Toray Advanced Composites is a global materials technology company that supports a wide range of applications for engineered composites. With its heritage, manufacturing technology, and technical capabilities, the company can support the employment of advanced composite materials in four areas of application: space & aerospace; safety & protection; sport & recreation, and infrastructure & environment. All the production sites of Toray Advanced Composites, whether in the United Kingdom, the Netherlands, North America, or Canada, have their own expertise and specialty.
Go Lighter
Industrial – Both thermoplastic and thermoset options across a wide range of performance targets and prices are available from Toray. The following markets benefit from Toray’s materials:
- Consumer electronics
- Medical
- Sport & recreation
- Marine
Go Further
Transportation – Materials offered by Toray reduce the weight of and improve fuel efficiency across a wide range of transportation industries including:
- Automotive
- Trucks
- Interiors
- Rail
Go Deeper
Energy – Toray’s high-performance composites provide an innovative alternative to non-reinforced plastics and conventional metals generally used in the oil and gas market. Some of the applications include:
- Pressure vessels
- Frac plugs
- Piping
- Gaskets
- Tubulars
- Overwraps
- Low dielectric enclosures
Go Together
Toray uses the synergy of global production sites via intensive internal cooperation at commercial and technical levels to benefits its customers. The advanced composite market is characterized by a partnership between suppliers, research institutes, and customers. After all, new applications are developed mainly in partnerships.
The benefits of advanced composites include:
.jpg)
Product Solutions
- Thermoset advanced composite prepregs and UD tapes
- Composite tooling prepregs
- Thermoplastic advanced composite UD tapes, laminates, and prepregs
- Film adhesives and syntactic
- Bulk molding compounds
- Compression-molded parts
- Honeycomb core
Toray offers a suitable solution to meet the various composite material requirements of customers.
Market Applications
- Automotive
- Energy
- Motorsport and Formula 1
- Medical
- Consumer electronics
- Sport and recreation
Advanced & Performance Composites Products - Industrial Applications
Transportation
Weight reduction and high volume manufacturing are two major considerations for the automotive industry. The fast stamping processes that were designed to be used with thermoplastic composite materials can meet these high volume needs. When compared to metallic parts and injection molded parts, continuous fiber-reinforced materials provide equivalent stiffness and strength with a lower weight. The rapid cure, out-of-autoclave thermoset prepregs from Toray are best suited for exterior body panels. The Toray Cetex® thermoplastics are ideal for underbody panels, impact beams, automotive seats, and pedals. The materials can also be used in various manufacturing processes, including automated tape placement, continuous compression molding, thermoforming, injection over-molding, and stamping.
.jpg)
Energy
In an industry where every minute counts, improving cycle time, and reducing downtime are critical. By using corrosion-resistant composite materials, downtime can be reduced. The infrastructure costs associated with pipeline component replacement can be reduced by spoolable pipe, rapid assembly methods, and the use of lighter structures. Toray’s products provide a combination of high strength, stiffness, and improved corrosion resistance in a lighter weight.
.jpg)
.jpg)
.jpg)
.jpg)
Some oil and gas applications include:
- Wrapped tubing and pipe for weight reduction, corrosion resistance, and increased strength,
- Electrically pure dielectric structures and enclosures for downhole inspection and monitoring
- Molded frac spheres
- Composite pressure cylinders
- Carbon fiber reinforced tethers
- Drill plugs
Other Applications
Consumer electronics – Toray offers lightweight, innovative, visually unique, and highly durable solutions for next-generation electronics, including tablets and smartphones. With its facilities in Asia, Europe, and North America, Toray is capable of supporting the requirements of turnkey manufacturing on a global scale.
Sport & recreation – The unique high stiffness, high strength, and lightweight properties of composites make them valuable across a variety of markets. Today, composites are used to produce tennis racquets, golf club shafts, fishing rods, bicycles, bats, boat paddles, hockey sticks, and a variety of other applications. CFRT® thermoplastic composites from Toray can be found in various applications from high-end athletic footwear to hockey skate base plates, providing stability with comfort and lightweight.
