Rheological testing of thermoplastic materials can be carried out on both melts and solid samples. Issues related to process ability can be correlated with polymer melt properties, or problems regarding product performance are often related to the properties of solid samples. Mechanical spectroscopy is typically used for testing thermoplastic solids to analyze the structure and polymer morphology and ultimately relate these to end-use performance.
Precise solid state measurements of the material’s modulus (G’), glass transition temperature (Tg), and damping (tan δ) are used to estimate many performance properties such as energy dissipation, impact properties, stiffness, etc. Rheological tests on thermoplastic melts determine the flow properties of material and offer useful data regarding polymer processing. In addition, it is possible to determine the rheological properties as the material experiences temperature-induced modifications from molten to solid and vice versa.
Viscosity and Elasticity
The viscosity of melts decreases as the shear rate increases. One way to measure the rate of the viscosity changes with shear rate (Cox-Merz) is to perform oscillation measurements across a range of frequencies. This is essential in terms of processing ease and for establishing processing energy requirements. In addition, this measurement gives a concurrent measure of melt elasticity and the source of such phenomena as die swell.
Low Shear
In material problem solving, low shear rate measurements in the linear viscoelastic region of melt play an important role. Whilst high shear rates are often involved in injection molds and extrusion, shear rate behavior often controls the quality of finished parts.
Time Dependence and Deborah Number
Since thermoplastic polymers are viscoelastic materials, they exhibit a pronounced time or frequency dependence. For convenience, thermoplastic melts are differentiated with a representative material relaxation time. Similarly, separate steps in a transformation or production process can be illustrated by a characteristic process time (Figure 1).
.jpg)
Figure 1. Process and material time
The De (Deborah) number is a key process parameter. In a film blowing process, increasing the take up speed is similar to decreasing the process time. To ensure that the De number remains constant, the material time needs to be altered by reducing the viscosity. Failing to adapt the characteristic materials time would cause the material to exhibit more solid-like behavior under the latest processing regime, thus leading to reduced performance and ultimate breakdown of the film.
Shear and Elongation
The majority of rheological tests are carried out in shear using capillary or rotational rheometers. The elongation viscosity of elastic materials at huge deformations can diverge considerably from the shear viscosity and hence represents a major parameter to design process equipment or estimate processing performance. Elongation characteristics at huge deformations correlate with molecular structure. As such the elongation viscosity is a highly sensitive indicator of long chain branch
Effect of Molecular Structure and Morphology
Molecular Weight
Molecular weight is the chief structural parameter of the flow behavior of polymers at temperatures over the melting point (for a semi-crystalline polymer) or the glass transition temperature (for an amorphous material). Melt viscosity is a constant at low frequencies or shear rates. For polymers of low molecular weight, the zero shear viscosity is proportional to the molecular weight of the polymer. However, over a critical molecular weight, chains start to entangle and the zero shear viscosity relies more strongly on molecular weight, proportional now to about the 3.4 power of the molecular weight, as illustrated in Figure 2. As a result, rheological measurements are suitable for analyzing the effects of molecular weight variations in resins because slight variations in molecular weight result in large changes in viscosity.
.jpg)
Figure 2. The zero shear viscosity is a sensitive measure of polymer molecular weight. The relationship for flexible linear polymers is ηo.
Molecular Weight Distribution
At constant molecular weight, the quantity of energy needed to process the polymer is proportional to the shear rate dependence of viscosity. The degree and onset of shear thinning differ among materials and qualitatively correlate with the molecular weight distribution. For instance, polymers having a wide broad distribution will thin more at lower shear rates when compared to polymers having a narrow distribution at the same average Mw. (Figure 3).
.jpg)
Figure 3. Molecular weight distribution differences in polymer melts are easily detected by measuring the complex viscosity η* as a function of frequency.
For example, molding and extrusion can be made easier by widening the molecular weight distribution of a polymer. The properties of end products such as surface smoothness in a range of thermoplastic molded goods, or sag and haze in blown LDPE films can be modified by changing the molecular weight distribution.
Branching
Branches of polymer chain can differ with respect to length, number and distribution along the main chain. Melt viscosity changes by increasing the size, number, or flexibility of the branches. In case the branches are few and sufficiently long to entangle, melt viscosity will be relatively high at low frequency when compared to a matching linear polymer of the same molecular weight, as shown in Figure 4.
