When purchasing a new thermal processing equipment, a company often spends months or even years of planning. Once it is bought and installed, the countdown begins. Degradation begins as soon as the equipment is switched on.
.jpg)
Figure 1. Equipment Failure Timeline.
Image Credit: Harper
Replacement Part Options
All technical equipment will fail and have to be repaired eventually. Equipment operators who were really happy are now wondering why the equipment is not functioning and when it will start functioning again. Generally, repair will include the replacement of dysfunctional or worn components.
The operator’s responsibility is to ensure that the thermal equipment is functioning correctly, as critical research and/or production is relying upon it. Therefore, decisions have to be made rapidly and efficiently. If the company’s technical staff are able to diagnose the problem and identify the components that need to be changed, the next query would be where to get those components.
In reality, the actual value is usually lost in a corporate world of three bids for every purchase. Original equipment manufacturer (OEM) components or other sources become a choice, and usually the option of aftermarket components or direct source components is made due to the actual purchase cost.
Aftermarket components are replicas that look like they possess the same function as those originally deployed. Direct source requires obtaining a component from an assembly and approaching the original manufacturer of that specific part. OEM components are those bought from the OEM and offer a much better value, which should be seriously considered.
Long-term reliability and cost efficiency can be improved by planning the purchase approach prior to the need. The manufacturer can offer technical support, history, the latest components, and a partnership of investment to reduce overall costs. It is planned to carry on this operation entirely, across the range of models for the sake of consistency.
The Bigger Picture
The beginning of the repair process involves diagnosing the issue and buying the replacement part, but there is much more to be done. When the replacement components arrive, they have to be installed, combined, modified and maintained. In most cases, a part is fundamental to the whole system, usually needing technical assistance for correct installation and commissioning.
The OEM knows the function of replacement components and also has the expertise regarding the right performance within the system as a whole. The technical support department of the OEM is able to provide access to engineers, original builders, and designers. Quality technical support simplifies installation and offers the assurance that the substituted components will operate properly when put into use.
An example to consider is a company that have chosen to buy a cheaper sensor from a vendor other than the OEM. For some time the sensor functioned as required and all looked well, but immediately deterioration started and gradually proceeded, leading to a failure over time. Though the sensor was replaced, failure happened almost immediately. The unit’s production had to be stopped for days until it was realised by the operators involved that a non-OEM component had been installed.
After the installation, the origin of the part had been forgotten and the personnel did not know of any proper installation methods. Finally, they opted to contact the original manufacturer and it was established that the component was not an OEM-supplied part. Soon afterwards an accurate replacement was provided with technical support, and the system was able to restart and function well. The customer was then provided with a plan to scale up the sensor system to the latest technology based on designs that the OEM was incorporating on the existing equipment.
When using a single-source OEM supplier, usage history is created and maintained. The history becomes useful in locating trends and estimating future preventative maintenance approaches. Furthermore, the OEM applies this historical data to make enhancements in future parts and equipment. The entire data can give wear predictions and cost analysis, and help in future troubleshooting. Regular feedback with the OEM will be integrated with their knowledge from other users of comparable equipment, enabling better precision. A vital spare parts strategy will have parts in stock when required, decreasing downtime and expediting charges.
Aftermarket part suppliers will provide lower cost according to copying components that have already been designed by an OEM. OEMs will carry on improving on design, perform research, and combine the better products into new version designs. Frequently, an OEM will suggest those modifications to the customer with current equipment during planning and discussions about replacement components.
The stability of components as they are replaced is preserved if bought through the single OEM supplier. At times, certain components may become obsolete during the equipment’s lifetime. If this occurs, the original manufacturer is the ideal choice as they can suggest a replacement that will match and not damage other system parts.
Developing a Partnership
The partnership between the OEM and the customer is very important. The OEM has additional benefits for working with suppliers on warranty and cost, as they generally procure such parts on a bigger scale compared to the individual user. This leverage can be used to the users own advantage and the OEM can help out with warranty claims.
Factory-trained technicians often have specific skill sets in order to support repairs, and the technician often carries out the functions as part of the manufacturing process. This is another point at which a total systematic understanding will be immensely beneficial. Unfortunately, all manufacturers do not stay in business. When this happens, it is advisable to contact a similar manufacturer who will provide assistance.
All businesses are constantly working towards increasing their bottom-line profits. One significant way to obtain this growth is to decrease the expenditure. Individuals responsible to maintain the system’s efficiency can experience a stressful situation when limited budgets are allocated for replacement parts and maintenance staff.
When being put to use, all parts begin to wear and they are further affected. This deterioration can be monitored with scheduled replacements when operating together with the manufacturer. Occurrence of a disastrous or partial failure can be reduced by replacing and repairing at planned intervals based on the time utilized or another quantifiable condition (Figure 2).
.jpg)
Figure 2. The risk of partial or catastrophic failure can be greatly reduced by replacing and repairing at scheduled intervals based on time used or other measurable conditions.
Image Credit: Harper
Individuals should spend sufficient time to research and select the manufacturer they will invest in to generate their capital equipment. Individuals will also benefit by buying both the parts required and the services needed from the selected OEM manufacturers.
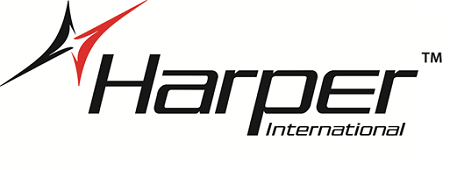
This information has been sourced, reviewed and adapted from materials provided by Harper International.
For more information on this source, please visit Harper International.