As soon as degradation starts, the conversation inevitably turns to how it occurred. It might be thought that the solution to this question is commonly known. However, it is not so. The good news is that the factors that bring about polymer degradation during processing are few.
Earlier, tests were carried out on two sets of polycarbonate parts. The outcomes showed exactly the circumstances that were summarized in that article. The “good” as well as the “bad” parts showed an extreme increase in melt flow rate (MFR) that is normally a sign of polymer degradation. The “good” parts were considered to be good as they had worked well in the application. The “bad” parts exhibited noticeable cracking that alerted the end user to the issue.
MFR Results
The molder had not offered a sample of the raw material; however, it had given documentation indicating the specific grade of material that was used in both runs. The raw material had a nominal MFR of 8.5 g/10 minutes. The “good” parts provided a MFR of 22.3 g/10 minutes, or a rise of 159%, while the bad parts offered a melt flow rate of 66.4 g/10 minutes, an increase of almost 670%. Both these outcomes cross the benchmark boundary of 40% MFR increase during processing, but clearly, the bad parts were molded from a material that had experienced much more negative impacts.
When such outcomes are shown, it is easy to put the blame on the molding process. This supposes that the raw material used to manufacture the parts was, indeed, as shown. It also supposes that the material was developed to the reported specification. The value of 8.5 g/10 minutes indicates the declared nominal value, and not essentially the value for the lot of material in question. However, if developed properly, a grade of material with a nominal value of 8.5 g/10 minutes should not go beyond 10.5 g/10 minutes. Yet, this positions both of these outcomes well outside the suitable range.
Reasons for Polymer Degradation
Once degradation has been determined, the debate immediately turns to how it occurred. It might be thought that the solution to this question is commonly known. However, the fact that it is asked as often as it is implies the opposite. The good news is that the factors that cause polymer degradation during processing are few.
The combined effect of heat and time when the material is in the melt state is a universal concern for all polymers. Polymers are generally organic and have a restricted tolerance for the shear stresses and temperatures related to molding processes, specifically injection molding. Polymers such as polypropylene and polyethylene will endure the processing environment rather well until the antioxidant package in the material lasts.
But polymers like nylons and polyesters are more prone to thermal degradation. The rate at which this degradation happens is dependent on the actual melt temperature of the material in the injection cylinder and the time that it spends there, also called the residence time.
If any material supplier is asked about the preferred residence time for their products, their answers will normally lie within the range of 5–10 minutes, based on the polymer. Sadly, as molds usually function in machines with barrels that are larger than those that would be regarded as optimal, residence times usually surpass these recommended values significantly.
The longest residence time that the author has personally seen is 51 minutes, and he has known of a situation where the residence time went beyond 60 minutes. At such time frames, even melt temperatures that lie in the range specified by the supplier may not guarantee the survival of the material.
Moisture is the other main problem. This is not a universal problem. Some materials like polystyrene and polyethylene are non-polar and cannot take up a considerable quantity of water. Other materials such as acrylic and ABS are hygroscopic; however, the water will only result in cosmetic issues, it will not have any chemical impact on the polymer. However, a small group of polymers, including polycarbonate, polyesters, and nylons, in fact react with more moisture in such a way that it breaks chemical bonds within the polymer chain, thereby decreasing the molecular weight of the polymer.
This process is called hydrolysis and it can only be stopped by drying the raw material to a suitable level before the material is brought into the heating cylinder of the molding machine. For certain materials, the maximum permissible moisture content for processing is as low as 200 parts per million (0.020%), and optimal levels can be as low as 50 ppm.
Just like most chemical reactions, hydrolysis occurs more quickly at higher temperatures. Therefore, in a condition where melt temperatures are increased or residence times are prolonged, material that is not dried properly will degrade even more rapidly than it would under optimal processing conditions. A number of processors and end users think that hydrolytic and thermal degradation will be visually clear. However, this is not the case often.
Thermal degradation may lead to some discoloration; however, colorants can hide this impact, and dark colors like black and brown can make color changes unnoticeable. Hydrolytic degradation is usually related to a visual defect called silver streaking or splay. However, by the time splay emerges on the part surface, it is already very late. Splay is usually caused by volatiles developed when surplus moisture in the material boils. The moisture that damages the polymer molecule has been used in the chemical degradation reaction and will not cause a visual defect. PET is an outstanding example of this.
PET can be molded with a considerable amount of moisture and still parts can be fabricated with a good surface appearance as it reacts with the water very effectively. An alert processor may observe a decrease in the viscosity of the material and the quality-control people conducting mechanical tests will definitely observe a fall in mechanical strength and ductility; however, the parts will appear good.
Drying Temperature
One more factor that can affect the molecular weight of a polymer during processing is the extreme drying process used to eliminate the moisture from the material. As drying involves increased temperatures, prolonged drying times can possibly have an impact on the integrity of the material, specifically if the drying temperatures go beyond supplier recommendations. This may not happen in most amorphous polymers such as ABS, polycarbonate, and acrylic, since the recommended drying temperatures are normally 20 °F to 30 °F below the softening point. Any major deviation in the drying temperature will rapidly create a sintered mass of material that will not flow through the hopper anymore.
However, the recommended drying temperature in semi-crystalline polymers may be 200 °F to 300 °F below the melting point. In these instances, considerably increased drying temperatures can take place without causing any obvious issues in conveying resin through the material-handling system. However, studies have demonstrated that nylon — specifically those grades that are not heat stabilized — will suffer an increase in MFR if dried for prolonged times at temperatures that go beyond supplier recommendations.
These MFRvariations happen even before the introduction of the material into the heating cylinder of the molding machine. The resultant brittle condition of parts developed from this degraded material is usually known as “overdrying.” However, it has no effect on the actual moisture content of the pellets. It can be ascribed to oxidation, another chemical reaction that leads to a decrease in the molecular weight of the polymer.
Unfortunately, this factor has gained attention to a considerably greater extent. It is an actual concern with nylons, and studies have demonstrated that the oxidation process is promoted by drying temperature much more than by drying time. Oxidation takes place at a much slower rate in a majority of the polymers when compared to nylons and can take days or even weeks, mainly if proper temperature control is in place.
However, this has not prevented material suppliers from including maximum drying-time recommendations in their literature. Some of these recommended times are extremely less, as short as 8–12 hours, and they give a bad message to processors that there is a possibility of damage to the polymer if these drying times are crossed.
Conclusion
These comparatively new recommendations have no science behind them. While talking about the conservation of the molecular weight of a polymer, the risks of inadequate drying are far more important than those related to drying for a longer period of time. Actually, disparities in the effectiveness of drying differentiated the “good” from the “bad” polycarbonate parts as discussed at the starting of this article. Although the “good” parts could certainly have been better, they were at least dried to a level that enabled a functional part to be produced. The “bad” parts were not, as demonstrated by splay on some of those parts.
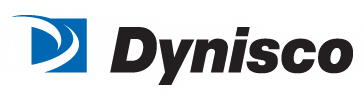
This information has been sourced, reviewed and adapted from materials provided by Dynisco.
For more information on this source, please visit Dynisco.