The electric vehicle (EV) revolution continues to pick up the pace, with no signs of slowing down. In 2008, there were fewer than 500 EV charging stations in the United States; in 2018, this number had risen to over 47,000. As recently as ten years ago, there were only 4 four battery or fuel-cell powered models of car available to North American car buyers; they now have the choice of upwards of 50 electric and hybrid automobiles. This same upward trend is also predicted for EV batteries, with recent forecasts projecting a 20% compound annual growth rate (CAGR) to a $15 billion market by 2026.
Such significant growth will require investment and improvement in battery and module construction technology. To extend battery life and improve driving range, the resilience of the device must be improved during both hot and cold temperatures. Battery module production costs need to drop, which may be achieved through a reduction in the number of manufacturing steps as well as the complexity of those steps. Automation also has a role to play in bringing down module costs. Vehicle materials costs and a further driving range can be achieved by reducing battery weight and size. It would seem that these disparate challenges need different solutions — fortunately, Saint-Gobain Norseal® PF Series compression pads can help address all of them simultaneously.
Inside the Materials Driving E-Mobility: Tape Solutions for EV Battery Pack Protection
Video Credit: Saint-Gobain
Temperature Issues
For electric and hybrid vehicles to truly dominate the market, the battery performance must remain steady in cold weather. If the battery experiences low temperatures, the chemical reaction slows down when charging and discharging, negatively impacting battery efficiency. Extreme cold can also harm the components themselves; plastics get brittle, and elastomers stiffen and weaken, for example. The cumulative effect is both a reduced range and lifetime of the battery.
Research has determined that optimal battery life is attained by letting the battery “breathe” while still applying the right amount of pressure to secure electrical and thermal connections. However, this process can be a challenge for large battery packs that contain numerous cells. When a battery is recharged, the internal chemistry can alter and cause it to physically change and expand, an effect that can lead to delamination of the internal cells and deformation in the components or battery pack.
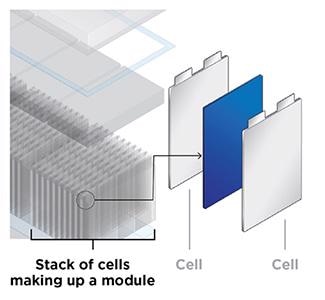
Compression pads — also known as dielectric foams — are used to maintain pressure on the face of a pouch cell (and in some cases of prismatic cells). They may also be used to insulate the cells to promote and maintain a uniform face temperature. If, when exposed to low temperatures, the elastomeric (rubber) compression pad demonstrates poor resilience or poor recovery, micro-cracks develop and ultimately result in fatigue. This causes little or no face pressure on the cell, bringing the cell to premature failure.
Compression pads keep pressure on the battery pack that ensures continuous electrical and thermal connections while allowing enough space in the package itself to expand and change shape. The spring-like behavior of the foam deflects and returns energy and then diffuses it across a range of compression amounts, a property called compression force deflection (CFD). Foam cushioning resists permanent deformation when exposed to extreme pressure or compression loads, and will typically maintain effectiveness beyond the lifespan of the battery pack.
To evaluate this effect, the cold temperature resilience of various compression pads found in the market can be tested. The graph below compares the results of the PF45 microcellular polyurethane foam versus a competitor’s microcellular PUR foam.
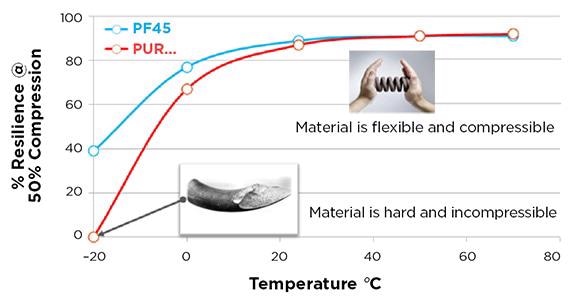
Saint-Gobain Norseal PF Series materials have superior capacity to operate at low temperatures, allowing better, more resilient performance over a wider range of temperatures than other PUR solutions in the market. In regards to overheating at high temperatures, Norseal foam’s insulative properties are inhibited by compression — it urges heat to dissipate into the heat sink rather than spreading into neighboring cells. This is critical as overheating is the primary reason for failure in batteries and electronics.