.jpg)
Figure 4. Effect of branching on the complex viscosity η* and the dynamic moduli G’, G””.
When compared to the viscosity of linear polymers, viscosity of long-branched polymers is more shear rate dependent. The extensional viscosity at high strains considerably increases with long chain branches. In Figure 5, the rheological responses of a long chain branched LDPE is compared with a linear LLDPE in elongation. The marked viscosity increase at large elongation strains is typical for long chain branching.
.jpg)
Figure 5. Elongation viscosity of LDPE (branched) and LLDPE (linear) show pronounced differences at high total strains. This strain hardening effect is a characteristic feature of long chain branching.
Fillers
When fillers are added to a polymer melt, its rheology is modified, affecting the way the melt processes and also the properties of the end product. Major factors are filler concentration, filler size and shape, and the degree of any interactions between the particles. The outcome of adding fillers are a decrease in die swell and an increase in melt viscosity. Filled polymers exhibit a higher viscosity at low shear rates, and yielding may occur with an increased concentration of filler (Figure 6). Adding fillers also leads to reduced linear viscoelastic range, defined by the onset of the strain dependent behavior.
.jpg)
Figure 6. The viscosity of a highly filled LDPE exhibits yielding at low shear rates.
Blends
Polymer blends are physical mixtures of two or more polymers. Polymer blends are heterogeneous if the components exist in separate phases, and homogeneous if the components are compatible and combine at a molecular level.
The minor component is often mixed in a matrix of the dominant component and the compatibility of a blend depends on temperature. In this instance, the blend is assumed to be partly miscible. In the event they are not compatible, mechanical energy is required to disperse the minor phase. Coalescence can occur if the blend morphology is not properly stabilized. In addition, the elastic properties of incompatible blends rely on energy storage mechanisms at the interphase. The relaxation of the dispersed phase is usually longer than that of the relaxation of the polymer chains of the separate components. Figure 7 illustrates the spectrum of a PMMA/PS blend with varied volume fractions of the minor phase. The extra low frequency contributions in G’ are the result of form relaxations of the large distributed domains of the minor phase. If the average droplet size is known, it is possible to determine the interfacial tension from the average relaxation time of the droplet relaxation.
.jpg)
Figure 7. The increase contributions of G’ at low frequency can be used to calculate the interfacial tension of non-compatible blends.
Blends that are not compatible exhibit clear glass transitions for each component. However, the value may change in relation to the pure components. Blends that are uniform show just a single glass transition. The assessment of the glass transitions therefore provides data regarding interphase effects and compatibility. Figure 8 depicts the tan d trace of a PPO/HIPS 50:50 blend, altered with a polymer called methyl-metacrylatebutadiene-styrene (MBS). The modifier displays as a further transition at -45°C temperature, independent of the concentration. The reduced compatibility is due to the structure of the MBS that includes a PMMA shell imbedding a SB rubber core.
.jpg)
Figure 8. PPO/HIPS blend modified with MBS. The additional transition at -45°C independent of concentration proves poor compatibility.
In addition, blending offers a way to change the elastic modulus. Pressure sensitive adhesives or PSA are known to have excellent adhesion properties when the modulus is from 5x105 to 105Pa at use temperature. By varying the content of tackifying resins in a natural or synthetic rubber matrix, the modulus can be adjusted as required(Figure 9).
.jpg)
Figure 9. Comparison of PSA adhesive based on natural rubber and SIS copolymers. The SIS-based adhesive exhibits a wider application window (constant G’= 105Pa)
Application Examples
Processing -Molecular Structure and Ability To Process
Rheological measurements are widely utilized to analyze polymer melts. The acquired parameters illustrate the basic behavior of materials like PVC, ABS, polyolefin, etc. In injection molding, bottle blow molding, sheet forming, fiber spinning, cable jacket extrusion and other similar processes, rheological measurements correlate LCB, molecular weight, molecular structure, and molecular weight distribution to such processing behavior as melt stability, flow rate, die swell, frozen-in stresses and recoverable shear. Melt viscosity and the initial normal stress difference data determined in cone plate is shown in Figure 10.