Medical - Toray Advanced Composites, which continually invests in product development, has a portfolio of thermoplastic and thermoset materials that have been specifically developed for use within medical applications such as X-ray couches, tables and mammography plates, surgical target devices and tools, MRI & C scanner components, orthotics, prosthetics, wheelchairs, and walking aids.
Thermoset Composites
Thermoset composites from Toray use both direct impregnation and film impregnation to control the resin content and the degree of impregnation to meet unique handling and processing requirements for each customer. The company works with industry-standard glass, carbon, and aramid fibers in UD, woven, and multi-axial (NCF) reinforcements. Toray’s product range also includes visual quality standard carbon reinforcements. The company offers a wide range of proprietary resin systems ranging from toughened epoxies to high-temperature cyanate esters and BMIs.
Low-Temperature Curing Thermoset Prepregs
Product name |
Resin type |
Tg (onset) |
Cure temp / Cure time |
Key product characteristics |
Toray E644 |
Epoxy |
124 °C (255 °F) |
3.5 hours at 70 °C (158 °F) |
- Toughened epoxy capable of rapid cure
- Excellent surface finish
- 7 days out life
|
Toray E650 |
Epoxy |
121 °C (250 °F) |
3.5 hours at 70 °C (158 °F) |
- Lower tack version of Toray E644
- Medium tack level, easier lamination
- 5 days out life
|
Low to Mid Temperature Curing Thermoset Prepregs
Product name |
Resin type |
Tg (onset) |
Cure temp / Cure time |
Key product characteristics |
Toray 8020 |
Epoxy |
121 °C (250 °F) |
5.5 hours at 80 °C (176°F) |
- Flexible cure schedules 70-130 °C (158-266 °F)
- Post curable for higher Tg applications
|
Toray 8020-FR |
FR Epoxy |
121 °C (250 °F) |
5.5 hours at 80 °C (176°F) |
- Toray 8020-FR is fire resistant under FAR 25.853 Appendix F - vertical burn material test criteria (i)
- 30 days out life at ambient temperature with good adhesive properties for honeycomb core
|
Toray 8020 Rapi-Ply |
Epoxy |
111 °C (232 °F) |
5.5 hours at 80 °C (176 °F) |
- Outstanding vacuum-only (out of autoclave) processing capability. No debulking required
- Bi-layer form facilitates fast lay-up
- Significantly reduced lay-up times (up to 75%) compared with traditional prepreg routes
- Flexible low to medium cure schedules 70-130°C (158-266°F)
- 7 days out life
|
Toray RS-1 |
Epoxy |
107 °C (225 °F) |
1.5 hours at 93 °C (200 °F) |
- Low cure temperature curing epoxy
- 21 days out life
|
.jpg)
Mid Temperature Curing Thermoset Prepregs
Product name |
Resin type |
Tg (onset) |
Cure temp / Cure time |
Key product characteristics |
Toray E760 NEW |
Epoxy |
204 °C (399 °F) |
2 hours at 180 °C (356 °F) |
- High temperature resistance and high mechanical performance
|
Toray E750 NEW |
Epoxy |
148°C (298°F) |
60 minutes at 135 °C (275 °F) |
- Variable temperature cure, starting at 80 °C (176 °F)
|
Toray TC250 |
Epoxy |
140 °C (285 °F) or 180 °C (356 °F) with post cure |
60 minutes at 88 °C (190 °F) follow by 2 hours at 130 °C (265 °F) Optional post cure of 60 minutes at 177 °C (350 °F) for higher Tg |
