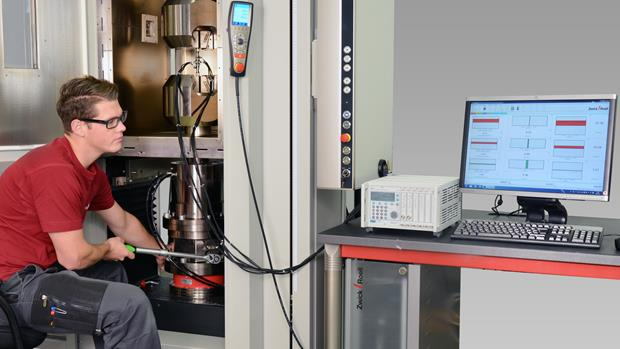
Image Credit: ZwickRoell GmbH Co. KG
Originally a worldwide accreditation program for suppliers to the aerospace and defense industries, Nadcap stands for "National Aerospace and Defense Contractors Accreditation Program". Nadcap's aim is to create economical approaches to special products and processes and to promote continual improvement within accredited companies.
In contrast to certification of quality management systems such as EN 9100 and ISO 9001, Nadcap accreditation includes both an audit with regard to the observance of defined specifications and guidelines and detailed examination of special technical processes.
In particular, aerospace industry manufacturers and suppliers define very demanding requirements for the staff and technical qualifications of testing laboratories. These needs are specified in directives, standards, and audit criteria, and are checked via Nadcap audits, enabling maximum process stability to be achieved and the standardization of quality guaranteed.
One component of Nadcap accreditation is alignment measurement and it is based on ASTM E1012, which stipulates compliance with defined tolerances. This is reflected in Nadcap-defined audit criteria AC 7101 and AC 7122, which outline the conditions for the measuring procedure, which is the verification of test axis alignment.
Further to service providers and aerospace manufacturers, an increasing number of companies in other sectors are affected by alignment measurement as part of Nadcap accreditation requirements, e.g., in the mechanical and plant engineering industry and in the metals industry.
Alignment Measurement to ASTM E1012
The standardized choice for alignment measurement is described in ASTM E1012 and includes a recorded inspection of test axis alignment. The electronic measurement of bending influences that can be a result of offset in the test axis or the smallest angular errors is required.
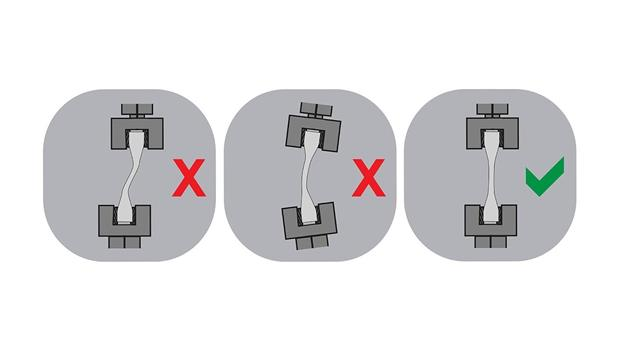
Image Credit: ZwickRoell GmbH Co. KG
Erroneous Alignments of Test Axes (Misalignments) Cause Non-Uniform Force Application to the Specimen. This Results in an Increased Risk of Breakage Near the Clamping.
Misalignments can be particularly common with brittle materials. Brittle and stiff materials break with seeming low tensile strain and stress in the area of the largest bending.
This is where ZwickRoell's alignment services are beneficial: a highly developed procedure permits visualization of the specific bending strain with the help of strain gages and reporting to initiate the measures for alignment needed.
ZwickRoell Services
Strain-gaged alignment transducers, based on ASTM E1012, which preferably conform to the geometry of the specimen to be tested at a later time, are necessary. An experienced ZwickRoell service technician positions the strain-gaged alignment transducer in the test axis of a testing system before it is loaded in the elastic range.
Their tools and equipment meet the best quality standards. This ensures precise alignment measurement to find possible bending influences in a test axis. The applied strain gages will register different strains in the event of non-uniform force application to the specimen.
Via a connected electrical measurement amplifier and transferred to a special testXpert II software test program, these can be digitized. Material properties are established and logged in testXpert II according to specimen geometries and standard specifications.
On the basis of characteristic measurement results, a simple, structured evaluation in testXpert II allows a ZwickRoell service technician to identify errors in the test axis. Measures can be taken using components specifically developed for alignments to resolve alignment errors if necessary.
Furthermore, testXpert II supplies adjustment recommendations for the alignment unit option, enabling detected alignment to be corrected conveniently and easily. ZwickRoell’s standardized strain-gaged alignment transducer works with a large number of the materials testing machines to be tested.
Additionally, defined geometry data can be utilized with strain-gaged alignment transducers according to specific requirements.

Image Credit: ZwickRoell GmbH Co. KG
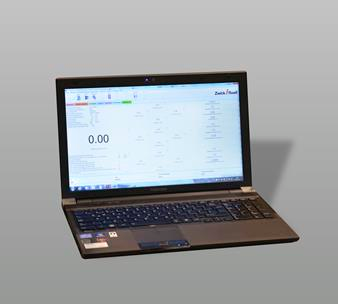
Image Credit: ZwickRoell GmbH Co. KG
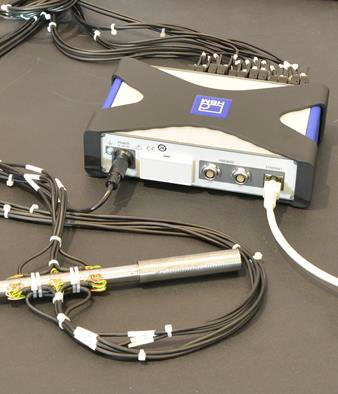
Image Credit: ZwickRoell GmbH Co. KG
ZwickRoell Benefits
- Predefined test sequences consist of measurements at a 0 °/90 °/180 °/270 ° transducer mounting position, zero-measurement repetition, zero-measurement, measurement under load, measurement clamped without axial strain, and top-down measurements.
- ZwickRoell guarantees a high degree of comparability with customer-specific specimen dimensions (adaptation) by utilizing standardized strain-gaged alignment transducers.
- Alignment measurement as part of inspection and calibration is possible, which means no additional travel costs are incurred.
- Individual geometry data may be converted and used with the strain-gaged alignment transducer.
- Precise measurement results using measurement of inverted positioning.
- Alignment measurement is fast due to ZwickRoell's standard-compliant strain-gaged alignment transducers.
- Convenient testXpert II software with adjustment diagrams display the individual components of the alignment error and adjustment instructions for the operator directly.
- Correction of alignment errors by adjustment via the optionally available alignment unit.
- Continuous numerical and graphic display of test results of bending and percentage bending.
- Everything from a single source, from advice to implementation
- Alignment measurement is also viable on machines from other manufacturers
- Qualified ZwickRoell experts guarantee professional and individualized support for questions and individual requirements.
- Factory test report stating mechanical and electrical characteristics of the ZwickRoell strain-gaged alignment transducer.
- Complete, detailed recording of measurement results as required by the standards and beyond (incorporation of images possible).
- Complete integration of the HBM measurement amplifier in the testXpert II testing software.
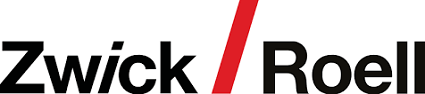
This information has been sourced, reviewed and adapted from materials provided by ZwickRoell.
For more information on this source, please visit ZwickRoell GmbH Co. KG