Interview conducted by Courtney Garner, MAJan 24 2020
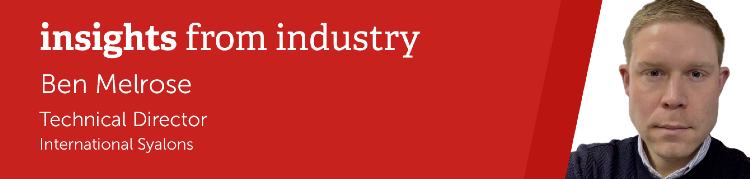
AZoMaterials spoke to Ben Melrose, Technical Director at International Syalons, about the properties of silicon nitride and sialon ceramics, the challenges associated with manufacturing technical ceramics, and how International Syalons are providing the solutions to demanding industrial and engineering challenges.
Can you give a brief overview of International Syalons and the types of materials that you manufacture?
International Syalons was established in the late 1980s in Newcastle upon Tyne, England, as a solution to the challenges associated with manufacturing silicon nitride ceramic products. Sialon ceramics were jointly invented by the founding researchers of International Syalons in collaboration with the Newcastle University in the early 1970s (independently, but at the same time as a Japanese research group) and commercialised in the 1980s. It was discovered that the addition of the oxide ceramic alumina to silicon nitride lead to the formation of a new group of ceramics called ‘sialon’, who’s name originates from its constituent elements (Si-Al-O-N).
In addition to silicon nitride (Si3N4) and sialon (Si-Al-O-N), International Syalons also supplies other advanced technical oxide- and non-oxide ceramics including zirconia (ZrO2), alumina (Al2O3), and silicon carbide (SiC), each of which offer slightly different material properties which suit specific applications.
.jpg)
β-sialon SEM micrograph and Jänecke prism showing phase relations in the Y-Si-Al-O-N system
Image Credit: International Syalons
What are the different forms and grades of sialons?
Silicon nitride was discovered in the mid-nineteenth century by the chemists Henri Étienne Sainte-Claire Deville and Friedrich Wöhler. This fascinating but rather crude new material was studied for many years as a series of European scientists pushed to unlock silicon nitride’s theoretical potential. It was not until around 1950 when silicon nitride became commercially available as high-temperature tubes, crucibles, and nozzles in the US. It was around this time that excitement sparked numerous research projects to develop novel high-temperature resistant gas turbines using either reaction-bonded (RBSN) or hot-pressed silicon nitride (HPSN). Sadly, due to the difficulties of producing complex shapes, and the low fracture toughness of advanced ceramics, many of these ambitious projects failed and the interest in ceramics waned while attention moved to novel high-temperature metal alloys.
The development of sialon, a silicon-aluminium-oxynitride alloy of Si3N4, was the answer to the problems associated with difficulties of producing complex shapes, relatively poor mechanical properties, and high manufacturing costs of HPSN and RBSN. The addition of small quantities of alumina (Al2O3) and rare earth oxides such as CeO, MgO, Y2O3, or Yb2O3 resulted in fully dense ceramics with improved thermo-mechanical properties by pressureless sintering at lower temperatures.
Since the inception of sialon, International Syalons has developed several commercially available grades of advanced ceramic:
Syalon 101 is a high strength β-sialon which can withstand thermal shock of up to Δ900 °C. This all-purpose technical ceramic surpasses the hardness, corrosion resistance and thermal stability of almost any metal and can be used up to temperatures of 1200 °C.
Syalon 050 has been specifically designed to offer high performances under the most extreme abrasive and wear intensive environments, thanks to its mixed α-β sialon crystalline composition. Like most sialon ceramics, Syalon 050 offers excellent corrosion resistance in addition to even higher hardness (94 HRA), creep and high temperature resistance (1400 °C).
.jpg)
Wear resistant Sialon components
Image Credit: International Syalons
Syalon 110 was developed specifically for use in break rings for the horizontal continuous steel casting process. As such, it offers improved corrosion resistance to molten steel, high thermal shock resistance (Δ800 °C), and a maximum operating temperature of 1450 °C.
.jpg)
Sialon thermocouple protection sheaths
Image Credit: International Syalons
Syalon 501 is a composite grade of sialon which was developed to offer an electrically conductive advanced ceramic with the typical high strength and hardness of silicon nitride. Whereas silicon nitride and sialon are generally superb electrical insulators, Syalon 501’s electrical conductivity allows it to be electro-discharge-machined or wire eroded to form complex die profiles.
What types of advanced technical ceramic solutions does International Syalons offer?
At International Syalons, we pride ourselves on offering technical ceramic solutions which are specific to our customer’s needs, whether they are experienced in designing and using ceramics, or new to this special family of materials.
We work closely with our customers and research partners to help them develop and implement innovative products which either would not survive if made from metallic or polymeric materials, or where the choice to use ceramics significantly improves operational efficiency.
