SiAlONs were developed as a more cost-effective substitute for hot pressed silicon nitride. They have a complex chemistry, and should be considered a family of alloys with a broad range of properties. SiAlONs are formed when silicon nitride (Si3N4), aluminium oxide (Al2O3) and aluminium nitride (AlN) react. The materials combine to form a wide range of chemical compositions.
.jpg)
Image Credits: shutterstock.com/Domagoj Burilovic
Fully dense polycrystalline bodies can be formed via pressureless sintering if sintering aids, such as yttrium oxide or magnesium oxide, are added to the compact. This innovative technique allows near net complex shaped components to be produced in a cost-effective way. The two most common crystalline phases formed in sialon ceramics are β-SiAlON and α SiAlON, where combinations of both phases can be incorporated into a single monolithic ceramic with compositions being developed to suit specific applications.
Key Properties
SiAlONs can exhibit the following properties:
- low density
- high strength
- superior resistance to thermal shock
- excellent wear resistance
- fracture toughness
- mechanical fatigue and creep resistance
- oxidation resistance
In comparison to hot-pressed silicon nitride, the very high temperature-resistance properties of SiAlON materials produced via pressureless sintering are limited by the glassy phases that form at grain boundaries during the sintering process. These materials are only suitable for long term use at temperatures < 1200 °C. Typical properties are outlined in Table 1.
Table 1. Typical Physical and Mechanical Properties of SiAlON (Syalon 101)
Property |
|
Density (g.cm-3) |
3.25 |
Young’s Modulus (GPa) |
288 |
Bend Strength (MPa) |
945 |
Fracture Toughness K1c (MPa.m 0.5) |
7.7 |
Hardness, (GPa) |
15.0 |
Thermal Expansion Coefficient (x 10-6/°C) |
3.04 |
Thermal Conductivity (W/m.K) |
28 |
Maximum Operating Temperature (°C) |
1200 |
Weibull Modulus |
11 |
β–SiAlON is built on the atomic arrangement existing in β–Si3N4. In this material, some Si is substituted by Al, with corresponding replacement of N by O. Subsequently, up to two–thirds of the silicon in β–Si3N4 can be replaced by Al without causing a structural change. The chemical replacement consists of exchanging Si–N bonds for Al–O bonds. The bond lengths are approximately the same for the two cases, but the Al–O bond strength is significantly higher than that of Si–N. In SiAlONs, the Al is co–ordinated as AlO4 and not as AlO6 as in alumina (Al2O3). Consequently, in β–SiAlON the bond strength is 50% stronger than in Al2O3. Thus SiAlONs intrinsically display superior properties than both Si3N4 and Al2O3. β-SiAlON grains have a long and needle-like, and orientate themselves randomly within the microstructure. This forms an interlocking structure of strong crystalline grains within the glassy-phase matrix, and is the reason for β-SiAlON ceramic’s high bend strength and toughness.
β–SiAlON is produced by International Syalons using and marketed under the trade name Syalon 101. During sintering at temperatures exceeding 1400 °C, the oxides react to form an oxynitride liquid with the sintering additives which is necessary for densification. This viscous liquid then forms an intergranular glass on cooling. Syalon 101 is a fully dense ceramic characterized by high strength and toughness.
.jpg)
Figure 1. Syalon 101 (β-SiAlON) microstructure (photo courtesy International Syalons Newcastle Ltd)
As a solid solution, the vapour pressure of β–SiAlON is lower than that of Si3N4, thus the SiAlON will form more liquid at a lower temperature with the presence of sintering additives. SiAlON is hence more easily densified using normal sintering techniques. Furthermore, it is significant that the lower vapour pressure of SiAlON reduces decomposition at high temperatures so that the SiAlON is more thermodynamically stable than Si3N4.
These β–SiAlONs are particularly useful in applications such as non–ferrous molten metal handling. During this process, thermal shock resistance and chemical stability when in contact with molten metals is critical for SiAlONs as components in thermocouple protection sheaths and in heater and riser tubes.
α–SiAlON
The second phase of SiAlON that is iso–structural with Si3N4 is α–SiAlON. The stacking structure in α–Si3N4 varies from β–Si3N4 in that the long 'channels' which run through the β structure are blocked periodically. This results in a series of interstitial holes. In α–SiAlONs, the Si in the tetrahedral structure is replaced by Al with limited substitution of N by O. To satisfy valency requirements, cations occupying the interstitial holes are modified. In this way, cations of elements such as yttrium (Y), calcium (Ca), lithium (Li) and neodymium (Nd) can be incorporated into the structure. In comparison to the needle-like grain morphology of β-SiAlON, α-SiAlON grains are small and equiaxed, which results in an intrinsically hard material. The high hardness can be attributed to both the grain structure and to the high bond energy density.
International Syalons are able to produce a SiAlON which contains both β–SiAlON and α–SiAlON grains under the trade name Syalon 050. During the sintering and subsequent heat treatment of Syalon 050, the intergranular phase is incorporated into the structure, producing a dense, hard ceramic with an almost absent grain boundary phase. This allows the material properties to be retained at up to 1400 °C. This is highly important in wear mechanisms; for example, hot hardness above 1000 °C is required for cutting tips.
.jpg)
Figure 2. Syalon 050 (α /β-SiAlON) microstructure (photo courtesy International Syalons Newcastle Ltd).
An additional, vital advantage of this material is oxidation resistance. The absence of a grain boundary phase in this ceramic results in restriction of the transport of diffusing species needed for oxidation to occur at higher temperatures. Simply, there is limited liquid phase to assist transport, leading to improved oxidation resistance. These SiAlONs also demonstrate substantial resistance to abrasive wear, and are being utilized as nozzles for shot blasting, particularly for highly aggressive grits. Furthermore, the absence of a grain boundary phase makes them attractive candidates for applications involving high temperatures, such as in gas turbines.
