Despite the mixed reports about the levels of consumer spending during the Christmas and New Year period, what is not in doubt is that much of the festivities were paid for on credit.
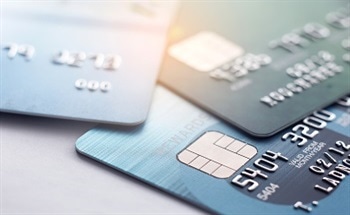
While good news for those companies offering credit, it also put the actual credit cards themselves through something of a battering. A recent survey has shown that around 30% or 14 million people in the UK have a store card and many more have debit cards issued by their banks.
With the advent of more sophisticated electronic smart cards, the use of ‘plastic’ is here to stay, so checking the quality of the cards during manufacture has never been more important.
Manufacture and Mechanical Properties of Credit Cards
The manufacture of plastic cards is a complex process. Cards are often squashed together in wallets and are frequently swiped through tills and machines, so must be resilient to damage and bending. More importantly, the surface laminates must not peel apart.
In short, the card must be robust, sufficiently flexible, yet not too rigid or brittle that it snaps. The usage rate and intended function must also be taken into account. Of the 14 million people who have a store card, most only use it three times a year.
Typically, a store card lasts for two years, a credit or debit card for three or four years, and the more sophisticated smart cards are designed with a five-year life span. That means the testing criteria must be appropriate for the type of card being manufactured.
Design and Construction of a Credit Card
Cards themselves range in thickness from 0.25mm to 0.76mm and are typically made up of two or three layers of PVC-related polymers. Usually, one of the layers is screen printed, then a clear PVC layer is laminated on top.
The printed surface, sandwiched between the two plastic sheets, acts as an adhesive, so the effects of printing on the card must also be assessed. Other features, such as special finishes, magnetic strips, signature panels, holograms and smart chips will also affect the design of the card.
Inks for Credit Card Printing
There is a vast array of inks and pigments available to the card manufacturer, allowing cards to become powerful extensions of corporate brands and services.
The majority of inks used still tend to be solvent-based, the vapours of which can be a problem during production, so there is a drive towards developing a more environmentally friendly process. One solution is to use UV-cure inks that cure only when exposed to a controlled dose of UV radiation.
These give manufacturers better control over the screening process and as there are no associated problems with evaporated fumes, they are kinder to the environment and workforce.
Testing of Credit Cards
Although the technical abilities of ink pigments and polymer composites are constantly improving, the one requirement that remains constant is the quality standard test. Like most manufactured products, plastic cards must meet with quality standards to satisfy customer requirements.
The complex design elements that make up a card mean that the best way to achieve a successful manufacturing process is to test the product at different stages during production. There are many suitable tests, from checking the melt flow of raw polymers, to the bend, flexure, peel and impact strength tests of finished laminated items.
For plastic cards, peel strength is the most valuable test. Traditionally used to check the bond strength of adhesives, a peel test involves gripping a sample horizontally and measuring the tensile force needed to peel away one of the laminates at 90° or 180°. The resulting data is then used to determine the bond strength of the individual laminate layers that make up the card.
Environmental Testing of Credit Cards
Environmental tests and aging tests can also be used to simulate the accelerated life of the card. Card laminates, for example, can be heated for a designated length of time, then retested to check the effects of heat on laminate performance.
Environmental chambers can be used to subject the card to increased conditions of humidity and temperature, before retesting to check the bond performance of the laminate layers.
Credit Card Test Methods
The international standards that such tests conform to include ISO/IEC 7810 (Identification Cards - Physical Characteristics), which sets out a range of physical characteristics including the mechanical robustness of the card, and ISO/IEC 10373 (Identification Cards - Test Methods), dealing with credit card test methods.
These international test standards are particularly important to Coates Screen, a supplier of printing inks to the plastic card manufacturing industry. The company tests the effect of its inks on the performance of plastic cards, and supports its ink products with detailed testing data for its customers.
Working closely with its clients, the company makes testing an integral part of its research and development programme, and recently decided that improvements could be made to its existing test procedures.
Consequently, testing machine specialists Lloyd instruments was asked to supply it with a 5kN LRXPlus single-column universal testing machine, equipped with two special credit card peel fixtures and tensile grips.
Download the LRXPlus Brochure for More Information
Hardware for Checking to Suitability of Inks on Credit Cards
Lloyd Instruments is an established global manufacturer of materials testing equipment and software for checking the quality and strength properties of materials, components and finished products in many industries worldwide.
The machine supplied to Coates was designed to test the delamination strength of individual layers that make up credit cards. For this it was equipped with fixtures for testing peel strength at angles of both 90° and 180° Such tests ensure the printed ink has no detrimental affect on the strength of the card’s laminated layers.
These tests are conducted after the card has been laminated and then again after the card has been either heat-aged or undergone environmental cycling tests. With other jigs used on the same machine, flexural tests on both the horizontal and vertical axis of the card are also possible.
‘We were delighted with the test system and the dedicated fixtures Lloyd Instruments designed for us,’ said Stewart Kessel, International Product Development Manager for Coates. A key requirement from listening to our customers was a need to quantify our test data in a more userfriendly and efficient manner. We upgraded to the latest NEXYGEN MT software, which has helped us enormously in this area.'
Software Supplied with the Hardware
NEXYGEN MT, the software supplied, with the unit, is well renowned in manufacturing industries as the leading ISO 9001 TickIT accredited materials testing software available.
The latest version, 4.5, contains a comprehensive library of international standard tests and features password security and full data audit trails to ensure data is completely traceable. Video capture and playback are available to help during product development, allowing visually checking of the test in parallel with the data.
Summary
Testing machines have evolved during the past 30 years, so much so that only minimal training is needed before employees can begin a product testing programme. Minimising downtime and the associated costs is also particularly important, so much effort from Lloyd Instruments has gone into designing solutions that are easy to set-up and operate.
The fact that this expertise is now extended to ink manufacturers who supply the credit card industry ensures that our flexible friends will stay strong and resilient for their intended lifespan, irrespective of the amount of use they get.
|