- Long out time with excellent toughness for impact resistance
- Has the ability to be post cured for higher temperature performance
|
Toray E731 NEW |
Epoxy |
140 °C (284 °F) |
60 minutes at 125 °C (257°F) |
- High cosmetic clarity for automotive components e.g. door panels, centre console, dashboard
|
Toray BT250E-1 |
Epoxy |
125 °C (257 °F) |
60 minutes at 121 °C (250 °F) |
- Excellent overall system with moderate toughness for impact resistance
|
Toray E721-FR |
FR Epoxy |
120 °C (248 °F) |
60 minutes at 120 °C (248 °F) |
- Fire retardant version of E720 under FAR 25.853 Appendix F - vertical burn material test criteria (i)
|
Toray E722 |
Epoxy |
120 °C (248 °F) |
60 minutes at 120 °C (248 °F) |
- Excellent drapability
- General-purpose component prepreg
|
Toray E745 NEW |
Epoxy |
118 °C (244 °F) |
60 minutes at 135 °C (275 °F) |
- High toughness and impact properties
|
Toray
E720
|
Epoxy |
110 °C (230 °F) |
60 minutes at 120 °C (248 °F) |
|
Toray E726 NEW |
Epoxy |
105 °C (221 °F) |
60 minutes at 120 °C (248 °F) |
- Controlled flow
- Good surface finish
- 60 days out life
|
High Service Temperature Thermoset
Product name |
Resin type |
Tg (onset) |
Cure temp / Cure time |
Key product characteristics |
Toray C640
|
Cyanate Ester |
335 °C (635 °F) |
10 hours at 80 °C (176 °F), followed by 2 hours at 300 °C (572 °F) post cure |
- Variable cure temperatures 70-135 °C (158-275 °F)
- Postcurable for high Tg
- High-Temperature resistance for applications such as brake ducts
|
Toray C740 |
Cyanate Ester |
325 °C (617 °F) |
2 hours at 135 °C (275 °F), followed by 2 hours at 280 °C (536 °F) post cure |
- Excellent high-temperature capabilities for pipework and ducting applications
- Features long out time for larger parts
|
TorayTC420 |
Cyanate Ester |
177 °C (350 °F) or 348 °C (658 °F) with post cure |
3 hours at 177 °C (350 °F) Optional post cure of 260 °C (500 °F) for higher Tg |
- Toray’s highest temperature cyanate ester
- Processes like an epoxy yet yields a Tg and performance of a BMI
- Excellent thermal stability, good resistance to microcracking.
|
Toray RS-8HT |
BMI |
255 °C (545 °F) |
2 hours at 204 °C (400 °F), followed by post cure of 6 hours at 230 °C (450 °F) |
- Thermal stability under high temperatures
- Moderate toughness with good moisture resistance
- Available in RTM resin form
|
Toray Ambertool® Composite Tooling Solutions - Tooling Prepregs
The HX and TC prepreg series of the Toray AmberTool® range have over two decades of pedigree in high-performance motorsport, and are sold globally by a proven team of tooling experts. The comprehensive range of tooling products offered by Toray allows customers to complete tool design freedom and flexibility.
Toray provides a complete service, enabling a single supplier approach to all-composite tooling requirements, from master to material to technical support. The company’s tooling product solutions enable the fabrication of “machined to shape” or highly precise molded tools for tight tolerance part fabrication.
