This article discusses a number of problems that can be solved simply with an understanding of flow behavior without having to perform calculations.
Given that most processes for shaping plastic and rubbers involve flow, it might be expected that rheological concepts are widely used in problem solving. However, in practice quantitative applications are limited to a certain extent, because of the fact that cooling often occurs while the melt is still flowing, the complex flow patterns involved in shaping operations (e.g. the filling of an injection mold), and the complex flow behavior of polymer melts.
Nevertheless, a qualitative understanding of flow behavior can help overcome processing problems.
Effect of Flow Channel Shape
Greater flow rates occur when the channel is circular than when it is in the form of a slit for a flow channel of a fixed cross-sectional area. The narrower the slit, even when the cross-sectional area is the same, the lower the flow rate, under a constant delivery pressure. This is a relevant difference if attempts are being made to extrude complex shapes, where the extruded cross-section includes components of different shapes and thicknesses.
Flow will tend to be faster through the round sections and slower through the bridging slit if, for instance, if the extrudate cross-section is in the form of a dumbbell with two almost spherical parts being bridged by a slit. This will result in stretching, and possibly tearing, of the central section of the extrudate.
Even greater problems may result when the extrudate cross-section resembles a half dumbbell, or key cross-section, with one circular section attached to a slit. In such a case, the extrudate will tend to curl up as it leaves the die.
Although such designs are best avoided, it is possible to solve the problem by lowering the parallel portion of the die in those regions where the flow is slowest (i.e., in the slit zones). Another effective way could be to throttle the flow in the regions where flow is fastest, by the inserting a mandrel or pin into the flow channel at the entrance to the die parallel.
Unbalanced Flow in Tubular Extrusion
The extrusion of polymer through the annular gap between an inserted mandrel or pin and the walls of a circular die results in tubing. At times it has been observed that the inside wall of the tube has a number of transverse ripples. These ripples result from variations in the flow velocity through the die in the radial direction.
In a simple rod die, the flow rate is zero, or almost zero, at the wall and highest in the center of the die. (With water and other such simple liquids, the velocity profile is parabolic in shape, while with polymer melts it is flatter to some extent). The velocity profile would not be considerably affected if one were to extrude over a very thin pin (of a thickness close to that of a thin piece of wire).
The flow rate of a short distance from the thin pin would be much greater than the flow rate of the same distance from the die wall. The difference will decrease as the diameter of the pin increases, but, to a greater or lesser extent, the flow rates will continue to be higher nearer to the pin than to the die wall.
As the melt comes out faster on the inside of the tube this will tend to cause buckling and hence rippling on the inside of the tube. This can be reduced by fitting a restrictor bulge or ring around the pin to slow down the flow in this region.
Uneven Die Swell
As a general rule, die swell decreases with the length of the die parallel and increases with shear rate. Extrusion of a complex section with different cross-sections will result in different shear rates that exist at the walls of the different cross-sections. The highest shear rates are seen where the cross-section is the least.
These differences can be compensated when performing die sizing. However, the die parallel at that cross-section may be reduced to compensate if it is found that swell at one point is lower than elsewhere. If this is done, the back end of the die parallel should be machined to make sure that all modifications in cross-section are gradual.
Die Swell and Parison Sag During Blow Molding
It is common to extrude a parison vertically downwards in extrusion blow molding. The tube diameters, while having a tendency to increase due to swell, will also tend to decrease as the parison sags under its own weight. Although the swell effect will be independent of parison length, when the tube length increases, the sag will also increase.
This can be compensated using a tapered die and pin, which move axially with respect to each other, to open the die gap during the extrusion of the parison. The parison pin movement may be programmed either with the use of theoretical data or as the result of trial and error experiments.
Extrudates Exhibiting Melt Fracture or Sharkskin
Surface defects on an extrudate are often found to have a regular pattern on the surface. With extrudates that have a large diameter, this is probably due to sharkskin. With smaller diameter products, this may be due to melt fracture. If the defects are transverse to the direction of flow, it could be a form of sharkskin. If the defects are helical in structure, then it is possibly melt fracture.
If the issue is identified as melt fracture, then the following possibilities have to be considered:
- Reduce output rate (not typically commercially desirable)
- Increase the melt temperature (raises cooling times)
- Increase the taper of the die entry
- Taper the ‘die parallel’ up to 10 degrees
- Use a polymer with lower molecular weight
If the issue is identified as sharkskin, then the following possibilities have to be considered:
- Decrease output rate
- Vary the die temperatures
Either decreasing or increasing the die body temperature may help, while additional heating of the die exit may be particularly advantageous.
Short Injection Moldings
Assuming that the injection stroke length has been properly set (so that the exact mass of material is provided to the mold), failure to fill the mold cavities is due to freezing of the polymer before the filling can be completed. Increasing the melt temperature will both lower the melt viscosity and extend the time taken for the melt to freeze.
However, if this happens a lot, the polymer may degrade or the cooling times may become very long. The mold temperature can be increased, but this may result in a long cooling time which is undesirable. An easier flowing grade can also be used, if such a material exists.
If that is not possible, it may be better to re-site the gate to reduce the length of flow path needed. There are computer programs designed to enhance gate positions and allow visualization of mold filling operations.
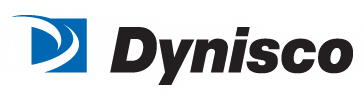
This information has been sourced, reviewed and adapted from materials provided by Dynisco.
For more information on this source, please visit Dynisco.