The majority of global shipping companies are practicing slow steaming operations in view of the overcapacity of shipping on profitable trade routes, and depressed freight rates. When the main two-stroke engines are run at 40 to 60% of their nominal output, a significant saving can be made on fuel costs, but this may result in cylinder cold corrosion if lubrication is not properly controlled. To further compound this problem, low sulfur emission control areas (SECA) have been recently expanded on lucrative trade routes, making ship operators switch to low sulfur fuels in such zones. As a result, these operational and business differences are leading ship owners/operators to turn to other technologies that not only keep up with the latest changes, but also provide a better understanding of the engine lubrication conditions.
Wärtsilä and other engine developers highlight the need for more frequent inspections of the piston underside, as well as the need to determine the residual base number (BN) regularly so as to improve cylinder feed rates and prevent cold corrosion (Figure 1). The Wärtsilä Two-stroke Services Team launched RT-161, a new technical bulletin with updated needs regarding the management of cylinder lubrication, along with the latest guidelines on shipboard condition monitoring in today’s operating climate.
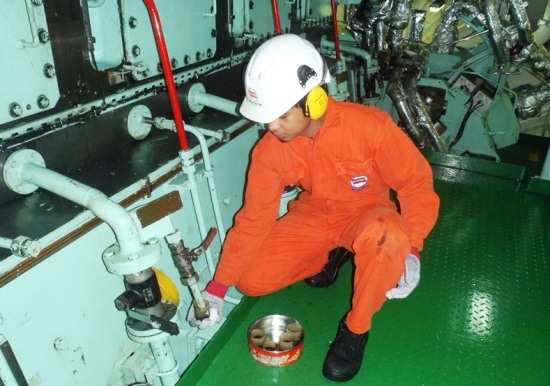
Figure 1. Operators drawing daily cylinder lube oil samples from piston underside drain.
Wallem Ship Management, and other ship operators, handle this complex business operation and its environment, and are using innovative tools to track changing lubrication conditions on board. The aim is to find new ways to sustain and enhance ship reliability, and also reduce costs to a large extent.
Tomasz Placzek, Technical Superintendent for Wallem, said that the use of low sulfur fuels has changed the recommendations of most engine manufacturers with respect to engine performance parameters, corrosion control, and cylinder lubrication methods. Operators are now more focused on day-to-day monitoring of drained oil piston undersides and stuffing boxes. Measurement of BN, along with other parameters, aids the definition of the exact feed rate of cylinder lubrication and inlet BN of the lubricant being used.
Since cylinder oil continues to be costly, using the right amount of oil at the right time is vital. In a present-day scenario, costs of new cylinder oil can span between $1300 and $2500 per ton. Over lubrication can cost more than US $100,000 in terms of lubricant costs per ship per annum. This value can be significantly reduced with closer BN monitoring to calibrated feed rates.
Current Challenges
Lubricant suppliers' onshore labs are used by a large number of ship operators for their oil analysis requirements, but this takes considerable amount of time, and thus makes it difficult to change the feed rates of cylinder lubrication depending on a data point collected 10 or more days in the past. To obtain an onboard result, certain ship owners have invested in a manual chemical shaker kit technique (Figure 2). However, these systems still take considerable amount of time, and involve the use of dangerous chemicals. As a result, ship operators scarcely use these systems, thus limiting the benefits of regularly onboard BN measurement. As a result of a standard testing time between 3 and 10 minutes, different accuracies, and chemical handling, ship owners and operators have looked for a better option.
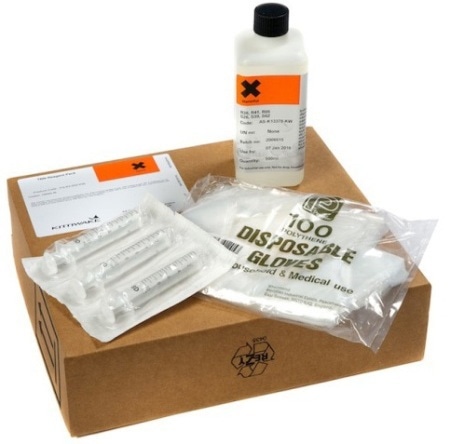
Figure 2. Typical hazardous materials supplies for shaker kits. They require safety training and proper storage.
A New Approach
The FluidScan infrared analyzer is a portable spectrometer that provides accurate and reliable measurement of water contamination and lubricant condition, and eliminates the requirement for hazardous materials or solvents. The instrument determines the oil absorbance spectrum in the mid-infrared range, and uses a diffraction grating-based optic with a detector for improved durability and portability, instead of FTIR technology that is more extensively employed in oil analysis laboratories. On the raw infrared spectrum, a specific chemometric calibration is applied so as to acquire oil condition data like nitration, sulfation, oxidation, anti- wear additive, BN, total acid number (TAN), soot, water, and glycol contamination.
A patented flip top cell analyzer uses a single drop of oil, eliminates the use of solvents/chemicals to clean, and takes less than a minute (Figure 3). In addition, an onboard database is included, with asset data and preset alarm limits using a traffic light system. All these ensure that maintenance workers can take instant decisions following the measurement. The US Navy marine logistics arm — the Military Sealift Command TAK-E — class of supply ships used this analyzer and not only saved time, but also enhanced the results, which led them to implement the system across the fleet.