.jpg)
Master and Surface Coat Package
- High-performance epoxy block*
- EC85 surface coating technology*
Complete Tooling Solutions
- Wide range of glass and carbon reinforcements
- Machinable
- Quick delivery solutions for standard materials
- Glass and carbon backing structures
Experienced Technical Support
- Proven processing guidelines documented in Toray’s Tooling Processing Guide
- Mold life-cycle maintenance solutions
- Specialized knowledge on mold surface treatment
Toray Ambertool® Prepregs
Product name |
Resin type |
Tg (onset) |
Cure temp / Cure time |
Key product characteristics |
Toray AmberTool® HX40 |
Epoxy |
203 °C (397 °F) after post cure |
12 hours at 65 °C (149 °F), followed by post cure |
- Long out life system (10 days) with high-temperature performance
|
Toray AmberTool® HX42 |
Epoxy |
200°C (392 °F) after post cure |
8 hours at 60 °C (140 °F), followed by post cure |
- Proven system with aerospace qualifications
- Excellent resistance to phenolic resins
- Good high-temperature performance
- 5 days tack life
|
Toray AmberTool® HX50* |
Epoxy |
190 °C (374 °F) after post cure |
8.5 hours at 50 °C (122 °F), followed by post cure |
- Excellent system for small to medium-sized autoclave tooling
- Provides excellent surface finish with a fast cure
- 60 hours tack life
|
Toray AmberTool® HX44* |
Epoxy |
188 °C (370 °F) after post cure |
10 hours at 60 °C (140 °F), followed by post cure |
- Excellent tooling system for most applications
- Ideal for glass fabric use
- 4 days tack life
|
Toray AmberTool® HXR56* NEW |
Epoxy |
185 °C (365 °F) after post cure |
8.5 hours at 50 °C (122 °F), followed by post cure |
- Two-layer product for rapid speed of lamination
- Fully impregnated multi-axial construction
|
Toray AmberTool® TC40** |
BMI |
213 °C (415 °F) after post cure |
6 hours at 177 °C (350 °F), followed by post cure |
- High service temperature tooling prepreg
- Long 30 days out life with a 14 days tack life
- Thermally stable at high temperature
|
Ancillary Materials
Product name |
Resin type |
Tg (onset) |
Cure temp / Cure time |
Key product characteristics |
Toray EC85 surface coat* |
Epoxy |
65 °C (167 °F) after post cure |
N/A |
- Surface coating technology for tooling block
- High hardness, high gloss 2 part liquid system
|
Sourced from: * Europe ** North America
Toray Cetex® Thermoplastic Composites - UD Tapes, Prepregs, and Laminates
Toray Cetex® and Toray CFRT® have more than three decades of experience and pedigree. They have set the standard for high quality, engineered thermoplastic composite materials. The company has expertise in semicrystalline and amorphous thermoplastics. From PP, PA6, and PMMA all the way to PEI, PEEK, and engineered PAEK, Toray can design the polymer to meet customers’ requirements.
Toray’s Cetex® thermoplastic materials are available in a wide range of fabric-based laminates (RTLs), UD tapes, or prepregs to facilitate the manufacturing process and part design of customers.
.jpg)
Toray Cetex® Thermoplastics
Product name |
Thermoplastic matrix |
Tg /Tm* |
Application examples |
UD tape |
Prepreg |
RTL |
Toray Cetex® TC1225 |
Engineered Poly-Aryl-Ether-Ketone (PAEK) |
147 °C (296 °F) Tm 305 °C |
- Suited for overmolding
- Excellent mechanical performance
- Medical, oil, and gas applications
|
O |
O |
O |
Toray Cetex® TC1200 / TC1220 |
Poly-Ether-Ether-Ketone (PEEK) |
143 °C (289 °F) Tm 343 °C |
- Very high strength, used in oil, gas, and structural applications
- Good heat resistance to 121 ºC (250 ºF) and above depending upon load
|
O |
O |
O |
Toray Cetex® TC1100 |
Poly-Phenylene-Sulfide (PPS) |
90 °C (194 °F) Tm 280 °C |
- Ideal for structural applications under 93 ºC (200 ºF) service temperature
- Very resistant to solvents