Composites SiAlONs
Due to their excellent sinterability, SiAlONs they can be made into composite ceramics, especially with other nitride ceramics. As such, International Syalons have developed a number of composite grades of SiAlONs.
The first, Syalon 501, is an electrically conductive grade based on β–SiAlON, which can be electro-discharge-machined into complex shapes. It demonstrates many of the outstanding properties of Syalon 101 and has found a niche in extrusion dies and die-pressing dies.
Syalon 110 is a composite, also based on Syalon 101, which demonstrates improved resistance to attack by steel and outstanding thermal shock resistance. It has found application as a break ring for the horizontal continuous casting of steel.
Applications
As with other silicon nitride based ceramics, SiAlONs are currently used for niche market applications. For example in:
Industrial Wear Applications
Metal Forming Tools
SiAlONs are also commonly used in metal wire drawing and tube forming tools for non-ferrous metals such as copper and aluminium alloys. In general, the material’s hardness, low coefficient of friction, and lack of adhesion or reaction have produced positive results.
.jpg)
Figure 3. Syalon 101 weld rolls (photo courtesy International Syalons Newcastle Ltd).
Wear components exploit the material’s low thermal conductivity, electrical insulation, and resistance to wear and thermal shock. Typical wear applications are fixtures for positioning and transferring metal parts during processes, such as induction heating or resistance welding (see Figure 1). For example, Syalon 101 is commonly used to produce location pins during the resistance welding of automotive components. In this case the Syalon 101 pin lasted a year, whereas the conventional hardened steel pin with an alumina sleeve lasted only 8 hours.
Syalon 101 and Syalon 050 are characterized by excellent mechanical strength and hardness, making them ideal candidates for many extreme industrial wear applications.
Shot Blast Nozzles
Shot blasting is a method for cleaning or preparation of surfaces. It involves blasting an abrasive grit such as sand, alumina or chill cast iron, at high velocities towards surface to be treated.
Traditionally, liners have been made from tungsten carbide. However, at the low angle of impact encountered in many blasting operations, tungsten carbide nozzles wear excessively due to the erosion of the relatively soft and ductile cobalt used to cement the carbide grains together.
Syalon 050 has a high hardness, fracture toughness and Young's modulus, resulting in excellent wear resistant properties. This makes it an ideal material for shot blast liners.
.jpg)
Figure 4. Syalon 050 shot blast nozzles (photo courtesy International Syalons Newcastle Ltd).
A standard 3/8" nozzle in Syalon 050, tested using chill–cast iron grit and operating at 100 psi, performed for more than 1000 hours without noticeable wear.
Milling Media
International Syalons produce a range of grinding media for the preparation of industrial and analytical samples.
In trials, weight losses for Syalon 101 bowls and media were approximately 14% of the reported weight losses for agate, alumina, zirconia and tungsten carbide. Consequently, contamination of the sample is substantially reduced, as well as extension the media life. Additionally, milling efficiencies for Syalon 101 are typically improved, resulting in reduced milling times.
Paper Dewatering Foils
During paper manufacturing, a section of the process involves removal of water from the fibre/water pulp. To achieve this, the pulp is spread over a fabric mat which travels over a series of suction boxes. These boxes apply a vacuum which draws the water out of the pulp as the fabric covers them.
The suction boxes consist of a series of foils, which can be many meters long. These foils can be formed from high density polyethylene (HDPE) or ceramic material. Ceramics are generally used in the high-speed applications. The foils are diamond-ground to produce a mirror finish, which is vital for the quality of finish of the paper.
Initially, alumina was the ceramic of choice. However, as machine speeds have increased, reaching up to 100km/min, the need for greater resistance to wear has emerged. It is here that Syalon 101 may be applied. Its excellent wear resistant properties, as well as thermal shock resistance, make it the ideal choice for modern high-speed applications.
Molten Metal Handling Applications
Leading manufacturers International Syalons produce three primary SiAlON components for molten metal handling, which are widely used in the aluminium industry:
- Thermocouple Protection Sheaths: Advanced ceramic tubes capable of precisely and reliably monitoring the temperature of aluminium foundries, with a choice of Syalon materials demonstrating outstanding physical properties at temperatures of up to 1200°C, and 1400°C
- Riser & Heater Tubes: High strength SiAlON ceramic cylindrical heaters used for heating the melt in aluminium processing. These can be built to a range of specified dimensions as required
- Level Sensors: Sensors used in the extrusion die casting of molten metals, including aluminium, into ingots or their final fit-for-purpose shapes. Temperature applications of SiAlON level sensors range up to 800 °C, ensuring accurate monitoring of molten aluminium in pressurized cavities
The durability of SiAlON components and their capacity for repeated use in aluminium production is instrumental in recycling processes. Aluminium displays exceptional corrosion resistance, allowing for technically unlimited recycling properties. Recycled aluminium is typically smelted into ingots, conforming to the ordinary aluminium refractory process. The ingots are then compounded into foundry alloys and shaped for a wide range of potential purposes using extrusion die apparatuses.
.jpg)
Figure 5. Cross-section of Syalon 101 thermocouple sheath after use in aluminium production, displaying zero porosity or ingress of molten metal into ceramic (photo courtesy International Syalons Newcastle Ltd).
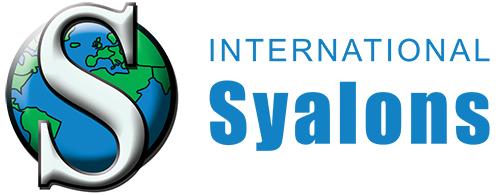
This information has been sourced, reviewed and adapted from materials provided by International Syalons.
For more information on this source, please visit International Syalons.