.jpg)
Figure 10. Shear viscosity and first normal stress difference of two blow molding polyethylenes M-1 and M-2 exhibiting significant process performance.
M-1 and M-2 are HDPEs that were found to be quite similar by GPC and capillary viscometry and yet perform very differently in a normal bottle blowing line. M-2 created heavier bottles. While the molecular weight distribution and viscosity (Table 1) of these two materials are almost similar, the normal stresses reported vary considerably.
Table 1. Two HDPEs, M-1 and M-2.
Table 1 |
M-1 |
M-2 |
MF1 (190; 2.16) |
0.6 |
0.5 |
GPC (Mw) |
131500 |
133600 |
GPC (Mz) |
907000 |
1035000 |
η (@ 1s1) |
84000 |
83000 |
η (@ 100s1) |
10200 |
9500 |
Swell (%) |
28 |
42 |
The quantified normal stress variation matches well with the parison swell - a variation in long chain branching or a small quantity of high molecular weight component may be the origin. Owing to the increased die swell, the parison is thicker and hence the increased weight of the bottle. Uniaxial elongation viscosity measurements in the melt can be carried out to assess the effect of long chain branching. Data is illustrated in Figure 11 for three polyethylenes, an HDPE, LDPE and LLDPE.
The LDPE shows a distinct strain hardening, while the HDPE shows less strain hardening. The LLDPE follows closely the trace of 3x the zero shear viscosity and also reaches steady state more rapidly than the LDPE and HDPE.
.jpg)
Figure 11. Shear and elongation viscosity for LDPE, HDPE and LLDPE5
Rheology During Injection Molding - Effect on Residual Strain
For high viscosity melts such as filled thermoplastics or unvulcanized elastomers, cone plate measurements suffer from difficulties forming the sample prior testing as well as edge effects at higher shear rates during testing. In contrast, oscillation measurements probing the material with a sinusoidal shear deformation using parallel plates instead of cone plate, are easier to perform. The dynamic mechanical characterization of an injection molding grade ABS is shown in Figure 12.
.jpg)
Figure 12. Oscillation and capillary data for an injection molding ABS compound. Cox-Merz η*(w)= η (γ) holds.
Besides viscosity, oscillation measurements also offer a measurement of the materials elasticity, denoted by the storage modulus G’. Melt strength and relative warpage effects also rely on the elastic nature of the polymer melt and the flow behavior in the mold.
Irregular surface cracking and crazing issues on the molded ABS components are the outcome of surplus orientation and residual strains. In the glass transition region, torsion tests on the solid sample can be utilized to measure the quantity of residual strains in an injection molded part. Figure 13 shows a DMA trace on newly molded samples and on companion parts annealed under vacuum for a period of eight hours at 180°C temperature. The tan d and storage modulus G’ were determined at a strain of 0. 07% and a frequency of 1Hz from 120°C to 130°C. Marked variations were observed between the unannealed and annealed samples close to the main glass transition. The sample having residual strains exhibited a higher tan δ across a wide range of temperatures below the glass transition temperature Tg. This corresponds to the relaxation of the backbone conformations of the oriented styreneacrylnitrile component in the continuous phase.
.jpg)
Figure 13. Effect of annealing on loss tangent of an injection molded ABS part.
Melt Degradation of PV
Melt degradation plays a key role in almost all melt processing operations. It can be easily tracked by recording the dynamic moduli at a constant frequency as a virtue of time at process temperature. PVC is highly sensitive to process temperature, as illustrated in Figure 14 for the two injection molding compounds, A and B. Both compounds differed in terms of color concentrate and flame retardant additives. In comparison to sample B, sample A displays fast degradation after 20 minutes at 215°C.
.jpg)
Figure 14. PVC melt stability followed in oscillation for sample A and B at different temperatures.
Extrusion Problems of Thermoplastic Melts
Thermoplastic extrusion is a high shear process. However, once the extrudate exits from the die, the shear rate reduces significantly. Figure 15 illustrates the storage modulus as a virtue of frequency acquired from dynamic mechanical tests on two grades of polyurethanes utilized for medical tubing. The material with the higher G’’ offers too thick tubing and the material having the lower G’ provides too thin tubing.
