Scientists do not completely comprehend the principal cause of wear and friction between two surfaces at the molecular level.
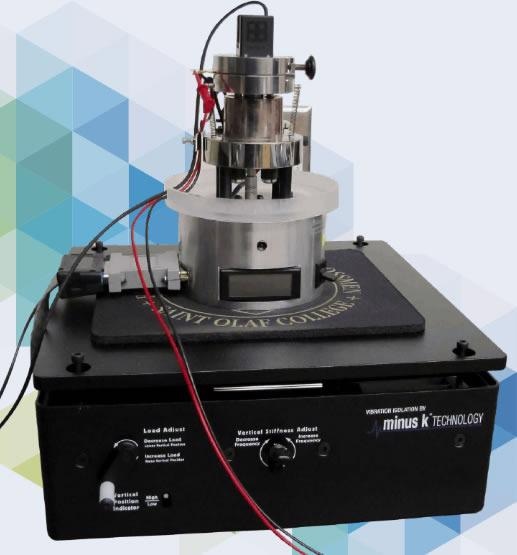
The nanoindenter-quartz microbalance mounted on a negative-stiffness vibration isolator. Image Credit: St. Olaf College
Whenever you are trying to design a micromechanical system, it is likely to include the fundamental machine parts of gears, gimbals, hinges, pistons and suspended beams that flex.
Brian Borovsky, Associate Professor, Physics Department at St. Olaf College
Borovsky continues, "Basic motions, which are the essence of mechanics, rely on these materials having durability and low or controllable friction. Mastering these forces that occur on such small-scale surfaces of micromachines is a considerable challenge.
When the mechanical parts are so small, their properties are dominated by surface forces in a way that macroscopic machines are not. Entirely new questions are raised about how to keep them moving and protected from wear or breakage."
Silicon Uniformity
To lower friction and maintain the movement of parts inside tiny silicon-constructed microelectromechanicaI systems (MEMS) engineers have typically depended on incredibly thin lubricant films.
The effectiveness of these films has proven to have been insufficient in micromachines reliant on parts moving at relatively high-speeds when in contact with one another, including gears, gimbals and pistons.
Since the early 1980s, when micromechanical machines were first introduced, the idea has been to batch-fabricate these devices as silicon chips and wirelessly connect them with the necessary circuitry. After just a few hours of operation, however, these small silicon machines deteriorate rapidly.
This technology has for some time been struggling to make it to the marketplace. Literally, decades of research in both academia and business has been undertaken to understand friction and wear well enough at these micro- and nano-scales to effectively lubricate and provide wear protection.
Brian Borovsky, Associate Professor, Physics Department at St. Olaf College
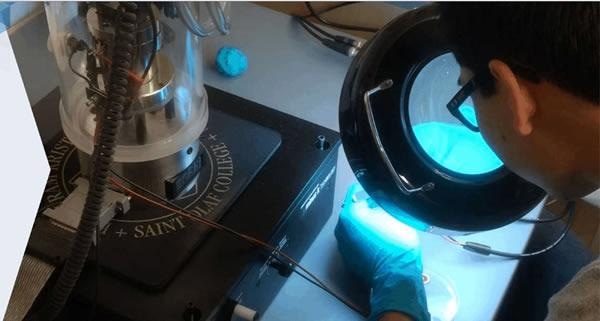
A researcher performing a nanotribology experiment using the nanoindenter-quartz microbalance. Image Credit: St. Olaf College
The New Research Methodology
Focusing on micro/nanotribology at St Olaf College, Borovsky has been researching friction applied to very tiny micromechanical machines for over two decades. This has resulted in the progress of instrumentation and a procedure aimed at preventing frictional properties of surfaces coated in ullrathm lubricants.
Borovsky’s is just one of a handful of labs that can measure the friction of micromachines that come into contact at significant high-speeds.
The lab is home to a wide variety of scanning electron microscopy (SEM) and atomic force microscopy (AFM) equipment, but the primary instrumentation is the nanoindenter-quartz microbalance of which Borovsky says, "It is unique and unlike anything else found in other laboratories studying friction."
In essence, Borovsky and his colleagues have tailored two separate tribology systems and incorporated them into one: specifically, the Hysitron TriboScope rigid nanoindenter probe, fabricated by Bruker, and a quartz crystal microbalance (QCM).
Attached to the indenter probe tip is an aluminum oxide (sapphire) microsphere. The Indenter probe is positioned onto a laterally oscillating surface that moves back and forth below the probe tip at exceedingly high-speeds.
Upon contact, the resonant frequency and quality factor of the quartz crystal fluctuate between the tip and the surface.
These fluctuations are marked as functions of oscillation amplitude at a pre-determined normal load. The quartz crystal’s increasing frequency is used to establish static friction. The decreasing quality factor of the quartz crystal is used to indicate kinetic friction.
It is straightforward to reach speeds and differentials that correspond to the fastest micromachines due to the quartz crystal oscillating at five million times per second.
