A range of polymeric materials such as synthetic rubbers, adhesives, and paints have been produced using emulsion polymerization, which is carried out in an aqueous environment. The reaction involves using an appropriate surfactant or emulsifier to maintain the monomer species within a single phase and maintaining the surfactant concentration in excess of the critical micelle concentration in order to produce a stable emulsion by retaining the unsaturated monomer in the center of the micellar structure. The polymerization is initiated by a free-radical mechanism and continues as a double bond addition reaction, yielding polymers or copolymers in a latex form.
Significance of Monitoring Process
Having the ability to monitor the consumption rate of monomer species or the relative consumption rate of co-monomers is crucial to ensure the occurrence of the rate of formation of desired products. If the reaction involves co-monomers, it is essential to ensure the consistency of the relative reaction rates with the production of desired products. Residual monomer is another problem and revealed by the existence of unreacted double bonds.
Instrumentation and Experimental Procedure
The sensitivity of Raman systems to measure specific double bonds and their immunity to interference from the aqueous environment makes them ideal for monitoring emulsion polymerization reactions. In addition, Raman systems allow monitoring of the reaction from outside via walls of the glass reactors.
This experiment studied the formation of styrene–butyl acrylate copolymer. The reaction summary is provided in Figure 1. The analysis involved a 3L glass reactor mounted with a Raman fiber optic probe from outside and a reaction mixture of styrene and butyl acrylate monomers irradiated by a laser radiation.
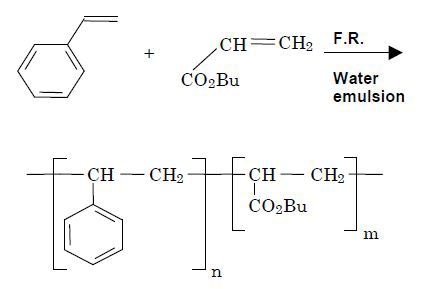
Figure 1. Reaction summary
The reaction mixture was dispersed in a dodecylbenzene sulfonate (surfactant) solution consisting of ammonium persulfate (initiator), sodium sulfate, tert-dodecyl mercaptan (moderator), and sodium hydroxide in small quantities. The mixing rate and the reaction temperature were remained constant during the reaction. An external water bath was used to maintain the temperature at 55°C, with addition of ice for further cooling whenever needed.
Kaiser Optical Systems’ RamanRxn2™ analyzer was used to monitor the reaction using 785-nm laser excitation. A multi-element lens system was used to collect the Raman scattered light, which was redirected to the spectrometer using a 10-µm core fiber optic cable.
Experimental Results
Figure 2 presents the Raman spectra, showing the interference of the glass reactor walls as represented by the region 1100-1800cm-1. Monitoring of the overall reaction is through the observation of decreasing intensity of a1631-cm-1 band, which represents both styrene’s characteristic 1631-cm-1 C=C band which overlaps butyl acrylate’s characteristic 1639-cm-1 C=C band.
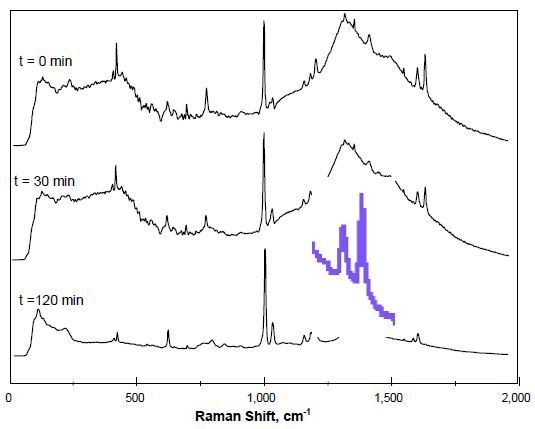
Figure 2. Monitoring changes in unsaturation of monomers.
