X-ray fluorescence is a particularly versatile tool as it can be used to examine the composition of materials, yet can also be used for measuring the thickness of very thin metallic coatings. X-Ray Fluorescence for Compositional Analysis In the former application, a high energy electron beam is directed at a target, usually tungsten, generating a broad spectrum of X-rays. The beam of X-rays is restricted to a narrow beam by passing through a collimator before going on to irradiate the sample under test. Each element, when irradiated, produces characteristic secondary radiation as orbiting electrons jump between the different energy levels, or shells, around the nucleus of the atom. This secondary radiation, or X-ray fluorescence, is analysed, giving details of the material under examination. X-Ray Fluorescence as a Method of Measuring Coating Thickness The latter application - examining a coating - is a little more complex. Here, the coating and the substrate material both produce X-ray fluorescence radiation, but the coating attenuates the substrate’s radiation. The degree of attenuation depends on the characteristics of the coating, particularly its thickness, so a correlation can be derived between the secondary emissions and the coating thickness. Difficulties in Measuring Coating Thickness There are other complications in examining coatings. Radiation from different electron shells often produce spectra that overlap with the main peaks, and there are also interactions between secondary emissions. In order to exclude unwanted and confusing secondary radiations, conventional thickness measuring X-ray instruments often use the ‘window’ method to eliminate unwanted peaks. Here, only a small part of the spectrum is analysed - that encompassed by the window. However, if the position of the window drifts or jitters, large errors can be introduced. Errors are also generated from the internal system components, such as the secondary emission detector, usually a proportional counter. These devices require very stable voltage supplies and can become saturated with excessive secondary radiation. Overcoming the Difficulties To improve accuracy many instruments use a solid-state pin diode as the detection device, which also improves the resolution. To improve accuracy further some instruments examine the whole spectrum, rather than just a portion of it. With this method the secondary characteristic peaks of elements can add to the information gained from a substrate or coating. Where the sample may be of unknown composition the use of the whole spectrum is a necessity. Standardless Measurement of Coating Thickness Until quite recently, using X-ray fluorescence to measure the thickness of coatings required an empirical approach, relying on thickness standards to calibrate instruments. A new approach, called fundamental parameter analysis, uses the basic characteristics of the substances being irradiated and has brought significant improvements in accuracy and removed the requirement for complex sets of standards. This technique is also applicable to energy dispersive spectrometers, so it has become possible to combine the two processes of energy dispersive spectrometry and X-ray fluorescence in one instrument. Hardware Configuration The physical architecture of a typical X-ray spectrometer is ideally as simple as possible. The unit may be required to measure a whole range of samples automatically so a programmable XY table is useful, and as samples may vary in size, a motorised Z-axis is often used to allow focusing onto difficult shapes. One such machine, from Fischer, figure 1, has both these additions, making measurements convenient and automatic. In this unit the X-ray generator and electronics are positioned above the sample with the beam projected downwards. The samples are also viewed through a video camera, operating like a reflex lens so that the exact size and location of the X-ray beam can be determined. 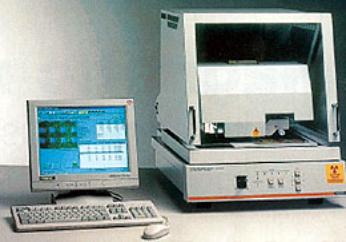 | Figure 1. An automated XRF set up. | Software The strength of any design depends enormously on the software it runs. The Fischer unit runs the latest generation of fundamental parameter X-ray software, version 6. This software allows the quantitative analysis of materials consisting of up to 24 elements (from aluminium to uranium) and, within a coating system of up to 24 individual layers, it can measure the thicknesses of each. Coating systems with five or more individual coatings - the individual coatings can even be made of alloys - can be measured foralloy composition. In addition, this software is capable of analysing the substrate material through the coating. Case Studies Electronics Industry Such nondestructive examination power lends itself to many applications - in the electronics industry the inspection of SMD components is a particularly complex task. Here, a unit would be required to measure and analyse several coatings of tin/lead alloys (solders) and silver/copper/lead alloys (conductivity pastes). In a typical quadruple coating system, figure 2, the first and the third coating (SnPb) are of similar type, while the conducting paste (Ag+Cu+Pb) also contains the element lead (Pb). The fact that the element nickel (second coating from top) is also contained in the ferrite substrate material is another, and in the past, significant problem. 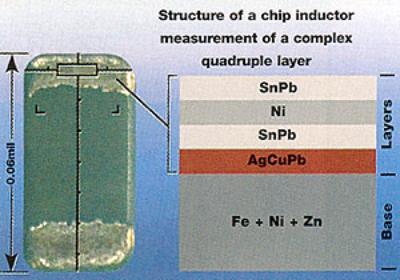 | Figure 2. A chip conductor with quadruple layer coating.. | The software in the Fischer machine is able to interpret the complex fluorescence spectrum as a quadruple coating and determine each layer’s thickness and composition. The results obtained from the spectrometer have been confirmed by examining a physical cross-section of the chip inductor. Jewellery Analysis The Fischer system has also been used in the jewellery industry. Typically in assay applications, the objective is to confirm coating thickness and to prove the purity of gold. Often, these coatings consist of alloys with various compositions of silver, gold, copper and possibly iron, cobalt and cadmium. It is possible to make a complete analysis of such materials and confirm the true value of the item. It is also possible to measure the very thin pure gold flash coatings that are just a few nanometres thick on the lower quality gold carat bases. Summary The combination of materials analysis and coating thickness measurement into a single spectrometer is a vital development for scientists and engineers involved in analysing complex structures. The perfection of fundamental parameter analysis software and the addition of solid-state detection devices has enabled the examination of alloy and multi-layer coatings. Electronic component manufacture and jewellery, two industries that have offered the most challenging scenarios to date, have both found that the innovative software and hardware offers an unparalleled solution. |