As a major specialty materials supplier, Toray Advanced Composites provides a host of product solutions, including thermoset advanced composite materials, thermoplastic advanced composite materials, bulk composite molding compounds, tooling prepregs, thermoplastic advanced composite materials, compression molding capabilities for part fabrication, honeycomb services, film adhesives and syntactics.
Advanced Composites in the Oil and Gas Industry
All industries demand improved cycle time and shortened downtime. Lowering downtime and maintenance expenses can be achieved using corrosion resistant composite materials.
The deployment of lighter structures, spoolable pipe, and rapid assembly techniques decreases the infrastructure expenses involved in the replacement of pipeline components. Moreover, the work environment will be safer with the use of lightweight materials.
Toray offers lightweight products with a unique combination of high strength, stiffness and improved corrosion resistance. The following are some of the oil and gas applications where Toray products can be used:
- Bridge plugs
- Composite pressure cylinders
- Carbon fiber reinforced tethers
- Electrically pure dielectric structure and enclosures for inspection and monitoring of down holes
- Wrapped pipe and tubing for weight reduction, improved strength, and corrosion resistance
- Molded frac spheres
Toray internal thermoplastic liner and CFRT® overwrap are used in land and subsea umbilicals (Figure 1). In high pressure applications, downhole bridge plugs have found use as it is easier to drill out composite bridge plugs for removal. Thermoplastics and thermosets can be used in the fabrication of oil and gas pipes.
.png)
Figure 1. Land and subsea umbilicals using Toray internal thermoplastic liner and CFRT® overwrap.
Lightweight compressed natural gas tanks with improved strength can be produced using prepreg tapes as carbon fiber overwraps. Many different gases are stored in compressed gas tanks to open or close valves quickly. For this application, Toray provides a range of thermoset prepregs from epoxy to BMIs for use in high-temperature applications.
The fiber-reinforced spoolable thermoplastic composite pipe is used for umbilicals. It comprises a liner strengthened with glass or carbon fiber utilizing Toray Cetex® TC1200 polyetheretherketone (PEEK) or Toray Cetex® TC930 polyethylene (PE) unitapes. The longitudinal reinforcement of this pipe provides high tensile strength and adequate spools ability without fatigue to it.
Thermoplastic Materials Selection Guide
The selection guide for thermoplastic materials is given in the following table:
Product Name |
Thermoplastic Resin |
Process Temp. |
Neat Resin Heat Distortion under Load 1.8 MPa/ 265 psi |
Applications |
Performance Thermoplastics |
Toray Cetex® TC910 |
Nylon 6 (PA6) |
480-520 °F/ 249-271 °C |
392 °F/200 °C |
• Automotive and recreational applications as a result of temperature resistance, toughness, and solvent resistance |
Toray Cetex® TC920 |
Polycarbonate/ABS |
540-580 °F/ 282-304 °C |
205 °F/96 °C |
• Electronic enclosures as a result of its high-quality surface finish and toughness. V0 fire rating maybe over-molded |
Toray Cetex® TC930 |
High-Density Polyethylene (HDPE) |
360-390 °F/ 182-199 °C |
253 °F/123 °C |
• Oil and gas applications such as pipe overwrapping as a result of its strength and toughness |
Toray Cetex® TC940 |
Polyethylene Terephthalate (PET) |
509 °F/265 °C |
392 °F/200 °C |
• Excellent for recreational and low-cost applications for its good impact resistance |
Toray Cetex TC960 |
Polypropylene (PP) |
390-420 °F/ 199-216 °C |
318 °F/159 °C |
• Used in applications where low cost and high toughness desired (vehicles) |
Engineering Thermoplastics |
Toray Cetex® TC1100 |
Poly-phenyl-sulfide (PPS) |
536 °F/280 °C |
230 °F/110 °C |
• Ideal for structural applications under 200 °F/93 °C service temperature
• Very resistant to solvents |
Toray Cetex® TC1200 & TC1220 |
Poly-ether-ether-ketone (PEEK) |
649 °F/343 °C |
300 °F/149 °C |
• Very high strength, used in oil and gas and structural applications
• Good heat resistance to 250 °F/121 °C and above depending upon load |
*For further information on Toray's line of thermoplastic composite materials, please refer to the Toray Cetex® and CFRT® Thermoplastic Composite Brochure.
