The electricity used in various chemical plants is obtained from a co-generation plant burning waste gas streams or from a natural gas power plant. In large boilers, such as the one shown in Figure 1, air and fuel are brought together by power plants (coal, oil, waste gas, or natural gas) for combustion, thereby producing heat which boils the water and generates steam. This steam runs through a turbine and spins it, producing electricity.
.jpg)
Figure 1. Typical boilers follow this process to generate electricity: Air and fuel are combined, combust and create heat, which then boils the water, creating steam. The steam causes a turbine to spin, generating electricity.
In such boiler applications, it is important to measure the flow energy — flows that cost money, such as steam, water, waste gas, and natural gas — to enhance energy efficiency, identifying waste, and reducing the emission of greenhouse gases into the atmosphere. Informed decisions can be made to enhance the energy efficiency only through accurate flow measurement.
Boiler Efficiency Considerations
How to choose the best flowmeter technology to measure the steam, water, and gas for boiler applications? Decision on the suitable flowmeters can be made based on the fluid being measured. Three primary applications are involved when enhancements to boiler efficiency are considered:
- Accurate measurement of inlet fuel (coal, oil, waste gas, or natural gas) and air for efficient combustion
- Measurement of inlet feed water for determining steam production efficiency and identifying waste
- Outlet steam production measurement
Increase Combustion with Optimal Fuel-To-Air Ratio
Combustion of inlet fuel (coal, oil, waste gas, or natural gas) and air is required for power generation. To ensure efficient combustion in the boilers, engineers should accurately measure the gas and air ratio. While too little gas will produce inadequate flame for boiling the water efficiently, too much gas is expensive, dangerous, and wasteful.
Orifice and Turbine Meters
Conventionally, a turbine or orifice meter is used for monitoring fuel gas to boiler units. Yet, these are not the ideal choice for measuring devices for this application since both require regular skilled maintenance to ensure reliable and accurate measurement as they are prone to failure.
Engineers could also be worried by constrained piping conditions. For instance, to negate the impact of flow disturbances, 10 to 50 diameters of upstream piping are required for an orifice meter. Since it is hard to find long straight pipe runs, majority of the flow measurement systems are detrimentally impacted by differing flow profiles within the pipe.
However, a major source of concern is that turbine and orifice meters measure volumetric flow. Hence, to infer or calculate mass flow, additional temperature, pressure, and differential pressure sensors, along with a flow computer, are required (Figure 2). Apart from degrading the accuracy of flow measurement, this kind of compensated measurement leads to additional installation and maintenance costs, thereby increasing the cost of ownership.
.jpg)
Figure 2. This is a typical differential pressure flow meter set-up with additional pressure, temperature, and differential sensors to infer mass flow.
Thermal Mass Flowmeters
On the other hand, thermal mass flowmeters can be used only for the direct measurement of mass flow of gases, and not volumetric flow. Since thermal mass flowmeters count the gas molecules, they are not affected by variations in inlet pressure and temperature and can directly measure mass flow without compensation. The performance of thermal flowmeters is optimal in inlet gas and air flow boiler applications since the optimal fuel-to-air ratio to ensure efficient combustion in boilers is not computed on a volumetric basis but based on mass (Figure 3).
.jpg)
Figure 3. This diagram demonstrates direct mass flow measurement using thermal mass flowmeters.
In the most simple working configuration of a thermal flowmeter, the fluid flows through a heated thermal sensor and a temperature sensor. When molecules in the fluid flow through the heated thermal sensor, the flowing fluid absorbs the heat. The thermal sensor is cooled down, and the temperature sensor continuously measures the comparatively constant temperature of the flowing fluid. The thermal characteristics and flow rate of the fluid govern the amount of heat lost. Hence, the flow rate can be determined by measuring the temperature difference between the temperature and thermal sensors (Figure 4).
.jpg)
Figure 4. A thermal flowmeter determines flowrate by measuring the temperature difference between the thermal and temperature sensors.
Innovative advancements in four-sensor thermal technology in combination with stable “dry sense” sensor technology and sophisticated thermodynamic modeling algorithms allow certain thermal flowmeters to achieve a reading accuracy of ±0.5%, competing with the accuracy of Coriolis flowmeter at a lower cost. In-situ validation, gas-mixing capability, and dial-a-pipe can also be realized through on-board software apps.
Measure Inlet Feed Water Accurately
Apart from being a limited resource, water is also a high-cost flow energy. In the case of boiler applications, accurate measurement of the inlet feed water flow to the boiler is important since the efficiency at which the boiler converts this feed water into steam must be measured (Figure 1).
