KLA has come out with a highly accurate scratch test which can yield a fount of valuable information regarding scratch hardness, mar resistance, coating adhesion, delamination of film, and failure modes, among other characteristics. This is a quantitative test mode which uses millimeter-scale movements to produce nanometer-scale measurements. This scratch testing option will be a desirable add-on to iNano and iMicro tests, and those who choose to use it will get a conical indenter (90º, R 5 µm), in addition to a test modality which is capable of autodetecting the critical threshold of load applied before film failure.
Materials and methods
Using a bulk polycarbonate sample, scratch testing was performed to give a quantitative assessment of its mar resistance. This included taking a baseline profile of the scratch vector, a profile before applying the scratch test, the scratch itself, another profile following the scratch, the last profile and one cross profile. The scratch was applied by a linearly progressing load up to 5 mN. The final profile was meant to quantify the width of the scratch produced and the height to which the material piled up following the scratch.
Results and discussion
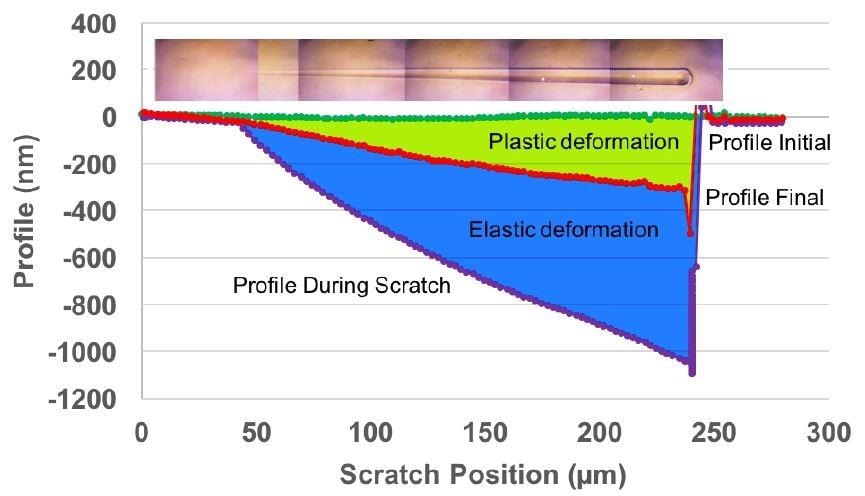
Figure 1. Scratch curves for polycarbonate. The green trace is the original morphology scan, the red trace is the residual deformation, and the purple trace is the scratch cycle. The insert is the micrograph of the full scratch length. All profiling was done at 5 μN.
The scratch application using a progressive load did not change the deformation characteristics in any drastic manner. The scratch was smooth over the whole length, whereas it became wider and deeper from beginning to end of the load application. The width was 4.7 µm and the height to which the pile-up occurred was 72.1 nm.
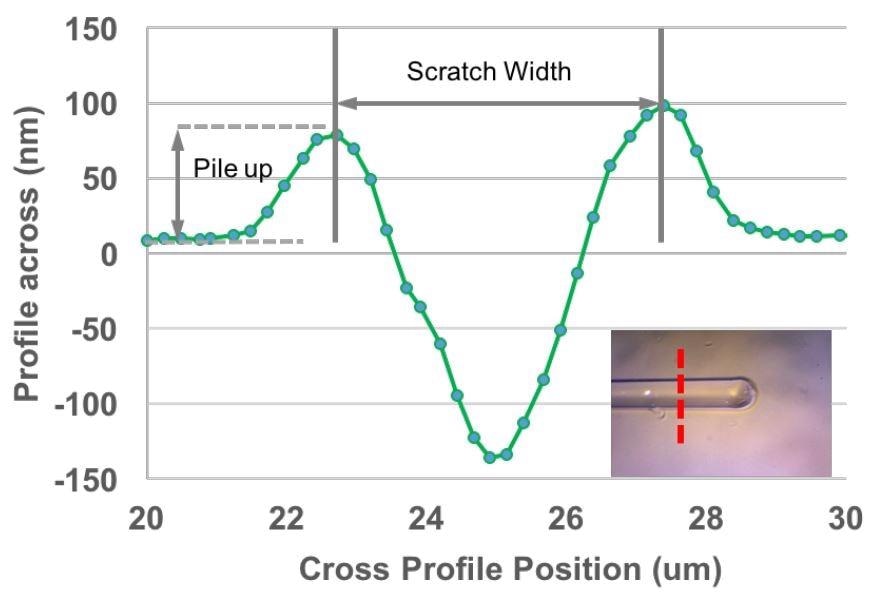
Figure 2. Profile across the scratch groove. Scratch width is defined as the peak-to-peak distance perpendicular to the scratch length. The insert shows the scratch at the location of the cross profile.
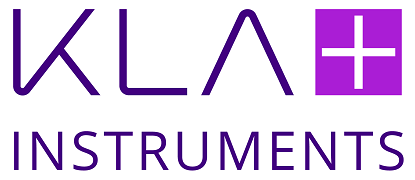
This information has been sourced, reviewed and adapted from materials provided by Nanomechanics, Inc., a KLA-Tencor company.
For more information on this source, please visit KLA.