|
O |
O |
O |
Toray Cetex® TC1000 Design |
Polyetherimide (PEI) |
217 °C (423 °F) |
- Excellent FST performance
- Medical applications and transportation e.g. train door applications
|
|
O |
O |
Toray Cetex® TC925 |
Polycarbonate (PC) FST grade |
153°C (307°F) |
- Good surface qualities, impact toughness
- Good heat resistance
|
|
O |
O |
Toray Cetex® TC950 / TC951 |
Polymethyl Methacrylate (PMMA) |
|
- Broad range of application-specific materials**
- Engineered to meet the structural demands of volume applications including orthotics**
|
|
|
O |
Toray Cetex® TC910 |
PA6 (Nylon 6) |
60 °C (140 °F) |
- Temperature and solvent resistant
- Excellent toughness
- Automotive and recreational applications
|
O |
|
|
Toray Cetex® TC912 |
PA6 (Nylon 6) |
60 °C (140 °F) |
- Specifically developed for high volume processes
- Especially suitable as a preform insert for compression and over-molding to increase part performance
|
|
|
O |
Toray Cetex® TC930 |
High-Density Polyethylene (HDPE) |
210 °C (410 °F) |
- Oil and gas applications such as pipe overwrapping as a result of its strength and toughness
|
O |
|
|
Toray Cetex® TC940 |
Polyethylene Terephthalate (PET) |
|
|
O |
|
|
Toray Cetex® TC960 / TC962 |
Polypropylene (PP) |
130 °C (266 °F) |
- Used in applications where low cost and high toughness are desired (vehicles)
|
O |
|
O |
*Melting point is only shown for semi-crystalline (PAEK family) thermoplastic products
**For further information please refer to Toray’s Materials for the Consumer Footwear and Orthotics Markets selector guide
Lightweight Composites - Design, Part, and Fabrication Services
Compression Molded Parts
Toray’s CCS Composites group specializes in designing, tooling, and fabrication of complex compression molded parts with chopped thermoplastic and thermoset-based materials. Compression molding provides an alternative to machining and hand lay-up for complex geometry components. It also offers high volume production at a lighter weight and lower cost.
General reinforcements used in CCS’s compression molding process are glass and carbon chopped fiber, with thermoplastic resins or toughened epoxy.
.jpg)
Bulk Molding Compounds
Compression molding is a highly controlled process that uses precise resin-infused fiber-reinforced tape made of standard, intermediate, or high modulus fibers. The resins can be either thermoplastic (PEEK and PPS) or thermoset resin.
For making bulk molding compounds, these UD tapes are chopped into fiber lengths ranging from 12 to 50 mm (1/2” to 2”). While longer fiber lengths provide higher strengths, smaller length fibers allow more complex structural details to be molded into the part.
.jpg)
Product name |
Resin type |
Tg (onset) |
Description |
Resin Properties |
MS-1A |
Epoxy |
164 °C (327 °F) |
- Epoxy with high modulus fiber
|
Tensile Strength - 290 MPa (42 ksi)
Tensile Modulus - 131 GPa (19 Msi) |
MS-1H |
Epoxy |
191°C (375 °F) |
- Fast cure epoxy with intermediate modulus fiber
|
Tensile Strength - 255 MPa (37 ksi)
Tensile Modulus - 69 GPa (10 Msi) |
MS-4H |
Epoxy |
191 °C (375 °F) |
• Fast cure epoxy with standard modulus fiber |
Tensile Strength - 303 MPa (44 ksi)
Tensile Modulus - 41 GPa (6 Msi) |
Toray Cetex® MC1100 |
PPS |
90 °C (194 °F) |
- Thermoplastic based with standard or intermediate modulus fibers
- Fire retardant
|
Tensile Strength - 193 MPa (28 ksi)
Tensile Modulus - 40.4 GPa (5.9 Msi) |
Toray Cetex® MC1200 |
PEEK |
143 °C (290 °F) |
- Thermoplastic based with standard or intermediate modulus fibers
- Fire retardant
|
Tensile Strength - 289 MPa (42 ksi)
Tensile Modulus - 43.4 GPa (6.3 Msi) |
.jpg)
Full sole footplate Toray Cetex® TW2000 Carbon / PMMA (TC950).
.jpg)
Electrical enclosure Toray Cetex® TC910 Carbon / PA6.
