Fine powders and granular materials are extensively used in industrial applications. To control and to optimize processing techniques, it is necessary for these materials to be characterized accurately. The characterization techniques are either associated with the properties of the grains (such as chemical composition, granulometry, morphology, etc.) or with the behavior of the bulk powder (such as density, flowability, electrostatic properties, blend stability, etc.).
However, with regards to the physical behavior of bulk powder, the majority of the methods used in R&D or quality control laboratories are based on traditional measurement methods. During the past 10 years, Granutools has updated these methods to fulfill the current demands of R&D laboratories and production departments. Particularly, the measurement processes have been automatized and stringent initialization techniques have been developed to achieve reproducible and interpretable outcomes. Furthermore, the use of image analysis methods enhances the measurement precision.
In SLM (Selective Laser Melting), EBM (Electron Beam Melting), and SLS (Selective Laser Sintering techniques), consecutive thin layers of powders are produced with a rotating cylinder or with a ruler. Each layer is partially melted or sintered with an energy beam (electron or laser beam). The vertical resolution is defined by the layer thickness. Therefore, a thin layer results in a better resolution.
In order to achieve this effect, the powder is made as fine as possible. Unfortunately, as the grain size reduces, the flowability decreases and the cohesiveness increases. Furthermore, the powder becomes increasingly sensitive to moisture. Thus, it is necessary to find a compromise between grains size and flowability. The quality of the part developed with Additive Manufacturing (AM) is in direct relation with the powder flowing properties. The flowability should be adequately good to achieve homogeneous successive powder layers.
Various recent publications have proved that the traditional flowmeters do not have the ability to offer relevant information about powder flow behavior in powder-bed-based AM. In shear cell tested and standard rheometers, the existence of a compressive load is not compatible with the free surface flow employed in AM devices.
However, the measurement method based on the rotating drum is an excellent candidate since the powder flow is analyzed accurately at the powder/air interface with no need for compressive load. Furthermore, the rotating drum geometry enables investigating the natural aeration of the powder during the flow.
This article shows that the probability to obtain waves during the layer formation is proportional to the cohesive index computed by the GranuDrum instrument. In addition, it can estimate the optimal ruler (recoater) speed to obtain a homogeneous layer.
GranuDrum
GranuDrum instrument is an automated powder flowability measurement technique that is based on the principle of a rotating drum. The powder sample is half filled in a horizontal cylinder with transparent sidewalls, known as the drum. The drum rotates around its axis at an angular velocity varying between 2 and 60 rpm. A CCD camera takes pictures (30 to 100 images separated by 1 second) for each angular velocity.
The air/powder interface is identified in each picture using an edge detection algorithm. Later, the average interface position and the fluctuations around this average position are calculated. Then, for each rotating speed, the flowing angle (also known as the “dynamic angle of repose”) αf is calculated from the average interface position and the dynamic cohesive index σf is computed from the interface fluctuations.
Generally, a low value of the flowing angle αf denotes a good flowability. A broad set of parameters influences the flowing angle: the shape of the grains, the cohesive forces (van der Waals, electrostatic, and capillary forces) between the grains, and the friction between the grains. The dynamic cohesive index σf determines the cohesive forces between the grains. A cohesive powder results in an irregular flow, while a non-cohesive powder results in a regular flow. Therefore, a dynamic cohesive index near to zero corresponds to a non-cohesive powder. The increase in powder cohesiveness results in an increase of the cohesive index.
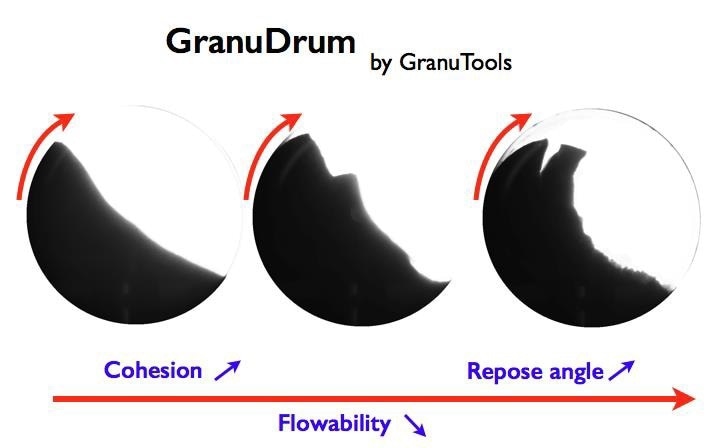
GranuDrum not only enables the measurement of the cohesive index (CI) and the flowing angle αf as a function of the rotating speed but also enables measurement of the first avalanche angle and the powder aeration during the flow.