Deviations in overall measured intensity over the course of the reaction are offset by the ratio of the 1631-cm-1 band and the1000-cm-1 band of the intense styrene, aromatic ring. The concentration of residual C=C double bands was also separately measured by GC analysis using grab samples. Figure3 shows the correlation between the GC data and the ratioed Raman intensities, quantifying the reaction as a function of total unsaturation.
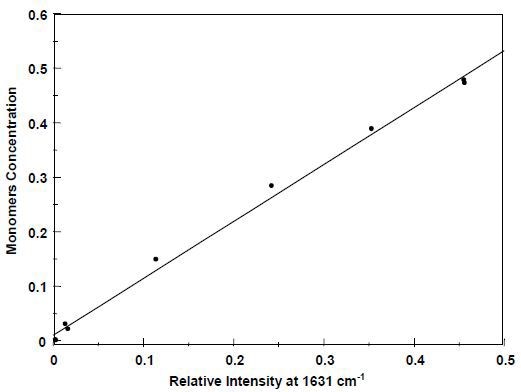
Figure 3. Total monomer concentration: Raman vs. GC.
The ratio between the 1412-cm-1 vinyl C–H band and the 1000-cm-1 ring band is monitored to determine the styrene monomer consumption rate. The difference may help determine the butyl acrylate concentration. Figure 4 presents the overall monomer-to-polymer conversion, with superimposed GC and gravimetric data.
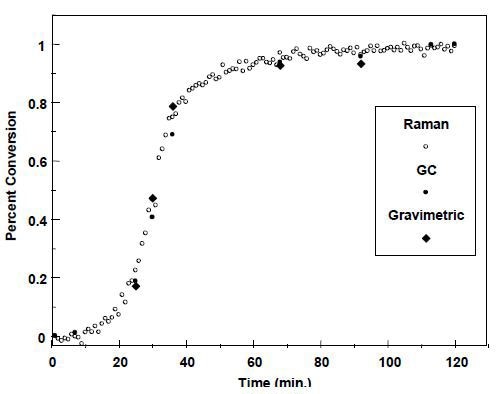
Figure 4. Conversion profile for styrene–butyl acrylate emulsion polymerization.
Conclusion
From the results, it is evident that Raman spectroscopy is ideally suited to monitor addition polymerizations, especially emulsion systems. The resultant Raman spectra are free from the interference of the aqueous environment. FTIR systems cannot be used for this experiment due to the high absorbance of the aqueous matrix and their incapability to monitor the reactions through the reactor walls.
About Kaiser Optical Systems
Kaiser Optical Systems, Inc. is a world leader in spectrographic instrumentation and applied holographic technology. Principal products include Raman sensors and instrumentation, advanced holographic components for spectroscopy, and astronomy and ultra-fast sciences. Principal offices and the manufacturing facility are located in Ann Arbor, Michigan.
Their products and services are deployed throughout the world in such diverse applications as pharmaceutical and chemical manufacturing, nanotechnology, telecommunications, education, forensic science, deep-sea exploration, and astronomy. From particles smaller than a human hair to objects as large as planets, their products are providing their customers unique insights into both today’s as well as “age-old” questions.
Kaiser was founded in 1979 to meet the need for diffractive or holographic optics for the avionics market. Kaiser entered the spectroscopy market in 1990 with the introduction of the holographic notch filter. In 1993 Kaiser released their first Raman analyzer, the HoloProbe. In 2013, the company became part of the Endress+Hauser Group.
To better serve the European community, Kaiser opened a new subsidiary in Europe in 1998. Kaiser Optical Systems SARL is located in Lyon, France. Kaiser SARL supervises their distributor network within Europe.
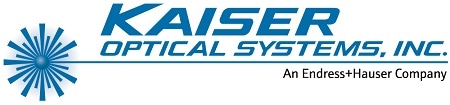
This information has been sourced, reviewed and adapted from materials provided by Kaiser Optical Systems.
For more information on this source, please visit Kaiser Optical Systems.