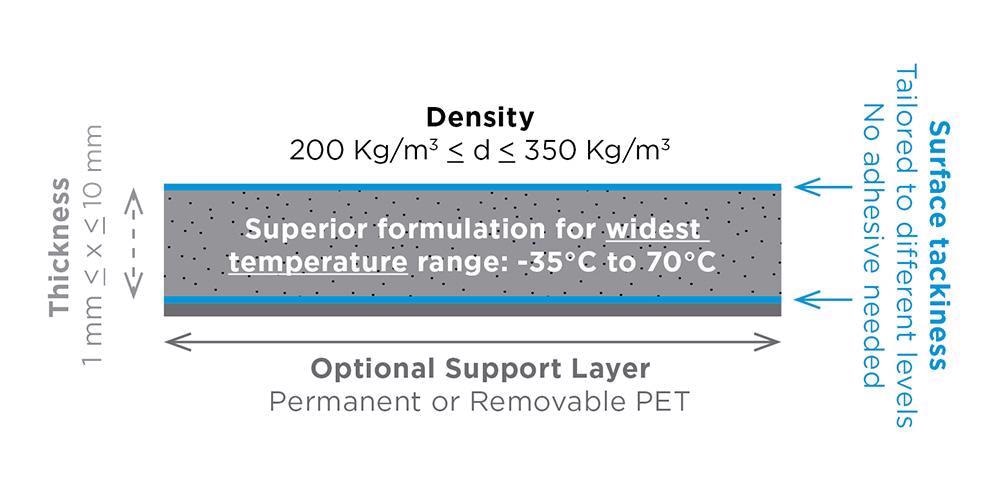
Tackiness and Foam Surface Tailoring
To meet the demand for electric vehicles, battery production will have to increase significantly, setting the stage for automation to increase its role in battery production and battery-pack assembly. As automation becomes more integral to the manufacturing process, minimizing the number of steps and parts will be crucial. In the majority of cases, when compression or tolerance pads are between the cells, an extra step is included to hold the pads to individual cells during the assembly — which is often done by using adhesive or glue. The disadvantage of adhesives is that if an alignment error occurs, the faulty pad must be removed from the cell, causing wasted materials and costs. Fixes like this also impact the production process by slowing or stopping an otherwise smoothly running production line.
To handle this issue and make automation easier to implement, Norseal PF series pads were developed to have an inherent tackiness to them, without further application of adhesive or glue. If the pad is applied in the wrong area, it can easily be peeled off and replaced without wasting material. Tackiness is assessed using a technique that was designed to simulate the application as closely as possible. The Norseal PF Series’ tackiness is compared to competitor pads in the chart below.
Some applications may not need this tackiness, so Norseal PF series, therefore, includes an option to decrease, or even remove it altogether. For compatibility with other automatic assembly processes, PF series products are also available with either a removable or permanent PET liner.
Thickness and Density Range
Norseal PF Series products possess the widest range of thicknesses in the industry, even at densities as low as 200 kg/cm3. When looking to minimize the overall weight of the module, pack, and vehicle itself, low density is the key parameter to look for. PF Series products have overcome an important benchmark to reach thicknesses as low as 1 mm at densities of 200 kg/m3.
The standard densities in the PF Series are 200 kg/m3 and 250 kg/m3, but customers can request even higher custom densities. These may be used to address scenarios in which the cell chemistries and types (for example, prismatic versus pouch) necessitate firmer foams to withstand cell swelling with higher forces. The PF Series offers a standalone foam with the unique combination of both low thickness and low density, where foams from other manufacturers require an additional film support layer to achieve a similar combination of density and thickness.
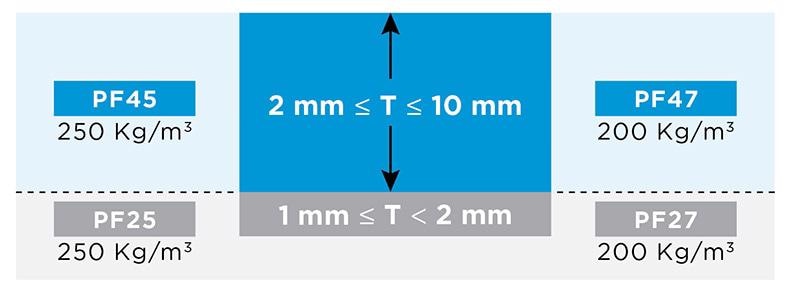
Conclusion
The promise of efficient, low-cost, and long-range electric vehicles will only come about through improvements in battery manufacturing technology. Modern foam materials, such as the Norseal PF Series, offer consistency and reliability over wide temperature ranges, are designed with automation in the manufacturing and placement processes in mind, and provide low weight while improving battery robustness. Using them in electric vehicle production will be key to manufacturing growth and an overall greener future.
Inside the Materials Driving E-Mobility: Tape Solutions for EV Battery Pack ProtectionPlay
To find out more about Norseal PF Series tape solutions, visit their product web page today.
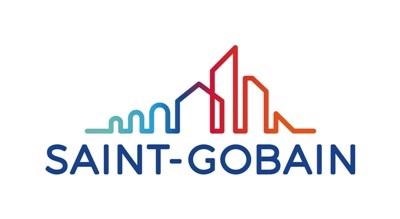
This information has been sourced, reviewed, and adapted from materials provided by Saint-Gobain Tape Solutions.
For more information on this source, please visit Saint-Gobain Tape Solutions.