Thermoset Materials Selection Guide
The selection guide for thermoset materials is given in the following table:
Product Name |
Resin Type |
Tg |
Cure Temp/Cure Time |
Description |
Low to Moderate Service Temperature Thermoset Prepregs |
BT250E-1 |
Epoxy |
257 °F/125 °C |
60 minutes at 250 °F/121 °C |
• Excellent overall system with moderate toughness for impact resistance |
TC275-1 |
Epoxy |
327 °F/164 °C or 362 °F/ 183 °C with post cure |
360 minutes at 275 °F/135 °C, or 120 minutes at 350 °F/177 °C |
• Designed for thick parts under low cure pressures
• Low void laminates
• Compatible adhesive TC263 for bonding core or parts to laminate |
High Service Temperature Thermoset |
EX-1522 |
Epoxy |
396 °F/202 °C |
120 minutes at 350 °F/177 °C |
• Toughened
• Low moisture absorption |
RS-8HT |
BMI |
471 °F/244 °C |
120 minutes at 400 °F/204 °C, followed by post cure of 360 minutes at 450 °F/230 °C |
• Thermal stability under high temperatures
• Moderate toughness with good moisture resistance
• Available in RTM resin form |
TC350-1 |
Epoxy |
397 °F/230 °C |
120 minutes at 350 °F/177 °C |
• Excellent laminate quality with low pressure cures
• Good temperature performance with excellent toughness
• Very long work life, 30 days tack life and 45 days for tool life |
TC420 |
Cyanate Ester |
350 °F/177 °C or 610 °F/ 321 °C with post cure |
180 minutes at 350 °F/177 °C Optional post cure of 500 °F/260 °C for higher Tg |
• TenCate's highest temperature cyanate ester
• Processes like an epoxy yet yields a Tg and performance of a BMI
• Excellent thermal stability, good resistance to microcracking |
TC800 BMI+ |
BMI |
471 °F/244 °C |
6 hours at 350 °F/177 °C, followed by 2 hours at 450 °F/230 °C |
• An out of autoclave, vacuum cure processible high temperature BMI
• Excellent high temperature resistance while offering easier oven processing |
Bulk Molding Compounds
Toray's CCS Composites designs and manufactures high-performance compression molded composite components. CCS Composites is a specialist in the design and fabrication of components that take advantage of the properties of molding compounds, especially in the manufacture of extremely high tolerance, geometrically intricate components.
Compression molding is an alternative solution for intricate components typically fabricated from aluminum or titanium (Figure 2). Glass and carbon chopped fiber are the typical reinforcement materials; however other materials are also used.
.jpg)
Figure 2. Compression molding is an alternative solution for intricate structures made of aluminum or titanium.
As a highly controlled process, compression molding uses precise resin infused fiber-reinforced tape made from standard, intermediate or high modulus fibers, and thermoplastic (PEEK, PPS, PEI or Nylon) or thermoset (BMI, cyanate ester, epoxy, and much more) resins.
To make bulk molding compounds, these unitapes are chopped into a fiber length range of 12-258 mm. Smaller length fibers enable molding more intricate structural details into the component, while longer fiber lengths improve strength.
