Drug companies optimize their production operations across the world to stay competitive in the pharmaceutical industry. However, production delocalization forces them to thoroughly analyze the incoming raw materials for quality control, product safety and regulatory purposes, which can eventually increase the cost. Additionally, the industry is shifting from a representative sampling method towards total traceability of the incoming materials, thus affecting factory efficiency and operational costs. Hence, stringent control over the quality and safety of all materials used in the production of pharmaceuticals is essential.
This article covers the affordability and advantages of using handheld Raman for this purpose.
Handheld Instruments
The advent of portable and handheld instruments has enabled new analytical capabilities for production traceability, quality control and quality assurance in the pharmaceutical industry. Nowadays, warehouses can be equipped with a variety of analytical techniques such as X-ray fluorescence (XRF), Mid-IR, NIR, and UV-Visible capabilities.
These portable devices can deliver data quality comparable to conventional laboratory-grade bench devices in certain cases.
One of the most widely adopted portable devices for this type of quality control is Raman spectroscopy, which enables rapid determination of unknown compounds, such as the measurement of pharmaceutical ingredients, the validation of high purity chemicals, and the authentication of drug compounds.
Raman technology is ideal for the direct analysis of an unknown material in a warehouse environment as it requires little to no sample preparation. Moreover, it can handle different forms of samples, including slurries, gels, solutions, crystals, powder, and can perform analysis directly through a plastic bag or clear container.
A major drawback of the Raman technology is the associated auto-fluorescence signal, which can affect the capability to collect an interference-free Raman signature of a material. Nevertheless, this issue can be alleviated by compensating for the fluorescence signal using algorithms. The following are the key advantages of the Raman technique that make it the most robust methodology for material identification:
- Reduction of the instrument size
- Lowering of the detection limits
- Low cost of operation
- Outstanding usability of the technique
Handheld Raman in the Warehouse
Increasing existing analytical laboratory capabilities is one option (Option/Scenario 1) to improve the analytical capability at a minimum cost. However, considering the overall analytical capabilities of the company and the return on investment (ROI), this option is acceptable only if the numbers of samples to be studied are very small. This option is typically suitable for companies that handle less than 10 different materials and when the majority of the samples are already under analysis, so their operational costs are slightly affected by the incremental increase.
Another option (Option/Scenario 2) is equipping the warehouse with new analytical capabilities. Prior to this, the company’s technical department must conduct a technology study to find the most suitable technique. To gain insights into the cost benefits of Option 1 and Option 2, an ROI analysis was performed using real-world data provided by three pharmaceutical companies with production facilities in North America and Western Europe.
Instrumentation
For this analysis, the NanoRam handheld spectrometer from B&W Tek was selected. The NanoRam Raman spectrometer and integrated computing system is specially designed for novice users to perform material identification and validation within GMP compliant facilities. It enables developing standardized and validated procedures rapidly to facilitate purity and quality control applications.
For determining pharmaceutical materials, the NanoRam is equipped with a software package that conforms to both cGMP and 21CFR part 11 certification. B&W Tek also offers optional IQ/OQ services and library/method development services for all NanoRam users.
ROI Analysis
The workload showing current sampling frequency (Option 1) is listed in Table 1, while the proposed number of samples to be analyzed by the handheld Raman instrument is shown in Table 2.
Table 1. Workload showing current sampling frequency (Option/Scenario 1)
Incoming Raw Materials |
Sampling/Frequency |
Operational |
300 days per year |
Raw materials delivered |
3 truck loads per day |
Each load contains (average) |
25 batches of raw materials |
Each batch contains (average) |
5 drums/bags |
Current sampling frequency (7) |
1 sample per batch |
Total number of samples analyzed per year by analytical laboratory (current) |
300x3x25x1 = 22,500 samples |
Table 2. Workload showing proposed sampling frequency (Option/Scenario 2)
Incoming Raw Materials |
Sampling/Frequency |
Proposed testing frequency |
5 samples per batch |
Total number of samples analyzed per year in warehouse using a handheld Raman spectrometer (proposed) |
300x3x25x5 = 112,500 samples |
In Scenario 1, the estimated cost per sample in raw material identification for one of the company that uses its existing laboratory services was in the range of $13-15/sample. Hence, the actual cost needed to be calculated and compared with the cost per sample if all the incoming raw material batches were sampled and determined in the warehouse utilizing the handheld Raman method. A detailed breakdown of the overall cost per sample for Option/Scenario 1 is listed in Table 3.
Table 3. Overall cost per sample for Option/Scenario 1
Current Central Laboratory Capability |
Amount/Cost ($US) |
Operational and maintenance costs per year |
$417,500 |
Salaries of 2 technicians plus a QC/QA manager |
$249,000 |
Total cost of running the lab per year |
$666,500 |
Percentage of time the lab is used for raw materials identification |
60% |
Cost of raw materials identification per year |
$400,000 |
Actual cost of analysis per sample for raw materials identification, based on 22,500 samples/year |
$400,000/22,500 = $17.78 per sample |
In Scenario 2, the central laboratory capabilities of the company are phased out over three years to use handheld Raman devices for materials identification in the warehouse. In this scenario, there has been an increase in the sampling frequency from 22,500 samples to 112,500 per year.
