Unique expertise drawn from the domains of positive displacement blowers and screw-type compressors: this was the center for developing the new and innovative future technology that is the Delta Hybrid, the first range of rotary lobe compressors in the world
.jpg)
Image Credit: Aerzen
Delta Hybrid
Delta Hybrid is a synergy of blower and compressor technology that offers totally new opportunities for the generation of positive and negative pressure of air and neutral gases, owing to the design-based amalgamation of the benefits of both systems.
With a total of seven patents or patent applications, the Delta Hybrid is one of the most innovative products in the compressor technology category. For lower pressure ranges, the Roots Principle of isochoric compression is the first choice, while in higher pressure ranges, the screw-compression principle with internal compression is used.
The unit concept is based on Aerzen’s well-known and successful Delta range (Delta Blower and Delta Screw), but this has been additionally developed along systematic lines.
Versatility in Numbers
- Suction volume flow rates from 110 m3/h to 9.000 m3/h
- Overpressures up to 1,500 mbar
- Control range from 25 to 100%
- Nominal sizes DN 100 to DN 300
Applications
- Drinking water treatment
- Wastewater cleaning
- Ventilation of lakes, rivers and a lot more
Benefits
- Reduced life-cycle costs
- Amazing energy efficiency
- High levels of reliability, long service life
- Significantly increased range of application and pressures
- Processed air is 100% free of oil and absorbing material
- Reduced maintenance requirements
- Made by AERZEN
Technology
Two Profiles, One Packaged Unit
Delta Hybrid is the suitable synthesis of positive displacement blower and screw compressor. The advanced rotary lobe compressor uses two different rotor profiles in a single system: A twisted 3+3 blower profile, providing for lower pressure differences up to 800 mbar. Alongside that is a 3+4 compressor profile, built for higher pressures up to 1,500 mbar.
The outcome is a new level of cost efficiency for compressed air applications. Compared to positive displacement blowers, the processed air is moved diagonally via the stage. Here, conveying chambers are designed from the rotors and the walls of the housing. An important difference here is that, based on the rotor profile, internal compression and increased volumetric efficiency can be realized.
.jpg)
Specially designed 3+4 compressor profile with interior compression for lower pressure applications. Image Credit: Aerzen
.jpg)
3+3 blower profile with twisted shafts and patented pulse charging as well as lower crushing losses. Image Credit: Aerzen
Compression Principle of Twisted 3+3 Rotary Piston Profile (Delta Hybrid L)
Basically, the twisted rotary pistons use isochoric compression, similar to a straight positive displacement blower. This profile, along with the stage concept, utilizes physical effects to accomplish an energy advantage. The diagonal inflow of the medium, along with the flow-opening of the conveying chamber, decreases the recoil and thereby ensures that the blower stage is filled more efficiently. The so-called gas-dynamic shock is also utilized to attain a pre-compression of the medium in the conveying chamber. This boosts the volumetric efficiency of this blower.
ηV: Volumetric efficiency ηV= Q1/ Q0
Q0: Theoretical volume flow which is defined by the volume of the conveying chambers in the blower
Q1: Usable volume flow
If the usable volume flow is increased (for instance the blower stage is filled more efficiently) while the size of the conveying chamber remains the same, the volumetric efficiency is boosted.
Gas-Dynamic Shock
If a compressible medium that flows in an extending space (for example a pipeline) comes to an abrupt stop (for example - caused by a unexpectedly closing slide), an impulse occurs. This impulse moves backwards via the space from the position of the stop to the inlet (at a speed similar to that of sound). As the impulse moves, the medium behind the impulse is compressed. When the impulse reaches the inlet, the medium relaxes again.
However, if the space is closed at the inlet before the impulse can reach it, then internal compression occurs in this chamber. In this case, the degree of compression depends on the progress of the impulse in the space prior to the opening being closed. Assuming that in principle, the twisted rotary piston profile applies isochoric compression, the impact of the coupling performance can be shown using the following formula.
.jpg)
Image Credit: Aerzen
PK=Pth+ PV=Q0*(Δp +pV)
It is obvious; the pressure difference (Δp) has a direct impact on the coupling performance PK. The pressure difference can be easily described by the following formula:
Δp= p2-p1
As p1 does not vary with the gas-dynamic shock in the conveying chamber, i.e. it does not increase linearly, the pressure difference Δp is decreased, which causes a reduction of the coupling performance needed to convey the same volume flow.
The impact of internal compression on the power requirement becomes more evident for a screw profile.
Compression Principle 3+4 Screw Profile (Delta Hybrid S/H)
When a medium is compressed using a screw profile, then only marginal isochoric compression occurs. The majority of the necessary compression power is attained by internal compression. This signifies energy savings when compared to isochoric compression as the pressure ratio within the stage is predefined. If the internal pressure ratio matches the downstream system pressure, then this non-energy efficient isochoric compression would not take place. The process air is also transferred diagonally through the stage for the screw profile. The conveying chamber is also formed by the rotor profile and the stage housing.
The meshing of the rotors prevents a backflow between the rotors and thus fixes the conveying direction. The rotation movement of the screw moves the medium from the upper intake side to the opposing discharge side. As a result of the predefined size of the opening of this discharge side, the medium is pre-compressed to a specified pressure.
Based on the system pressure, this internal compression has a benefit over isochoric compression, in that it already transports the medium into the system at a predefined admission pressure. This means that the energy requirement that would otherwise have been used to act against the system pressure is not already partially (or, in an ideal case, completely) utilized in the stage. The result is lower power consumption.
.jpg)
Image Credit: Aerzen
These power savings using the p-V diagram can be illustrated as shown above. Assuming that the plane of this diagram matches to the required power consumption, isochoric compression (of a positive displacement blower) for a system pressure of 1 bar (ü) would require the power as illustrated by the plane created by the dotted line (----------). Here, there is internal precompression in the stage to 0.8 bar (ü). This internal compression needs less power, as the solid-line curve in the diagram reveals. The medium is transported into the system with an admission-pressure of 0.8 bar (ü).
This means only 0.2 bar (ü) is needed for isochoric compression. This is shown in the diagram by the violet rectangle (1). The difference between the planes for internal and isochoric compression signify the different power consumption levels needed to compress the same volume.
.jpg)
Image Credit: Aerzen
Characteristics of the Positive Displacement Blower
Approximately 90% of the life-cycle costs of a compressor are energy based. This figure signifies a challenge anywhere where environmental concerns and international competitiveness demand the use of all resource potential. But Aerzen is up to the challenge: they offer energy savings of up to 15% with an ROI that, based on volume flow and compression rates, can be recouped after two years. That is what the Delta Hybrid represents.
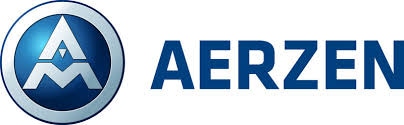
This information has been sourced, reviewed and adapted from materials provided by Aerzen Machines Ltd.
For more information on this source, please visit Aerzen Machines Ltd.