Determination of Powders Spreadability
Powders Descriptions
For this article, four titanium powders were chosen. They have various sizes and shapes (cf. Figure 1 and Figure 2, Yablokova et al., 2015) and they are called TNZ-1, TiNb-1, Ref-Ti, and NiTi-1.
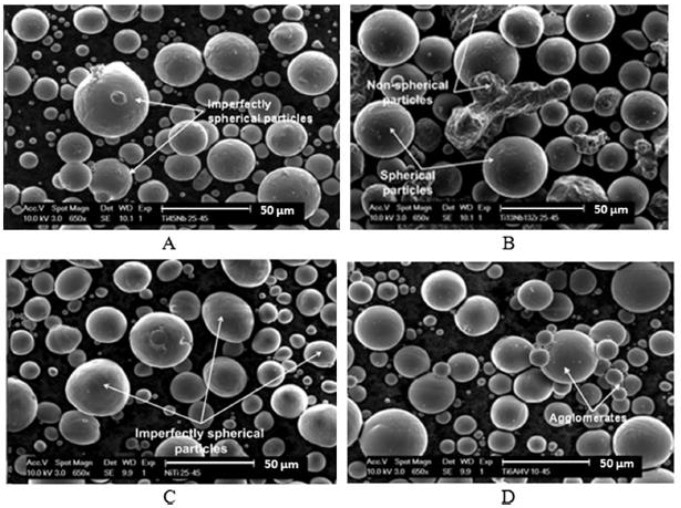
Figure 1. SEM pictures of 25–45 µm fraction powders: (A) TiNb-1, (B) TNZ-1, (C) NiTi-1, and (D) Ref-Ti at magnification 650×.

Figure 2. SEM pictures of 25–45 µm fraction powders: (A) TiNb-1, (B) TNZ-1, (C) NiTi-1, and (D) Ref-Ti at magnification 3500×.
These powders were particularly chosen since two of them have bad spreadability for a recoater process (TiNb-1 and NiTi-1), hence the developed powders layer is not homogeneous (with irregularities and waves, cf. Figure 3 A). However, after the recoater operation, TNZ-1 and Ref-Ti form a flat surface without any irregularities (i.e., with good processability, that is, spreadability, cf. Figure 3 B).
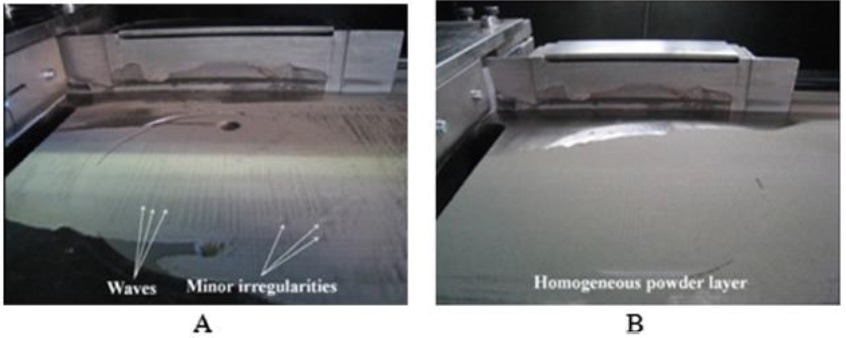
Figure 3. Deposition of the first powder layer on the SLM building platform of (A) NiTi-1 /TiNb-1 and (B) TNZ-1 / Ref- Ti powders.
GranuDrum Analysis
The GranuDrum instrument was used to test these powders. The results demonstrate the evolution of the cohesive index computed using the rotating drum technique as a function of the rotating speed. The measurements have been conducted with an increasing rotating speed ranging from 2 to 20 rpm.
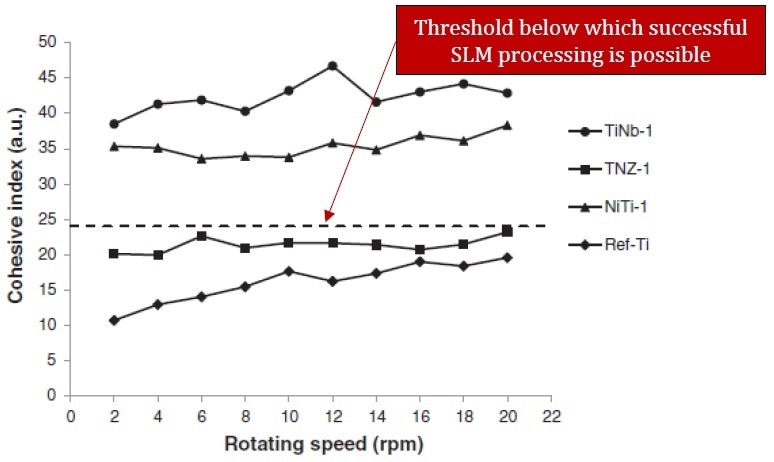
Figure 4. Evolution of the cohesive index versus rotating speed for TiNb, TNZ, NiTi and Ref-Ti powders.
