Quality and reliability are essential for the pharmaceutical industry. This is especially the case with the manufacturing and application of pharmaceutically active substances and excipients.
The objective here is twofold. Firstly, substances must be safely handled at all times in order to protect the operating personnel; and secondly, products must be faultless and have appropriate quality concepts built into the product and its process development. This is commonly known as Quality by Design.
Process Analytical Technology (PAT)
A core aspect of this concept is the Process Analytical Technology (PAT) initiative developed by the US Food and Drug Administration (USFDA). The USFDA carefully manages and monitors these production processes, from the intermediate products right through to the completion of the final product. This is done using a range of in-process control measures.
In order for these control measures to be effective, critical process parameters (CPP) must be measured promptly. This is achieved by using the right systems for analyzing and controlling production processes. These parameters influence the critical quality attributes (CQA) for both source and in-process materials so it is essential that they are managed appropriately.
To demonstrate this concept within a practical example: a commonly used process step during the manufacturing of the finely dispersed active ingredient powder used within solid dosage forms is air jet grinding in the kilo lab.
This process requires suitable online analysis and without this, the grinding process would need to be analyzed on a regular basis (by manually removing samples and taking these to a lab to be analyzed), causing interruption in the process and lowering throughput and efficiency.
Online Particle Size Analysis
However, using online particle size analysis it is possible to provide real-time monitoring of the grinding level with no need to interrupt the grinding process. This also ensures that the active substance can remain fully contained, reducing any risk to operators.
By using appropriate sampling systems such as probes or TWISTER, it is possible to retrieve minimal but still representative product quantities directly from the process before discharging them on the MYTOS laser diffraction sensor.
The MYTOS system can be also operated operated in a bypass line to the main process stream and is supplied with product samples from the product stream via a sampling system. A multiplex installation, in which multiple sampling points are connected to just one sensor, can also be implemented. The precision vibratory feeder VIBRI can be used as the interface for transferring the process sample; with a uniform, regulated product supply it guarantees the optimum sample concentration in the measuring zone of the MYTOS system.
.jpg)
Laser diffraction sensor MYTOS for process-related on-line installations in a mobile rack
Vital Grinding Parameters
Not only that, but online monitoring can provide real-time, reliable results for particle size distribution. Vital grinding parameters like quantity, form and classifier speed can be optimized and adjusted during the operation, and because the active ingredient can remain in a closed system throughout the whole process, risks of contamination can be avoided during the analysis.
.png)
Online measurement with MYTOS & TWISTER for targeted air jet grinding of lactose | Achieving the desired particle size distribution (x10 < 4 microns, x50 = 8 microns, x90 > 14 microns) within 20 minutes after two adjustments
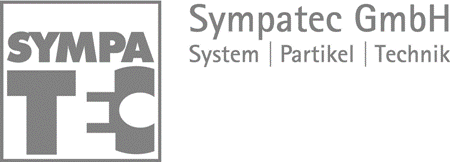
This information has been sourced, reviewed and adapted from materials provided by Sympatec GmbH.
For more information on this source, please visit Sympatec GmbH.