Pressure spikes, i.e. pressure overloads that take place over a short timespan, happen in many transducers in fluid power systems. If these spikes are particularly strong they can result in a permanent, positive zero shift in the transducer’s signal output.
Following extended research into pressure spikes Dynisco designed a method of determining the extent of the pressure spike that caused a field failure. This research found that pressure spikes can occur at pressures that far exceed the standard pressure of a system.
Dynisco found that two transducers, which Dynisco received back from one of their customers, had undergone pressure spikes reaching peaks of 19,500 and 21,500 psi. These values were so much higher than the operating pressures that their customers found them hard to believe. The transducers in question used a cushioned hydraulic ram, had functioning relief valves and had a working pressure of just 1,350 psi.
It appeared that the conclusion that the pressure spikes were around 15 times greater than the systems operating pressure defied all logic.
To solve this issue Dynisco used a disk recorder and digital storage oscilloscope to test the hydraulic machinery in the die casting systems that had experienced transducer failure. The recording triggered automatically and provided a measurement resolution of 0.5 us/point.
The recordings showed that the pressure spikes ranged between magnitudes of 5,500 to greater than 20,000 psi, this was all for a working pressure of 1,250 – 1,350 psi.
Dynisco ran similar experiments for injection molding systems at Massachusett’s University of Lowell. Here, spikes of between 4 x to 20 x more than the operating pressure were experienced, depending on which region of the machine’s hydraulics the measurement took place in. In these tests the pulse width was around 0.25 ms – the same value as the dye casting systems.
Experimental Conclusions
The data collected from these experiments, and further tests carried out 6 months later, allowed the following conclusions to be made:
- If air is trapped in the hydraulic fluid it can result in stronger pressure spikes. It was found that purging air from hydraulic fluids can reduce spikes by up to 60%.
- Hydraulic systems can be subject to pressure spikes, with the largest spikes occurring as a result of rapid changes in the flow of the fluid. These changes can be the result of pistons, rams, valves, pumps and control systems.
- The typical pulse duration of a pressure spike is around 0.25 ms – this is too rapid for most safety valves and other forms of pressure relief to respond.
- It is possible for pressure spikes greater than 20,000 psi to occur in systems which have a working pressure of just 1,300 psi.
- The extent of the pressure spike is location dependent.
- Pressure snubbers can be used to limit the magnitude of the spike that the transducer experiences by absorbing pulses and shocks.
Recommendations
The following steps should be taken for the selection, installation and protection of transducers in systems that experience pressure spikes.
- Bleed air from a hydraulic system before startup
- Where possible, transducers should not be installed at the end of long, straight pipe runs
- Transducers with the greatest pressure range that is practical should be chosen to replace transducers which have been damaged by a pressure spike. E.g., a 2,500 psi transducer which has been damaged should be replaced by a 3,000 or 5,000 psi version.
- The smallest possible length of piping should be used to connect the transducer to the point of pressure measurement. If ram inlet pressure is being measured the transducer should be installed as close as possible to the ram inlet.
- A correctly sized pressure snubber should be installed either near to or at the transducer to protect it against spikes in pressure.
- The most damaging spikes are generated by rapid change in system flow rate. Pressure rise can be extremely high if fast-acting solenoid valves stop flow. If possible, slow valve closure rates to reduce or even eliminate the shock pulse. This applies to all fast-acting flow controls.
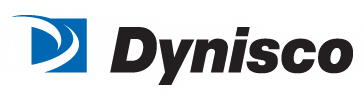
This information has been sourced, reviewed and adapted from materials provided by Dynisco.
For more information on this source, please visit Dynisco.