From Figure 4, two different rheological behaviors can be emphasized — NiTi-1 and TiNb-1 have a high cohesive index, and therefore, they have low processability (forming non-homogeneous powder layer). However, TNZ-1 and Ref-Ti powders have a small cohesive index, suggesting that they will have better spreadability and flowability when compared to other samples.
Finally, GranuDrum instrument enables the comparison of one sample with another as well as defining a threshold (24 in this case) below which a successful Selective Laser Melting (SLM) process for Additive Manufacturing process can be achieved.
Optimization of Recoater Speed
Powder Used
The sample used is a commercial stainless-steel 316L powder (from Hogänäs) with a basic particle size of approximately 50 µm.
GranuDrum Analysis
The GranuDrum instrument was used to test this powder. The cohesive index and the dynamic angle of repose were plotted as a function of the GranuDrum rotating speed. The measurements have been carried out with increasing rotating speed (from 2 to 60 rpm) and then a decreasing rotating speed (from 60 to 2 rpm).
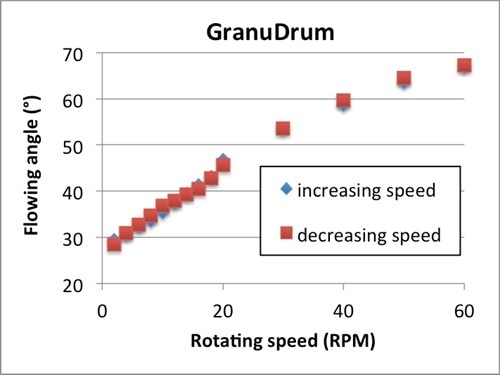
Figure 5. Dynamic angle of repose versus GranuDrum rotating speed for the stainless-steel 316L powder.
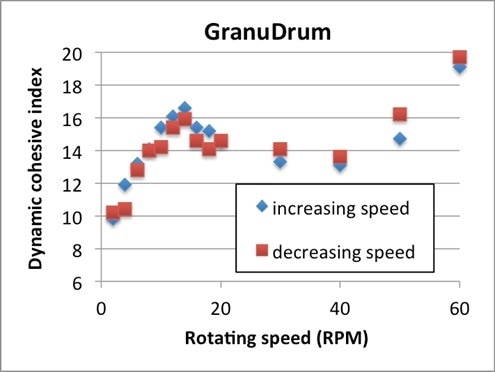
Figure 6. Cohesive index versus GranuDrum rotating speed for the stainless-steel 316L powder.
Figure 5 demonstrates that the dynamic angle of repose (also called flowing angle) increases linearly with the process velocity. Therefore, this parameter is not the ideal one to increase the recoater speed.
Cohesive index variations for various rotating speeds are explored in Figure 6. There will be a linear increase in cohesive index for a speed ranging from 2 to 18 rpm. It will decrease for a speed between 18 and 40 rpm, and finally, it will increase for a speed greater than 40 rpm. These results are very much fascinating as they enable concluding that the powder flowability will be better at 40 rpm than at 18 rpm. A recoater process speed of around 40 rpm would be better for achieving the best recoater speed with a good spreadability.
Furthermore, it is necessary to compare the linear speed of the drum wall (which relates to the average flowing speed at the powder/air interface layer as per the mass conservation law) with the recoater speed. Subsequently, the range of speeds considered at the time of the GranuDrum measurement should be chosen accordingly. The next plot demonstrates the surface flow speed as a function of the drum rotating speed to assist in choosing the correct rotating speed.
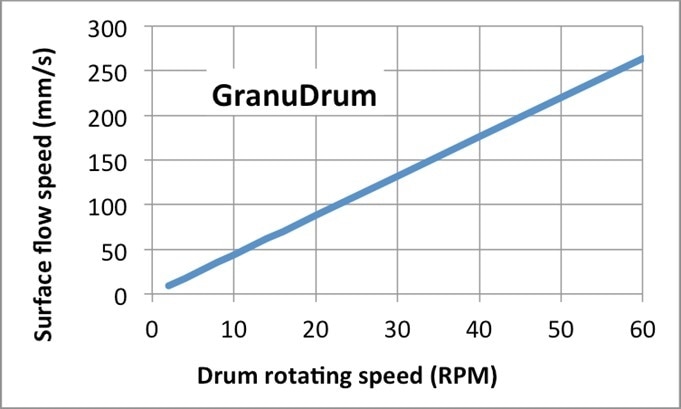
Figure 7. Recoater speed (in mm/second) versus GranuDrum rotating speed (in rpm).