Thanks to the thermo-mechanical properties which sialon ceramics offer, they are used in a wide range of demanding applications and industries including; molten metal handling, aluminium casting, metal forming, welding pins and fixtures, oil and gas processing, chemical and process engineering, and countless niche high-temperature corrosive environments and wear intensive applications.
Where the thermomechanical property requirements are different to those offered by sialon, we would recommend alternative technical ceramics such as zirconia, alumina, or silicon carbide.
These popular materials can offer greater fracture toughness, hardness, maximum working temperature, or thermal conductivity, while there will be a trade off with other material properties such as density, strength, or thermal shock resistance.
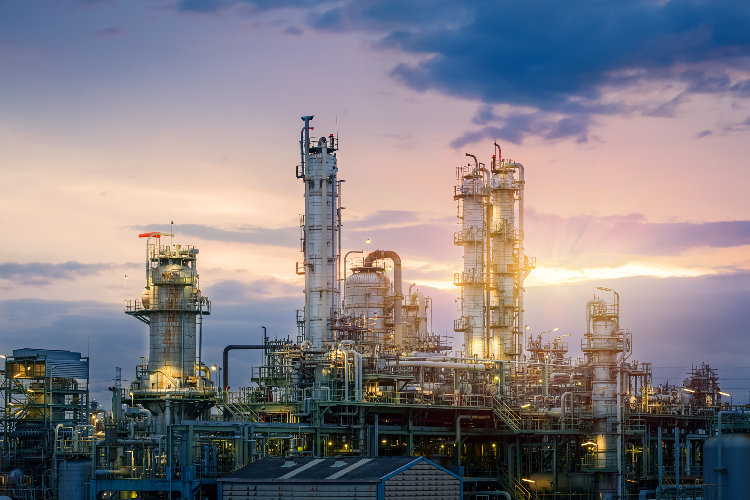
Image Credit:Manine99/shutterstock.com
How is advanced silicon nitride helpful in the molten metal handling industry?
Silicon nitride, and more specifically sialon ceramics offer great advantages to non-ferrous metal casting industries. The casting process of aluminium, tin, and zinc, as well as the handling of many precious metals can be greatly improved by using sialon products such as thermocouple protection sheaths, heater and riser tubes, ladles, crucibles, and stirrers. Importantly, Syalons 101 and 050 are non-wetting to most non-ferrous metals which prevents a build up of dross on the parts, reducing maintenance. The superb thermal shock resistance and high strength of sialon ceramics allows for much faster pre-heating and more forgiving handling of tubes.
The outstanding corrosion resistance of sialon compared to traditional refractory materials such as nitride- or carbon-bonded SiC, aluminium titanate, graphite or cast iron means that sialon tubes can be produced with much thinner wall thicknesses; this significantly reduces the weight of the tube making handling much easier and improving the sensitivity of the temperature measurement system or increasing the efficiency of an emersion heater.
While in comparison sialon products may be more expensive, if well maintained and handled correctly, they will offer greater efficiency and overall cost savings.
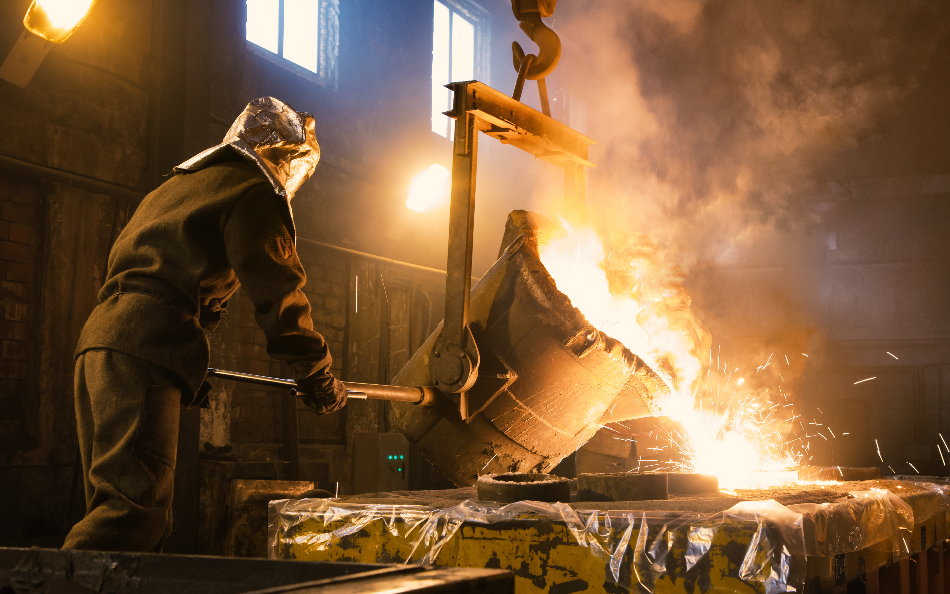
Image Credit: Panksvatouny/shutterstock.com
What are the challenges involved with the traditional manufacturing methods of complex silicon nitride ceramic shapes?
