New and in-service fluids encounter solid contamination from machinery burrs, filter deterioration and blow-by, worn mechanical seals, dirt and sand from the environment, and solid oxides from oxidation of surfaces within the machinery.
Solid contamination of these fluids can be monitored by particle counting. All particulate irrespective of their shape and composition can be measured by particle counters with output as size distribution, particle count, and ISO code.
Types of Particle Counters
Pore Blockage Particle Counters
Pore blockage particle counters (Figure 1) use a fine mesh to accumulate the particulate for in-service machinery oil analysis. The on-site particle counters operate on the basis of a constant pressure or constant flow design. In both designs, extrapolation is used to estimate the particle count distribution. The limited data generated by these counters hinders their widespread use in commercial laboratories.
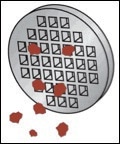
Figure 1. Pore blockage particle counter uses a fine mesh for in-service machinery oil analysis.
Laser Light Blocking Particle Counters
Laser light blocking particle counters (Figure 2) are traditionally employed for in-service oil analysis. When the laser light illuminates a specimen, part of the light is blocked by particles, allowing only less light to reach the photodetector array. The resulting voltage change varies in proportion to the area of the particles. The presence of air bubbles or water in the sample affects the results significantly. Hence, the sample needs to be ultrasonically agitated and treated with water-stripping solvents to obtain a more accurate count.
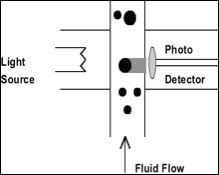
Figure 2. The working principle of traditional light blockage particle counters
LaserNet Fines (LNF) Direct Imaging Particle Counter
LNF particle counter features a solid-state laser coupled to a CCD array, creating a direct imaging particle counter as shown in Figure 3. The sample is illuminated by the laser and the laser light is magnified by an optical lens. The images of the sample are captured by a CCD video camera and stored in the memory for subsequent size and shape analysis.
For each image, an equivalent circular diameter (ECD) is estimated to provide a report of particle count and size distribution with ISO codes. Although, the LNF can deliver results in other output formats, the most common format is ISO 4406.
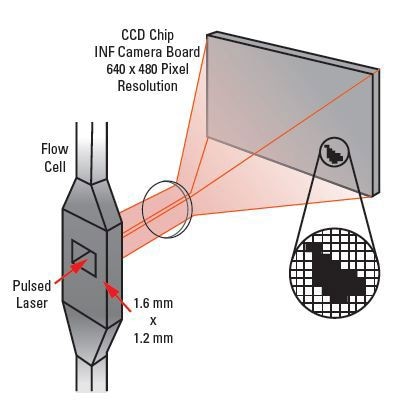
Figure 3. The working principle of LNF particle counter
The LNF enables an 'Automated Ferrography' capability for classification of wear particles, thanks to its ability to acquire the actual wear particle silhouette. Determining the type of wear particle and yielding information on size distribution, particle count, and the severity level of each of the abnormal wear mechanisms supports the data collected by other techniques, including ferrous monitoring and analytical ferrography. Spectro LNF Q220 and Q230 instruments have this capability.
The LNF is capable of differentiating between air bubbles, water droplets, and solid particles of larger than 20µm. The true net particle count can be determined by subtracting the count of water and air bubbles from the total particle count. The comparison of LNF and light blockage particle counters is summarized in Table 1.
Table 1. Comparison of LNF and light blockage particle counters
FACTORS |
OPTICAL PARTICLE |
COUNTERS LNF Q200 |
Calibration |
Annual Calibration, typically by Manufacturer. |
No Calibration required. Validate as desired with PartiStan. |
Dilution |
Yes, for dark oil, dirty oil or high viscosity oil. |
For high viscosity oil (>320 cSt) only. |
Coincident error |
Typical 8-10% |
< 2% |
Saturation level |
10,000-300,000 parts/ml (typical) |
5,000,000 parts/ml |
Equivalent circular diameter |
Estimate. Based on light transmission. Errors with semitransparent particles and water bubbles. |
Actual. Detects and classifies nonmetallics, water and air bubbles > 20um. |
Repeatability |
Poor. Multiple tests needed, typical lab reports an average of three measurements. |
Excellent. No multiple tests needed. |
Automation |
Yes, factory supplied turnkey. |
Yes. Field expansion possible. |
Advantages of LNF Direct Imaging Particle Counter
The LNF does not require routine calibration and its performance validation can be done by conducting the standard sample test with PartiStan™ calibration fluid. This instrument has a low coincidence error of 2% and a very high saturation limit of 5 million particles /ml as it employs a 2D 640 x 480 photodetector array instead of a one dimensional point source photodetector.
Moreover, the LNF flow cell allows simultaneous viewing of multiple particles. It observes the trajectory of single particles and is capable of monitoring any subsequent splitting of the image into two tinier ones, which is unfeasible in the case of a photodiode.
The high saturation limit of the LNF enables measurement of dirtier and darker oils with no dilution. The LNF requires dilution only for samples more than 320cSt. Hence, it produces more accurate and reproducible results than laser-based particle counters.
Furthermore, the LNF can distinguish between semi-translucent particles and solid particles, enabling it to monitor both total particle count and the count of non-metallic (contaminant) particles.
In laser light blockage system, light passes through semi-translucent particles. As a result, the photodetector is not able to measure the entire area of the silhouette (Figure 4). Conversely, the direct imaging LNF provides an accurate particle size because the missing areas are filled in by the neural network.
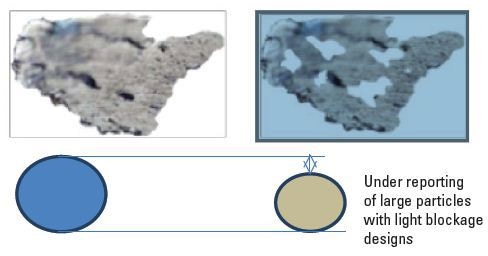
Figure 4. Semi-translucent particles and Equivalent Circular Diameter calculation
Correction for water and air bubbles to the measured particle count is possible with the LNF (Figure 5). In addition, particle count for water bubbles larger than 20µm are measured and reported as a separate category, thus facilitating the determination of water quantity required for water-stripping solvent preparation technique (ASTM D7647). The presence of free water in a specimen is measured and reported by LNF instruments. The LNF employs automatic gain control of the laser to capture sample images for measurement of soot level of up to 2%.
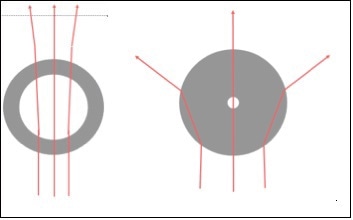
Figure 5. At left, slight laser light refraction because the refractive index of the water is very close to that of the oil. At right, laser light refracts considerably because the refractive index between the oil and the air differs greatly.
Conclusion
The comparison demonstrates the supremacy of the LNF particle counter for analysis of in-service oils. It yields particle count codes with multiple output codes for a particle size range of 4-100µm. Water and air bubble correction, and the ability to measure count of non-metallic particles for monitoring contaminants as well as total particles are the other key features of the LNF particle counter.
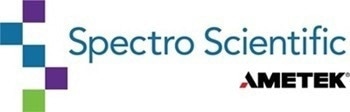
This information has been sourced, reviewed and adapted from materials provided by AMETEK Spectro Scientific.
For more information on this source, please visit AMETEK Spectro Scientific.