Engineers within the fertilizer industry are all too aware of the toxic and combustible nature of ammonia. In 2013, a catastrophic nitrate explosion occurred in a fertilizer storage plant in the West Texas, USA, which took 15 lives through an explosive force of 7.5-10 tonnes of TNT. Improper handling and monitoring of ammonia can be a costly mistake.
Ammonia is a colorless and pungent smelling gas and is found naturally in trace amounts. However, ammonia is also lighter than air, and this means that it can form clouds and travel beyond the perimeters of a fertilizer plant if there is an accidental release. The problems can be further exacerbated if water is mixed in with ammonia clouds, because the cloud remains lower to the ground, posing a risk to the employees inside a plant.
Ammonia is used to produce fertilizers. It also used in pharmaceuticals, as a refrigerant in food processing operations and as cleaning agents. Industrial grade ammonia is usually supplied as anhydrous ammonia in tanks or as a liquid form. It is the anhydrous form that is used for fertilizers.
Fertilizer for agricultural applications is commonly produced using the Haber-Oswald process. This is done so using a combination of gas phase anhydrous ammonia and concentrated nitric acid, to produce ammonium nitrate. Upon mixing of the reagents, a chemical reaction occurs followed by a drying process to remove the excess water. Small beads, also known as prills, are created using an ammonium nitrate melt from a spray tower. For granules to be produced, the process requires spraying at tumbling in a drum.
Health and safety authorities around the world conclude that toxic exposure to ammonia (depending on the form and dose) can cause eye, nose and throat irritation, dyspnea, wheezing and chest pain, pulmonary edema, pink frothy sputum, skin burns, blistering and frostbite. The various regulatory controls put in place by governments to the exposure limits of ammonia at fertilizer (and other industrial) plants. Monitoring any ammonia gas leaks is a require safety feature, regardless of where it is used.
Detecting Ammonia
If being toxic wasn’t enough, ammonia is also combustible. Even though it is not highly flammable, contained ammonia is explosive under high heat. The lower explosive limit of ammonia is around 15%, with the upper limit being around 28%. The most common types of ammonia gas sensor are electrochemical, infrared, metal-oxide semiconductor (MOS) and charge-injection (CI).
.jpg)
Figure 1. Fertilizer plant exterior.
.jpg)
Figure 2. Senscient ELDSTM laser-based open path gas detector (OPGD).
Depending on the layout of the plant, it can be difficult to detect ammonia. A lot of fertilizer plants are crowded with machinery, so perimeter monitoring is an essential process to protect both the plant and surrounding community. For this, plant safety teams need a mixture of portable detectors that can be worn by employees, and fixed gas detection systems for 24/7 monitoring.
Fertilizer plant processes that require ammonia gas detectors include:
- Spray towers
- Plant perimeter monitoring
- Pumps and compressors
- Pipelines and valves
- Storage tanks
- Rail or truck loading and unloading
- Port shipping terminals
All ammonia gas detection sensors have pros and cons, but they all do a relatively efficient job, depending on the plant application, the environment, specific installation location, routine maintenance and staff competency. Depending on the sensor, problems can include saturated cells, calibration drift and dirty lenses – all of which need periodic attention.
The best safety practice in a plant is by using multiple sensors to detect ammonia. This includes both portable and fixed sensors to keep a track on the application needs and employee exposure. This enables a highly secure web of coverage, with some redundancy towards guarding people, equipment and facilities.
There are some gas detector problems that are shared by all types of gas sensor, not just ammonia detector. Common complaints from plant operators include short sensor life, sensor fouling and poisoning, the need for frequent sensor testing, regular cleaning and maintenance and regular replacement. Due to this, the safety industry is working continuously to improve existing gas sensor technologies and address these issues.
The Solution
To help fertilizer plants address the concerns of ammonia detection, MSA offers a new open path gas monitoring technology for use in multiple fertilizer plant process locations. This includes perimeter monitoring. This approach now provides the maximum level of protection for ammonia monitoring, alongside the highest service uptime and minimal maintenance.
Senscient ELDSTM gas detectors create a highly reliable detection perimeter around any fertilizer plant for the detection of ammonia – both in the plant and in the process areas. The technology behind ELDS open path gas detectors (OPDG) relies on enhanced laser diode spectroscopy (ELDS) to detect traces of ammonia. In the event of a gas leak occurring, the sensors technology recognizes and analyses.