Thus, the optimum recoater speed for the stainless-steel powder is around 175 mm/second (40 rpm).
Conclusions
The GranuDrum instrument enables:
- Optimization of the recoater speed for a given powder to have the best powder spreadability and optimum process speed
- Choosing the best powder in terms of “spreadability”
Bibliography
- Cascade of granular flows for characterizing segregation, G. Lumay, F. Boschin, R. Cloots, N. Vandewalle, Powder Technology 234, 32-36 (2013).
- Combined effect of moisture and electrostatic charges on powder flow, A. Rescaglio, J. Schockmel, N. Vandewalle and G. Lumay, EPJ Web of Conferences 140, 13009 (2017).
- Compaction dynamics of a magnetized powder, G. Lumay, S. Dorbolo and N. Vandewalle, Physical Review E 80, 041302 (2009).
- Compaction of anisotropic granular materials: Experiments and simulations, G. Lumay and N. Vandewalle, Physical Review E 70, 051314 (2004).
- Compaction Dynamics of Wet Granular Assemblies, J. E. Fiscina, G. Lumay, F. Ludewig and N. Vandewalle, Physical Review Letters 105, 048001 (2010).
- Effect of an electric field on an intermittent granular flow, E. Mersch, G. Lumay, F. Boschini, and N. Vandewalle, Physical Review E 81, 041309 (2010).
- Effect of relative air humidity on the flowability of lactose powders, G. Lumay, K. Traina, F. Boschini, V. Delaval, A. Rescaglio, R. Cloots and N. Vandewalle, Journal of Drug Delivery Science and Technology 35, 207-212 (2016).
- Experimental Study of Granular Compaction Dynamics at Different Scales: Grain Mobility, Hexagonal Domains, and Packing Fraction, G. Lumay and N. Vandewalle, Physical Review Letters 95, 028002 (2005).
- Flow abilities of powders and granular materials evidenced from dynamical tap density measurement, K. Traina, R. Cloots, S. Bontempi, G. Lumay, N. Vandewalle and F. Boschini, Powder Technology, 235, 842-852 (2013).
- Flow of magnetized grains in a rotating drum, G. Lumay and N. Vandewalle, Physical Review E 82, 040301(R) (2010).
- How tribo-electric charges modify powder flowability, A. Rescaglio, J. Schockmel, F. Francqui, N. Vandewalle, and G. Lumay, Annual Transactions of The Nordic Rheology Society 25, 17-21 (2016).
- Influence of cohesives forces on the macroscopic properties of granular assemblies, G. Lumay, J. Fiscina, F. Ludewig and N. Vandewalle, AIP Conference Proceedings 1542, 995 (2013).
- Linking compaction dynamics to the flow properties of powders, G. Lumay, N. Vandewalle, C. Bodson, L. Delattre and O. Gerasimov, Applied Physics Letters 89, 093505 (2006).
- Linking flowability and granulometry of lactose powders, F. Boschini, V. Delaval, K. Traina, N. Vandewalle, and G. Lumay, International Journal of Pharmaceutics 494, 312–320 (2015).
- Measuring the flowing properties of powders and grains, G. Lumay, F. Boschini, K. Traina, S. Bontempi, J.-C. Remy, R. Cloots, and N. Vandewall, Powder Technology 224, 19-27 (2012).
- Motion of carbon nanotubes in a rotating drum: The dynamic angle of repose and a bed behavior diagram, S. L. Pirard, G. Lumay, N. Vandewalle, J-P. Pirard, Chemical Engineering Journal 146, 143-147 (2009).
- Mullite coatings on ceramic substrates: Stabilisation of Al2O3–SiO2 suspensions for spray drying of composite granules suitable for reactive plasma spraying, A. Schrijnemakers, S. André, G. Lumay, N. Vandewalle, F. Boschini, R. Cloots and B. Vertruyen, Journal of the European Ceramic Society 29, 2169–2175 (2009).
- Rheological behavior of β-Ti and NiTi powders produced by atomization for SLM production of open porous orthopedic implants, G. Yablokova, M. Speirs, J. Van Humbeeck, J.-P. Kruth, J. Schrooten, R. Cloots, F. Boschini, G. Lumay, J. Luyten, Powder Technology 283, 199–209 (2015).
- The influence of grain shape, friction and cohesion on granular compaction dynamics, N. Vandewalle, G. Lumay, O. Gerasimov and F. Ludewig, The European Physical Journal E (2007).
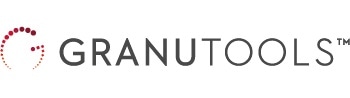
This information has been sourced, reviewed and adapted from materials provided by Granutools.
For more information on this source, please visit Granutools.