable threads
- Economical as it increases tool life by reducing tool wear.
Practical power and induction frequency requirements for thread rolling applications on steel or Waspaloy fasteners are shown in table 1 below.
Table 1. Practical power and induction frequency requirements.
STEEL Waspaloy |
3mm |
1mm |
25mm |
Power (kW) |
10 |
30–60 |
50–100 |
Throughput |
18,000/hour |
40,000/hour |
9,000/hour |
Minimum Frequency (kHz) |
>10 |
>1.5 |
>1.5 |
Thread Patching
Induction heating is a suitable process for curing the powder material or paint used in thread patching. Thread patching productivity can be significantly improved by Ambrell systems as they rapidly heat fasteners up to 300° C for flowing the powder coating or paint.
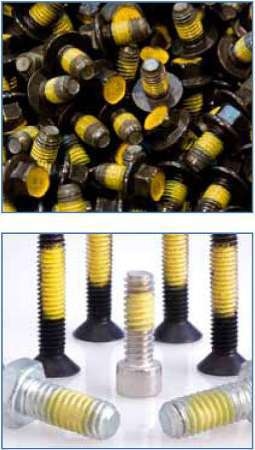
Many fastener manufacturers already use Ambrell induction heating systems for their patching lines and process fasteners as small as 0.5 mm OD up to 25 mm OD, with process rates as high as 81,000 parts per hour for 10mm OD.
Application of induction heating in thread patching offers the following benefits:
- Precision heating: localized heat aimed at only to the part that requires heating
- Quality parts: Individual monitoring is possible for quality
- Quality curing: offers a superior re-flow of powder coatings to fastener threads
- Controllable: adjust to precise fastener temperatures with homogenous heating
- Fast heating results in higher yields and improved production rates
- Economical: no lengthy warm up or cool down cycles
Typical induction heating systems for patching lines comprise a short channel coil having a length of 460 mm for preheating the fastener before patching and a longer channel coil of 4300 mm for flowing the powder subsequent to spraying. Unlike IR or oven heating methods, induction heating allows for any outgassing of the patching material as it heats from the inside out.
Practical power and induction frequency perquisites for patching applications for steel fasteners are shown in table 2.
Table 2. Practical power and induction frequency perquisites for patching applications.
STEEL |
3mm |
10mm |
25mm |
Power (kW) |
10 |
30-60 |
50-100 |
Throughput |
36,000/hour |
81,000/hour |
18,000/hour |
Minimum Frequency (kHz) |
>10 |
>1.5 |
>1.5 |
Summary
Ambrell offer its EASYHEAT systems with power ranging between 1.2 and 10 kW and frequencies ranging between 150 and 400 kHz.
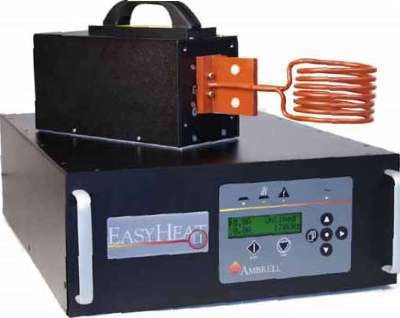
EASYHEAT by Ambrell.
Ambrell’s EKOHEAT offer power ranging between 10 and 800 kW and frequencies ranging between 1 and 150 kHz.
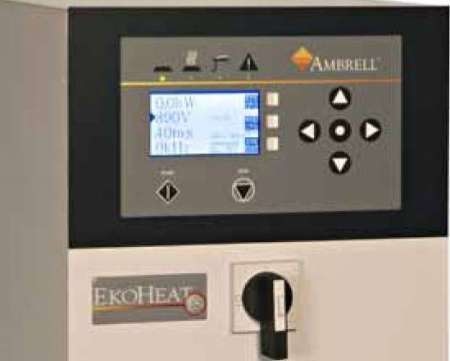
EKOHEAT by Ambrell.
The EKOHEAT systems are ideal for hot heading and thread rolling applications. They are also suitable for through heating thanks to their robustness and lower frequencies.
The material and part size decides the best Ambrell system to be selected for thread patching. An EASYHEAT system is ideal for small stainless steel fastener of 3 mm, while an EKOHEAT system is suitable for a large steel fastener of 25 mm.
Features of Ambrell induction heating systems include:
- Ambrell workhead technology that enables the processing of different parts without a system change-over
- Wider frequency ranges enable heating more fasteners with various specifications using the same power supply
- Multiple capacitor and tap transformer configurations
- Flexible frequency tuning for accurate, repeatable fastener heating
- Can be integrated easily into production processes with a portable workhead, up to 30 m in certain systems
- Expert coil designs that increase power delivery and reduce production time
- Efficient power conversion reduces energy expenses
- CE marked and produced in an ISO 9001:2008 certified facility
- User-friendly operator interface in five languages (EN, ES, FR, DE, IT).
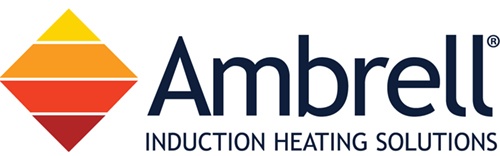
This information has been sourced, reviewed and adapted from materials provided by Ambrell Induction Heating Solutions.
For more information on this source, please visit Ambrell Induction Heating Solutions.