Zirconium dioxide (ZrO2), also known as Zirconia, is a popular and widely available high-strength advanced ceramic with exceptional wear- and impact-resistance properties which is commonly used in manufacturing industries, as well as in dentistry, abrasives, and refractory applications.
.jpg)
Resistance Welding Process (Image Credits: Shutterstock)
The three possible crystalline structures by which zirconia can exist (monoclinic, tetragonal, and cubic) are dependent both on forming temperatures and the presence of stabilizers and dopants including yttria (Y2O3), magnesia (MgO), or ceria (CeO2).
Generally, ceria-doped zirconia (CSZ) has a greater fracture toughness, while yttria-stabilised-zirconia (YSZ) imparts higher flexural (1200 MPa) and compressive strength (>2000 MPa) values, and magnesia-stabilised-zirconia (MgSZ) offers increased thermal shock resistance.
How does Zircalon 30 Compare?
A new grade of zirconia, Zircalon 30 has been developed specifically for applications and industries which require outstanding fracture toughness whilst maintaining the excellent strength and wear resistant characteristics for which electrically-insulating zirconia ceramics are renowned for.
Zircalon 30 is a co-stabilized zirconia and aluminium oxide (Al2O3) matrix based composite ceramic which is reinforced by self-grown alumina-based platelets.
The mechanical benefits of zirconia products which have been co-stabilized with multiple additives with the presence of a reinforced platelet microstructure results in a drastically improved fracture toughness of approximately 14-15MPa m½, compared with 10 MPa m½ for conventional YSZ.
In comparison with a typical YSZ, Zircalon 30 offers the advantage of a greater impact resistance – increased by as much as 50%.
Its intended main use is in metal forming and welding applications – especially as non-electrically conductive weld location and control pins.
Issues with Established Weld Pin Materials
During the resistance welding process, location or control pins are required to temporarily hold the sheet metal and other components, like captive nuts, in the correct place while the operator or robot applies the weld.
In general, this operation is performed by feeding the location pin through an aperture in the metal sheet which has been formed in advance. The second sheet or nut is naturally centred around the pin, and the two are fused together by the welding assembly. The whole operation typically takes less than 15 seconds, even when carried out manually.
This is achieved via the introduction of a voltage differential between the lower and upper domains of the welding unit. After this process, it is easy to retract the non-conductive control pin.
Issues can arise when using steel control pins, as their electrical conductivity is liable to cause arcing between the workpiece, the product, and the pin itself. This may result in a build-up of slag material on the pin which can potentially inhibit the retraction process.
Furthermore, they are liable to weld corrosion, or ‘pitting’, and metal contamination. Pitting can lead to a visible porosity which renders the component inoperable over time. As corroded control pins need to be replaced more regularly, this causes potential losses in production and maintenance costs which can be avoided.
For the fabrication of weld location pins, technical ceramics have become more commonly used, particularly on automotive manufacturing lines, where several thousands of welds can be performed by a single operator each day. This is a result of their demonstrable improvements in terms of ongoing operating performance and efficiency.
The lifespan of steel location pins for one major European automotive manufacturer was calculated at roughly 70,000 operations prior to failure. By comparison, control pins manufactured using Syalon 101, an innovative silicon nitride (Si3N4) derived ceramic, carried out over 7 million operation cycles without exhibiting noticeable wear or reduced functionality. As a result, Syalon 101 weld control pins are often considered to be essential consumable components on many automotive manufacturing lines.
The Emergence of Zirconia Weld Pins
Zirconia has emerged in engineering areas such as metal forming as a result of the demanding and complex mechanical conditions exhibited in high-throughput processing. On occasion, in facilities in which high impacting forces are a factor in the long-term performance of the weld assembly, it is advisable to use weld location pins made from zirconia, rather than silicon nitride.
.jpg)
Image Credits: International Syalons
In a weld assembly, the operating conditions are extreme, including potentially hazardous agents like ionized gases and particles, elevated ambient temperatures, and peak flame impingement temperatures of 3,500 °C (6,500 °F).
The traditional benefits of current zirconia-based control pins can be improved upon by Zircalon 30, as it has improved thermomechanical performance characteristics. Zircalon 30 control pins are already performing better than some Zircalon 10 pins, which had previously established the benchmark for zirconia’s strength and toughness properties.
Zircalon 30 control pins can perform high-throughput welding operations reliably, and with significantly increased resistance to fractures caused by placing the nut on the pin, retracting the component from the end-product, or unavoidable impacts while lining up the sheet metal aperture.
References
- http://huysindustries.com/wp-content/uploads/huysarticle08-Non-Conductive_Welding_Pins_Based_on_Zirconia_Ceramics.pdf
- https://www.ncbi.nlm.nih.gov/pubmed/28000266
- https://www.sciencedirect.com/science/article/pii/S0300571207001418
- https://patents.google.com/patent/US5248869A/en
- https://www.azom.com/article.aspx?ArticleID=11578
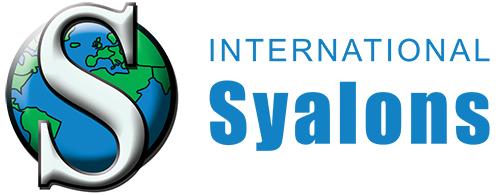
This information has been sourced, reviewed and adapted from materials provided by International Syalons.
For more information on this source, please visit International Syalons.