Moldables and refractory cement are very important for many industries. In the construction of large ovens and furnaces, where refractory linings or high-temperature firebricks are present, castable refractory cement is crucial. These are usually made up of specialized aggregate materials and thermally resistant clinker and are critical to thermodynamic stability in the heating chamber or in components that are subject to significant thermal stress.
Solids contract and expand during temperature change, especially metals, which are excellent thermal conductors. Cements which are utilized to adhere structural metals together in refractory applications need to keep their structural integrity when heat stress is present. To reduce the risk of mechanical failure during thermal expansion and contraction, refractory cement uses binding materials with enhanced thermodynamic properties. Fused minerals like alumina or aluminum oxide are employed to bind coarse aggregate materials and supply superior temperature resistant properties without compromising structure.
Aluminum Industry
Refractory material is employed as the lining of ladles, furnaces, or any crucibles in the aluminum industry, where molten metal is deposited until further processing is carried out. Refractories need to withstand extremely high temperatures and shield the container from the corrosive nature of the molten metal and the flux/slag. They also help to keep the temperature that is required inside the ladle because of their thermal properties.
Due to advancements in installation techniques, aluminosilicate-based low cement castables are now used extensively in the aluminum industry for refractory linings in melting and holding furnaces, and their utilization has become more commonplace. Refractory cement has to play the triple role of protection against corrosion, providing mechanical strength, and thermal insulation when used for aluminum manufacture.
Applications in the aluminum industry can include coatings for furnace linings, trough and ladle coatings, molten aluminum splash shield protection, burners and molds, troughs, and linings for molten aluminum transfer, high-temperature patching and sealing of refractory linings, lightweight refractory linings and induction furnace coil coating.
Protection Against Corrosion
An important consideration is the durability of materials, including both ceramics and metals which are exposed to molten aluminum.
This is because molten aluminum is an aggressive metal to a number of materials. Examples of processes where this is critical are molten metal containment, die-casting, and semi-solid processing. Molten aluminum can produce considerable corrosion of the container and handling materials resulting in an unpredictable lifetime.
In the aluminum industry, refractory performance against corrosion is an important factor which affects the standard of metal created and the durability of furnace lining. Corrosion of refractory materials during the casting process for aluminum alloys increases the overall cost of production. Choosing an appropriate refractory composition for Al-casting applications takes comprehensive characterization of the physical, chemical, and mechanical properties of the materials.
Improving Refractory Materials
By using three components; microsilica, calcium aluminate cement, and reactive alumina, bonding in low cement castables is accomplished. These have a strong influence on their corrosion behavior with molten aluminum as well as the mechanical and physical properties of the castables. Cement is a critical component and its content is between 5 and 8%. Typically, calcium aluminate phases are a mixture of calcium dialuminate and calcium monoaluminate.
Increasing the volume of cement also increases the amount of calcium aluminosilicates formed, which normally reduces the amount of free silica, and also improves the corrosion resistance of castables in contact with molten aluminum. The lime/silica ratio drastically impacts the liquid phase formation at high temperatures and so affects both the mechanical properties such as hot strength and creep resistance, and also the corrosion behavior.
Yet, cement phases are believed to be the starting point for corrosion, as they have been seen to be susceptible to molten metal attack. The higher the water necessity of these castables, the lower the density, which increases the porosity of the refractory matrix.
Reducing Cement Content and Adding Microsilica
Due to cement use, an increased porosity of castables has meant low (LCC), ultra-low (ULCC) and zero cement castables (ZCC) being created. Low cement castables contain greater amounts of fine/ultra-fine particles which results in improved densification and so better mechanical properties, although they possess higher porosity.
Microsilica is largely utilized as filler in refractory materials, especially in castables. This is because the particles are an amorphous form of silica and have an average size of 0.15 microns. Due to the small particle size, microsilica can decrease the cement content of refractory castables. It can also decrease the open porosity from about 20-30% to 8-16% and the drop in mechanical strength.
So, microsilica is added to alumina-based refractories to enhance the mechanical properties at lower cost. Yet, microsilica is thought to improve the flow behavior of castables through the formation of low melting liquid calcium aluminosilicate phases. This means the properties of castables containing microsilica are hugely influenced by the CaO content present in the composition.
Microsilica can also react with water and cement to create zeolite CaO-Al2O3-SiO2-H2O hydrated phases, which have an effect on castable surface porosity. Any silica in the castable that is free will be reduced by molten aluminum to form corundum, which is where the corrosion process begins. The presence of silica is not beneficial for use in the application of aluminum melting, because of its low chemical resistance to aluminum attack. Refractory cements also contain non-wetting agents to enhance the corrosion resistance of aluminosilicates. The most common additives are AlF3, BaSO4, and CaF2.
To reduce the surface tension and viscosity of the molten metal, alloying metals such as Mg and Zn can be added to molten aluminum. Resulting in an increase in penetration of molten aluminum into refractory material pores. Magnesium is a major cause of corundum development, which is the main cause of aluminosilicate refractory corrosion by molten aluminum.
.jpg)
.jpg)
.jpg)
Image Credit: Mid-Mountain Materials, Inc.
THERMOSEAL® Refractory Cement
Mid-Mountain Materials utilize three distinct refractory cements for thermal insulation and refractory adhesion applications. These have been optimized to withstand thermal contraction and expansion and to allow resistance to erosive media and secure adhesion of gaskets and seals in industrial furnaces.
The THERMOSEAL® range has temperature resistant properties of up to 1095 °C (2000 °F) (THERMOSEAL® 2000) and varied consistencies which depend on the application needs. THERMOSEAL® 1000/1000SF is a high-temperature cement, with a fibrous consistency, and a continuous use limit of 538 °C (1000 °F).
This has been formulated carefully to withstand thermal contraction and expansion under fluctuating heat conditions. There is also a range of moldable coatings and materials which incorporate the latest refractory technology to resist corrosion and expansion in aluminum processing.
References
- Firoozjaei, E. A., Saidi, A., Monshi, A., & Koshy, P. (2010). The effect of microsilica and refractory cement content on the properties of andalusite based Low Cement Castables used in aluminum casthouse. Cerâmica, 56(340), 411-421
- M. Yan and Z. Fan, Review: Durability of materials in molten aluminum alloys, Journal of Materials Science 36 (2001) 285 – 295
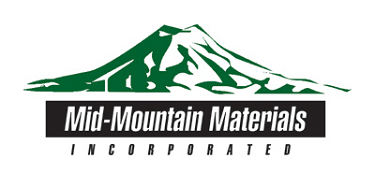
This information has been sourced, reviewed and adapted from materials provided by Mid-Mountain Materials, Inc.
For more information on this source, please visit Mid-Mountain Materials, Inc.