The majority of manufacturers are in agreement that to ensure the success of a project, developing a flawless design, and choosing the most appropriate materials are paramount. Nevertheless, many underestimate the impact that choosing the best processing method for your materials can have on costs, time-to-market, and overall product quality.
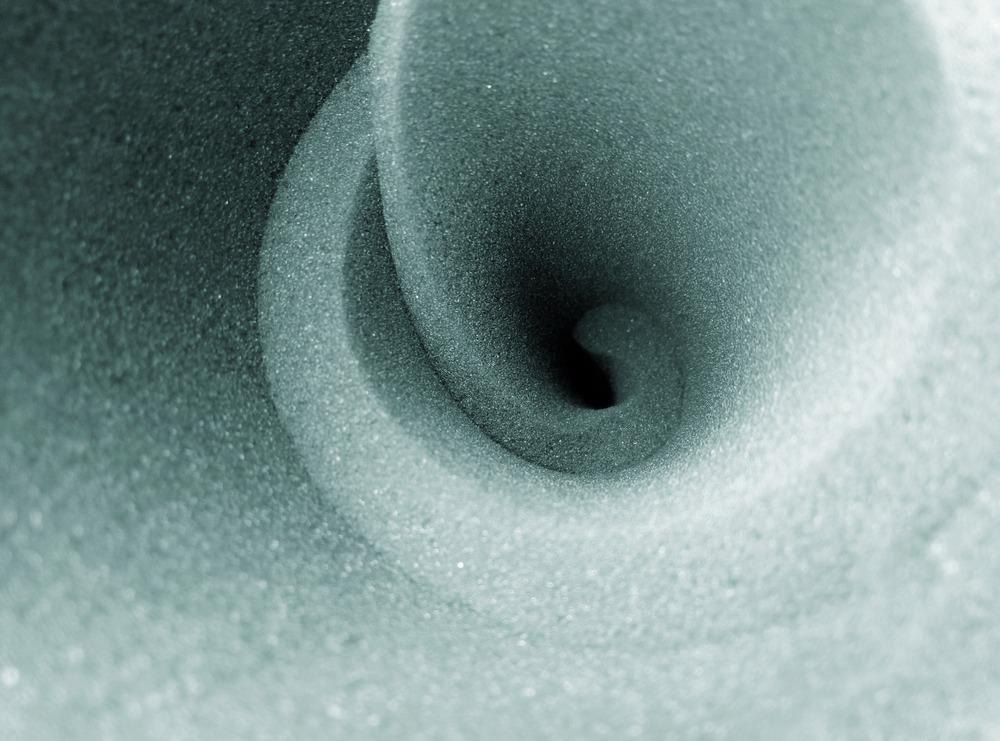
Image Credit: Shutterstock/Aulia1
Rigid and flexible polyurethane foams from General Plastics are frequently employed to create production parts in a vast range of industries, from automotive, aerospace and medical markets to recreation and consumer markets.
A commonly held misconception surrounding the use of foam is that it always involves machining. Many new clients will request CNC quotes, unaware that alternative processing options, including molding, are available.
A further misconception is that molding incurs higher costs than machining. Following decades spent working with clients on a broad range of complex applications, General Plastics has subsequently recommended cast molding for its foams, particularly with high volume runs.
With the aim of presenting a greater variety of processing options for consideration, this article will highlight the various nuances between the processes and results from molding versus machining.
Overview of Machining Versus Cast Molding
CNC machining employs computer software to govern machine tools that cut complex 2D and 3D shapes out of blocks of material. Typically, a CAD drawing or other digital depiction of the desired part is formed, and the drawing is subsequently converted into instructions, such as speeds, locations, and coordination, for the CNC machine.
To remove various layers and achieve the final shape, several routers, lathes, and other tools may be needed as part of the machining process. Overall, CNC machining is quick, precise, repeatable and able to achieve exact tolerances.
Cast molding, which is also referred to as casting, hand-poured molding, and clamshell molding, involves the production of a tool in the required shape and then the pouring of the liquid thermoset resin into the mold. The polyurethane swells to fill the void during the reaction and becomes polyurethane foam.
