The reflection-configured Digital Holographic Microscope (DHM®) is a non-scanning, non-contact technique for characterizing vibration, static, and dynamic 3D topography.

DHM-R measuring through a glass window. Image Credit: Park Systems
Unrivaled Speed
3D Profilometry at Unrivaled Speed
DHM® uses a single acquisition to measure a surface's 3D topographical map; no scanning mechanism is needed. With a camera rate of up to 100,000 frames per second, it offers incredibly quick acquisition, allowing:
- Analysis of the dynamic behavior of deformable samples in three dimensions
- High-productivity routine inspections
- Quick screen and large surface analysis
- 3D topography capture on the production line without halting the sample
MEMS Analysis, up to 25 Mhz
The DHM® measurements are synchronized with a MEMS device’s excitation signal by the optional stroboscopic unit. This particular collection of data’s analysis yields:
- Time-sequence of 3D topographies
- Frequency resonances and responses
- The vibration amplitude has a resolution of 5 pm for out-of-plane and 1 nm for in-plane displacement
- Characterization of complex motions and sample geometries, including those with holes
Innovation
Measure in Controlled Environmental Conditions
DHM®’s optical design ensures high-quality measurements.
- Through glass and immersion liquids
- Within vacuum and environmental chambers with regulated pressure, temperature, humidity, and gas composition
Measure Topography of Transparent Patterns
The following can be measured with the optional DHM® Reflectometry analysis software:
- Topography of transparent structures
- Structured multi-layers with thicknesses ranging from 10 nanometers to tens of microns were analyzed for their refractive index values
- Topography of soft materials and liquids

Time sequence of 3D topographies, limited by camera rate : evaporation of a liquid drop. Image Credit: Park Systems
DHM®
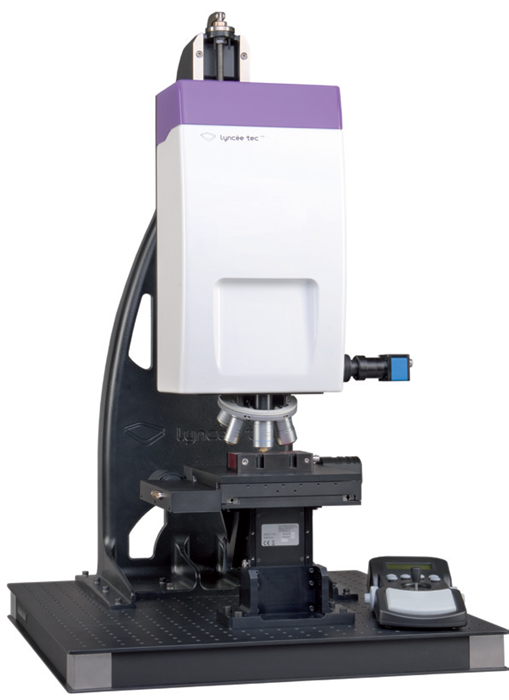
Reflection DHM. Image Credit: Park Systems
Digital Holographic Microscopy (DHM®) is a patented technology. The microscope's digital camera captures holograms caused by interference between the sample's reflected beam and an internal reference beam. The holograms are mathematically processed to produce a three-dimensional optical map of the specimen.
Advanced numerical processing of the recorded hologram makes it possible to conduct crisp focus concurrently or as a post-processing step after measurement, without manually changing the sample’s height.
Based on the number of wavelengths, Reflection DHM® comes in three different versions:
- The R1000 models, utilizing a single wavelength, are optimally suited for measuring smooth surfaces and vibrations.
- To measure complicated or discontinuous structures, R2100 models are set up to measure at two wavelengths concurrently.
- A third source is added to R2100 models to increase measurement capabilities, especially for transparent patterns.