During operation, some of the detectors laser light is continuously deflected through a gas sample of interest, which is contained in a reference cell. This ensures that the laser remains locked at the specific gas wavelength, e.g. for ammonia. Prior issues of interference gases in other detection technologies is no longer a problem. The detector patented harmonic fingerprint technology helps to ensure precise ammonia gas recognition, minimizing the risk of false alarms.
.jpg)
Figure 3. Harmonic Fingerprint ensures precise measurement.
False alarms are a major issue for many gas detection technologies. False alarms can cause plant downtime which then requires a combination of complex investigations and regulatory reporting. False alarms also lead to a lack of confidence from the employees if they happen frequently. This can breed a culture of apathy that may not take any swift measures if there is a real emergency.
Class 1 eye safe lasers in ELDS can penetrate thick fog, heavy rain and snow, which is beyond the capability of conventional open path infrared (OPIR) detectors. The daily automated SimuGasTM self-checking safety feature means that there is no need for the usual OPIR checks and recalibrations, that usually require the need for a qualified technician. ELDS is also target gas specific and possess no consumable sensing elements.
Fertilizer plant teams can appreciate that ELDS ammonia detectors are easy to install, commission and operate. They also feature Bluetooth wireless technology and advanced smart diagnostics. Using a combination of a mobile device and product specific software, the ELDS can be interrogated from a safe area. This is a useful feature for environments where safety harnesses or scaffolding may be necessary to prevent an employee from falling.
Processor engineers in fertilizer plants will find this detector to be an excellent choice for perimeter monitoring and other internal process applications. With a response time of 3 seconds, ELDS technology provides a quick response to the presence of gaseous ammonia compared to other detector technologies. ELDS gas detectors also feature separate receivers and transmitters, that are certified for use in explosive atmospheres and detect ammonia at distances from 5 to 120 meters.
ELDS gas detectors are made of high-grade corrosion resistant stainless steel which helps to ensure longevity in industrial scenarios. Unlike conventional point detectors, ammonia corrosion is less of a concern because the detector arrangement enables the components to be located away from the high ammonia concentrations near any potential leak source.
ELDS detectors are suited for both open and enclosed environments, including freezing winter temperatures and extremely high temperatures. Heated optics allow for use over a wide temperature range between -67 °F and 140 °F (-55 °C to 60 °C). ELDS detectors are also suitable for use in hazardous areas approved to CSA, UL, Class 1, ATEX, IECEx, EAC and INMETRO standards.
With the self-diagnostic SimuGas feature, ELDS detectors offer better installation and operational financial advantages against conventional fixed-point detectors. SimuGas also negates the need for ongoing costs from routine gas tests – a cost which can often exceed the initial cost of the gas detection instrument.
Even though the up-front cost of the open path detector may be more than conventional point gas detectors, the total cost of the whole installation is similar (or less expensive) once all of the fixed point devices (to cover a wide area) have been installed. For example, a 50-60 m path length will most likely require six individual point gas detectors to cover the same area, and provide the same monitoring effectiveness, as one ELDS detector.
ELDS detectors are also virtually maintenance-free. They possess no consumable parts, so there are no costs for replacing the sensing components, as well as the associated labor costs. These devices are calibrated for life and require no re-calibration. As such, ELDS detectors offer much reduced lifecycle costs compared to conventional point gas detectors.
Conclusion
Ammonia is both a toxic and combustible hazard for fertilizer plants in its gaseous form. When developing an ammonia safety plan, it is imperative that you have a reliable gas sensing technology that is effective across the various processing areas inside the plant, and the surrounding communities. Gas technologies are not always interchangeable due to the varying environments with the plant. You also need to make sure that you consider maintenance and reliability requirements, because in the long-term, the maintenance costs can exceed the initial cost of the detector.
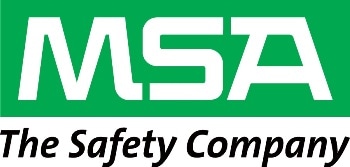
This information has been sourced, reviewed and adapted from materials provided by MSA - The Safety Company.
For more information on this source, please visit MSA - The Safety Company.