Once the foam has cured and hardened, it is detached from the mold and the tool is ready to produce the next, duplicate part.
Injection molding is similar to casting but has a number of key differences. In injection molding, materials are injected into the mold at high pressures. As a result, the injection molds need sturdier materials, more time, and greater expenses to produce.
Casting tools are typically quicker and have lower costs since this process simply depends on low pressure or gravity only to pour the blended reactants into the mold. Furthermore, the setup and teardown for injection molding is a lengthier process than that for casting and could necessitate support from heavy lifting equipment.
The Differences between Machining Versus Cast Molding
Following this brief introduction to the key features of machining and casting techniques, a more in-depth exploration of their differing costs, lead times, quality and other factors will be detailed below.
Cost
When deciding between the two methods, cost is typically a key factor for consideration. Variations in cost can be influenced by production volume, tool costs, material savings, and the size of the part.
Production volume is one of the simplest factors to define. On the whole, if the production run for the life of the part is fewer than 100 parts, machining is a suitable option, while if the lifetime volume is more than 100 parts, the casting makes more sense.
.png)
In general, CNC machining is less costly for low volume runs and prototyping, but eventually, a crossover point is reached where molding is more cost-effective for larger production volumes.
For cast molding, the cost of the tool is lower than what is often expected. Depending on the volume, the casting tool can be formed from aluminum, filled epoxy, silicon, or even high-density foam.
To compare, metallic tools have the highest costs but are most likely to last for the full lifetime of the program, while composite tools cost only around one-third of the price of metallic tools, but may need repair over time.
Material savings have an impact on the cost of the processing method. Subtractive manufacturing, such as machining, consists of producing a product by removing, cutting, and drilling away excess material to yield the preferred shape. This process does, of course, result in the production of excess waste. This waste is a raw material that is included in your costs and must now be discarded.
Alternatively, formative manufacturing employs methods such as casting, injection molding, and stamping to produce or cast materials directly into the shape of the final product. With this method minimal excess waste is produced, thus, depending on the size or complexity of the part produced, there may be substantial material savings.
.jpg)
Subtractive manufacturing, like machining, involves cutting out the desired component from a block of material. Whereas formative manufacturing, like molding, involves forming the part with very little material waste.
Lastly, the size of the component has an impact on the final decision between machining versus casting. For out-sized components, in which the casting tool would be even greater in size, it may be less costly to opt for machining rather than molding the part.
Nonetheless, outside circumstances can have an impact on this. Recently, General Plastics worked alongside a company in the oil and gas industry who was in need of support to produce large flotation modules for subsea pipe supports.
It was assumed that it would be necessary to machine the floatation modules from large foam blocks, as the cost of producing a tool of that size for casting or molding would be prohibitive.
However, following a number of calculations, it was found that the expenses and time factors linked with machining were in fact, not appropriate and as such, a large molded part would be more suitable for the client’s needs. There were no other known instances of anyone creating a custom casting of polyurethane foam of that size, so this was considered a unique case.
By switching from machining to casting, the project accomplished substantial savings in both cost and materials. The key point to bear in mind is that each application is different, and thus consulting with a materials specialist such as General Plastics at an early point is highly beneficial.
Lead Times
From the initial customer communication to the first part delivered, CNC-supplied components offer shorter lead times than molded parts. On the other hand, if the tool has already been produced and the order is simply a delivery of additional parts, the molded components will be must quicker.
To offer an example of timelines for tool production, the quickest and least complex tools produced from rigid foam may take around 40 to 120 hours to produce, from design to first pour. Conversely, more complex tools will take upwards of 200 hours to create. Further time should be factored in for more complex designs.
Product Quality
There are some differences between the finished parts created by machining and molding which are worth noting. Since it is tricky to produce detailed textures with machining, components produced in this way will have a smooth, uniform surface. As a result of the machined part’s cellular foam surface, there may be a need for additional sealing and painting.
In contrast, since a molded part comes away from the tool with a smooth or textured skin that is already sealed, such parts have a superior finish. It is even possible to pre-apply paint inside the mold. For post-processing, all that is required is to wipe off the mold release and get rid of the parting line, and the product is fully ready.