Technical specifications
Source: Park Systems
System |
DHM models |
R1000 |
R2100 |
R2200 |
Number of laser sources |
1 |
2 |
3 |
Operating wavelength (± 1.0 nm) |
675 nm |
675 nm, 794 nm |
666 nm, 794 nm, 675 nm |
Laser wavelength stability |
0.01 nm / °C at 675 nm |
Sample stage |
Manual or motorized XYZ stages up to 300 mm x 300 mm x 38 mm travel range |
Objectives |
Magnification 1.25x to 100x, standard, high NA, long working distance, water/oil immersion |
Objective turret |
6 positions |
Computer |
Workstation with the latest multicore Intel® processor, high-performance graphics card optimized and configured for DHM, with a screen of at least 21 inches and a mouse |
Software |
Proprietary Koala software based on C++ and .NET
Additional optional software modules are available for advanced analysis |
Data compatibility |
Measurement data recorded in bin format, exportable in .txt format, recorded and reconstructed images exportable in .tif format or .txt array |
Performance |
Measurement mode |
Single wavelength at 675 nm |
Short synthetic wavelength at 4.4 μm |
Long synthetic wavelength at 50 μm |
DHM models |
R1000, R2100, R2200 |
R2100, R2200 |
R2200 |
Accuracy 1 [nm] |
0.15 |
0.15 / 3.0* |
20 |
Vertical resolution 2 [nm] |
0.30 |
0.30 / 6.0* |
40 |
Repeatability 3 [nm] |
0.01 |
0.01 / 0.1* |
0.5 |
Vertical measuring range |
up to 200 μm |
up to 200 μm |
up to 200 μm |
Max. height of steps with sharp edges |
up to 333 nm4 |
up to 2.1 μm4 |
up to 24 μm4 |
Surface type |
Smooth surfaces |
Complex or discontinuous structures |
Complex or discontinuous structures |
Vertical calibration |
Determined by an interferometric optical filter, ±0.1 nm |
Acquisition time |
Standard: 500 μs (optional 10 μs) |
Acquisition rate |
Standard: 190 fps (1024 x 1024 pixels). (optional up to 100,000 fps). |
Reconstruction rate |
Up to 25 fps 1024 x 1024 pixels hologram (data analysis dependent) (optional up to 60 fps) |
Lateral resolution |
Objective dependent, down to 300 nm** |
Field of view |
Objective dependent, from 66 μm x 66 μm up to 5 mm x 5 mm** |
Working distance |
Objective dependent, from 0.3 to 18 mm** |
Digital focusing range |
Up to 50x depth of field (objective dependent) |
Min. sample reflectivity |
Less than 1% |
Sample illumination |
Down to 1 μW/cm2 |
Stroboscopic unit |
Compatibility with single and short synthetic wavelengths |
Power requirements |
Input voltage |
85-260 VAC – 50/60 Hz |
Power requirements |
max. 250 W |
Dimensions & weight |
Dimensions (L x W x H) |
600 x 600 x 800 mm |
Weight |
48 kg |
1 As demonstrated by taking the temporal standard deviation on 1 pixel over 30 measurements
2 Defined as twice the accuracy
3 As demonstrated by taking the one sigma Rq value of 30 repeatability measurements without sample
4 Depends on the laser source(s) and operating wavelength(s)
* With / Without single wavelength mapping
** Objectives specifications on www.lynceetec.com/microscope-objectives
Numerous solutions are compatible with DHM® systems.
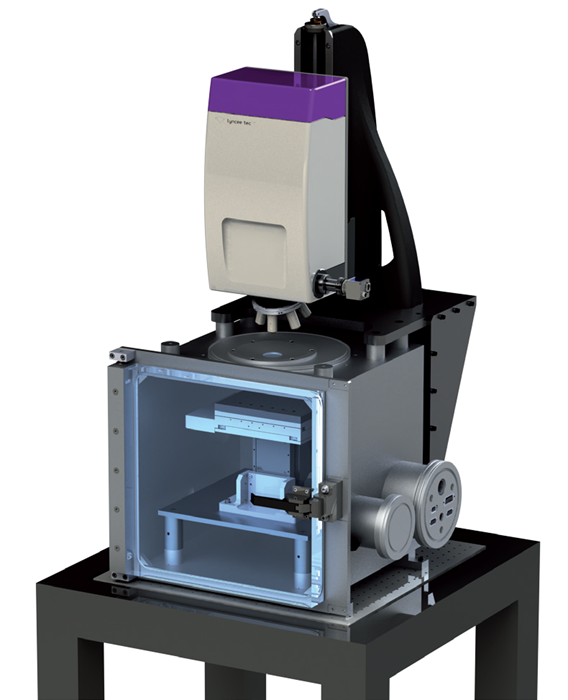
Reflection DHM® mounted on a vacuum chamber. Image Credit: Park Systems
- Goals for immersion, cover-glass correction, extra-LWD, etc.
- DHM automation and remote control via a remote TCP/IP module
- Stroboscopic unit for the investigation of MEMS
- Motorized stage for automation and stitching
- Remote TCP/IP module for automating and remotely controlling DHM