Clamp-on Ultrasonic Flowmeters
Although a volumetric vortex flowmeter can be used to measure inlet water, it is best to use clamp-on ultrasonic flowmeters for water flow applications as they are easy to use and have better application flexibility. In addition to realizing high accuracy at low and high flows, they save time with no process shutdown or pipe cutting and are not influenced by external noise (Figure 5). At present, developments in ultrasonic technology include on-board apps and software that enable easy installation of the meter, giving a visual signal indicating correct installation.
.jpg)
Figure 5. Ease of use and flexibility make clamp-on ultrasonic flowmeters suitable for water and liquid flow applications, and easy to install.
Optimize Steam Production
It is important to accurately measure the steam from the boiler to determine whether the boiler is generating the expected amount of steam or has to be tweaked for improved efficiency (Figure 1). Conventionally, a differential pressure device, typically an orifice plate, has been used to measure the steam flow.
Yet, such devices intrinsically perform volumetric flow measurements. The mass flow rate of steam changes with variations in temperature and pressure. A “small” change in steam pressure of even 10% will lead to a 10% error in non-compensated mass flow. This indicates that in the case of a typical differential pressure measurement installation, it is important to compensate for the volumetric flow rate by measuring pressure and temperature. Then, these three measurements (P, ΔP, and T) are combined with a flow computer to compute the mass flow.
Insertion Multivariable Vortex Flowmeters
Insertion multivariable vortex flowmeters have the ability to accurately measure steam output produced from boilers. Mass flow rate, volumetric flow rate, temperature, fluid density, and pressure can be simultaneously measured by using one insertion vortex flowmeter in combination with one process connection. Since the density of saturated steam differs with pressure or temperature, and superheated steam varies with pressure and temperature, multivariable vortex flowmeters ensure that the density calculations of the flowmeter, and in turn the mass steam flow measurements, are accurate.
The steam accuracy provided by multivariable vortex flowmeters is ±1% of reading; they also provide pressure and temperature compensation, as well as 30:1 turndown. Moreover, sensor advancements and recent technology take external vibration into account, thereby enhancing low flow measurement and rendering the vortex flowmeter more accurate. Innovative on-board software apps also enable in-situ calibration validation, easy setup, troubleshooting, tuning, and data logging.
Case Study: Thermal Flowmeters Improve Boiler Efficiency at a Purified Terephthalic Acid Chemical Plant in China
Purified terephthalic acid (PTA), which is the precursor to polyethylene terephthalate (PET), is a ubiquitous material used across the globe in textiles, plastic bottles, and other products. In China, a PTA chemical plant produced steam and electricity from its on-site power plant employing coal as the fuel. It also included a wastewater treatment station that synthesized methane, which was then burnt. Both these processes emit large amounts of greenhouse gases.
New government regulations mandated that the company should reduce its CO2 emissions. Decisions were made by the plant to alter its four boilers to burn coal as well as the waste gas (methane) flared off earlier. The savings in coal per year were estimated to be approximately 0.5 million dollars. Engineers of the plant worked with a single-source supplier to rework the designs of the boilers and installed Sierra Instruments’ industrial insertion thermal flowmeters for measuring its combustion air and waste gas fuel, assuring optimal combustion (Figure 6).
.jpg)
Figure 6. Sierra Instruments’ Steel-Mass 640S thermal mass flowmeter was installed at a PTA chemical plant in China to measure methane waste gas.
While one thermal flowmeter measured the flow of waste gas, the other four thermal flowmeters carry out sub-metering of the gas stream to each boiler. Four other meters carry out measurement of the pre-heated (200 °C, 392 °F) combustion air to each boiler, enabling the boiler control system to improve the fuel-to-air ratio. Apart from providing precision flow data to ensure compliance with government regulations, the Sierra flowmeters helped the company minimize waste while improving efficiency.
Following are the other potential metering applications under scrutiny:
- Feed water to the boilers with the help of clamp-on ultrasonic flow: Since this is a pre-existing feed piping system, a clamp-on ultrasonic meter would be a flexible solution.
- Measurement of steam flow: Measuring steam flow from the boilers to the turbine generator and sub-metering to the other plant processes.
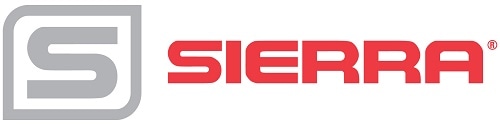
This information has been sourced, reviewed and adapted from materials provided by Sierra Instruments.
For more information on this source, please visit Sierra Instruments.