
Ken Smith, Business Development Manager at Olympus NDT, talks to AZoM about recent advancements in handheld X-ray fluorescence (XRF) and how these have benefitted a variety of industries.
How has handheld XRF predominantly been employed by metals manufacturers over the last decade?
Handheld (HH) XRF is primarily used for alloy grade confirmation and identification. These are similar tasks, but depending on the operation there are small differences between “grade confirmation” and “grade identification.”
In grade confirmation, the inspector knows what the grade should be. Whether it is a surgical implant manufacturer’s receiving department confirming “Medical Grade 316 Stainless” or a Petrochemical Valve manufacturer doing final QC on a 5 Chrome valve order.
In grade identification, the inspector is sorting. The inspector doesn’t know what the material is exactly and is going through to identify the material. This happens more frequently with scrap recycling operations, but the same sort of using HH XRF to figure out “what is it?” can be done in pricing a building demolition or simply sorting out maintenance materials that have gotten mixed up.
Could you briefly explain what is meant by Positive Material Identification (PMI) testing and why this is important when manufacturing alloys?
Positive Material Identification (PMI) is one of a few terms used to describe “the grade confirmation” process above. The term is most commonly used in the Petrochemical Industry. The American Petroleum Institute’s (API) Recommended Practice (RP) 578 is titled “Material Inspection Program for New & Existing Alloy Piping Systems.”
However, the same approach is used in many manufacturing processes, (aerospace alloys and surgical implant manufacturing for example) where verifying the alloy is what is specified is critical.
Wherever in the ordering, manufacturing, shipping, receiving, installing, & maintaining process that an alloy is handled, human error is a possibility. Alloys look identical. There is no visual difference between a nickel alloy and a stainless steel or a chrome-molybdenum steel and a titanium alloy. However, the metallurgical properties – corrosion, creep resistance or strength to weight ratio for example - are dramatically different.
What benefits does handheld XRF have over other non-destructive testing methods with regards to Positive Material Identification (PMI) and quality control/assurance (QA/QC)?
The other common point & shoot PMI technology is OES (Optical Emission Spectroscopy). There are 3 basic differences between OES & XRF:
- XRF is truly non-destructive. OES leaves a dime sized burn mark on the material.
- XRF’s size and shape independence is very flexible. Whether it’s strands of wire for a surgical implant material or metal turnings at a scrap recycling process, XRF can produce accurate analytical results.
- Size – XRF is typically smaller and easier to take to the sample.
Could you give an overview of how handheld XRF technology has developed in the last few years?
I would say the significance is really over the last decade or so. In terms of hardware, in 2001, Innov-X (now Olympus NDT) came out with the first fully operational X-ray tube based HH XRF. Other manufacturers of HH XRF rapidly followed suit. The big deal at the time was eliminating the burden of using radioactive material to generate the X-rays. However, the real difference was analytical performance. X-ray tubes generated higher count rates. The net count rate drives precision, accuracy, and test duration. More counts is better in every way – delivering faster and more accurate results across a wider range of elements and concentrations. Also, in 2009, all the manufacturers started to incorporate silicon drift detectors. This technology is 10 to 100 times faster than the previous technology (Silicon Pin Detectors). This essentially took even greater advantage of the power of the X-ray tube.
Advancing electronics have also helped. As with cell phones and PCs, everything has become smaller, faster, less expensive. This means performance goes up and prices go down, which is great! The analytical horsepower delivered in a HH XRF is dramatically greater per pound and per dollar and per second.
How has this influenced the QA/QC of alloys in manufacturing facilities?
XRF is now a standard technology. It enables 100% QC where every sample can be tested either manually or with automated online systems (which implement the hand held technology). But most importantly, it allows redundant testing. I listed earlier all the opportunities to mix materials, via human error. The ability to take 3 seconds to confirm the material with a HH XRF makes real time, redundant testing economically and logistically practical.
What is the importance of being able to detect lighter elements (<Ti) and also having lower detection limits?
It simply extends the range of materials that can be tested reliably. Whether it is aluminum or magnesium grades for helicopter components, or looking at low level aluminum differences in nickel super alloys for jet engines, the utility and certainty of the analysis improves when more elements can be measured and especially at lower concentrations.
How have recent advancements in hardware made it possible to measure alloys at higher temperatures?
Olympus/Innov-X has always been able to function well in what is called “in-service” testing. The pipe, valve or vessel to test is in use in a chemical process, and can be as hot as 1000F!
Two things have recently really advanced this application:
- Experience – we continue to learn how to better handle this application
- Hardware – speed is especially critical in handling hot testing. All of the items listed earlier that improve count rate – the tube, detector and electronics – apply directly to the realm of hot testing.
These 2 elements combine to allow us to reach lower levels faster and for more elements. This allows analytical confidence in short tests on critical components at high temperatures. This means not having to wait for a plant shutdown to perform a test. Plant turnarounds are extremely busy times at petrochemical plants. Being able to test outside of that window is a huge bonus.
Could you give an application example of why this is important in petrochemical plants?
Sulfidic corrosion is a concern in low alloy steels used in some petrochemical plants. RP 939C is an API document that addresses this directly and explains how the presence of sulfur and high temperature can accelerate the corrosion process. The presence of Silicon in the range of 1000 to 2000 ppm (0.1% to 0.2%) reduces the rate of sulfidic corrosion substantially.
If a lack of silicon is identified in an at-risk component, it means an accelerated corrosion testing cycle and replacement cycle can be implemented and the risk of a component failure (rupture) can be greatly reduced.
What is beam collimation and how has this affected weld analysis?
Beam collimation is simply narrowing the beam so the active analysis spot size decreases from 10mm to 3mm. This is primarily a convenience - it allows the inspector to simply touch the screen to select the narrow beam spot when wanting to test only the weld material – seam in a pipe for example.
How do you feel Olympus NDT is unique in the field of Handheld XRF?
Our customers have taught us the importance of productivity - speed with reliability. We aim with our many “smart” features to automate and streamline the process of quickly and accurately testing alloy materials.
How do you believe handheld XRF technology will advance over the next 10 years and how will Olympus be a part of this?
Great question, let me get out my crystal ball! I think it will be more of the same:
- Hardware will improve – tube, detector and electronics – the holy trinity of HH XRF, so to speak!
- Software, driven by customer needs, will continue to streamline and extend reliable field performance
- More applications will be possible, and all applications will run faster and better.
About Ken Smith
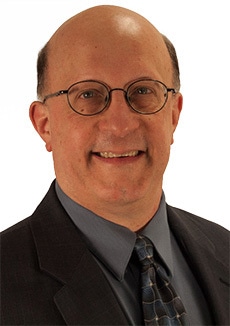
Innov-X Systems incorporated in 2001 & began delivering the world’s first portable tube based XRF analyzer in April, 2002. The company grew to 150 people in the Boston HQ and 40 more at other locations. In July 2010, Olympus purchased Innov-X Systems.
In addition to the original hand-held XRF, products include a range of applied analytical systems, including on-line XRFs for 24-7 industrial analyses, portable bench top style XRF & XRD systems for on-site mining, geotechnical, & environmental testing, and vacuum/purge based XRF analyzers for light element liquid analysis.
One of five original members of Innov-X Systems, Ken’s current responsibility includes business development, product development, & product positioning. With 25 years of varied XRF and analytical experience, he has given many seminars & training classes on XRF for material testing.
Disclaimer: The views expressed here are those of the interviewee and do not necessarily represent the views of AZoM.com Limited (T/A) AZoNetwork, the owner and operator of this website. This disclaimer forms part of the Terms and Conditions of use of this website.