Although frequently critiqued, Melt Flow Rate (MFR) is an excellent measure of the polymer’s relative average molecular weight. Since molecular weight (MW) is the force that drives the performance of polymers, it turns out to be a highly beneficial number.
Basics of MFR Testing
MFR testing can be characterized as the Rodney Dangerfield of material test techniques — it receives no respect. People from every area of the industry tone down the value of the test or completely belittle its practicality. Those who instruct industry experts on processing are quick to highlight that the MFR value for a material is a single point on a curve that describes viscosity as a function of shear rate. Since plastics are non-Newtonian, their viscosity differs with shear rate.
The MFR test pushes the molten material at a single flow rate, thus a single shear rate, and fails to record the complete range of the behavior of a material as a function of changing shear rate. To make issues worse, the shear rate is not even regulated. While the load on the material or the shear stress, is steady during the progression of the test, the shear rate is an output of the test. The MFR itself is a replication of the shear rate used during the progression of the test, but it is an outcome of the test and not a regulated input.
Academics do not like the units. How does one get from grams/10 minutes to anything significant in terms of ultimate polymer behavior? The author has written comprehensively on the comparative relationship between MFR and average molecular weight. This has resulted in the occasional irate e-mail from university professors demanding an explanation as to how one can convert from grams/10 minutes to the proper units for molecular weight, which is grams/mole. It is a valid question and one that will be answered as thoroughly as possible elsewhere.
In actuality, MFR testing is not a good tool for gauging processability. The reasons for this will be discussed exhaustively later in this series. However, it was never projected to be a measurement of processability; this is a version that has been applied by a few in the processing community. The notion that an MFR tester is some kind of poor man’s capillary rheometer is essentially incorrect. Furthermore, the relationship between MFR and average molecular weight is a comparative one. There are many factors that can tilt this relationship and make elucidation complicated.
For instance, incorporating ingredients to a compound such as impact modifiers, glass fibers, and some additives can modify the MFR of a material without altering the polymer’s average molecular weight even a little bit. However, if the test is highly impractical, why does the value get published on several material data sheets? Not only is it a line item on the bulk of published data sheets, but it is also usually the main characteristic that differentiates one grade of material from another within a particular polymer series. In materials as different as acetal, polycarbonate, and polystyrene, the MFR may be the only value on the data sheet that differs considerably from grade to grade within a specific product offering. The reason is not complicated. Assuming that all other parameters are kept unwavering, the MFR is an excellent gauge of the relative average molecular weight of the polymer. Since molecular weight (MW) is the driving force underneath the performance in polymers, it turns out to be a very beneficial number.
MFR Testing of Polymers
The flow rate of a polymer is inversely proportional to its viscosity. High-viscosity materials flow with greater resistance and therefore more gradually under any specific set of conditions compared to low-viscosity materials. Thus, higher-MW polymers possess lower MFR values and lower-MW polymers possess higher MFR values.
Specialists in injection molding favor the latter as it is easier to fill demanding flow paths in a mold with what is referred to as “high-flow” materials. Blow molders and extruders are more likely to favor higher-MW materials as they deliver higher melt strength, a parameter that makes it simpler to control the shape of a parison or a multifaceted profile, die-swell considerations aside. End users favor higher-MW polymers whether they understand it or not, since higher MW correlates with improved product performance. Impact resistance, environmental stress-crack resistance (ESCR), fatigue performance, and barrier properties (to name a few) all improve with higher MW.
The author’s first exposure to the significance of MW as a material-selection criterion came on the molding floor more than three decades ago. It was when his team was molding traffic-light signal housings out of a high-MW injection grade of polycarbonate. The nominal MFR of the material was 5 g/10 minutes. The geometry of the part, united with the age of molding machines, made this a very difficult part to make. As the performance of the part was very critical, a falling-dart impact test was conducted once every hour to ensure that the process was under control. At the end of the operation, 20 parts were randomly selected from the lot and the impact test was repeated. The standard result was that 20 out of 20 parts passed.
On another occasion, the author and his team decided to see what would occur if a lower-MW grade was used. The reasoning behind this was as follows: If a material that flows more easily can be used, then the melt temperature of the material can be lowered and the pressures linked with injection and packing can also be reduced. This will decrease the stress on the material and enhance the impact performance of the part or at least compensate for the lower impact strength of the lower-MW polymer.
When a grade with a nominal MFR of 10 g/10 minutes was sampled, it was noted that the melt temperature of the material could be reduced by 40 °F (22 °C), and pressure during first-stage filling dropped by 10%. However, when an impact performance assessment was done on 20 parts produced from this material, only four of them survived the test. This large variation in behavior took place regardless of the fact that the notched Izod impact values reported on the data sheets for these two grades were identical. This difference between actual performance and the expectations formed by the data sheet occurs daily in industry, and this will be addressed in a later article.
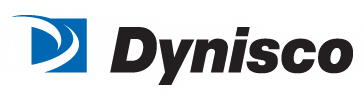
This information has been sourced, reviewed and adapted from materials provided by Dynisco.
For more information on this source, please visit Dynisco.