Sponsored by Mo-SciApr 20 2016
Solid Oxide Fuel Cells (SOFCs) are the subject of intense research for developers to help minimize the carbon emissions released during electricity generation, as they have a high conversion efficiency and are ideal for energy distribution.
They are capable of achieving ≥ 60% efficiency when compared to traditional power station/transmission setups with an optimum efficiency of 35%. SOFCs also have a high fuel flexibility, long-term stability, and are extremely cost-effective.
.jpg)
A simple schematic showing how a hydrogen-oxygen SOFC functions. Image credit: Mo-Sci Corp.
SOFCs have an operating temperature in the range of 500-1000 °C, which is considerably higher than traditional cells. This high operating temperature is the reason for their high efficiency, as it allows the use of relatively cheaper materials in the place of high-cost platinum catalysts. Their high operating temperature also results in A high energy density. However, developers need to address various technical challenges, especially for planer fuel cells, due to the energetic conditions caused by the high temperature.
The Problem with Conventional Glass Sealants
Like all other electrochemical systems that generate electricity through fuel oxidation SOFCs consist of a cathode, anode, and electrolytes. The integrity of the cell is protected by compartmentalizing these components. A sealant is required, but sealing cell compartments is a challenge for planar SOFCs due to their sandwich design and the high temperatures they are exposed to. Ordinary flat gasket seals are not suitable for this application due to creep and corrosion problems associated with the high-temperature and oxidation.
The variation in thermal expansion coefficients (CTE) between the compartments is another problem that results in thermal stresses and eventually causes the seal to crack. These drawbacks make ordinary glass sealants ineffective for use in SOFCs. Standard heat-resistant glass will experience cracks, even though they have adequate strength and insulating property. These cracks affect hermaticity, which defines the level of air tightness of each compartment. This has an impact on the cell’s electrochemistry and eventually causes cell failure.
Special Glass Sealants
The advent of novel glass sealants, such as glass-ceramic and viscous compliant glass seals effecitvely address this problem.
Glass-ceramic seals are widely used in the fuel cell and electronics industries. They are formed by applying and firing the glass at the interface between the individual components. A strong ceramic bond is formed between the components due to the crystallization of the glass upon firing. The likelihood of seal failure is more if the rate of expansion and contraction of the components is different, making it necessary to match the thermal expansion rates.
This issue is especially common in SOFCs where glass-ceramic seals are more likely to undergo thermal cracking, due to regular cycling between ambient temperature and temperatures of over 500 °C. Therefore, SOFCs that consist of a glass-ceramic seal will have a relatively short service life, due to the high probability for thermal cracking.
This short service life is the key barrier to the widespread adoption of SOFCs, in spite of their high efficiency. To address this problem extensive research is being carried out on the development and production of glass-ceramic seals with the necessary properties for use in SOFCs.
.jpg)
A schematic showing where MO-SCI's viscous sealing glasses are located in SOFC arrays. Image credit: Mo-Sci Corp.
Viscous compliant seals are a more effective alternative. The seals avoid crystallization meaning they stay in an amorphous glass state during their operation. This glassy behavior allows self-healing of the seal, which moves fluidly to occupy the gaps formed from cracking. This characteristic makes viscous glasses more suitable for SOFC applications, where thermal cycling is frequent. It also minimizes the need for a correct CTE match, as any gaps created by the expansion and contraction of components after heating and cooling are filled by the seal.
Research on Viscous Glass Seals
Mo-Sci Corporation, a company based in Missouri, has been involved in extensive research around the application of viscous glasses as SOFC seals. It has created glass capable of bonding to both ceramics and metals, with glass compositions customized to retain glassy behavior. Viscous glass seals remain vitreous even at high operating temperatures of more than 800 °C.
Promising results have been obtained from research commissioned by Mo-Sci Corp, and under the management of the U.S. National Energy Technology Laboratory (NETL). According to the results, the glass seals can heal cracks caused by thermal shock at temperatures in the range of 700-740 °C. The seals also showed superior longevity upon exposure to both dry and wet environments at 750 °C for more than 2000 hours without any significant weight loss.
Mo-Sci developed a new glass seal that has the ability to maintain a hermetic seal even after exposing to more than 148 thermal cycles for over 5000 hours. The temperature was cycled between 27 °C to 800 °C and the pressure was maintained constantly at 0.5 psid during each thermal cycle. These results are expected to transform SOFC technology as they demonstrate that viscous seals can deliver a reliable operation over an extended lifetime.
Download the Brochure on the Applications of Viscous Sealing Glasses
Mo-Sci is the sole developer of this technology and believes that its viscous sealing glasses will help to advance fuel cell-based near-zero emission coal plants. The energy landscape will be changed significantly if SOFCs are adopted into the wider energy industry. Also, SOFC sealing glasses are expected to have an impact on a variety of industries as they can be utilized in advanced electronic devices, novel solar cells, high-temperature sensors and in other applications where ceramic to ceramic or metal to ceramic sealing is required.
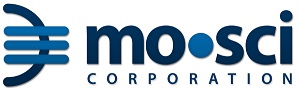
This information has been sourced, reviewed and adapted from materials provided by Mo-Sci Corp.
For more information on this source, please visit Mo-Sci Corp.