The materials selection guide for bulk molding compounds is given in the following table:
Product Name |
Resin Type |
Tg |
Description |
Resin Properties |
Bulk Molding Compounds |
MS-1A |
Epoxy |
327 °F/164 °C |
High modulus epoxy |
Tensile Strength - 42 ksi (290 MPa)
Tensile Modulus - 19 Msi (131 GPa) |
MS-1H |
Epoxy |
375 °F/191 °C |
Fast cure intermediate modulus epoxy |
Tensile Strength - 37 ksi (255 MPa)
Tensile Modulus - 10 Msi (69 GPa) |
MS-4A |
Epoxy |
327 °F/164 °C |
Standard modulus epoxy |
Tensile Strength - 45 psi (310 MPa)
Tensile Modulus - 9 Msi (62 GPa) |
MS-4H |
Epoxy |
375 °F/191 °C |
Fast cure standard modulus epoxy |
Tensile Strength - 44 ksi (303 MPa)
Tensile Modulus - 6 Msi (41 GPa) |
MS-4J |
Epoxy(FR) |
327 °F/164 °C |
Fire retardant standard modulus epoxy |
Tensile Strength - 50.5 ksi (348.0 MPa)
Tensile Modulus - 9.6 Msi (66.1 GPa) |
TenCate Cetex MC1100 |
PPS |
194 °F/90 °C |
Thermoplastic based with standard or IM fibers |
Tensile Strength - 28 ksi (193 MPa)
Tensile Modulus - 5.9 Msi (40.4 GPa) |
TenCate Cetex® MC1200 |
PEEK |
290 °F/143 °C |
Thermoplastic based with standard or IM fibers |
Tensile Strength - 42 ksi (289 MPa)
Tensile Modulus - 6.3 Msi (43.4 GPa) |
Various |
Thermoplastic |
Various |
Standard or intermediate modulus |
Various |
The following table provides comparison of reinforcements:
Material vs Reinforcements |
Filament Count |
Tensile Strength |
Tensile Modulus |
Density g/cc |
Steel |
n/a |
58 ksi (400 MPa ) |
29 Msi (200 GPa) |
7.8 |
Aluminum |
n/a |
70 ksi (483 MPa) |
10 Msi (69 GPa) |
2.8 |
E- Glass |
n/a |
290 ksi (2,000 MPa) |
10.5 Msi (72 GPa) |
2.6 |
S- Glass |
n/a |
680 ksi (4,689 MPa) |
12.5 Msi (86 GPa) |
2.5 |
Standard Modulus Carbon |
12K (also 18K, 24K, 48K) |
500-700 ksi (3,447-4,826 MPa) |
~30-34 Msi (207-234 GPa) |
1.8 |
Intermediate Modulus Carbon |
12K |
~800 ksi (~5,516 MPa) |
~40 Msi (276 GPa) |
1.9 |
High Modulus Carbon |
6K, 12K |
~575 ksi (~3,965 MPa) |
~60-80 Msi (414-552 GPa) |
1.9 |
Ultra High Modulus Carbon |
1K, 3K, 12K |
~500 ksi (~3,447 MPa) |
-115 Msi (793 GPa) |
2.2 |
The following table lists standard weave styles for fabrics:
Table of Standard Weave Styles for Fabrics |
Areal Weight (oz/yd2 / gsm) |
Description |
E-Glass |
120 (4 harness satin) |
3.14/106 |
Lightweight glass fabric |
|
7781 (8 harness satin) |
8.87/301 |
Drapable 8 harness fabric |
S-Glass |
6781 |
8.94/303 |
High strength drapable 8 harness fabric |
Ceramic |
Plain Weave or 5 harness |
7.2-24/244-814 |
Ceramic-based woven fabrics |
Carbon |
Plain Weave - 3k |
5.7/193 |
Good fabric stability, but less drapable |
|
2 x 2 Twill |
6.0/205 |
More drapability than pw, more stable |
5 harness |
8.3/281 |
Good drapability |
8 harness |
10.8/366 |
Excellent drapability |
Conclusion
Toray meets the specific composite material requirements of customers by providing the appropriate solution cost-effectively.
Advanced composites offered by Toray are beneficial to customers in many ways. The advantages include weight reduction, high strength and stiffness, corrosion resistance, excellent toughness and fatigue resistance, ease of fabrication via common molding processes, ability to optimize strength and stiffness, and low flame, smoke and toxicity performance.
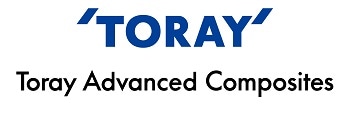
This information has been sourced, reviewed and adapted from materials provided by Toray Advanced Composites.
For more information on this source, please visit Toray Advanced Composites.