.jpg)
Backpack frame Toray Cetex® TC940 Glass / PET UD tape.
.jpg)
Military helmet accessory Toray Cetex® TC910 Carbon / PA6 UD tape.
Film Adhesives and Syntactics - Rolls, and Sheets
Toray provides a wide variety of film adhesives that are compatible with its prepregs. Film adhesives are used for bonding pre-cured or post-cured laminates or for honeycomb bonding of skin to core.
The syntactic offered by Toray represent epoxy films that are loaded with glass microspheres for high compressive strengths and low density. The Amlite and Amspand line of syntactic films from Toray are best suited for edge close outs, reinforcement areas, core splices, and sandwich core construction.
.jpg)
Product name |
Resin type |
Tg (onset) |
Cure temp |
Key product characteristics |
Toray 8020 SF |
Epoxy |
121 °C (250 °F) |
80 °C (176 °F) |
- Composite surfacing film which provides class A finishes
- Provides a protective, durable surface layer for composites
- Easily sandable and has 7 days out life
|
Toray EF44 |
Epoxy |
126 °C (258 °F) |
70 °C (158 °F) |
- Toughened epoxy adhesive film with 7 days out life
|
Toray EF72 |
Epoxy |
112 °C (234°F) |
120 °C (248 °F) |
- Structural epoxy film adhesive with 30 days out life
|
Toray EF8020 |
Epoxy |
116 °C (241 °F) |
80 °C (176 °F) |
- Wide cure temperature between 70-130 °C (158-266 °F)
- 30 days out life
|
Toray TC235SF-1 NEW |
Epoxy |
119 °C (246 °F) |
121 °C (250 °F) |
- Excellent surfacing characteristics
- Vacuum cure capable composite surfacing film
- Available with lightning strike screens
- 30 days tack life, 45 days out life
|
Redux® 212-NA Foaming Film Adhesive* |
Epoxy |
260 °C (500 °F) |
120 °C (248 °F) |
- Core splice foaming film adhesive
- 90 days out life
|
*Redux is a registered trademark of Hexcel, offered from Langley Mill, UK
Syntactic Core
Product name |
Resin type |
Tg (onset) |
Cure temp |
Key product characteristics |
Toray Amlite LT64 |
Epoxy |
130 °C (266 °F) |
50-80 °C (122-176 °F) |
- Low temperature, low-density film with 7 days out life
- Non expanding
- Co-compatible with Toray E600 series
|
Toray Amlite SC8020A |
Epoxy |
106 °C (223 °F) |
80 °C (176 °F) |
- Low density, non-expanding
- Flexible cure temperatures 70-130°C (158-266°F)
|
Toray Amlite SC72A |
Epoxy |
106 °C (223 °F) |
120 °C (248 °F) |
- Mid temperature curing, non-expanding, syntactic film. Ideal for sandwich structures under 3 mm (0.11 inches)
- Excellent for edge closeouts
|
Toray Amspand ES72A-2 |
Epoxy |
114 °C (237 °F) |
125 °C (257 °F) |
- Expanding syntactic core
- Varying density by tailoring cure pressure and / or volume
|
.jpg)
Honeycomb Core and Reinforcements - Honeycomb Core Materials and Material Comparisons
Toray Advanced Composites, UK (Langley Mill), has the largest independent core processing operation in Europe. In addition to Flex Core® honeycomb, Aluminum and Nomex® honeycomb are also available. The company has an extensive stock for customers to choose from. The company cuts all orders to customer’s thickness specifications and provides them with fast turnaround times.