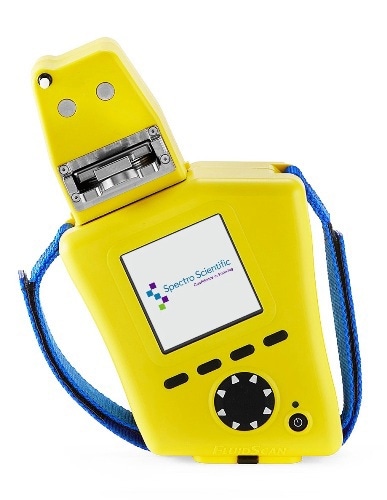
Figure 3. The FluidScan Q1200 IR analyzer provides a quick, accurate measurement for lubricant condition without the need for solvents or hazardous materials.
Practical Experience
The Wallem Group is one of the leading providers of maritime solutions, with Wallem Ship Management controlling more than 400 vessels. The latter explores new means to reduce costs, which eventually led the Hamburg Office Fleet Manager to explore the FluidScan infrared analyzer. Wallem Ship Management suggested that this analyzer could be used on the 229 m M/V Belo Horizonte (IMO 9605645), a large carrier that belonged to Verwaltungsgesellschaft Alexander Oetker Schifffahrt, Hamburg. In 2014, the M/V Belo Horizonte was operating on the Brazil Shanghai trade route.
Mr. Placzek stated that the use of the Spectro FluidScan analyzer has shown that day-to-day monitoring of drained cylinder oil condition reduces the cost of cylinder lubrication, and also prevents the risk of untimely wear of piston rings and cylinder liners. Samples are obtained from individual cylinders on a daily basis for on board analysis. The quantity of samples to be analyzed on board adds up quickly, given that a large number of carriers contain five or six cylinder engines. With about 200 days at sea per year, the carrier takes roughly 1000 - 1200 analyses of lubricant samples.
The BN of drain oil from each individual engine cylinder is reported on a daily basis to the technical staff in the ship for optimization of feed rate protocols. In addition to the BN, maintenance personnel keep records on board for other parameters. With the Fluidscan’s data logging feature, this can be easily obtained. Water content, and the total acid number of oil from the system and stern tube, are determined and tracked. Samples are taken from storage tanks comprising fresh lubricants, and the same are tested. Likewise, samples of circulation oil used with additives are also tested. The tool’s versatility, and the integrated oil application libraries, allow these analyses to be performed. The team at Wallem was impressed with both the speed and repeatability of the system.
Mr. Plazcek added that while the time taken for every day analyses is an added advantage of using the analyzer, precise measurement is also highly important. While BN measurements performed with standard shaker techniques give higher results of 3-5 BN numbers, these are inadequate for premature wear and corrosion control of engine parts. In contrast, the FluidScan analyzer generates results that are similar to oil analysis results acquired from shore-based, professional labs.
Onboard Monitoring Catches a Problem
The instant results can really have a positive impact on how the ship’s crew handles possible issues relating to lubrication that impede standard operations. On the Belo Horizonte, regular inspection of the engine crankcase oil, taken to modify the Blending-on-Board system, indicated unexpected BN results and higher water content on the system oil. A rapid onboard analysis showed that the issue was in a cylinder stuffing box region, and this was addressed instantly (Figure 4).
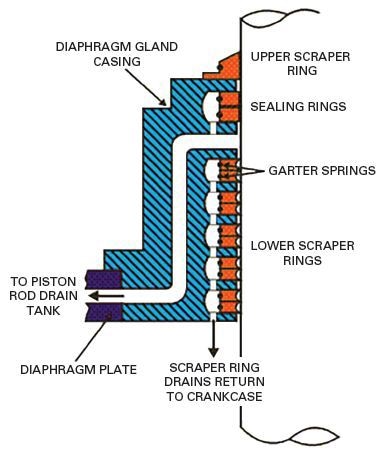
Figure 4. If rings are damaged or worn, more cylinder oil enters the system oil through the stuffing box. In the case described above, the cylinder oil polluted the system oil, and it was detected by the crew using Fluidscan.
Ease of Use and Maintenance
The FluidScan is integrated with intuitive and transparent operation procedures, allowing operators on board the ship to implement them properly. It also eliminates the need for oil analysis training. Mr. Placzek was happy that it is possible to fix the unit remotely. An issue that demanded a software upgrade was corrected by technical staff on board the ship. Also, there is no need to land ashore to carry out repairs.
Conclusion
One of the key areas of focus for ship owners/operators is to reduce maintenance expenses. Although the shipping market is gradually scaling back from the worldwide recession, lowering maintenance costs will continue to remain a major factor to secure lasting profits for ship owners. Reducing cylinder lubrication expenditures with high overhaul intervals, combined with extended service lifespan of engine parts, are the major targets in all budget estimations and maintenance plans.
Tested on board a Wallem-controlled bulk carrier, the FluidScan Q1200 instrument has shown to be a precise and consistent tool for oil analysis as it is safe to use for routine analyses, avoids delivery problems owing to its around-the-clock availability, and removes the use of solvents or reagents utilized in conventional analyses and measurements on board the carrier.
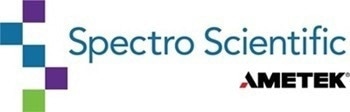
This information has been sourced, reviewed and adapted from materials provided by AMETEK Spectro Scientific.
For more information on this source, please visit AMETEK Spectro Scientific.