In similar processing conditions, the slight variation in elasticity denoted by G’ is sufficient to make the tubing off specification because of the differences in die swell. While extruding the die, the polymer accumulates internal strains. As the polymer excites the die, the strains recover, causing the polymer to swell. The extent of swelling relies on the ability of the material to store the shear rate, deformation energy, and the residence time in the die. In the material, the degree of branching and distribution of molecular weight impact the degree to which internal strains form and recover. Since G’ is related to the amount of stored energy during the course of deformation, it gives an estimate of the degree of recovery of the PU resin. The higher the die swell, the thicker the tubing.
.jpg)
Figure 15. Two grades of extrusion polyurethane. The grade with the higher elasticity (G’) produces the thicker tubing.
Performance
Effect of Multi-Stage Drawing and Moisture on the Morphology of Fibers
The end performance and morphology of synthetic fibers largely rely on their processing conditions. The drawing process leads to molecular orientation and can improve crystallization and orient the crystals themselves. These phenomena impart high strength and at the same time can impact end-use performance.
Figure 16 illustrates the elastic modulus as well as the damping of two fibers from the same PP grade drawn down to the same level. A higher elastic modulus is seen in the two stage drawn fiber at temperatures greater than the glass transition. This can be correlated to increased crystallinity owing to a greater degree of orientation. Although the glass transition at -11.5°C temperature is the same for both fibers, the two-stage drawn fiber display a smaller damping peak, denoting a higher crystallinity. These crystalline regions serve as cross-linking points, which prevent the sliding motion of the molecular chains, thereby offering a fiber that has greater strength.
.jpg)
Figure 16. Modulus and damping of PP fibers, drawn in a one and a two stage process down to the same extent. A smaller damping peak stands for higher crystallinity and fiber streng
Improving the Impact Behavior of Polystyrene Juice Cans
Orange juice cans made from rubber-modified high impact polystyrene resins had differences in impact resistance. High impact phenomena correspond to mechanical deformations in the order of milliseconds. Due to the equivalence of time and temperature, fast mechanical 8 AAN013 processes at ambient temperature correlate with low speed testing at low temperature. Hence, energy absorption determined at frequencies of 1Hz correlates to impact resistance and toughness. The change in the glass transition temperature Tg and the β peak is because of compounding effects to polymer phase and compatibilization of the rubber. In this case, the variations in tan δ results from differences in the type and amount of rubber impact modifier.
Bond Strength, Tack and Peel, Toughness and Flexibility of Adhesive
Rheological properties control the application characteristics and performance behavior of adhesives. Bond strength is tested by conducting a tack or peel test. Peel and tack resistance had to be properly balanced to form a suitable adhesive. Poor adhesives are found to exhibit low levels of elasticity at low rates and too much elasticity at high rates. This allows the substandard adhesive to stick inadequately or to rip the substrate when peeling.
It is important to ensure that hot melts are strong and flexible at use temperature for the majority of applications. Book binding compounds should not become fragile over the predicted use temperature range.
Figure 17 illustrates the dynamic modulus as well as the loss behavior for a standard hot melt. The variations in storage modulus denote a high performance difference at use temperature. Toughness can be related quantitatively to the transition denoted by tan δ.
.jpg)
Figure 17. Flexibility correlates with the loss modulus, toughness relates to the tan δ peaks.
The level of the loss modulus can be correlated to the flexibility of the adhesive. Another major parameter for hot melt adhesives is viscosity stability at processing temperatures. Resins are often stored for long periods of time in open tanks in dispersing systems. The viscosity against time for a polyamide-based resin defines open time. The poor sample accrues viscosity because of oxidative cross-linking and hence proves ineffective when long open times are needed.
Conclusion
This article provides a better understanding of the rheological characteristics of thermoplastic polymers. It also demonstrates the effect of molecular structure and morphology such as molecular weight, molecular structure, molecular weight distribution, etc. on the flow behavior of polymers.
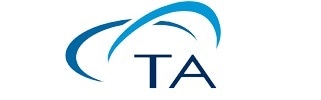
This information has been sourced, reviewed and adapted from materials provided by TA Instruments.
For more information on this source, please visit TA Instruments.