Honeycomb core*
Product name |
Configuration |
Key product characteristics |
Aluminum Honeycomb - Commercial Grade |
1.8-3/4-25N-3003
3.4-1/4-15N-3003
3.7-3/8-25N-3003
3.7-3/8-25P-3003
5.2-1/4-25N-3003
5.2-1/4- 25P-3003 |
- High strength-to-weight properties at relatively low cost
- Easily machined and formed for applications such as air or fluid control, light collimation, heat exchangers
- Protects surface damage when used in laser cutting
|
Aluminum Honeycomb - Aerospace Grade |
3.1-1/8-07N-5052
4.5-1/8-10N-5056
4.5-1/8-10N-5052
6.1-1/8-15N-5056**
5.2-1/4-25N-5052
8.1-1/8- 20N-5056**
8.1-1/8-20N-5052 |
- High strength-to-weight properties at relatively low cost
- Improved mechanical properties in comparison to commercial grades
- Broader selection of densities than commercial grades
- Sheet size 1250 x 2500 mm except **1220 x 2440 mm
|
Nomex® Honeycomb - Commercial Grade |
ANC-3.2-48 3.2 mm 48 kg/m3
ANC-4.8-32 4.8 mm 32 kg/m3
ANC-4.8-48 4.8 mm 48 kg/m3
ANC-4.8-48(OX) 4.8 mm 48 kg/m3 |
- Fire-resistant and self-extinguishing
- Good thermal and electrical insulating properties
- High strength-to-weight ratio and easily formable to shape
- Sheet size 1250 x 2500 mm
|
Nomex® Honeycomb Aerospace Grade |
ANA-3.2-29 3.2 mm 29 kg/m3
ANA-3.2-48 3.2 mm 48 kg/m3
ANA-3.2-64 3.2 mm 64 kg/m3*
ANA-4.8-48(OX) 4.8 mm 48 kg/m3 |
- Fire-resistant and self-extinguishing
- High-temperature strength up to 180°C (356°F)
- Good dielectric properties
- Nomex® paper sheets are coated and bonded together with a high modulus phenolic resin
- Sheet size 1250 x 2500 mm except** 1220 x 2440 mm
|
Aluminum Flex-Core® |
5052/F80 - .0013N Density 4.3
5052/F80 - .0024N Density 8.0
5056/F80 - .0014N Density 4.3 |
- Unique cell configurations that permit small radii of curvature without deformation of the cell walls or loss of mechanical properties
- For parabolic, spherical, and cylindrical shapes
|
Flex-Core® is a registered trademark of Hexcel. Nomex® is a registered trademark of E.I du Pont de Nemours and Company.
*Offered from Langley Mill, UK. Additional grades can be sourced upon request, subject to minimum order quantities and extended lead times
Material Comparisons
Material vs. reinforcements |
Filament count |
Tensile strength |
Tensile modulus |
Density g/cc |
Steel |
n/a |
400 MPa (58 ksi) |
200 GPa (29 Msi |
7.8 |
Aluminum |
n/a |
483 MPa (70 ksi) |
69 GPa (10 Msi) |
2.8 |
E-Glass |
n/a |
2,000 MPa (290 ksi) |
72 GPa (10 Msi) |
2.6 |
High Strength Carbon |
3K, 6K, 12K (also 18K, 24K, 48K) |
3,447-4,826 MPa (500-700 ksi) |
230-245 GPa (33-36 Msi) |
1.8 |
Intermediate Modulus Carbon |
6K, 12K |
~5,516 MPa (~800 ksi) |
275-304 GPa (40-44 Msi) |
1.9 |
High Modulus Carbon |
6K, 12K |
~3,965 MPa (~575 ksi) |
>340 GPa (>49 Msi) |
1.9 |
In addition to glass and aramid fibers in UD, woven and multiaxial (NCF) reinforcements, Toray works with high strength, intermediate and high modulus carbon fibers. The company offers both pitch- and PAN-based carbon fibers.
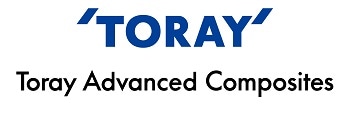
This information has been sourced, reviewed and adapted from materials provided by Toray Advanced Composites.
For more information on this source, please visit Toray Advanced Composites.