Table 4 illustrates the cost of phasing out the analysis utilizing central lab capabilities, by decreasing it by 50% in the first year, 75% in the second year, and 85% in the final year. Here, roughly 15% of all samples must be sent to the laboratory as ~10% of them are not appropriate for Raman testing and approximately 5% will be used for confirmation or retesting purposes.
Table 4. Plan to phase-out testing of raw materials by central laboratory
Three-Year Phasing out Plan to Reduce Number of Samples by 85% |
Year Number |
Number of Samples/Year (Based on 112,500 samples) |
Cost Per Sample/Year (Based on no change in the actual expenditure of the laboratory) |
Reduced by 50% |
1 |
56,250 (50%) |
$7.11 |
Reduced by 75% |
2 |
28,125 (75%) |
$14.22 |
Reduced by 85% |
3 |
16,875 (85%) |
$23.70 |
Handheld Raman Testing in the Warehouse
In the warehouse, the initial cost of testing is related to the cost of the Raman devices themselves. These particular companies procured two units, one for the central laboratory and another one for the warehouse. The central laboratory unit was utilized for validation protocols, method development, deployment of new IQ's/OQ's, and as a back- up unit.
The cost involved in the analysis of different chemicals was calculated based on technique validation, standard operation procedure (SOP) documentation, personnel time, and cost of reference materials. The time reduction was calculated to be a few hours compared to one or two days, while the space needed was decreased by roughly one-third. The estimations for all these parameters are on the basis of a three-year introduction plan. With the assumption that only 90% of the materials are suitable for Raman testing, the plan aims to implement and test 50% of the materials in the first year, 25% in the second year and 15% in third year.
Table 5. Plan to phase-in warehouse testing of raw materials using handheld Raman systems
Three-Year Phasing-in Plan to Increase Number of Samples by 90% |
Year Number |
Cost of Implementing New Handheld Raman Approach |
Number of Samples/Year (Based on 112,500 Samples) |
Cost Per Sample/Year |
Increase by 50% |
1 |
$150,000 spread over 3 years which includes cost of 2 Raman units plus associated validation procedures, extra consumables and holding additional materials in the quarantine area |
56,250 (50%) |
$1.07 |
Increase by 75% |
2 |
84,375 (75%) |
$0.59 |
Increase by 90% |
3 |
95,625 (90%) |
$0.42 |
Another assumption is that the sample count will remain the same over the three years. Nevertheless, the cost per analysis will be directly affected by the decrease in the number of samples tested by the central laboratory. The phasing-in of the warehouse testing over three years utilizing the two Raman devices is illustrated in Table 5, while Table 6 shows the total cost per sample in third year.
Table 6. Overall Cost of Analysis in Year 3
Breakdown of Workload in Year 3 |
Year Number |
Overall Cost of Analysis |
Number of Samples/Year |
Cost Per Sample |
Central lab samples (reduced by 85%) |
3 |
$400,000 |
16,875 |
$23.70 |
Warehouse Raman samples (increased by 90%) |
3 |
$40,000 |
95,625 |
$0.42 |
Overall cost and total number of samples |
3 |
$440,000 |
112,500 |
$3.91 |
Investment Cost for Additional Central Laboratory Capabilities to Handle Increased Testing
The investment cost for additional central laboratory capabilities to handle the increased workload from 22,500 samples to 112,500 samples per year is then analyzed. The cost of expanding existing analytical capabilities was estimated by adding one full-time and one part-time (50%) workers for preparing and handling samples in the warehouse. Other costs related to keeping the raw materials in the quarantine area for prolonged periods and the additional spaced needed for them were estimated to be 30% of the overall cost.
In addition, the use of existing laboratory equipment, sample handling consumables, and repairs were calculated to be roughly 250% higher when compared to the current expenses. For these companies, the additional cost required was roughly $300,000 per year. When factoring the current central laboratory operational/maintenance expenditure of $417,500 per year into the calculation, the total cost per sample obtained was $6.34 for the sample count increase from 22500 to 112,500. Nevertheless, this value is much lower than the initial cost of testing only 20% of the samples of $17.78. A cost comparison of these two lab-based testing scenarios using the handheld Raman warehouse solution is shown in Table 7.
Table 7. Cost per sample comparison for lab-based analysis and a handheld Raman testing approach in the warehouse
Testing Scenario |
No of Samples Tested |
Investment |
Cost per Sample |
Cost of analysis for raw materials identification, using central lab capability |
22,500 |
Uses existing laboratory services with an estimated cost of $417,500 |
$17.78 |
Cost of analysis for raw materials identification, using central lab capability |
112,500 |
Uses existing laboratory services of $417,500 plus an additional $300,000 (Total of $717,500) |
$6.34 |
Cost of testing in the warehouse using Raman handheld devices |
112,500 |
$100,000 (cost of 2 devices and cost associated with implementation) |
$3.91 |
Conclusion
The results clearly demonstrated that a handheld Raman method of testing in the warehouse provides a significant cost benefit over performing the testing in-house at the central laboratory. Furthermore, the estimations illustrated that the two Raman devices could be justified within the first year of procurement.
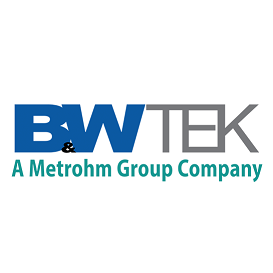
This information has been sourced, reviewed and adapted from materials provided by B&W Tek.
For more information on this source, please visit B&W Tek.