Manufacturing of technical ceramics is notoriously difficult, especially non-oxide ceramics such as silicon nitride. The typical manufacturing route for most ceramics involves the following steps; powder manufacturing and preparation, green forming, sintering, and possibly some final post-sintering machining such as grinding and polishing.
Non-oxide ceramics are extremely sensitive to many of the parameters surrounding their manufacturing such as the purity and particle size of the raw materials. There are numerous possible green forming methods, some of which date back many thousands of years (the word “ceramic” originates from the Greek keramos meaning “potter’s clay”), such as forming simple shapes by hand or using a wheel, and eventually slip casting.
These days ceramic manufacturers employ far more advanced methods such as injection moulding, extrusion, die pressing, or green machining from billets of cold pressed powder. Once ready, the green part is sintered, and once again the continual improvements in sintering technology such as temperature and environment control has enaled researchers to develop far more exotic materials with previously un-thinkable properties such as ultra-high temperature resistant tiles used in space shuttles, or novel electro-ceramics and the next generation of superconductors. Finally, any post-sintering grinding or lapping, which regularly occurs for traditional and advanced ceramics is a very skilled process and requires specialist equipment.
In the case of silicon nitride each of these manufacturing steps involves precise control of each parameter in order to achieve the chosen final material properties. For example, if a low-grade raw material is used the undesirable impurities can prevent stable slip preparation and inhibit densification resulting in inclusions or pores within the microstructure and poor mechanical strength.
Where slip casting is used to form a green body, the remaining water in the cast part must be removed prior to sintering, which is a very slow and delicate process taking many weeks for extremely large parts. The sintering of nitride ceramics also requires great attention as they are sensitive to sintering parameters such as heating rates and temperatures, atmospheres, and the presence of sintering furniture can cause unwanted crystalline phases and or surface discolouration if not chosen correctly.
Once a fully dense sialon component has been produced, to achieve tightly toleranced precision dimensions requires expert diamond grinding due to the extremely high hardness. Even though sialon is relatively high strength and offers a very good fracture toughness compared to most ceramics, it is still brittle and can chip easily if an operator is inexperienced or the incorrect equipment is used.
How has International Syalons overcome these challenges?
Through our many years of experience, International Syalons has refined a robust set of manufacturing processes in order to offer the highest possible quality products. Our highly skilled team have amassed a huge amount of knowledge surrounding sialon ceramics and their optimum production route.
We have worked closely with our customers, research and academic institutes, and project partners to ensure we meet their demands and evolve with their ever-changing needs by developing new materials and adopting new production techniques.
Not only have we always tried to maintain a positive and encouraging ‘family-run’ atmosphere within our business, working hard to develop our colleagues’ knowledge and skills, but we have also invested in the next generation of staff through apprenticeship programs in collaboration with local colleges.
What is next for International Syalons?
The future is bright for International Syalons as we build on our rich history as an independently run SME and grow thanks to the investments offered by our new owners, the CALSITHERM Group, who acquired us in 2018.
Now operating as a structured group of companies we are excellently placed to offer technical ceramic solutions in addition to the thermal insulation, fire protection, and refractory solutions products available from SILCA and CALSITHERM. We are in the process of expanding our factory in order to increase capacity and capabilities, as well as continually improve our product quality and lead times through process efficiency.
Our factory expansion allows us to install additional high-tech specialist equipment enabling us to provide new products and materials for increasingly demanding applications.
One of the most exciting areas of technological development which Syalons will continue to focus on is additive manufacturing of advanced ceramics. Nitride ceramics have long proven extremely difficult to produce via AM, however, we have been involved with the most successful AM technology providers and are able to offer extremely complex 3D-printed sialon parts with outstanding accuracy and surface finish with the thermo-mechanical properties of conventionally machined parts. This ground-breaking technology is opening doors and enabling innovative new ceramic components across a wide range of industries from textile manufacturing and biomedical implants to aerospace and defence applications.
.jpg)
Complex 3D printed Syalon 101 components
Image Credit: International Syalons
About Ben Melrose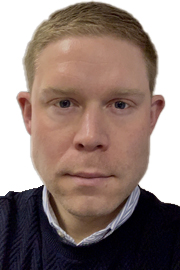
Ben Melrose is Technical Director at International Syalons (Newcastle) Ltd, having joined the company in 2012 as a Development Engineer and was appointed to the Board of Directors in 2019. After studying Engineering of Materials (MRes) at University of Birmingham Ben has focussed much of his attention working to develop new sialon-based advanced ceramic materials and ceramic fabrication techniques alongside customers and research partners, and is now responsible for all aspects of R&D and quality assurance at International Syalons.
Disclaimer: The views expressed here are those of the interviewee and do not necessarily represent the views of AZoM.com Limited (T/A) AZoNetwork, the owner and operator of this website. This disclaimer forms part of the Terms and Conditions of use of this website.