If an application requires a product to be both durable and waterproof, casting is likely to be the most suitable option.
Each process has advantages and disadvantages when it comes to tolerances. On the whole, machining is able to attain greater tolerances than molding, but there is also higher variability within both parts and lots compared to molding.
On many occasions in machining, a program is set up on a machine and then removed to allow the machine to be employed in a different project. When the program needs to be re-loaded, the positioning may differ slightly, which results in minor part consistency issues between lots (although all within acceptable tolerances).
In contrast, with casting, tools are designed to suffer minimal wear, so molded parts are almost identical between batches.
Selection of Materials
Depending on the properties required, there are a broad variety of types of polyurethane foams, including open versus closed-cell, density and strength, impact- and thermal-insulation, self-skinning, and buoyancy, among others. Depending on the particular mix of parameters, some processing techniques may be more appropriate than others.
Since rigid foams have the hardness to endure the cutting and grinding employed in machining, they are suitable for processing with either machining or casting.
Some flexible foams though may only be suitable for cast molding, as they may be too soft to withstand the machining process. However, it is possible for some flexible foam applications with simple design specifications, such as dunnage or packing material, to be machined.
Which Method is Right for You?
A number of varied factors and considerations have been introduced to compare machining against molding polyurethane foam. This chart helps to summarize the information provided, offering a clear picture for how to choose the most appropriate method for specific application requirements, including complexity, speed, design certifications, quantity, and surface finish.
.png)
Ideal Applications for Machining and Molding
In summary, for prototyping, runs of fewer than 100 parts, precision tolerances, and components with large, complex volumes, machining is the ideal process. For runs of more than 100 parts, precision from lot to lot, and parts where skin or complex texture is required, cast molding is recommended.
To illustrate, casting is employed in marine applications to create fuel floats where buoyancy is required and the skin assists by inhibiting water absorption. In cases of automotive use, the skin on the foam offers a pleasant surface that is protected against scraping during cleaning and regular use.
It is also possible to blend the two methods, for example, when a single part is made up of several types of foam so as to support precise material properties. On some occasions, this means foam A is machined and then foam B is molded over it, and other times, this process is reversed, with foam A molded and foam B poured over it and machined.
Examples of such processes can be seen in aerospace padded parts and automotive dashboards, in which both rigid and flexible foams are incorporated to offer structural strength and impact absorption.
Complex designs may also be best approached with mixed-mode processing. Here, a part may be initially molded with a textured surface, before recesses or sharp negative drafts are removed through machining.
Reduce Your Engineering Shadow
Cost is not the only consideration to be kept in mind when making decisions on manufacturing. Assumptions and misconceptions made at early points in the design process can result in negative and difficult to reverse impacts on decisions later on. This is known as the ‘engineering shadow’.
To reduce this effect, and to minimize costs in time and wastage, it is highly advisable to seek support from materials experts such as General Plastics at an early point in the planning stages.
General Plastics supplies a broad range of pioneering rigid and flexible polyurethane foam solutions, as well as offering complete in-house production services for converting foam and other nonmetallic substrates into production parts for OEMs and Tier 1 and Tier 2 vendors.
Their production facilities offer large-capacity CNC machining and cast molding services to accommodate projects of any size, as well as quality assurance and testing services to authenticate your products.
Whichever method you select, General Plastic’s team of scientists and engineers can support you in delivering machined or molded components with high efficiency, high convenience, and low costs.
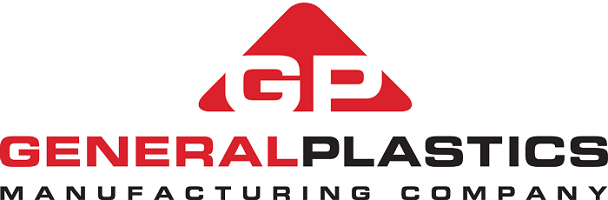
This information has been sourced, reviewed, and adapted from materials provided by General Plastics Manufacturing.
For more information on this source, please visit General Plastics Manufacturing.