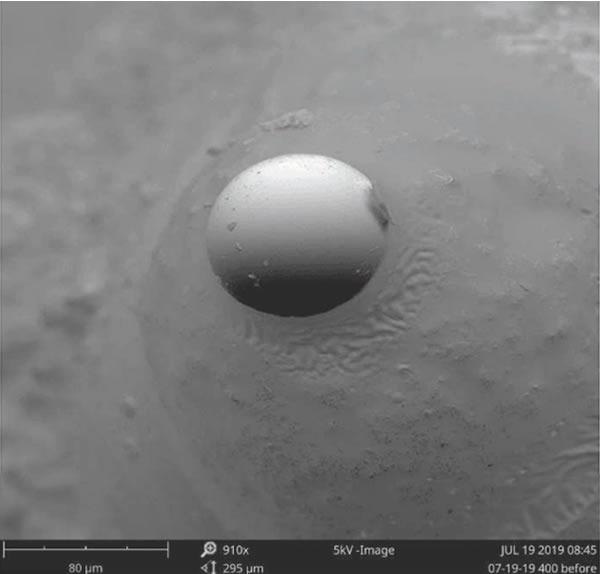
A silicon microsphere enlarged 910 x. Image Credit: St. Olaf College
Negative-Stiffness Vibration Isolators
This level of research necessitates vibrational interference reduced to a complete minimum, thus, the nanoindenter-quartz microbalance is loaded onto a negative-stiffness vibration isolator. Since 2001, St Olaf College has utilized negative-stiffness vibration isolators for all micra/nanotribology work.
These vibration isolators do not require a constant supply of electricity or compressed air and can be placed almost anywhere due to their compact size.
These qualities offer a certain freedom to a laboratory or production facility as sensitive instruments can be set up in a basement or where the building's vibration occurs, even compromised upper floors or rooftops are accessible.
Additionally, as there are no motors, chambers, or pumps no maintenance is required because there is nothing to wear out. They function exclusively in a passive mechanical mode.
The major benefits of negative-stiffness isolators is that they can accomplish a high-level of isolation in numerous directions. They offer the flexibility of custom tailoring resonant frequencies to 0 5 Hz* both vertically and horizontally (with some models at 1.5 Hz horizontally).
*For an isolation system with a 0.5 Hz natural frequency, isolation starts at 0.7 Hz and gets better with an expansion in the vibration frequency. The natural frequency is most frequently used to characterize the system.
Vertical-motion isolation is enabled by a stiff spring that bears a weight load in combination with a negative-stiffness mechanism. The net vertical stiffness is set extremely low without influencing the spring’s static load-supporting capacity.
Horizontal motion isolation is provided by beam-columns linked coupled in a series with the vertical-motion isolator. Each beam-column acts as a spring in combination with a negative-stiffness mechanism.
This results in a compact passive isolator, with the capacity of yielding exceptionally low, natural vertical and horizontal frequencies and significantly high internal structural frequencies.
Negative-stiffness isolators give excellent performance as measured by a vibration transmissibility curve. Vibration transmissibility is a measure of the vibrations that are transferred and communicated via the isolator relative to the input vibrations.
Negative-stiffness isolators that have been adjusted to 0.5 Hz reach around 93 percent isolation efficiency at 2 Hz, 99 percent at 5 Hz and 99.7 percent at 10 Hz.
Although our facilities have few external vibrations that could influence our experiments, like any laboratory, we are subject to vibration influence from HVAC systems, elevators, doors opening and closing, and even footfall near the instrumentation. These isolators are simple to set up and operate, and they just continue to work, day after day.
Brian Borovsky, Associate Professor, Physics Department at St. Olaf College
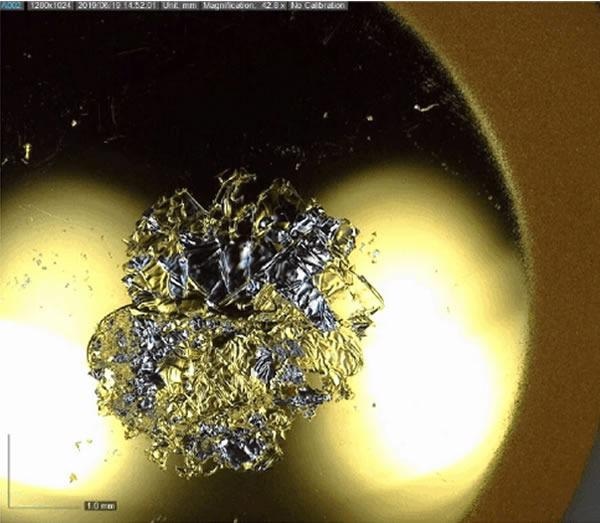
A quartz crystal before testing. Image Credit: St. Olaf College
Ongoing Research
The research that St. Olaf College is committed to, the investigation of solutions relative to friction in micromechanical systems, is set to continue thanks to the participation and support provided by a number of influential, established corporations. Commitment to decades of research in both business and academia have led to a comprehensive understanding of friction and wear at micro- and nano- scales to successfully lubricate and offer wear protection.
Borovsky concluded, “This work is motivated by the promise of micromechanical systems. Micromechanics could be a really big deal, with influence in virtually every aspect of our lives, similar to microelectronics. There are many institutions and researchers devoted to unraveling the mysteries of friction wear on these small devices. Step by step, we are making forward progress."
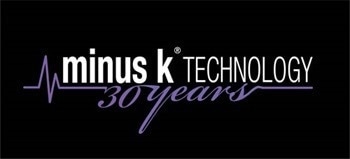
This information has been sourced, reviewed, and adapted from materials provided by Minus K Technology.
For more information on this source, please visit Minus K Technology.